Introduction to PCB Layout
Printed Circuit Board (PCB) layout design is a crucial step in the development of electronic devices. It involves the arrangement of components and the routing of traces on a PCB to ensure proper functionality, reliability, and manufacturability. In this comprehensive guide, we will delve into the intricacies of PCB layout design, covering essential concepts, best practices, and tips to help you create high-quality PCB layouts.
Understanding the Basics of PCB Layout
Before we dive into the specifics of PCB layout design, let’s review some fundamental concepts:
1. PCB Layers
PCBs can have multiple layers, depending on the complexity of the design. The most common layer configurations are:
- Single-layer PCB: Components and traces are placed on one side of the board.
- Double-layer PCB: Components are placed on both sides, with traces connecting them through vias.
- Multi-layer PCB: Additional layers are added between the top and bottom layers for more complex routing.
2. Component Placement
Proper component placement is essential for optimal PCB performance. Consider the following factors:
- Group related components together to minimize trace lengths and improve signal integrity.
- Place sensitive components away from sources of noise, such as power supplies or high-speed signals.
- Ensure adequate spacing between components for ease of assembly and thermal management.
3. Trace Routing
Trace routing involves connecting components using conductive paths called traces. Keep these guidelines in mind:
- Use appropriate trace widths based on the current carrying capacity and signal requirements.
- Maintain proper spacing between traces to minimize crosstalk and interference.
- Avoid sharp angles and use smooth curves to improve signal integrity.
PCB Layout Design Workflow
A typical PCB layout design workflow consists of the following steps:
-
Schematic Design: Create a schematic diagram that represents the electrical connections between components.
-
Component Placement: Arrange components on the PCB based on the schematic and design requirements.
-
Trace Routing: Connect components using traces, following the schematic and adhering to design rules.
-
Design Rule Check (DRC): Verify that the layout complies with the specified design rules to ensure manufacturability.
-
Gerber File Generation: Generate Gerber files, which are industry-standard files used for PCB fabrication.
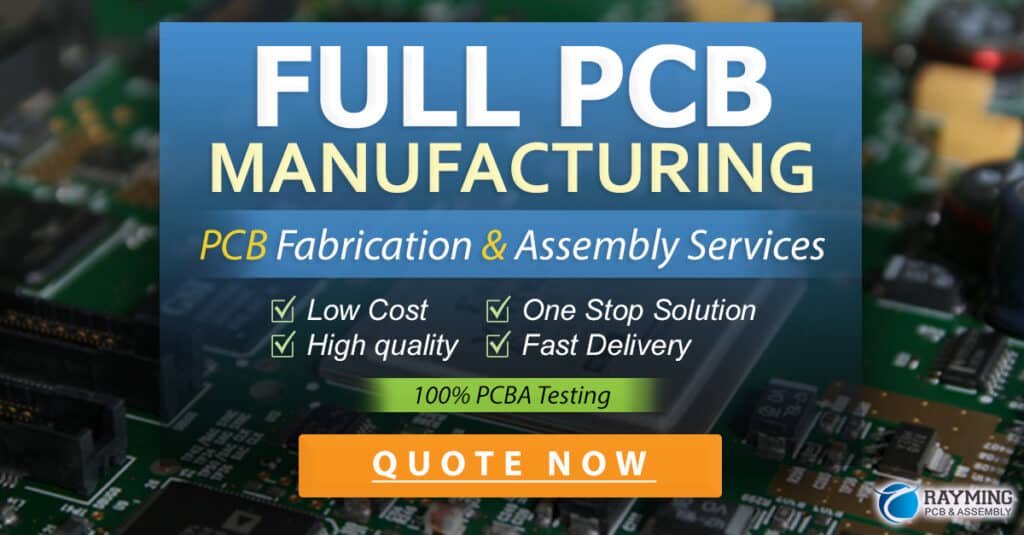
Best Practices for PCB Layout Design
To create robust and reliable PCB layouts, consider the following best practices:
1. Ground Plane
Use a solid ground plane to provide a low-impedance return path for signals and reduce electromagnetic interference (EMI). This helps maintain signal integrity and improves overall performance.
2. Power Distribution
Properly distribute power throughout the PCB to ensure stable and clean power delivery to components. Use appropriate trace widths and consider adding decoupling capacitors near power-hungry components.
