Introduction to ThermalPad and Its Significance in Heat Management
In the world of electronic devices and systems, effective heat management is crucial for ensuring optimal performance, reliability, and longevity. One of the key components in achieving efficient thermal management is the use of custom thermal pads, also known as ThermalPads. These specialized materials play a vital role in facilitating heat transfer and dissipation, preventing overheating and potential damage to sensitive electronic components.
ThermalPads are designed to fill the gaps and irregularities between heat-generating components and heat sinks, providing a seamless thermal interface. By establishing a direct and efficient thermal connection, ThermalPads enhance the overall cooling capabilities of electronic systems, allowing for better heat dissipation and temperature regulation.
The Importance of Proper Thermal Management
Proper thermal management is essential for several reasons:
-
Performance: Overheating can significantly impact the performance of electronic components, leading to reduced efficiency, slower processing speeds, and potential system failures.
-
Reliability: Excessive heat can cause premature aging and degradation of electronic components, compromising their reliability and longevity.
-
Safety: In extreme cases, inadequate thermal management can result in overheating, posing safety risks such as fire hazards or burns to users.
-
Energy Efficiency: Efficient heat dissipation allows electronic devices to operate at optimal temperatures, reducing energy consumption and promoting overall energy efficiency.
By employing custom ThermalPads, manufacturers and designers can address these concerns and ensure that their electronic systems operate within safe temperature ranges, delivering optimal performance and reliability.
Understanding the Properties and Characteristics of ThermalPads
To effectively utilize ThermalPads in thermal management solutions, it is essential to understand their key properties and characteristics. These attributes play a crucial role in determining the suitability and performance of ThermalPads in various applications.
Thermal Conductivity
Thermal conductivity is a measure of a material’s ability to conduct heat. It is expressed in units of watts per meter-kelvin (W/mK). ThermalPads with higher thermal conductivity values are more effective at transferring heat from the source to the heat sink, resulting in better cooling performance.
The thermal conductivity of ThermalPads can vary depending on the material composition and manufacturing process. Common materials used in ThermalPads include:
- Silicone-based compounds
- Ceramic-filled materials
- Graphite-based materials
- Phase-change materials (PCMs)
Each material offers different levels of thermal conductivity, and the choice depends on the specific requirements of the application.
Thermal Resistance
Thermal resistance, measured in units of Kelvin per watt (K/W), represents the opposition to heat flow through a material. Lower thermal resistance values indicate better heat transfer capabilities. ThermalPads with low thermal resistance allow heat to pass through more easily, resulting in efficient thermal connections between components and heat sinks.
Factors that influence thermal resistance include:
- Material thickness
- Surface roughness and contact pressure
- Interfacial gaps and air pockets
Minimizing thermal resistance is crucial for achieving optimal thermal performance in electronic systems.
Conformability and Compression
ThermalPads should possess excellent conformability and compression properties to ensure proper contact and heat transfer between surfaces. Conformability refers to the ability of the ThermalPad to adapt and mold itself to the contours and irregularities of the mating surfaces, eliminating air gaps and ensuring a tight thermal interface.
Compression, on the other hand, relates to the ThermalPad’s ability to maintain its integrity and performance under applied pressure. ThermalPads with good compression properties can withstand the clamping forces necessary to maintain proper contact without excessive deformation or degradation over time.
Electrical Insulation
In many applications, ThermalPads need to provide electrical insulation between components to prevent short circuits and ensure proper functioning. ThermalPads with high dielectric strength and insulation properties are essential in such cases. These pads can effectively transfer heat while maintaining electrical isolation, protecting sensitive electronic components from damage.
Thickness and Thermal Performance
The thickness of a ThermalPad can significantly impact its thermal performance. Thinner pads generally offer lower thermal resistance and better heat transfer, as they minimize the distance heat needs to travel. However, thinner pads may not always be suitable for applications with large surface irregularities or gaps.
Thicker ThermalPads, on the other hand, can accommodate larger gaps and surface variations but may have higher thermal resistance. The optimal thickness of a ThermalPad depends on the specific application requirements, including the size of the gap, the surface roughness of the mating components, and the desired thermal performance.
Thickness (mm) | Thermal Resistance (K/W) | Gap Filling Capability |
---|---|---|
0.5 | Low | Limited |
1.0 | Moderate | Moderate |
1.5 | Higher | Good |
2.0 | Highest | Excellent |
Table 1: Relationship between ThermalPad thickness, thermal resistance, and gap-filling capability.
