What is an LED PCB?
An LED PCB, or Light Emitting Diode Printed Circuit Board, is a specialized circuit board designed to efficiently power and control LED lights. These boards are crucial components in various applications, from simple indicator lights to complex LED displays and lighting systems.
LED PCBs are manufactured using a combination of standard PCB production techniques and specific design considerations to optimize the performance and longevity of the connected LEDs. They are engineered to provide the necessary electrical current, heat dissipation, and mechanical support for the LEDs.
Key components of an LED PCB
- Substrate material: The base material of the PCB, typically FR-4, aluminum, or flexible substrates like polyimide.
- Copper traces: Conductive paths that carry electrical current to the LEDs.
- Solder mask: A protective layer that covers the copper traces, preventing short circuits and oxidation.
- Silkscreen: Text and symbols printed on the PCB for identification and assembly guidance.
- LED pads: Designated areas where the LEDs are soldered to the board.
- Thermal management features: Heat sinks, thermal vias, or metal core PCBs (MCPCBs) that help dissipate heat generated by the LEDs.
Advantages of using LED PCBs
Energy efficiency
LEDs are known for their high energy efficiency compared to traditional lighting sources. By using LED PCBs, you can create lighting solutions that consume less power, resulting in lower energy costs and a reduced environmental impact.
Longevity
LEDs have a significantly longer lifespan than other lighting technologies. When properly designed and manufactured, LED PCBs can support the long-term operation of LEDs, minimizing the need for frequent replacements and maintenance.
Customization
LED PCBs can be customized to suit specific application requirements. Designers can create boards with unique shapes, sizes, and layouts to accommodate various LED configurations and control circuitry.
Improved heat dissipation
Proper thermal management is crucial for the performance and longevity of LEDs. LED PCBs often incorporate thermal management features, such as metal core substrates or thermal vias, which help dissipate heat more effectively, ensuring optimal LED performance.
Designing an LED PCB
Design considerations
When designing an LED PCB, several key factors must be considered:
- LED type and configuration: Select the appropriate LED package (e.g., SMD, COB) and determine the desired layout and spacing of the LEDs on the board.
- Current and voltage requirements: Ensure that the PCB can provide the necessary current and voltage to drive the LEDs efficiently.
- Thermal management: Incorporate thermal management features to dissipate heat generated by the LEDs, preventing performance degradation and premature failure.
- Control circuitry: Integrate the necessary control components, such as drivers and microcontrollers, to manage LED operation and dimming.
- Manufacturing constraints: Consider the limitations of the PCB manufacturing process, such as minimum trace widths, hole sizes, and clearances.
PCB layout guidelines
To create an efficient and reliable LED PCB layout, follow these guidelines:
- Minimize trace lengths: Keep the copper traces between the power source and the LEDs as short as possible to reduce voltage drop and power loss.
- Optimize current distribution: Ensure that the current is evenly distributed among the LEDs by using appropriate trace widths and thicknesses.
- Avoid high-current density: Prevent excessive current density in traces and vias, which can lead to overheating and potential failure.
- Implement proper grounding: Use appropriate grounding techniques, such as ground planes and star grounding, to minimize noise and ensure stable LED operation.
- Consider EMI and ESD protection: Incorporate electromagnetic interference (EMI) and electrostatic discharge (ESD) protection measures to safeguard the LEDs and control circuitry.
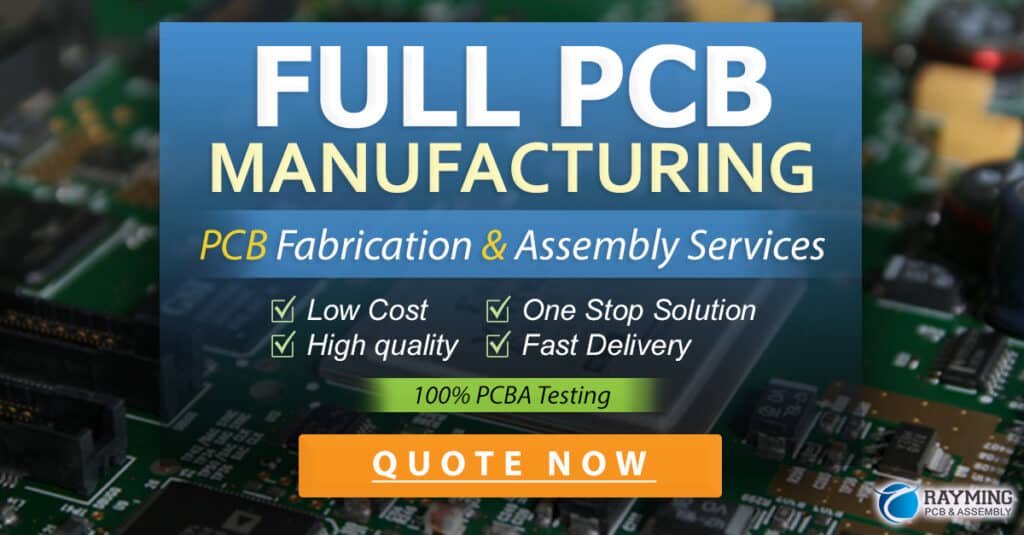
Manufacturing LED PCBs
PCB fabrication process
The LED PCB fabrication process involves several steps:
- PCB design: The PCB layout is designed using specialized software, adhering to the design considerations and guidelines mentioned earlier.
