Introduction to Thermal Pad PCBs
Thermal management is a critical aspect of electronic device design, especially in high-power applications such as power electronics, LED lighting, and computer processors. Efficient heat dissipation is essential to ensure the reliability, performance, and longevity of electronic components. One effective solution for managing heat in printed circuit boards (PCBs) is the use of thermal pads, particularly spoked copper pads.
What are Thermal Pads?
Thermal pads, also known as heat transfer pads or thermal interface materials (TIMs), are specialized components designed to facilitate heat transfer from electronic devices to heat sinks or other cooling solutions. These pads are typically made of materials with high thermal conductivity, such as silicone, graphite, or ceramic-filled compounds. They are placed between the heat-generating component and the heat sink to minimize thermal resistance and enhance heat dissipation.
The Importance of Thermal Management in PCBs
Proper thermal management is crucial in PCB design for several reasons:
-
Component reliability: Excessive heat can cause electronic components to degrade, malfunction, or fail prematurely. By efficiently dissipating heat, thermal pads help maintain component temperatures within safe operating limits, thereby improving reliability.
-
Performance optimization: High temperatures can negatively impact the performance of electronic devices, leading to reduced efficiency, increased power consumption, and potential system instability. Effective thermal management ensures that components operate at optimal temperatures, maximizing their performance.
-
Space constraints: As electronic devices become increasingly compact, the need for efficient heat dissipation in limited space becomes more critical. Thermal pads provide a thin, lightweight solution for transferring heat from components to heat sinks, enabling designers to create compact, high-performance systems.
Spoked Copper Pads: A Unique Thermal Pad Design
Spoked copper pads are a specific type of thermal pad PCB design that offers several advantages over traditional solid copper pads. This design features a central copper pad with multiple radial “spokes” extending outward, resembling the shape of a wheel.
Advantages of Spoked Copper Pads
-
Reduced thermal resistance: The spoked design allows for better heat spreading and dissipation compared to solid copper pads. The increased surface area and radial pattern of the spokes facilitate more efficient heat transfer from the central pad to the surrounding PCB and heat sink.
-
Improved mechanical stability: The spoked structure provides mechanical support and stability to the central pad, reducing the risk of pad delamination or lifting during the soldering process. This enhanced stability ensures a reliable and robust connection between the component and the PCB.
-
Enhanced thermal cycling performance: Thermal cycling, which occurs due to temperature fluctuations during device operation, can cause stress and fatigue in the solder joints. The spoked design helps distribute the thermal stress more evenly, minimizing the risk of solder joint failure and improving the overall reliability of the system.
-
Compatibility with various components: Spoked copper pads can be designed to accommodate a wide range of component packages, including surface-mount devices (SMDs), quad-flat packages (QFPs), and ball grid arrays (BGAs). This versatility makes them suitable for various applications and design requirements.
Design Considerations for Spoked Copper Pads
When incorporating spoked copper pads into a PCB design, several factors should be considered:
-
Pad size and spoke dimensions: The size of the central pad and the width and length of the spokes should be optimized based on the specific component and its thermal requirements. Factors such as the component’s power dissipation, package size, and thermal resistance should be taken into account.
-
Spoke pattern and spacing: The number and arrangement of spokes can impact the thermal performance and mechanical stability of the pad. A balanced spoke pattern with evenly distributed spokes is generally recommended to ensure uniform heat dissipation and mechanical support.
-
Copper thickness: The thickness of the copper layer used for the spoked pad affects its thermal conductivity and current-carrying capacity. Thicker copper layers provide better thermal performance but may increase the overall cost of the PCB.
-
Solder mask and pad finish: The solder mask and pad finish play a role in the solderability and thermal transfer characteristics of the spoked pad. Selective solder masking, where the spokes are exposed, can enhance heat transfer, while appropriate pad finishes, such as nickel/gold or organic solderability preservative (OSP), ensure good solderability.
Thermal Pad Material Selection
The choice of thermal pad material is crucial for achieving optimal thermal performance and compatibility with the PCB and components. Several factors should be considered when selecting a thermal pad material:
-
Thermal conductivity: The thermal conductivity of the pad material determines its ability to transfer heat efficiently. Materials with higher thermal conductivity, such as ceramics or metal-filled compounds, are preferred for high-power applications.
-
Electrical insulation: In some cases, electrical insulation between the component and the PCB is required. Thermal pads with insulating properties, such as silicone or ceramic-filled pads, can provide the necessary insulation while still allowing efficient heat transfer.
-
Softness and conformability: The softness and conformability of the thermal pad material affect its ability to fill gaps and conform to surface irregularities, ensuring good thermal contact between the component and the pad. Softer materials, such as silicone or elastomeric pads, can provide better conformability.
-
Thermal stability: The thermal pad material should maintain its properties and performance over the expected operating temperature range of the device. Materials with good thermal stability, such as ceramic-filled pads, are preferred for high-temperature applications.
