Introduction
Thermal Management is a critical aspect in the design and performance of high frequency RF and microwave printed circuit boards (PCBs). As these systems push the limits of speed and signal integrity, managing heat dissipation becomes increasingly important to ensure reliability and prevent premature failure of components. This article will delve into the challenges, techniques and best practices for effective thermal management in RF and microwave PCB designs.
Thermal Challenges in RF and Microwave PCBs
RF and microwave circuits operate at high frequencies, often in the gigahertz range. At these frequencies, several factors contribute to increased heat generation:
High Power Densities
RF power amplifiers and transmitters handle significant amounts of power in relatively small packages and circuit board areas. The concentrated heat flux puts tremendous thermal stress on the PCB.
Dielectric Losses
High frequency signals traveling through PCB dielectric materials cause dielectric loss, converting some of the signal energy into heat. Low-loss materials are essential, but still exhibit some degree of thermal loss.
Conductor Losses
Conductor losses due to skin effect and surface roughness increase with frequency. This resistive heating in transmission lines and traces generates additional heat that must be managed.
Component Power Dissipation
Active RF components like power amplifiers and high-speed digital ICs generate substantial heat based on their power consumption and efficiency. Providing adequate cooling and heat sinking for these components is crucial.
Consequences of Inadequate Thermal Management
Failing to effectively manage heat in RF and microwave PCBs leads to several problems:
Reduced Reliability
Excess heat accelerates various failure mechanisms like electromigration, dielectric breakdown, and solder joint fatigue. Components operate outside their specified temperature ratings, leading to shorter lifespans.
Degraded Performance
As PCBs heat up, material properties change. Dielectric constants, thermal conductivity, and mechanical dimensions can shift, altering the carefully designed characteristics of RF circuits. This leads to detuned filters, impedance mismatches, and reduced amplifier efficiency.
Thermal Runaway
Some active components like power amplifiers increase their current draw with rising temperature. This leads to a positive feedback loop known as thermal runaway, where increasing temperature causes increased power dissipation, further heating the device until catastrophic failure occurs.
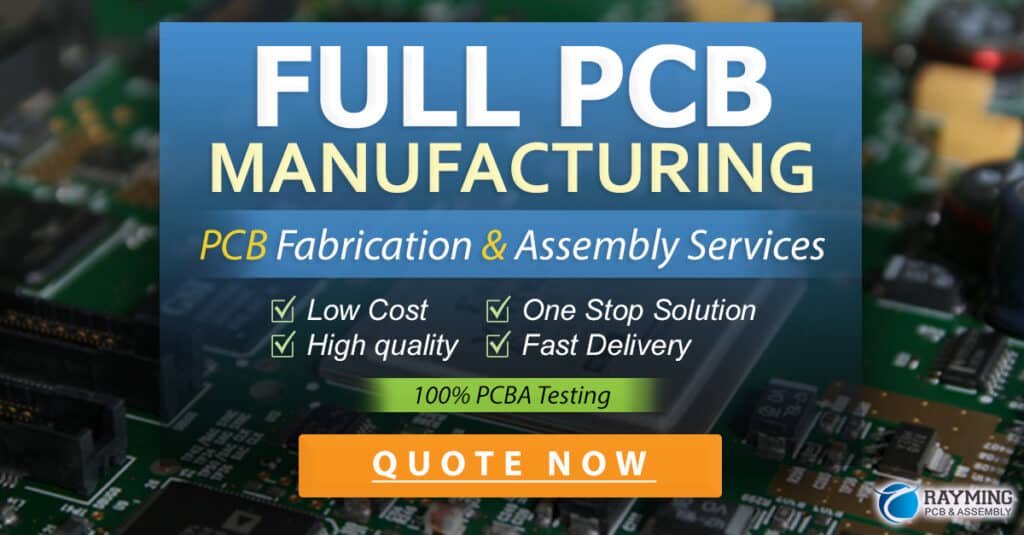
Thermal Management Techniques for RF and Microwave PCBs
Several techniques are employed to manage heat and mitigate the challenges described above. A combination of methods is often necessary for optimal results.
Material Selection
Choosing PCB materials with favorable thermal properties is the first step in thermal management. This includes:
- Using high thermal conductivity dielectrics to promote heat spreading.
- Selecting low-loss dielectrics to minimize heat generation from dielectric losses.
- Employing thermally conductive adhesives and fillers in the PCB stackup.
Some commonly used high performance materials are listed below:
Material | Thermal Conductivity (W/mK) | Dielectric Constant @ 10 GHz | Dissipation Factor @ 10 GHz |
---|---|---|---|
Rogers RT/duroid 6035HTC | 1.44 | 3.5 | 0.0013 |
Isola I-Tera MT40 | 0.62 | 3.45 | 0.0031 |
Rogers RO4835T | 0.66 | 3.33 | 0.0030 |
Thermal Vias
Thermal vias are small plated through-holes that transfer heat vertically through the PCB stackup. They provide a conductive path to heat sinks, ground planes, or dedicated thermal layers. Thermal vias are placed under or around high-heat-generating components.
Guidelines for thermal via use:
- Place vias as close to the heat source as possible
- Use arrays or staggered patterns for better heat transfer
- Ensure adequate via plating thickness for low thermal resistance
- Optimize via density based on PCB fabrication constraints and thermal simulations
Metal-Core PCBs
For the most demanding thermal requirements, metal-core PCBs (MCPCBs) offer a high-performance solution. An MCPCB uses a metal base layer, usually aluminum, as a heat spreader. Thermally conductive dielectric layers electrically isolate the metal core from the circuit layers.
