What is Industrial IoT?
Industrial Internet of Things (IIoT) refers to the application of Internet of Things (IoT) technologies in industrial sectors and applications. It encompasses the use of smart sensors, actuators, and other devices to collect and analyze data from industrial equipment and processes, enabling real-time monitoring, predictive maintenance, and optimization of industrial operations.
IIoT leverages advanced technologies such as:
- Machine-to-Machine (M2M) communication
- Big Data analytics
- Artificial Intelligence (AI) and Machine Learning (ML)
- Cloud computing
- Edge computing
- Wireless sensor networks
These technologies enable the creation of smart factories and intelligent manufacturing systems that can improve efficiency, productivity, and safety while reducing costs and downtime.
Key Components of Industrial IoT
-
Sensors and Actuators: These devices collect data from industrial equipment and processes and enable real-time monitoring and control.
-
Connectivity: IIoT relies on robust and secure communication networks, such as Wi-Fi, Bluetooth, Zigbee, and cellular networks (4G/5G), to transmit data between devices and to the cloud.
-
Edge Computing: Edge devices process data locally, reducing latency and bandwidth requirements while enabling real-time decision-making.
-
Cloud Platforms: Cloud-based IIoT platforms provide scalable storage, processing power, and analytics capabilities for large volumes of industrial data.
-
Data Analytics: Advanced analytics tools, including AI and ML algorithms, help extract valuable insights from industrial data to optimize processes, predict maintenance needs, and improve decision-making.
Benefits of Industrial IoT for Manufacturers
Implementing IIoT solutions offers numerous benefits for manufacturers, including:
-
Increased Operational Efficiency: IIoT enables real-time monitoring and optimization of industrial processes, leading to improved efficiency and reduced waste.
-
Predictive Maintenance: By analyzing sensor data, IIoT systems can predict equipment failures before they occur, minimizing downtime and maintenance costs.
-
Enhanced Product Quality: Real-time monitoring and analytics help identify and address quality issues quickly, resulting in higher-quality products and reduced scrap rates.
-
Improved Safety: IIoT solutions can monitor environmental conditions and worker safety, alerting personnel to potential hazards and reducing the risk of accidents.
-
Better Decision-Making: Access to real-time data and advanced analytics enables informed, data-driven decision-making at all levels of the organization.
-
Increased Agility: IIoT facilitates faster response times to market demands, supply chain disruptions, and other challenges, improving overall agility and competitiveness.
Real-World Examples of IIoT in Manufacturing
Company | IIoT Application | Benefits |
---|---|---|
Siemens | Predictive maintenance for wind turbines | Reduced downtime, increased energy production |
Bosch | Connected factory for real-time monitoring and optimization | Improved efficiency, reduced costs, enhanced product quality |
GE | Asset performance management for industrial equipment | Increased equipment reliability, optimized maintenance schedules |
Schneider Electric | Energy management and optimization for manufacturing facilities | Reduced energy consumption, lower costs, improved sustainability |
ABB | Remote monitoring and control of robotics systems | Enhanced productivity, reduced downtime, improved safety |
Challenges and Considerations for Implementing IIoT
While IIoT offers significant benefits, manufacturers must also navigate various challenges and considerations when implementing these solutions:
1. Cybersecurity
As IIoT systems connect more devices and generate vast amounts of data, the risk of cyber attacks increases. Manufacturers must prioritize cybersecurity measures, such as:
- Secure communication protocols
- Data encryption
- Access control and authentication
- Regular security audits and patches
2. Interoperability and Standards
The lack of standardization in IIoT can lead to interoperability issues between devices and systems from different vendors. Manufacturers should consider adopting open standards and protocols, such as:
- OPC Unified Architecture (OPC UA)
- Message Queuing Telemetry Transport (MQTT)
- Data Distribution Service (DDS)
3. Legacy Equipment Integration
Many manufacturing facilities have older equipment that may not be compatible with IIoT technologies. Manufacturers must develop strategies for integrating legacy systems, such as:
- Retrofitting sensors and communication devices
- Implementing gateway solutions for protocol translation
- Gradually replacing outdated equipment with IIoT-enabled devices
4. Data Management and Analytics
IIoT generates massive amounts of data, which can be challenging to manage, store, and analyze effectively. Manufacturers should invest in:
- Scalable data storage solutions, such as cloud platforms or data lakes
- Advanced analytics tools, including AI and ML algorithms
- Data governance policies to ensure data quality, security, and compliance
5. Skill Gap and Workforce Training
Implementing IIoT requires a workforce with the necessary skills and knowledge. Manufacturers must address the skill gap by:
- Providing training and education programs for existing employees
- Collaborating with educational institutions to develop relevant curricula
- Attracting and retaining talent with IIoT expertise
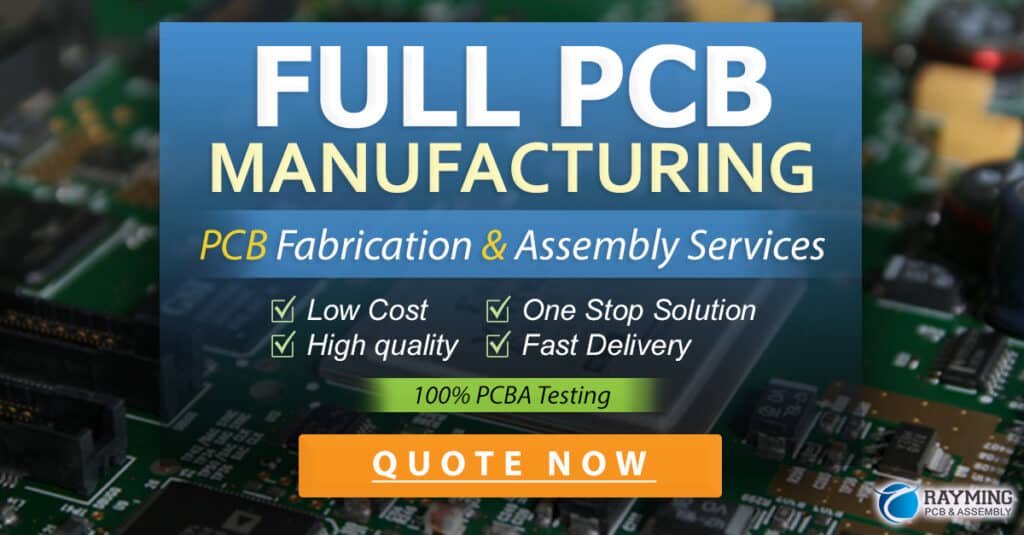
Best Practices for Successful IIoT Implementation
To ensure a successful IIoT implementation, manufacturers should follow these best practices:
-
Define Clear Objectives: Identify specific business goals and use cases for IIoT, ensuring alignment with overall organizational strategy.