It is essential to consider the trade-offs between thickness, thermal resistance, and gap-filling capability when selecting a ThermalPad for a specific application.
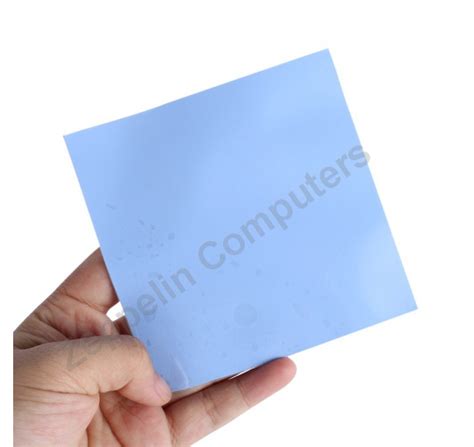
Selecting the Right ThermalPad for Your Application
Choosing the appropriate ThermalPad for your application is crucial for achieving optimal thermal management and ensuring the reliable operation of electronic components. Several factors should be considered when selecting a ThermalPad, including:
Application Requirements
- Operating temperature range
- Heat generation and dissipation requirements
- Space constraints and form factors
- Mechanical stress and vibration
Understanding the specific requirements of your application will help narrow down the suitable ThermalPad options.
Material Compatibility
- Compatibility with adjacent materials and surfaces
- Chemical stability and resistance
- Outgassing and contamination considerations
Ensuring material compatibility is essential to prevent any adverse reactions or degradation of the ThermalPad or surrounding components over time.
Thermal Performance
- Required thermal conductivity and resistance
- Gap-filling capability and conformability
- Thermal stability and long-term reliability
Selecting a ThermalPad with the appropriate thermal properties is crucial for achieving efficient heat transfer and maintaining optimal operating temperatures.
Electrical Properties
- Dielectric strength and insulation requirements
- Voltage breakdown and leakage current
- Electromagnetic interference (EMI) shielding
If electrical insulation is a concern, choose a ThermalPad with suitable dielectric properties to protect components and ensure proper functioning.
Ease of Installation and Handling
- Adhesive options (pressure-sensitive, thermally conductive adhesives)
- Cutting and shaping capabilities
- Reusability and reworkability
Consider the ease of installation and handling when selecting a ThermalPad, as it can impact manufacturing processes and maintenance procedures.
Cost and Availability
- Budget constraints and cost-effectiveness
- Availability and lead times
- Minimum order quantities and custom options
Balancing performance, cost, and availability is essential to ensure the feasibility and scalability of your thermal management solution.
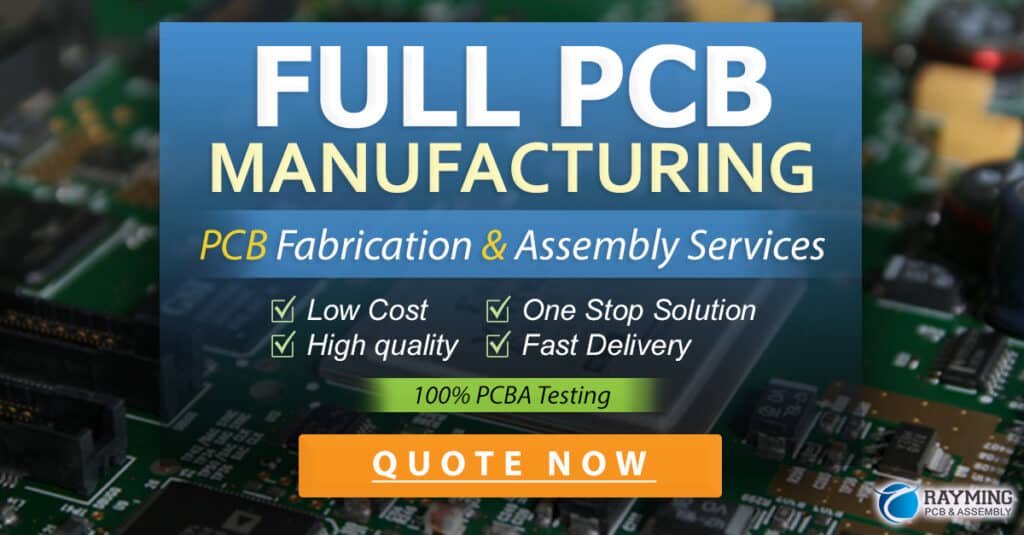
Installation and Best Practices for ThermalPads
Proper installation and handling of ThermalPads are critical for achieving optimal thermal performance and reliable operation. The following best practices should be followed:
Surface Preparation
- Clean and degrease mating surfaces to remove any contaminants or residues
- Ensure surfaces are dry and free from moisture
- Check for surface irregularities and address them if necessary
Proper surface preparation promotes better contact and adhesion between the ThermalPad and the mating surfaces.
