What is a PCB Annular Ring?
A PCB annular ring, also known as a pad or land, is a circular copper area surrounding a drilled hole on a printed circuit board (PCB). The primary purpose of the annular ring is to provide a reliable electrical and mechanical connection between the component lead or pin and the PCB trace. The annular ring also helps to distribute the thermal and mechanical stresses around the hole, preventing damage to the PCB during the soldering process and throughout the product’s lifetime.
Key Features of PCB Annular Rings
- Size: The size of the annular ring is determined by the hole diameter and the required copper-to-hole clearance.
- Thickness: The thickness of the annular ring is typically the same as the copper trace thickness on the PCB.
- Material: Annular rings are made of copper, just like the traces on the PCB.
- Placement: Annular rings are located around drilled holes on the PCB, allowing components to be securely attached to the board.
Importance of PCB Annular Rings
Annular rings play a crucial role in the overall performance and reliability of a PCB. Some of the key reasons why annular rings are essential include:
1. Electrical Connection
The primary purpose of an annular ring is to provide a reliable electrical connection between the component lead and the PCB trace. The annular ring ensures that the electrical signal can flow seamlessly from the component to the trace and vice versa. Without a properly designed annular ring, the electrical connection may be compromised, leading to signal integrity issues or complete failure of the circuit.
2. Mechanical Stability
Annular rings also provide mechanical stability to the component leads or pins. The copper area surrounding the hole helps to distribute the mechanical stress evenly, preventing the hole from becoming enlarged or deformed over time. This is particularly important for components that are subjected to vibration or thermal stress, as the annular ring helps to keep the component securely in place.
3. Thermal Management
During the soldering process, the annular ring helps to dissipate heat evenly around the hole. This prevents localized overheating, which can cause damage to the PCB or the component. A properly designed annular ring ensures that the soldering process is reliable and consistent, reducing the risk of manufacturing defects.
4. Manufacturing Reliability
Annular rings are critical for ensuring the manufacturing reliability of a PCB. The size and shape of the annular ring can affect the ease of soldering and the overall quality of the solder joint. A well-designed annular ring allows for consistent and reliable soldering, reducing the risk of manufacturing defects and improving the overall yield of the PCB Assembly process.
Designing PCB Annular Rings
When designing PCB annular rings, several factors must be considered to ensure optimal performance and reliability. These factors include:
1. Hole Size
The hole size is determined by the diameter of the component lead or pin that will be inserted into the hole. The hole must be large enough to accommodate the lead or pin, but not so large that it compromises the integrity of the annular ring.
2. Annular Ring Size
The size of the annular ring is determined by the hole diameter and the required copper-to-hole clearance. The IPC (Association Connecting Electronics Industries) provides guidelines for minimum annular ring sizes based on the hole diameter and the PCB’s manufacturing class. These guidelines ensure that the annular ring is large enough to provide a reliable electrical and mechanical connection, while also allowing for manufacturing tolerances.
Hole Diameter (mm) | Minimum Annular Ring (mm) |
---|---|
0.2 – 0.4 | 0.05 |
0.4 – 0.8 | 0.075 |
0.8 – 1.2 | 0.1 |
1.2 – 2.0 | 0.125 |
2.0 – 3.0 | 0.15 |
3.0 – 4.0 | 0.2 |
3. Copper Thickness
The thickness of the copper on the PCB, including the annular ring, is typically specified by the PCB designer based on the electrical and thermal requirements of the circuit. Thicker copper can help to improve electrical conductivity and thermal management, but it can also increase the cost and complexity of the PCB manufacturing process.
4. Solder Mask Clearance
The solder mask is a protective layer that is applied over the copper traces on the PCB, leaving only the annular rings and other solderable surfaces exposed. The solder mask clearance is the distance between the edge of the annular ring and the edge of the solder mask opening. This clearance is necessary to ensure that the solder can flow properly during the soldering process and that there is sufficient space for visual inspection of the solder joint.
5. Thermal Relief
In some cases, it may be necessary to add thermal relief to the annular ring to improve thermal management during the soldering process. Thermal relief is a pattern of copper spokes or voids that extend from the annular ring to the surrounding copper area. These spokes or voids help to dissipate heat more evenly, reducing the risk of localized overheating and improving the reliability of the solder joint.