-
Outgassing and contamination: Some thermal pad materials may release volatile compounds or contaminants during high-temperature operation, which can affect the reliability of the electronic components. Low-outgassing materials, such as certain silicones or ceramics, are recommended to minimize contamination risks.
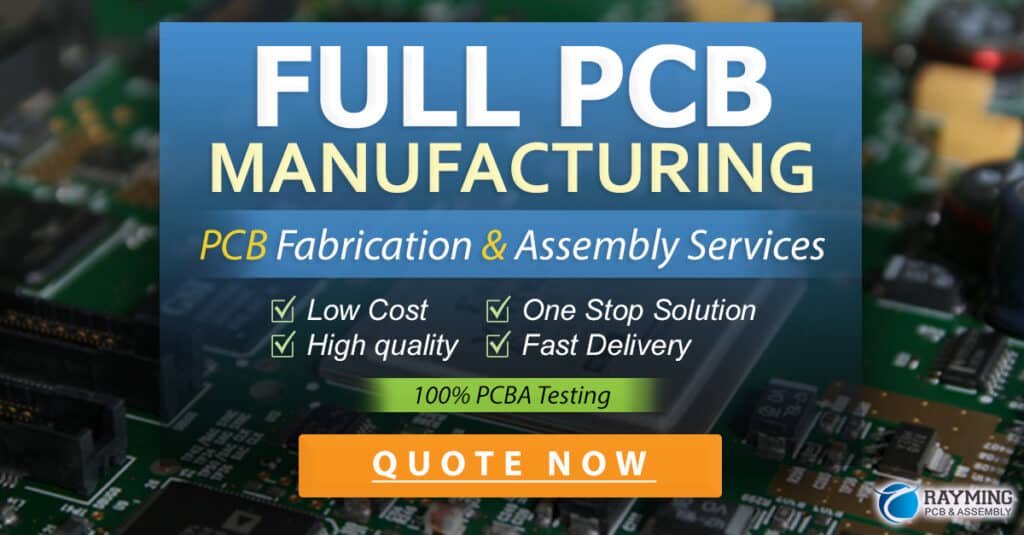
Thermal Pad Application Techniques
Proper application of thermal pads is essential for achieving optimal thermal performance and reliability. Several techniques can be used to apply thermal pads to PCBs and components:
-
Pre-cut pads: Pre-cut thermal pads are available in various sizes and shapes to match specific component packages. These pads can be easily placed on the PCB or component surface, providing a convenient and consistent application method.
-
Dispensing: Thermal pad materials can be dispensed directly onto the PCB or component using automated dispensing equipment. This technique allows for precise control over the amount and placement of the thermal pad material, making it suitable for high-volume production.
-
Screen printing: Screen printing involves applying a thin layer of thermal pad material onto the PCB using a stencil or screen. This method enables consistent and uniform application of the thermal pad material across multiple PCBs.
-
Lamination: Thermal pads can be laminated onto the PCB surface using pressure and heat. This technique ensures good adhesion between the pad and the PCB, minimizing the risk of delamination or gaps.
Thermal Pad Testing and Validation
To ensure the effectiveness and reliability of thermal pads in PCB designs, thorough testing and validation are necessary. Several methods can be used to evaluate the thermal performance and integrity of thermal pads:
-
Thermal resistance measurement: Thermal resistance is a key parameter that quantifies the ability of a thermal pad to transfer heat. It can be measured using specialized equipment, such as thermal transient testers or thermal imaging cameras. Lower thermal resistance indicates better heat transfer performance.
-
Temperature monitoring: Temperature monitoring involves measuring the temperatures of critical components and PCB areas during device operation. This can be done using thermocouples, resistance temperature detectors (RTDs), or infrared thermography. Temperature data can be used to validate the effectiveness of the thermal pad in maintaining safe operating temperatures.
-
Thermal cycling tests: Thermal cycling tests expose the PCB and components to repeated temperature fluctuations to assess the reliability of the thermal pad under varying thermal conditions. These tests help identify potential issues such as pad delamination, solder joint failure, or thermal fatigue.
-
Mechanical stress tests: Mechanical stress tests, such as shear or tensile tests, evaluate the adhesion and mechanical strength of the thermal pad. These tests ensure that the pad can withstand the stresses encountered during assembly, handling, and operation of the device.
-
Accelerated life tests: Accelerated life tests subject the PCB and components to elevated temperatures and/or humidity to assess the long-term reliability of the thermal pad. These tests help predict the expected lifetime of the thermal solution under normal operating conditions.
Case Studies and Application Examples
Thermal pad PCBs with spoked copper pads have been successfully implemented in various industries and applications. Here are a few case studies and examples:
Power Electronics
In power electronic devices, such as motor drives or power converters, efficient heat dissipation is critical for ensuring reliable operation and preventing component failure. Spoked copper pads have been used to enhance the thermal management of power semiconductor devices, such as insulated-gate bipolar transistors (IGBTs) and metal-oxide-semiconductor field-effect transistors (MOSFETs).
