What are Flex Circuits?
Flex circuits are thin, flexible, and lightweight printed circuit boards that can be bent, folded, or twisted to fit into confined spaces or to conform to the shape of the device they are used in. They consist of a flexible substrate, typically made of polyimide or polyester, with conductive traces and pads printed on one or both sides. Flex circuits can be single-sided, double-sided, or multi-layered, depending on the complexity of the design and the application requirements.
The Manufacturing Process of Flex Circuits
The manufacturing process of flex circuits involves several steps, each requiring precision and attention to detail. Let’s take a closer look at each step:
Step 1: Design and Artwork Creation
The first step in Manufacturing Flex Circuits is designing the circuit layout and creating the artwork. The design is typically created using computer-aided design (CAD) software, which allows engineers to precisely layout the conductive traces, pads, and other features of the circuit. The artwork is then generated from the CAD design, which includes the conductive pattern and any necessary markings or text.
Step 2: Material Selection and Preparation
Once the design is finalized, the appropriate materials for the flex circuit are selected. The most common substrate materials are polyimide and polyester, chosen for their flexibility, durability, and ability to withstand high temperatures. The substrate is typically supplied in rolls or sheets, which are then cut to the required size.
Step 3: Lamination
The next step is lamination, where the conductive material, typically copper foil, is bonded to the substrate. This is done using heat and pressure to ensure a strong and uniform bond between the copper and the substrate. The lamination process can be done in a vacuum press or a hydraulic press, depending on the specific requirements of the project.
Step 4: Photolithography
After lamination, the circuit pattern is transferred onto the copper-clad substrate using photolithography. This process involves applying a light-sensitive photoresist coating to the copper surface, exposing it to UV light through a photomask containing the circuit pattern, and then developing the photoresist. The exposed areas of the photoresist are removed, leaving behind a protective layer in the shape of the circuit pattern.
Step 5: Etching
The unwanted copper is then removed through an etching process, typically using a chemical etchant such as ferric chloride or ammonium persulfate. The etchant dissolves the exposed copper, leaving behind the desired conductive pattern protected by the photoresist.
Step 6: Photoresist Removal and Cleaning
After etching, the remaining photoresist is removed using a chemical stripper, and the circuit is thoroughly cleaned to remove any residues.
Step 7: Cover Layer Application (Optional)
Depending on the application and design requirements, a cover layer may be applied to one or both sides of the flex circuit. The cover layer is typically made of polyimide or a similar flexible material and serves to protect the conductive traces and pads from damage or environmental factors.
Step 8: Drilling and Cutting
If required, holes are drilled through the flex circuit to accommodate component leads or to create interconnections between layers in multi-layer designs. The circuit is then cut to its final shape using a precision cutting tool, such as a laser or a die cutter.
Step 9: Surface Finishing
To enhance the durability and solderability of the flex circuit, various surface finishes can be applied to the exposed copper areas. Some common surface finishes include:
- Hot Air Solder Leveling (HASL): A thin layer of solder is applied to the copper pads and then leveled using hot air.
- Electroless Nickel Immersion Gold (ENIG): A layer of nickel is deposited on the copper, followed by a thin layer of gold, providing excellent solderability and shelf life.
- Immersion Silver: A thin layer of silver is deposited on the copper, offering good solderability at a lower cost compared to ENIG.
Step 10: Electrical Testing
To ensure the integrity and functionality of the flex circuit, electrical testing is performed. This may include continuity tests, insulation resistance tests, and high-potential (hipot) tests, depending on the specific requirements of the application.
Step 11: Packaging and Shipping
Finally, the completed flex circuits are inspected, packaged, and shipped to the customer or the next stage of the manufacturing process, such as component assembly or integration into the final product.
Advantages of Flex Circuits
Flex circuits offer several advantages over traditional rigid printed circuit boards (PCBs):
-
Flexibility and Conformability: Flex circuits can bend, fold, and twist, allowing them to fit into tight spaces and conform to the shape of the device they are used in.
-
Lightweight and Compact: Flex circuits are thinner and lighter than rigid PCBs, making them ideal for applications where weight and space are critical factors, such as in aerospace and portable electronics.
-
Improved Reliability: Flex circuits eliminate the need for connectors and cables between rigid boards, reducing the number of potential failure points and improving overall system reliability.
-
Enhanced Electrical Performance: Flex circuits can have shorter signal paths and reduced electromagnetic interference (EMI) compared to rigid PCBs with connectors and cables.
-
Design Versatility: Flex circuits offer greater design freedom, allowing for unique form factors and the integration of components directly onto the circuit.
