What is FR4 PCB?
FR4, or Flame Retardant 4, is a type of printed circuit board (PCB) material that is widely used in the electronics industry. It is a composite material made of woven fiberglass cloth with an epoxy resin binder that is flame resistant. FR4 PCBs are known for their excellent mechanical, electrical, and thermal properties, making them suitable for a wide range of applications.
Composition of FR4 PCB
FR4 PCBs are made up of several layers of materials, including:
-
Copper foil: This is the conductive layer that carries electrical signals and forms the circuit patterns on the PCB.
-
Prepreg: Short for “pre-impregnated,” this is a layer of fiberglass cloth that has been pre-impregnated with a partially cured epoxy resin. It acts as an insulating layer between the copper foil layers.
-
Core: This is a fully cured fiberglass-epoxy laminate that provides rigidity and stability to the PCB.
The number of layers in an FR4 PCB can vary depending on the complexity of the circuit design. The most common configurations are:
Layers | Description |
---|---|
1 | Single-sided PCB with components on one side |
2 | Double-sided PCB with components on both sides |
4 | Four-layer PCB with two internal copper layers |
6-12 | Multi-layer PCBs for complex designs |
Properties of FR4 PCB
FR4 PCBs have several desirable properties that make them a popular choice for electronic applications:
-
High mechanical strength: FR4 has excellent tensile, flexural, and impact strength, making it resistant to vibration and shock.
-
Flame retardancy: The epoxy resin used in FR4 is self-extinguishing, which helps prevent the spread of flames in case of a fire.
-
Electrical insulation: FR4 has a high dielectric strength and provides excellent electrical insulation between conductive layers.
-
Thermal stability: FR4 has a glass transition temperature (Tg) of around 130°C to 140°C, meaning it can withstand high temperatures without deforming.
-
Moisture resistance: FR4 has low moisture absorption, which helps prevent delamination and other moisture-related issues.
Applications of FR4 PCB
FR4 PCBs are used in a wide range of electronic applications, including:
Consumer Electronics
FR4 PCBs are commonly used in consumer electronics such as:
- Smartphones
- Tablets
- Laptops
- Televisions
- Home appliances
These devices require PCBs that are reliable, cost-effective, and capable of handling high-speed signals.
Industrial Electronics
FR4 PCBs are also used in industrial electronics applications, such as:
- Motor controllers
- Power supplies
- Sensors
- Automation systems
These applications often require PCBs that can withstand harsh environmental conditions, such as high temperatures, vibration, and humidity.
Automotive Electronics
FR4 PCBs are used in various automotive electronic systems, including:
- Engine control units (ECUs)
- Infotainment systems
- Advanced driver assistance systems (ADAS)
- Body control modules
Automotive PCBs must meet stringent reliability and safety requirements, as well as be able to operate in extreme temperature ranges.
Medical Devices
FR4 PCBs are used in medical devices such as:
- Patient monitors
- Diagnostic equipment
- Imaging systems
- Implantable devices
Medical PCBs must meet strict regulatory requirements for safety, reliability, and biocompatibility.
Manufacturing Process of FR4 PCB
The manufacturing process of FR4 PCBs involves several steps:
-
Design: The PCB layout is designed using computer-aided design (CAD) software, taking into account the circuit requirements, component placement, and manufacturing constraints.
-
Fabrication: The PCB is fabricated by laminating the copper foil, prepreg, and core layers together under high temperature and pressure. The copper layers are then patterned using photolithography and etching processes.
-
Drilling: Holes are drilled through the PCB to allow for component mounting and electrical interconnections between layers.
-
Plating: The drilled holes are plated with copper to create electrical connections between layers.
-
Solder mask application: A solder mask layer is applied to the PCB surface to protect the copper traces and prevent short circuits during soldering.
-
Silkscreen printing: Text and symbols are printed on the PCB surface using silkscreen printing to aid in component placement and identification.
-
Surface finishing: A surface finish, such as HASL (hot air solder leveling), ENIG (electroless nickel immersion gold), or OSP (organic solderability preservative), is applied to the exposed copper areas to improve solderability and protect against oxidation.
-
Testing: The finished PCB is tested for electrical continuity, insulation resistance, and other quality control measures to ensure it meets the required specifications.