For example, a manufacturer of industrial motor drives implemented spoked copper pads on their PCBs to improve the thermal performance of their IGBT modules. By using spoked pads in combination with high-performance thermal interface materials, they were able to reduce the junction temperatures of the IGBTs by 15°C compared to traditional solid copper pads. This improvement in thermal management allowed them to increase the power density of their drives while maintaining reliable operation.
LED Lighting
LED lighting applications often require effective thermal management to ensure consistent light output, color accuracy, and long-term reliability. Spoked copper pads have been employed in LED PCB designs to dissipate heat from high-power LED packages.
In one case, a manufacturer of LED streetlights utilized spoked copper pads to optimize the thermal performance of their LED modules. By carefully designing the spoke pattern and dimensions, they achieved a 20% reduction in thermal resistance compared to conventional pad designs. This improvement allowed them to operate the LEDs at higher currents, resulting in increased luminous output and energy efficiency.
High-Performance Computing
High-performance computing systems, such as servers and data centers, generate significant amounts of heat that must be efficiently dissipated to maintain optimal performance and reliability. Spoked copper pads have been used in the PCB designs of these systems to enhance the thermal management of processors, memory modules, and other heat-generating components.
For instance, a server manufacturer implemented spoked copper pads in the PCB design of their high-end server processors. By using a combination of spoked pads and advanced thermal interface materials, they were able to reduce the processor temperatures by 10°C under full load conditions. This thermal improvement allowed them to boost the processor clock speeds, resulting in increased system performance.
Frequently Asked Questions (FAQ)
-
What are the benefits of using spoked copper pads compared to solid copper pads?
Spoked copper pads offer several advantages over solid copper pads, including reduced thermal resistance, improved mechanical stability, enhanced thermal cycling performance, and compatibility with various component packages. The spoked design allows for better heat spreading and dissipation, while also providing mechanical support and reducing the risk of pad delamination or solder joint failure. -
How do I choose the right thermal pad material for my application?
When selecting a thermal pad material, consider factors such as thermal conductivity, electrical insulation, softness and conformability, thermal stability, and outgassing properties. The choice of material depends on the specific requirements of your application, such as the power dissipation of the components, operating temperature range, and environmental conditions. Consult with thermal pad manufacturers or material specialists to determine the most suitable material for your needs. -
What are the different methods for applying thermal pads to PCBs?
Thermal pads can be applied to PCBs using various techniques, including pre-cut pads, dispensing, screen printing, and lamination. Pre-cut pads are convenient for small-scale applications, while dispensing and screen printing are suitable for high-volume production. Lamination ensures good adhesion between the pad and the PCB. The choice of application method depends on factors such as the size and shape of the components, production volume, and available equipment. -
How can I test and validate the thermal performance of my thermal pad PCB design?
Testing and validation of thermal pad PCBs involve methods such as thermal resistance measurement, temperature monitoring, thermal cycling tests, mechanical stress tests, and accelerated life tests. Thermal resistance measurement quantifies the heat transfer performance of the pad, while temperature monitoring verifies the effectiveness of the thermal solution in maintaining safe operating temperatures. Thermal cycling and mechanical stress tests assess the reliability of the pad under varying conditions, and accelerated life tests help predict the long-term performance of the thermal solution. -
Can spoked copper pads be used with any component package type?
Spoked copper pads can be designed to accommodate a wide range of component packages, including surface-mount devices (SMDs), quad-flat packages (QFPs), and ball grid arrays (BGAs). The pad size, spoke dimensions, and pattern can be customized to match the specific requirements of the component. However, it is important to consider the thermal and mechanical characteristics of the component when designing the spoked pad to ensure optimal performance and reliability.
Conclusion
Thermal pad PCBs with spoked copper pads offer a highly effective solution for managing heat in electronic devices. By leveraging the unique design of spoked pads, designers can achieve reduced thermal resistance, improved mechanical stability, and enhanced thermal cycling performance compared to traditional solid copper pads.
The selection of the appropriate thermal pad material, based on factors such as thermal conductivity, electrical insulation, and thermal stability, is crucial for optimizing the thermal performance and reliability of the system. Various application techniques, including pre-cut pads, dispensing, screen printing, and lamination, can be employed to integrate thermal pads into PCB designs effectively.
Thorough testing and validation, involving methods such as thermal resistance measurement, temperature monitoring, and accelerated life tests, are essential for ensuring the effectiveness and long-term reliability of thermal pad PCBs. Case studies from industries such as power electronics, LED lighting, and high-performance computing demonstrate the successful implementation of spoked copper pads in real-world applications.
As electronic devices continue to push the boundaries of performance and power density, the importance of efficient thermal management cannot be overstated. Thermal pad PCBs with spoked copper pads provide a powerful tool for designers to tackle the challenges of heat dissipation, enabling the development of reliable, high-performance electronic systems across a wide range of industries and applications.
No responses yet