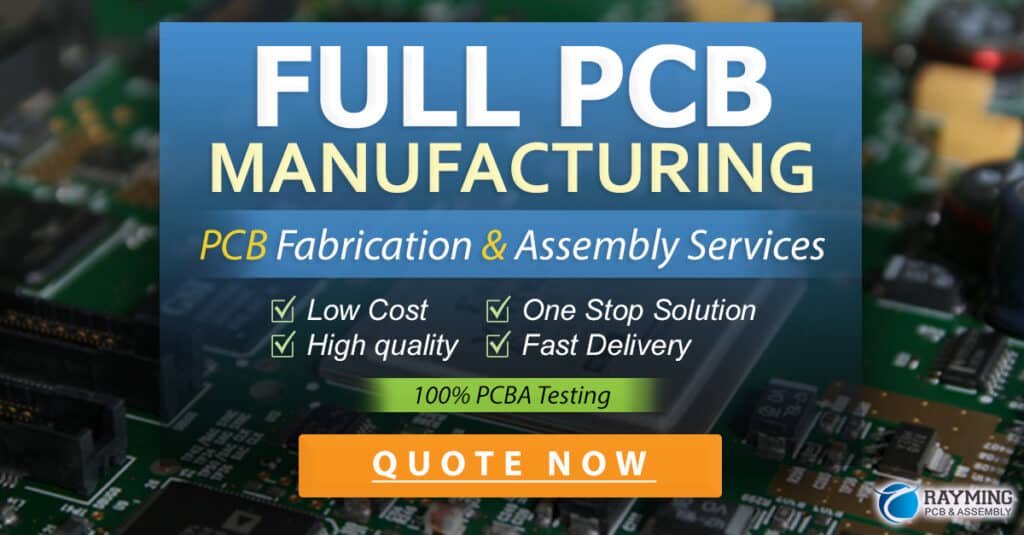
Applications of Flex Circuits
Flex circuits are used in a wide range of industries and applications, including:
- Consumer electronics: Smartphones, wearables, laptops, and tablets
- Medical devices: Implantable devices, diagnostic equipment, and patient monitoring systems
- Automotive: Instrument clusters, sensors, and entertainment systems
- Aerospace: Satellites, aircraft, and drones
- Industrial: Robotics, automation systems, and control panels
Frequently Asked Questions (FAQ)
1. What is the typical thickness of a flex circuit?
Flex circuits can be as thin as 0.05mm (0.002 inches) or as thick as 0.25mm (0.010 inches), depending on the number of layers and the specific application requirements.
2. Can flex circuits be used in high-temperature environments?
Yes, flex circuits can be designed to withstand high temperatures by using appropriate substrate materials, such as polyimide, which can withstand temperatures up to 200°C (392°F) or more.
3. How do flex circuits compare to rigid PCBs in terms of cost?
Flex circuits are generally more expensive than rigid PCBs due to the specialized materials and manufacturing processes involved. However, the overall system cost can be lower when using flex circuits, as they can reduce the need for connectors, cables, and additional assembly steps.
4. Can flex circuits be repaired if damaged?
Repairing flex circuits can be challenging, especially if the damage is extensive or if the circuit is multi-layered. In some cases, minor repairs can be made using specialized techniques, such as micro-soldering or conductive epoxy. However, in most cases, it is more cost-effective to replace the damaged flex circuit.
5. How do I choose the right surface finish for my flex circuit?
The choice of surface finish depends on factors such as the operating environment, soldering requirements, and cost. HASL is a common and cost-effective choice for general-purpose applications, while ENIG and immersion silver offer improved solderability and durability for more demanding applications.
Conclusion
Flex circuit boards have become an essential component in modern electronics, offering a flexible, lightweight, and compact solution for connecting electronic components. The manufacturing process of flex circuits involves several steps, each requiring precision and attention to detail. By understanding these steps and the advantages of flex circuits, designers and engineers can leverage this technology to create innovative and reliable products across various industries.
As the demand for smaller, lighter, and more flexible electronic devices continues to grow, the use of flex circuits is expected to increase. With advancements in materials, manufacturing processes, and design tools, flex circuits will continue to push the boundaries of what is possible in the world of electronics.
Step | Process | Description |
---|---|---|
1 | Design and Artwork Creation | Circuit layout and artwork creation using CAD software |
2 | Material Selection and Preparation | Selection and preparation of substrate materials (polyimide or polyester) |
3 | Lamination | Bonding of conductive material (copper foil) to the substrate using heat and pressure |
4 | Photolithography | Transfer of circuit pattern onto the copper-clad substrate using photoresist and UV light exposure |
5 | Etching | Removal of unwanted copper using chemical etchants, leaving the desired conductive pattern |
6 | Photoresist Removal and Cleaning | Removal of remaining photoresist and cleaning of the circuit |
7 | Cover Layer Application (Optional) | Application of a protective cover layer to one or both sides of the flex circuit |
8 | Drilling and Cutting | Drilling of holes and cutting of the circuit to its final shape |
9 | Surface Finishing | Application of surface finishes (HASL, ENIG, or immersion silver) to enhance durability and solderability |
10 | Electrical Testing | Performance of electrical tests to ensure circuit integrity and functionality |
11 | Packaging and Shipping | Inspection, packaging, and shipping of the completed flex circuits |
No responses yet