Pad Sizing and Cutting
- Measure and select the appropriate pad size for your application
- Use sharp cutting tools or die-cutting methods for precise shapes
- Avoid stretching or deforming the pad during handling
Accurate sizing and cutting of the ThermalPad ensure proper coverage and contact with the heat-generating components and heat sinks.
Pad Placement and Alignment
- Carefully align the ThermalPad with the mating surfaces
- Ensure the pad covers the entire contact area without overhang or gaps
- Use alignment features or guides if available
Proper placement and alignment of the ThermalPad are essential for optimal heat transfer and preventing any potential short circuits or component damage.
Pressure and Compression
- Apply uniform pressure to ensure good contact between the ThermalPad and surfaces
- Follow the manufacturer’s recommended compression range
- Use appropriate clamping mechanisms or fasteners
Adequate pressure and compression help eliminate air gaps and improve the thermal interface between the ThermalPad and mating surfaces.
Thermal Grease or Adhesive Application
- If required, apply thermal grease or adhesive sparingly and evenly
- Avoid excessive application, as it can create air pockets or hinder heat transfer
- Follow the manufacturer’s guidelines for application and curing
Thermal greases or adhesives can enhance thermal conductivity and improve the bond between the ThermalPad and surfaces, but they should be used judiciously.
Post-Installation Inspection
- Visually inspect the installed ThermalPad for any signs of damage or misalignment
- Verify that the pad is making proper contact with the mating surfaces
- Check for any excess thermal grease or adhesive that may have squeezed out
Post-installation inspection helps identify any issues that may impact the thermal performance or reliability of the system.
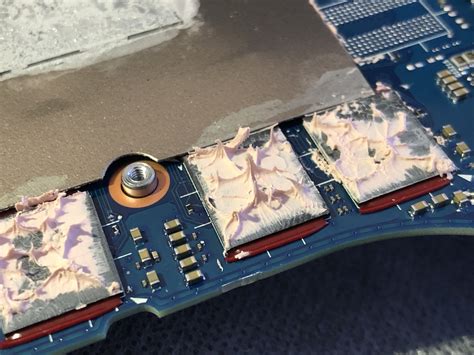
Maintenance and Replacement Considerations
Over time, ThermalPads may degrade or lose their effectiveness due to various factors such as aging, contamination, or mechanical stress. Regular maintenance and timely replacement are necessary to ensure consistent thermal performance and prevent potential failures.
Monitoring Thermal Performance
- Regularly check the operating temperatures of critical components
- Use thermal imaging or temperature sensors to identify hot spots or anomalies
- Compare thermal performance against baseline measurements or specifications
Monitoring thermal performance helps detect any degradation or issues with the ThermalPads and enables proactive maintenance or replacement.
Cleaning and Reapplication
- Periodically clean the mating surfaces and ThermalPads to remove any dirt or contaminants
- Replace ThermalPads that show signs of wear, damage, or hardening
- Follow proper installation procedures when reapplying ThermalPads
Regular cleaning and reapplication of ThermalPads maintain optimal thermal conductivity and prevent any potential failures due to contamination or degradation.
Replacement Intervals
- Establish replacement intervals based on the application and operating conditions
- Consider factors such as temperature cycling, vibration, and environmental exposure
- Follow the manufacturer’s recommendations for replacement intervals
Proactive replacement of ThermalPads at appropriate intervals ensures consistent thermal performance and minimizes the risk of unexpected failures.
Proper Disposal and Environmental Considerations
- Follow local regulations and guidelines for the disposal of used ThermalPads
- Consider recycling options or proper disposal methods to minimize environmental impact
- Consult with the manufacturer or supplier for specific disposal recommendations
Proper disposal of ThermalPads helps protect the environment and ensures compliance with relevant regulations.
Advanced ThermalPad Technologies and Future Trends
As electronic devices continue to evolve and become more powerful, the demand for advanced thermal management solutions, including ThermalPads, is on the rise. Manufacturers and researchers are continuously developing new technologies and materials to enhance the performance and capabilities of ThermalPads.