Benefits of MCPCBs:
- Excellent heat spreading due to high thermal conductivity metal core
- Reduced thermal resistance from heat sources to heat sinks
- Mechanical stability and flatness provided by the metal substrate
Considerations for MCPCBs:
- More complex fabrication process compared to standard PCBs
- Potential for thermal expansion mismatch between metal core and PCB layers
- Higher cost than standard PCBs
Heat Sinks and Thermal Interface Materials
Attaching heat sinks to high-power components is a common thermal management strategy. Heat sinks provide a large surface area for convective cooling and help spread heat away from the source.
Thermal interface materials (TIMs) are used between the component and heat sink to minimize thermal resistance. TIMs fill air gaps and surface irregularities, ensuring efficient heat transfer.
Types of TIMs include:
- Thermal greases and pastes
- Phase-change materials
- Thermally conductive adhesives
- Thermal pads and gap fillers
Proper heat sink sizing and TIM selection are critical for optimal performance. Thermal simulations and calculations help determine the required heat sink dimensions and TIM properties for a given power dissipation and temperature rise target.
Thermal Simulations and Analysis
Thermal simulations using finite element analysis (FEA) or computational fluid dynamics (CFD) tools help predict the thermal behavior of RF and microwave PCBs. These simulations guide design decisions and optimize thermal management strategies.
Key aspects of thermal simulations:
- Modeling PCB stackup, materials, and components
- Applying power dissipation and boundary conditions
- Analyzing temperature distribution, hot spots, and heat flow paths
- Evaluating the effectiveness of thermal vias, heat sinks, and other cooling methods
Thermal simulations enable designers to iterate and refine the thermal management approach before committing to fabrication, saving time and cost.
Best Practices for RF and Microwave PCB Thermal Management
-
Start with a thermal budget: Determine the maximum allowable temperature rise for each component and the overall PCB based on reliability and performance requirements.
-
Optimize component placement: Place high-heat-generating components away from temperature-sensitive devices. Consider heat flow paths and available cooling mechanisms when arranging components.
-
Use thermal vias strategically: Place thermal vias close to heat sources, and use appropriate via density and plating thickness for effective heat transfer.
-
Select low-loss, thermally conductive materials: Choose PCB dielectrics and conductors that minimize thermal losses and promote heat spreading.
-
Incorporate heat sinks and TIMs: Use well-sized heat sinks and appropriate thermal interface materials to dissipate heat from high-power components.
-
Exploit ground planes for heat spreading: Utilize ground planes and power planes as heat spreaders by providing good thermal connections to heat sources.
-
Minimize thermal interfaces: Reduce the number of thermal interfaces between heat sources and heat sinks to lower overall thermal resistance.
-
Conduct thorough thermal simulations: Perform detailed thermal simulations to predict hot spots, optimize cooling strategies, and validate the thermal design before fabrication.
-
Consider active cooling methods: For extreme thermal demands, consider active cooling techniques like forced air, liquid cooling, or thermoelectric coolers.
-
Monitor temperatures during testing: Include temperature monitoring in the test and validation process to ensure the thermal management solution performs as intended.
Frequently Asked Questions
1. What is the importance of thermal management in RF and microwave PCBs?
Thermal management is crucial in RF and microwave PCBs to ensure reliable operation, prevent component failure, and maintain the designed performance characteristics of the circuit. Proper thermal management helps dissipate heat generated by high-frequency losses and high-power components.
2. What are some common thermal management techniques for RF and microwave PCBs?
Common thermal management techniques for RF and microwave PCBs include:
– Using high thermal conductivity and low-loss PCB materials
– Employing thermal vias to transfer heat through the PCB stackup
– Incorporating metal-core PCBs for enhanced heat spreading
– Attaching heat sinks and thermal interface materials to high-power components
– Conducting thermal simulations to optimize the thermal design
3. How do thermal vias help in managing heat in PCBs?
Thermal vias are small plated through-holes that provide a conductive path for heat to flow vertically through the PCB layers. They transfer heat away from high-temperature components to heat sinks, ground planes, or dedicated thermal layers, aiding in heat dissipation.
4. What are metal-core PCBs, and when are they used?
Metal-core PCBs (MCPCBs) have a metal base layer, usually aluminum, that acts as a heat spreader. The metal core is electrically isolated from the circuit layers by thermally conductive dielectric layers. MCPCBs are used in applications with high thermal demands, offering excellent heat spreading and reduced thermal resistance.
5. How can thermal simulations help in the design of RF and microwave PCBs?
Thermal simulations using finite element analysis (FEA) or computational fluid dynamics (CFD) tools help predict the thermal behavior of PCBs. These simulations allow designers to analyze temperature distributions, identify hot spots, evaluate the effectiveness of cooling methods, and optimize the thermal management strategy before fabrication, saving time and cost.
Conclusion
Effective thermal management is a vital consideration in the design of high performance RF and microwave PCBs. The high-frequency nature of these circuits presents unique challenges, such as increased dielectric and conductor losses, high power densities, and component heat dissipation. Failure to manage heat adequately can lead to reduced reliability, degraded performance, and even catastrophic failures.
To address these challenges, a multifaceted approach to thermal management is necessary. This includes selecting thermally favorable PCB materials, employing thermal vias and metal-core PCBs for enhanced heat spreading, incorporating heat sinks and thermal interface materials, and conducting thorough thermal simulations.
By following best practices and carefully considering thermal management throughout the design process, engineers can ensure that their RF and microwave PCBs operate reliably and maintain their intended performance characteristics. As the demands on these high-frequency systems continue to increase, effective thermal management will remain a critical aspect of successful PCB design.
No responses yet