Introduction
When it comes to ensuring optimal heat transfer between electronic components and heatsinks, two popular solutions emerge: thermal pads and thermal paste. Both materials serve the crucial purpose of filling the microscopic gaps and irregularities between surfaces, allowing for efficient heat dissipation. However, each option has its own unique properties, advantages, and disadvantages. In this article, we will delve into a comprehensive comparison of thermal pads and thermal paste, exploring their composition, performance, ease of use, and specific applications.
What are Thermal Pads?
Thermal pads, also known as thermal interface pads, are pre-cut, solid sheets of thermally conductive material. They are typically made from a combination of silicone or other polymer matrices filled with thermally conductive particles such as ceramic, aluminum oxide, or boron nitride. These pads come in various thicknesses, ranging from 0.5mm to 5mm, and are designed to be placed between the heat source and the heatsink.
Advantages of Thermal Pads
- Ease of use: Thermal pads are incredibly simple to apply. They require no preparation or curing time, and their pre-cut nature eliminates the need for precise application techniques.
- No mess: Unlike thermal paste, thermal pads are solid and do not create any mess during application or removal. This makes them ideal for quick installations or situations where cleanliness is a priority.
- Electrical insulation: Most thermal pads offer excellent electrical insulation properties, preventing short circuits and protecting sensitive components.
- Gap-filling ability: Thermal pads are effective at filling larger gaps between surfaces, making them suitable for applications with higher tolerances or uneven mating surfaces.
Disadvantages of Thermal Pads
- Lower thermal conductivity: Compared to high-quality thermal pastes, thermal pads generally have lower thermal conductivity. This means they may not provide the same level of heat transfer efficiency.
- Limited conformity: While thermal pads can fill gaps, they may not conform as well to the microscopic irregularities of the mating surfaces, potentially leaving small air pockets that can hinder heat transfer.
- Thickness limitations: Thermal pads come in pre-determined thicknesses, which may not always match the exact requirements of a specific application. Using a pad that is too thick or too thin can negatively impact thermal performance.
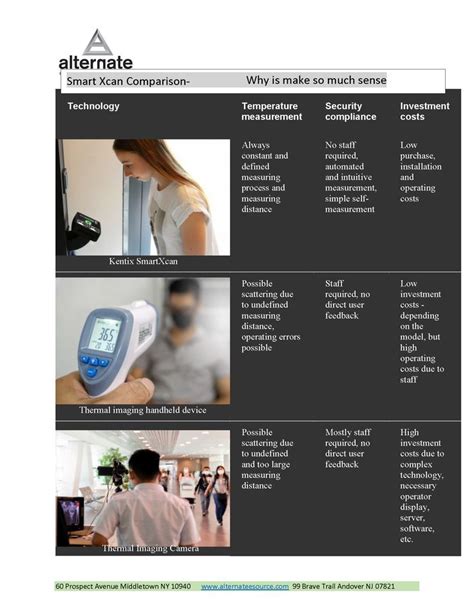
What is Thermal Paste?
Thermal paste, also referred to as thermal grease, thermal compound, or heat sink compound, is a viscous substance applied between a heat source and a heatsink to enhance heat transfer. It is composed of a base material, typically silicone or other synthetic oils, mixed with thermally conductive filler particles such as silver, aluminum, zinc oxide, or boron nitride.
Advantages of Thermal Paste
- Higher thermal conductivity: High-quality thermal pastes often boast superior thermal conductivity compared to thermal pads. This allows for more efficient heat transfer between surfaces.
- Excellent conformity: Thermal paste can easily fill the microscopic gaps and irregularities between mating surfaces, ensuring optimal contact and minimizing air pockets.
- Thin bond line: When applied correctly, thermal paste creates an extremely thin layer between the heat source and heatsink, which helps minimize thermal resistance.
- Versatility: Thermal paste can be used in a wide range of applications, from desktop computers and laptops to high-performance gaming systems and industrial equipment.
Disadvantages of Thermal Paste
- Application complexity: Applying thermal paste requires a certain level of skill and precision. Applying too much or too little paste can lead to suboptimal performance.
- Messy: Thermal paste can be messy to work with, especially for inexperienced users. It can easily spread to unwanted areas and may require careful cleanup.
- Pump-out effect: In some cases, thermal paste can be prone to the pump-out effect, where the paste is squeezed out from between the mating surfaces due to thermal cycling and pressure changes over time.
- Drying out: Some thermal pastes may dry out or harden over extended periods, leading to reduced thermal performance and the need for reapplication.