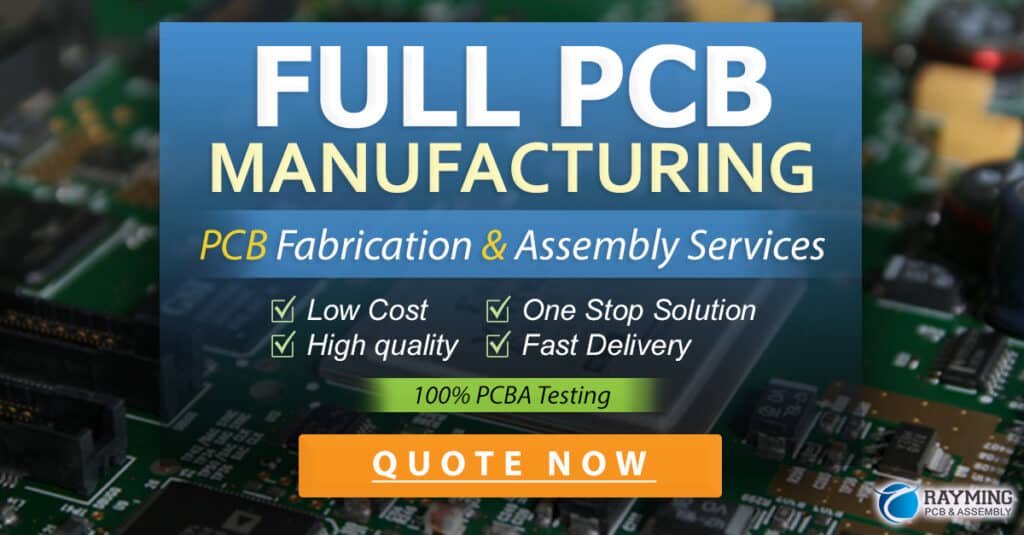
PCB Annular Ring Manufacturing Considerations
In addition to the design factors discussed above, there are several manufacturing considerations that must be taken into account when producing PCB annular rings. These considerations include:
1. Drilling Accuracy
The accuracy of the drilling process is critical for ensuring that the annular rings are properly aligned with the holes on the PCB. Any deviation in the hole placement can result in a misaligned annular ring, which can compromise the electrical and mechanical integrity of the solder joint. Modern PCB manufacturing processes use high-precision drilling machines and advanced vision systems to ensure that the holes are drilled accurately and consistently.
2. Plating Uniformity
The copper plating process is used to create the annular rings and other copper features on the PCB. It is important that the plating is uniform and consistent across the entire board to ensure reliable electrical and mechanical performance. Variations in the plating thickness or quality can lead to issues such as poor electrical conductivity, weak solder joints, or even complete failure of the circuit.
3. Solder Mask Application
The solder mask must be applied accurately and consistently to ensure that the annular rings are properly exposed for soldering. Any defects in the solder mask, such as incomplete coverage or excessive clearance, can affect the quality of the solder joint and the overall reliability of the PCB.
4. Inspection and Testing
After the PCB has been manufactured, it is important to perform thorough inspection and testing to ensure that the annular rings and other features meet the required specifications. This may include visual inspection, electrical testing, and mechanical testing to verify the integrity of the solder joints and the overall performance of the PCB.
Frequently Asked Questions (FAQ)
1. What is the difference between an annular ring and a pad?
Annular rings and pads are often used interchangeably, but there is a slight difference between the two terms. An annular ring specifically refers to the circular copper area surrounding a drilled hole, while a pad can refer to any solderable surface on the PCB, including annular rings and SMD (surface-mount device) pads.
2. Can the size of the annular ring affect the strength of the solder joint?
Yes, the size of the annular ring can have a significant impact on the strength of the solder joint. A larger annular ring provides more surface area for the solder to bond to, creating a stronger mechanical connection between the component lead and the PCB. However, it is important to balance the size of the annular ring with other design factors, such as the available space on the PCB and the required electrical performance.
3. What happens if the annular ring is too small?
If the annular ring is too small, it can compromise the electrical and mechanical integrity of the solder joint. A small annular ring may not provide enough surface area for the solder to bond to, resulting in a weak or unreliable connection. In extreme cases, a small annular ring can lead to complete failure of the solder joint, causing the component to become disconnected from the PCB.
4. How do I determine the appropriate size for an annular ring?
The appropriate size for an annular ring depends on several factors, including the hole diameter, the component lead size, and the manufacturing capabilities of the PCB fabricator. The IPC provides guidelines for minimum annular ring sizes based on these factors, which can be used as a starting point for PCB design. However, it is important to work closely with the PCB fabricator to ensure that the annular ring size is appropriate for the specific requirements of the project.
5. Can annular rings be used for surface-mount components?
Annular rings are primarily used for through-hole components, where the component lead is inserted into a drilled hole on the PCB. However, some surface-mount components, such as connectors or switches, may also require annular rings for mechanical stability or to provide additional solderable surface area. In these cases, the annular ring is typically combined with an SMD pad to create a hybrid mounting solution.
Conclusion
PCB annular rings are a critical feature of printed circuit board design, providing a reliable electrical and mechanical connection between component leads and PCB traces. Properly designing and manufacturing annular rings is essential for ensuring the overall performance and reliability of the PCB.
When designing annular rings, it is important to consider factors such as hole size, annular ring size, copper thickness, solder mask clearance, and thermal relief. These factors must be balanced with the specific requirements of the project, including electrical performance, mechanical stability, and manufacturing capabilities.
During the manufacturing process, it is critical to ensure drilling accuracy, plating uniformity, and consistent solder mask application to produce high-quality annular rings. Thorough inspection and testing are also necessary to verify the integrity of the solder joints and the overall performance of the PCB.
By understanding the importance of PCB annular rings and following best practices for design and manufacturing, PCB designers and manufacturers can create reliable, high-performance electronic products that meet the demands of today’s complex applications.
No responses yet