3. Signal Integrity
Maintain signal integrity by minimizing crosstalk, reflections, and noise. Some techniques include:
- Impedance matching: Match the impedance of traces to the source and load impedances to minimize reflections.
- Differential pairs: Use differential signaling for high-speed signals to cancel out common-mode noise.
- Shielding: Use shielding techniques, such as ground planes or guard traces, to isolate sensitive signals.
4. Thermal Management
Consider thermal management during PCB layout design to ensure proper heat dissipation. Place heat-generating components strategically and use thermal reliefs or heat sinks when necessary.
5. Manufacturing Considerations
Keep manufacturing considerations in mind during the layout process. Adhere to the fabrication house’s design rules, such as minimum trace widths, clearances, and hole sizes. This ensures that your PCB can be reliably manufactured.
Advanced PCB Layout Techniques
For more complex designs, consider these advanced PCB layout techniques:
1. High-Speed Design
When designing high-speed circuits, pay special attention to signal integrity and timing. Some key considerations include:
- Impedance control: Use controlled impedance traces to maintain signal integrity and minimize reflections.
- Length matching: Match the lengths of critical signals to ensure proper timing and synchronization.
- Termination: Use appropriate termination techniques, such as series or parallel termination, to minimize reflections.
2. RF and Microwave Design
RF and Microwave PCB layouts require special considerations due to the high frequencies involved. Some important aspects include:
- Impedance matching: Ensure proper impedance matching throughout the RF signal path to minimize reflections and power loss.
- Grounding: Use a solid ground plane and provide adequate grounding for RF components.
- Shielding: Implement shielding techniques to minimize electromagnetic interference (EMI) and crosstalk.
3. Flex and Rigid-Flex PCBs
Flex and rigid-flex PCBs offer unique advantages in terms of flexibility and space savings. When designing these types of PCBs, consider:
- Bend radius: Ensure that the bend radius of the flexible portions is within the manufacturer’s specifications.
- Stiffeners: Use stiffeners in areas where components are mounted to provide mechanical support.
- Strain relief: Incorporate strain relief features to prevent damage to the flexible portions during use.
PCB Layout Tools and Software
There are various PCB layout tools and software available to streamline the design process. Some popular options include:
- Altium Designer
- Cadence OrCAD
- KiCad
- Eagle PCB
These tools offer features such as schematic capture, component libraries, auto-routing, and design rule checking to assist in creating efficient and reliable PCB layouts.
Table: Common PCB Layer Stackups
Layers | Stackup | Applications |
---|---|---|
2 | Signal – Ground | Simple, low-cost designs |
4 | Signal – Ground – Power – Signal | Moderate complexity, improved power distribution |
6 | Signal – Ground – Power – Ground – Power – Signal | Complex designs, better signal integrity |
8+ | Multiple signal, power, and ground layers | High-speed, high-density designs |
Frequently Asked Questions (FAQ)
- What is the difference between a schematic and a PCB layout?
-
A schematic is a graphical representation of the electrical connections between components, while a PCB layout is the physical arrangement of components and traces on a PCB.
-
How do I choose the appropriate trace width for my PCB layout?
-
Trace width depends on factors such as the current carrying capacity, signal frequency, and PCB fabrication capabilities. Consult trace width calculators or follow the manufacturer’s guidelines to determine the appropriate width.
-
What is the purpose of a ground plane in a PCB layout?
-
A ground plane provides a low-impedance return path for signals, reduces electromagnetic interference (EMI), and improves overall signal integrity.
-
How can I minimize crosstalk in my PCB layout?
-
To minimize crosstalk, use proper trace spacing, route sensitive signals away from noisy signals, use ground planes for shielding, and consider techniques like differential signaling.
-
What are the common file formats used for PCB fabrication?
- Gerber files (RS-274X) are the industry-standard file format used for PCB fabrication. Other common formats include ODB++ and IPC-2581.
Conclusion
PCB layout design is a critical aspect of electronic product development. By understanding the basics, following best practices, and utilizing advanced techniques when necessary, you can create robust and reliable PCB layouts. Remember to consider factors such as component placement, trace routing, signal integrity, and manufacturability throughout the design process.
With the knowledge gained from this ultimate guide to PCB layout design, you are well-equipped to tackle your next PCB design project with confidence. Happy designing!
No responses yet