- Material selection: The appropriate substrate material, copper weight, and solder mask are chosen based on the application requirements.
- Printing and etching: The PCB design is printed onto the substrate, and the unwanted copper is etched away, leaving the desired traces and pads.
- Drilling and plating: Holes are drilled for through-hole components, and the holes are plated with copper to ensure electrical conductivity.
- Solder mask and silkscreen application: The solder mask is applied to protect the copper traces, and the silkscreen is added for identification and assembly guidance.
- Surface finish: A surface finish, such as HASL, ENIG, or OSP, is applied to the exposed copper to prevent oxidation and enhance solderability.
LED assembly techniques
After the PCB fabrication is complete, the LEDs are assembled onto the board using one of the following techniques:
- Through-hole assembly: LEDs with long leads are inserted into drilled holes and soldered onto the PCB.
- Surface-mount assembly: Surface-mount device (SMD) LEDs are placed onto designated pads and soldered using reflow or wave soldering processes.
- Chip-on-board (COB) assembly: LED chips are directly bonded onto the PCB substrate, offering high-density packaging and improved thermal performance.
Applications of LED PCBs
LED PCBs find applications in various industries and products, such as:
- Automotive lighting: Headlights, taillights, and interior lighting in vehicles.
- General illumination: Residential, commercial, and industrial lighting fixtures.
- Backlighting: LCD displays, signs, and instrument panels.
- Stage and entertainment lighting: Theater, concert, and event lighting.
- Medical devices: Endoscopes, surgical lamps, and phototherapy equipment.
- Horticulture: Grow lights for indoor and greenhouse cultivation.
- Signage and advertising: LED billboards, channel letters, and digital signage.
Troubleshooting and maintenance
Common issues and solutions
- LED flickering or dimming: Check for loose connections, inadequate power supply, or faulty control circuitry.
- Overheating: Ensure proper thermal management, including adequate heat sinking and ventilation.
- Color inconsistency: Verify that the LEDs are sourced from the same bin and that the current is evenly distributed across the board.
- Premature failure: Investigate potential issues with power supply, thermal management, or environmental factors like humidity and vibration.
Maintenance tips
- Regularly inspect the LED PCB for signs of damage, corrosion, or loose connections.
- Clean the PCB and LEDs with a soft, dry brush or compressed air to remove dust and debris.
- Ensure that the ambient temperature and humidity levels are within the specified range for the LED PCB.
- Follow the manufacturer’s guidelines for power cycling and dimming to minimize stress on the LEDs and control circuitry.
Future trends in LED PCB technology
- Miniaturization: Advancements in LED packaging and PCB manufacturing technologies will enable smaller, more compact LED PCB designs.
- Flexible and stretchable PCBs: The development of flexible and stretchable substrate materials will allow for the creation of conformable LED PCBs for wearable and unconventional applications.
- Smart LED systems: The integration of wireless connectivity, sensors, and microcontrollers will enable intelligent LED lighting systems that can adapt to user preferences and environmental conditions.
- Sustainable materials: The use of eco-friendly, biodegradable, and recyclable materials in LED PCB production will become more prevalent as the industry focuses on sustainability.
Frequently Asked Questions (FAQ)
-
What is the difference between an LED PCB and a regular PCB?
An LED PCB is specifically designed to power and control LEDs, incorporating features like thermal management and current distribution optimization. Regular PCBs are more general-purpose and may not have these specific design considerations. -
Can I design my own LED PCB?
Yes, you can design your own LED PCB using specialized PCB design software. However, it is essential to have a good understanding of LED characteristics, PCB design principles, and manufacturing constraints. -
How do I select the right LED PCB for my application?
When selecting an LED PCB, consider factors such as the required LED type and configuration, power and control requirements, thermal management needs, and environmental conditions. Consult with a professional or LED PCB manufacturer for guidance. -
What is the lifespan of an LED PCB?
The lifespan of an LED PCB depends on various factors, including the quality of the components, design, manufacturing, and operating conditions. Properly designed and maintained LED PCBs can last for several years or even decades. -
How can I ensure the longevity of my LED PCB?
To ensure the longevity of your LED PCB, follow best practices for design, manufacturing, and maintenance. This includes proper thermal management, using high-quality components, following recommended power and control guidelines, and regular inspection and cleaning.
Feature | LED PCB | Regular PCB |
---|---|---|
Design focus | Optimized for powering and controlling LEDs | General-purpose, not specific to LEDs |
Thermal management | Incorporates features like metal core substrates, thermal vias, or heat sinks | May not have specific thermal management features |
Current distribution | Designed to evenly distribute current among LEDs | May not have optimized current distribution |
Substrate materials | Can use specialized substrates like aluminum or flexible materials | Typically uses standard FR-4 substrate |
Applications | LED lighting, displays, backlighting, and signage | Wide range of electronic applications |
In conclusion, LED PCBs are essential components in the rapidly growing field of LED lighting and display technology. By understanding the design considerations, manufacturing processes, and best practices for LED PCBs, engineers and manufacturers can create efficient, reliable, and long-lasting LED solutions for a wide range of applications. As the technology continues to evolve, we can expect to see more innovative and sustainable LED PCB designs that push the boundaries of lighting performance and functionality.
No responses yet