-
Start Small and Scale Gradually: Begin with pilot projects to validate IIoT concepts and benefits before scaling up to full implementation.
-
Choose the Right Partners: Collaborate with experienced IIoT solution providers, system integrators, and technology vendors who understand your industry and specific needs.
-
Prioritize Data Security: Implement robust cybersecurity measures, such as encryption, access control, and regular security audits, to protect industrial data and systems.
-
Invest in Employee Training: Provide comprehensive training programs to ensure your workforce has the necessary skills to operate and maintain IIoT systems effectively.
-
Establish Data Governance: Develop policies and procedures for data collection, storage, analysis, and sharing to ensure data quality, consistency, and compliance with regulations.
-
Continuously Monitor and Optimize: Regularly assess the performance of your IIoT systems, using data insights to drive continuous improvement and optimization of industrial processes.
Future Trends in Industrial IoT
As IIoT continues to evolve, several key trends are shaping the future of industrial manufacturing:
-
5G and Edge Computing: The widespread adoption of 5G networks and edge computing will enable faster, more reliable data transmission and real-time processing, unlocking new IIoT applications and use cases.
-
Artificial Intelligence and Machine Learning: AI and ML will play an increasingly important role in IIoT, enabling advanced analytics, predictive maintenance, and autonomous decision-making.
-
Digital Twins: The use of digital twins, virtual replicas of physical assets and processes, will become more prevalent, allowing manufacturers to simulate and optimize industrial operations in real-time.
-
Blockchain Integration: The integration of blockchain technology with IIoT will enable secure, tamper-proof data sharing and transactions between devices and stakeholders, improving trust and transparency in industrial ecosystems.
-
Augmented Reality and Virtual Reality: AR and VR technologies will be increasingly used in IIoT for remote assistance, training, and visualization of complex industrial processes.
Frequently Asked Questions (FAQ)
-
What is the difference between IoT and IIoT?
IoT refers to the general concept of connecting devices to the internet, while IIoT specifically focuses on the application of IoT technologies in industrial sectors, such as manufacturing, energy, and transportation. -
How does IIoT improve energy efficiency in manufacturing?
IIoT solutions can monitor energy consumption, identify inefficiencies, and optimize energy usage in real-time, leading to reduced costs and improved sustainability. For example, smart sensors can detect and adjust lighting, temperature, and equipment settings based on occupancy and production needs. -
What are the key challenges in implementing IIoT in legacy manufacturing environments?
The main challenges include the lack of compatibility between older equipment and IIoT technologies, the need for significant investments in infrastructure and training, and potential disruptions to existing processes during implementation. -
How can manufacturers ensure the security of their IIoT systems?
Manufacturers should adopt a multi-layered approach to cybersecurity, including secure communication protocols, data encryption, access control, and regular security audits. They should also work closely with IIoT solution providers to ensure the implementation of best practices and timely security updates. -
What skills are required for a successful IIoT implementation in manufacturing?
A successful IIoT implementation requires a combination of technical skills (e.g., data analytics, cybersecurity, and network management) and domain expertise in manufacturing processes. Manufacturers should invest in training programs to upskill their existing workforce and attract new talent with IIoT-related competencies.
Conclusion
Industrial IoT is transforming the manufacturing landscape, enabling smart factories, predictive maintenance, and optimized production processes. By leveraging advanced technologies such as AI, edge computing, and 5G networks, manufacturers can improve operational efficiency, product quality, and safety while reducing costs and downtime.
However, successful IIoT implementation requires careful planning, investment, and collaboration with experienced partners. Manufacturers must prioritize cybersecurity, data governance, and workforce training to ensure a smooth and secure transition to IIoT-enabled operations.
As the technology continues to evolve, manufacturers that embrace IIoT and adapt to emerging trends will be well-positioned to remain competitive in the increasingly connected and data-driven industrial landscape.
No responses yet