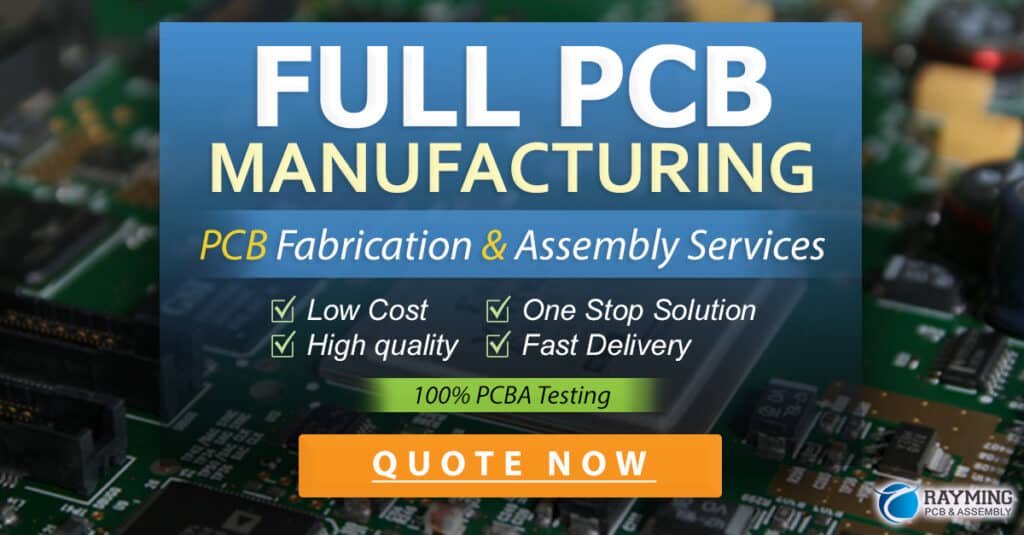
Thermal Conductivity Comparison
One of the key factors in determining the effectiveness of a thermal interface material is its thermal conductivity. Thermal conductivity is measured in watts per meter-kelvin (W/mK) and represents the material’s ability to transfer heat. Here’s a table comparing the typical thermal conductivity ranges of thermal pads and thermal pastes:
Thermal Interface Material | Thermal Conductivity Range (W/mK) |
---|---|
Thermal Pads | 0.5 – 10 |
Thermal Paste | 2 – 15 |
As evident from the table, thermal pastes generally offer higher thermal conductivity compared to thermal pads. However, it’s important to note that the actual thermal conductivity can vary significantly depending on the specific product and its composition.
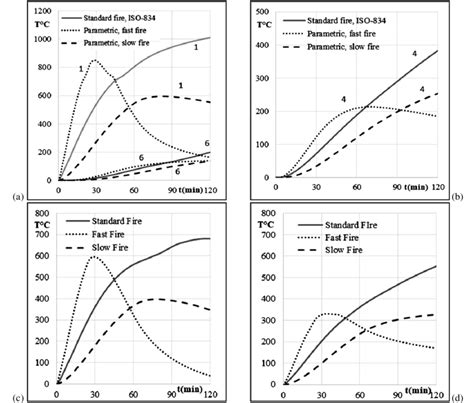
Application Techniques
Applying Thermal Pads
- Clean the surfaces: Ensure that the heat source and heatsink surfaces are clean and free from dust, dirt, or old thermal material residue.
- Cut the pad (if necessary): If the thermal pad is larger than the required size, carefully cut it to match the dimensions of the heat source.
- Remove protective layers: Most thermal pads come with protective films on both sides. Peel off these layers to expose the adhesive surfaces.
- Place the pad: Position the thermal pad on the heat source, ensuring that it is centered and covers the entire surface.
- Apply pressure: Gently press the heatsink onto the thermal pad to ensure good contact and adhesion.
Applying Thermal Paste
- Clean the surfaces: As with thermal pads, make sure the mating surfaces are clean and free from any residue.
- Apply the paste: There are several methods to apply thermal paste, such as the dot method, line method, or spread method. The most common technique is to place a small dot (about the size of a rice grain) at the center of the heat source.
- Spread the paste (optional): Some users prefer to spread the thermal paste evenly using a flat object like a credit card. However, this step is not always necessary as the pressure from the heatsink will spread the paste.
- Attach the heatsink: Carefully place the heatsink onto the heat source, ensuring that it is centered and aligned correctly.
- Secure the heatsink: Use the appropriate mounting mechanism (e.g., screws, clips, or brackets) to securely fasten the heatsink in place.