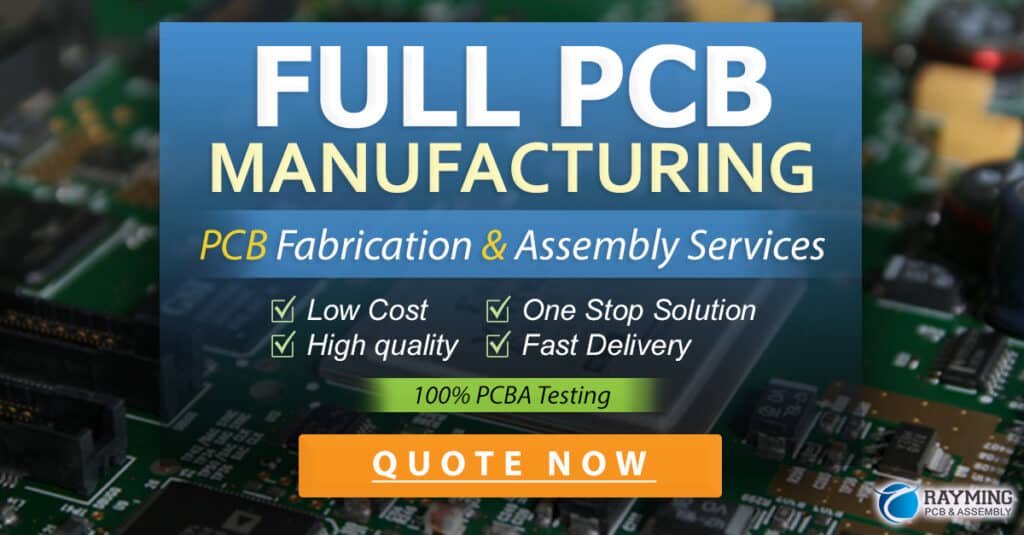
Advantages of FR4 PCB
FR4 PCBs offer several advantages over other PCB materials:
-
Cost-effectiveness: FR4 is relatively inexpensive compared to other PCB materials, making it a cost-effective choice for many applications.
-
Wide availability: FR4 is widely available from many suppliers, ensuring a stable supply chain for PCB manufacturers.
-
Versatility: FR4 can be used in a wide range of applications, from simple single-layer boards to complex multi-layer designs.
-
Reliability: FR4 has proven reliability in various environmental conditions, making it suitable for use in harsh industrial and automotive applications.
-
Easy processing: FR4 is easy to drill, cut, and machine, which simplifies the PCB manufacturing process.
Disadvantages of FR4 PCB
Despite its many advantages, FR4 PCBs also have some limitations:
-
Limited high-frequency performance: FR4 has a relatively high dielectric constant and dissipation factor, which can limit its performance in high-frequency applications above a few gigahertz.
-
Thermal expansion mismatch: The coefficient of thermal expansion (CTE) of FR4 is higher than that of copper, which can lead to thermal stress and delamination in high-temperature applications.
-
Moisture absorption: Although FR4 has low moisture absorption compared to other PCB materials, it can still absorb moisture over time, which can lead to delamination and other reliability issues.
Future Trends in FR4 PCB
As electronic devices continue to become more complex and sophisticated, the demand for high-performance PCBs will continue to grow. Some of the future trends in FR4 PCB technology include:
-
High-speed materials: The development of new FR4 variants with lower dielectric constants and dissipation factors will enable higher-speed applications, such as 5G wireless communication and high-speed data transfer.
-
Embedded components: The integration of passive components, such as resistors and capacitors, into the PCB substrate will help reduce board size and improve signal integrity.
-
Advanced manufacturing processes: The adoption of new manufacturing technologies, such as additive manufacturing and laser drilling, will enable more complex and high-density PCB designs.
-
Environmental sustainability: There will be a growing focus on developing more environmentally friendly PCB materials and manufacturing processes, such as halogen-free flame retardants and lead-free solders.
FAQ
1. What is the difference between FR4 and other PCB materials?
FR4 is a composite material made of woven fiberglass cloth with an epoxy resin binder, while other PCB materials may use different reinforcement fibers or resin systems. FR4 offers a good balance of mechanical, electrical, and thermal properties at a relatively low cost, making it a popular choice for many applications.
2. Can FR4 PCBs be used for high-frequency applications?
FR4 PCBs can be used for high-frequency applications up to a few gigahertz, but their performance may be limited by their relatively high dielectric constant and dissipation factor. For higher-frequency applications, specialized PCB materials with lower loss tangents, such as Rogers or Teflon, may be required.
3. How many layers can an FR4 PCB have?
FR4 PCBs can have anywhere from one to over 20 layers, depending on the complexity of the circuit design. However, the most common configurations are single-sided, double-sided, and four-layer boards.
4. What surface finishes are available for FR4 PCBs?
Common surface finishes for FR4 PCBs include HASL (hot air solder leveling), ENIG (electroless nickel immersion gold), OSP (organic solderability preservative), and immersion tin or silver. The choice of surface finish depends on the specific application requirements, such as solderability, shelf life, and cost.
5. How can I ensure the reliability of my FR4 PCB design?
To ensure the reliability of your FR4 PCB design, consider the following factors:
- Use appropriate design rules and guidelines for your specific application and manufacturing process
- Specify the correct material grade and thickness for your requirements
- Use appropriate surface finishes and solder mask materials
- Follow good design practices for signal integrity, power distribution, and thermal management
- Perform thorough testing and quality control measures during the manufacturing process
By following these guidelines and working closely with your PCB manufacturer, you can ensure that your FR4 PCB design will meet your performance and reliability requirements.
No responses yet