High-Performance Materials
- Novel filler materials with enhanced thermal conductivity
- Carbon nanotubes and graphene-based composites
- Hybrid materials combining different filler types
Advanced materials with improved thermal properties enable the development of ThermalPads with higher thermal conductivity and lower thermal resistance.
Phase-Change Materials (PCMs)
- Materials that change phase (solid to liquid) at specific temperatures
- Absorb and release heat during phase transition
- Provide efficient heat spreading and temperature regulation
PCMs offer unique thermal management capabilities by leveraging the latent heat of phase change to maintain stable operating temperatures.
Anisotropic Thermal Conductivity
- Materials with directional thermal conductivity properties
- Higher thermal conductivity in the vertical direction (through-plane)
- Enables efficient heat transfer from the source to the heat sink
Anisotropic ThermalPads optimize heat transfer in the desired direction while minimizing lateral heat spread, enhancing overall thermal management efficiency.
Thin and Ultra-thin Form Factors
- Development of thinner ThermalPads with maintained or improved thermal performance
- Enables application in compact and space-constrained electronic devices
- Facilitates the design of slimmer and more portable devices
Thin and ultra-thin ThermalPads address the growing demand for thermal management solutions in increasingly miniaturized electronic systems.
Integrated Sensors and Monitoring
- Incorporation of temperature sensors or thermocouples within ThermalPads
- Real-time monitoring of thermal performance and temperature distribution
- Enables adaptive thermal management and early detection of anomalies
Integrated sensors and monitoring capabilities in ThermalPads provide valuable data for optimizing thermal management strategies and ensuring reliable operation.
As technology advances, it is expected that ThermalPads will continue to evolve, offering enhanced thermal performance, innovative materials, and integrated features to meet the ever-growing demands of electronic systems.
Frequently Asked Questions (FAQ)
-
Q: What is a ThermalPad, and how does it differ from thermal paste or grease?
A: A ThermalPad is a pre-cut, solid material designed to fill the gaps between heat-generating components and heat sinks, providing efficient thermal transfer. Unlike thermal paste or grease, which are applied in liquid or semi-liquid form, ThermalPads are solid and offer a more convenient and less messy installation process. -
Q: Can ThermalPads be cut or resized to fit specific applications?
A: Yes, ThermalPads can often be cut or resized to fit specific applications. However, it is important to use sharp cutting tools and avoid stretching or deforming the pad during the process. Some manufacturers offer custom-sized ThermalPads or die-cutting services for precise shapes and dimensions. -
Q: How do I choose the right thickness for a ThermalPad?
A: The optimal thickness of a ThermalPad depends on the specific application requirements. Thinner pads generally offer lower thermal resistance and better heat transfer but may not adequately fill larger gaps or surface irregularities. Thicker pads can accommodate larger gaps but may have higher thermal resistance. Consider factors such as gap size, surface roughness, and desired thermal performance when selecting the appropriate thickness. -
Q: Are ThermalPads reusable, or do they need to be replaced after each application?
A: The reusability of ThermalPads varies depending on the specific material and design. Some ThermalPads are designed for single use and should be replaced after each application to ensure optimal thermal performance. Others may be reusable to a certain extent, but their effectiveness may diminish over time due to contamination, wear, or compression set. It is generally recommended to follow the manufacturer’s guidelines regarding reusability and replacement intervals. -
Q: Can ThermalPads be used in conjunction with thermal grease or adhesives?
A: In some cases, ThermalPads can be used in conjunction with thermal grease or thermally conductive adhesives to enhance thermal conductivity and improve the bond between the pad and mating surfaces. However, it is important to use these additional materials sparingly and follow the manufacturer’s guidelines for application and compatibility. Excessive use of thermal grease or adhesives can create air pockets or hinder heat transfer, negatively impacting thermal performance.
Conclusion
ThermalPads play a crucial role in the thermal management of electronic devices and systems, providing efficient and reliable heat transfer solutions. By understanding the properties, selection criteria, installation best practices, and maintenance considerations of ThermalPads, designers and engineers can optimize the thermal performance and reliability of their products.
As electronic systems continue to advance and become more complex, the development of innovative ThermalPad technologies and materials will be essential to meet the evolving thermal management challenges. From high-performance materials and phase-change compounds to thin and ultra-thin form factors, the future of ThermalPads holds exciting possibilities for enhanced thermal conductivity, adaptability, and integration.
By staying informed about the latest advancements in ThermalPad technologies and adopting best practices for their application and maintenance, manufacturers can ensure that their electronic devices operate at optimal temperatures, delivering reliable performance and long-term durability.
No responses yet