Specific Applications
When to Use Thermal Pads
Thermal pads are particularly suitable for the following applications:
1. Solid-state drives (SSDs): Thermal pads are commonly used to cool SSDs, as they provide good thermal transfer while electrically insulating the components.
2. Memory modules: High-performance memory modules, such as those used in gaming or workstation systems, often employ thermal pads to dissipate heat.
3. Power electronics: In power electronic devices, like voltage regulators or MOSFETs, thermal pads help manage heat while providing electrical insulation.
4. Rough or uneven surfaces: When dealing with surfaces that have significant irregularities or high tolerances, thermal pads can help bridge the gaps and ensure adequate thermal contact.
When to Use Thermal Paste
Thermal paste is the preferred choice for the following scenarios:
1. CPU and GPU cooling: Thermal paste is the go-to solution for cooling central processing units (CPUs) and graphics processing units (GPUs) in computers and gaming consoles.
2. High-performance applications: In demanding applications where optimal thermal transfer is critical, such as overclocked systems or high-performance computing, thermal paste provides the best results.
3. Smooth, flat surfaces: When the mating surfaces are smooth and flat, thermal paste can achieve an extremely thin bond line, minimizing thermal resistance.
4. Frequent disassembly: If the heatsink needs to be removed and reattached often, thermal paste allows for easier cleanup and reapplication compared to thermal pads.
Frequently Asked Questions (FAQ)
-
Can I use both thermal pad and thermal paste together?
While it is possible to use both thermal pad and paste together, it is generally not recommended. Using both materials can lead to increased thermal resistance and potential air gaps, negatively impacting cooling performance. It’s best to choose either a thermal pad or thermal paste based on your specific application and requirements. -
How often should I replace thermal pads or thermal paste?
The lifespan of thermal pads and thermal paste depends on various factors, such as the quality of the material, operating temperatures, and environmental conditions. As a general guideline, thermal pads can last for several years without needing replacement, unless they become damaged or lose their adhesion. Thermal paste, on the other hand, may need to be replaced every few years or when you notice a decrease in cooling performance. If you frequently disassemble your system, it’s a good idea to check the condition of the thermal interface material and replace it if necessary. -
Can I use any thermal pad or paste for my application?
Not all thermal pads and pastes are created equal. It’s essential to choose a high-quality thermal interface material that is suitable for your specific application. Consider factors such as thermal conductivity, thickness, electrical insulation, and compatibility with the surfaces you are working with. Always refer to the manufacturer’s specifications and recommendations to ensure optimal performance and safety. -
How do I remove old thermal paste or pads?
To remove old thermal paste, start by using a soft, lint-free cloth or paper towel to wipe away as much of the paste as possible. For stubborn residue, you can use a small amount of isopropyl alcohol (90% or higher) to help dissolve the paste. Be gentle and patient to avoid damaging the surfaces. For thermal pads, carefully peel off the old pad from the surfaces. If there is any residue left behind, use a soft cloth dampened with isopropyl alcohol to clean it off. -
Can I reuse thermal pads or thermal paste?
It is not recommended to reuse thermal pads or thermal paste. Once a thermal pad has been compressed and removed, its thickness and adhesion properties may be compromised, leading to reduced cooling performance. Similarly, thermal paste that has been applied and removed may contain debris or have lost its optimal consistency. For the best results, always use fresh thermal pads or paste whenever you reassemble your cooling solution.
Conclusion
In the realm of thermal interface materials, both thermal pads and thermal paste have their place. Thermal pads offer ease of use, electrical insulation, and gap-filling capabilities, making them suitable for applications like SSDs, memory modules, and power electronics. On the other hand, thermal paste provides superior thermal conductivity, excellent conformity, and versatility, making it the preferred choice for CPU and GPU cooling, high-performance systems, and smooth, flat surfaces.
Ultimately, the decision between thermal pad and thermal paste depends on the specific requirements of your application, including factors such as the desired level of thermal performance, ease of installation, and the nature of the mating surfaces. By understanding the properties, advantages, and disadvantages of each option, you can make an informed choice that ensures optimal cooling and reliability for your electronic components.
Remember to always follow best practices when applying thermal pads or paste, and consider the manufacturer’s recommendations for your specific use case. Regular maintenance and inspection of your cooling solution can help you identify any issues and ensure long-term performance.
As technology continues to advance and heat dissipation becomes increasingly critical, thermal interface materials will play a crucial role in maintaining the stability and longevity of electronic devices. Whether you opt for thermal pads or thermal paste, investing in high-quality materials and proper application techniques will help you achieve optimal thermal management and keep your components running cool and efficient.
No responses yet