Introduction to Multilayer PCB Boards
Multilayer PCB (Printed Circuit Board) boards have become increasingly popular in the electronics industry due to their ability to accommodate complex circuitry in a compact space. These boards consist of multiple layers of conductive and insulating materials, allowing for the routing of signals and power between components on different layers. However, despite their numerous advantages, multilayer PCB boards also have certain limitations that can affect their performance and manufacturability.
Limitations of Multilayer PCB Boards
Signal Integrity Issues
One of the primary limitations of multilayer PCB boards is the potential for signal integrity issues. As the number of layers increases, so does the complexity of the board’s design and the risk of signal degradation. Some common signal integrity problems in multilayer PCBs include:
- Crosstalk: Unwanted coupling of signals between adjacent traces or layers.
- Electromagnetic Interference (EMI): Interference caused by electromagnetic radiation from the board or external sources.
- Impedance mismatch: Inconsistencies in the characteristic impedance of the traces, leading to signal reflections and distortions.
Manufacturing Challenges
Another limitation of multilayer PCB boards is the increased manufacturing complexity and cost. As the number of layers grows, the fabrication process becomes more challenging and time-consuming. Some manufacturing challenges associated with multilayer PCBs include:
- Registration and alignment: Ensuring proper alignment of the layers during the lamination process.
- Drilling and plating: Creating precise and reliable interconnections between layers through drilled holes and plating.
- Inspection and testing: Verifying the quality and functionality of the finished board, which becomes more difficult with increasing layer count.
Thermal Management
Multilayer PCB boards also face limitations related to thermal management. As the component density and power consumption increase, so does the amount of heat generated within the board. Ineffective thermal management can lead to several issues, such as:
- Component overheating: Excessive heat can cause components to fail prematurely or perform poorly.
- Board warpage: Uneven heating and cooling can cause the board to warp, affecting its mechanical stability and reliability.
- Thermal stress: Temperature gradients across the board can induce mechanical stress, potentially leading to cracks or delamination.
Solutions to Multilayer PCB Limitations
Despite these limitations, there are several strategies and techniques that can be employed to mitigate the challenges associated with multilayer PCB boards.
Improved Design Techniques
One approach to addressing the limitations of multilayer PCBs is through the use of advanced design techniques. These techniques aim to optimize the board layout and minimize the impact of signal integrity issues and manufacturing challenges. Some examples include:
- High-speed design considerations: Implementing techniques such as controlled impedance routing, differential pairs, and ground planes to minimize signal integrity issues in high-speed circuits.
- Design for manufacturability (DFM): Adhering to design guidelines and best practices that facilitate the manufacturing process, such as maintaining appropriate trace widths and spacings, avoiding sharp angles, and providing adequate clearances.
- 3D modeling and simulation: Utilizing 3D CAD tools and simulation software to analyze and optimize the board layout, identify potential issues, and verify the design before fabrication.
Advanced Materials and Technologies
Another solution to the limitations of multilayer PCB boards is the adoption of advanced materials and technologies. These innovations can help improve the performance, reliability, and manufacturability of the boards. Some examples include:
- Low-loss dielectrics: Using materials with low dielectric constant and dissipation factor to minimize signal loss and improve signal integrity.
- Embedded components: Integrating passive components, such as resistors and capacitors, directly into the PCB substrate, reducing the need for surface-mounted components and improving board density.
- High-density interconnect (HDI) technology: Employing microvias and fine-pitch traces to achieve higher routing density and reduce the overall board size.
Thermal Management Techniques
To address the thermal management limitations of multilayer PCB boards, several techniques can be employed to effectively dissipate heat and maintain acceptable operating temperatures. Some common thermal management strategies include:
- Thermal vias: Incorporating thermal vias, which are conductive paths through the board layers, to transfer heat from hot components to other layers or external heatsinks.
- Copper pours: Utilizing large copper areas on the board to spread heat and improve thermal conductivity.
- Heatsinks and cooling solutions: Implementing external heatsinks, fans, or other cooling solutions to actively dissipate heat from the board and its components.
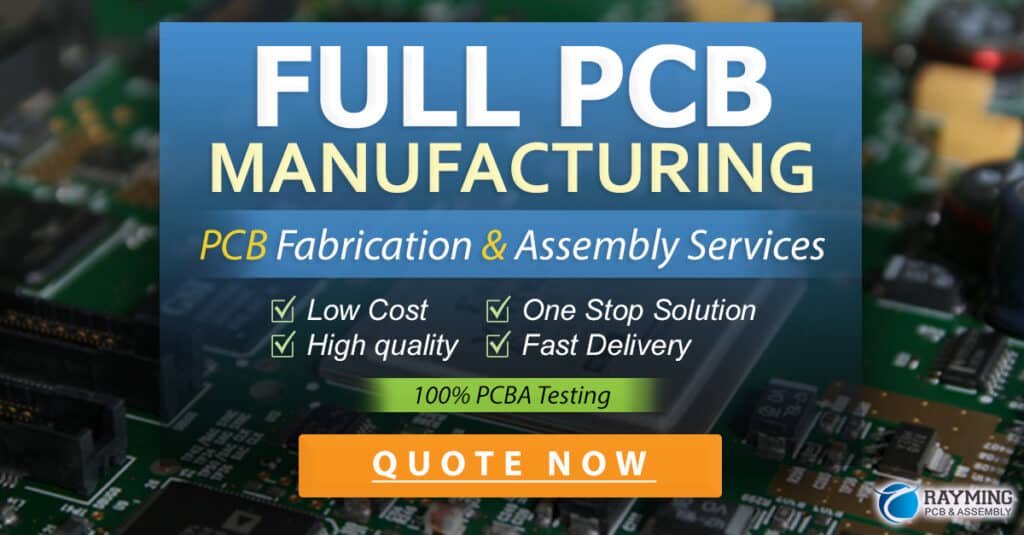
Case Studies and Examples
To illustrate the effectiveness of these solutions in addressing the limitations of multilayer PCB boards, let’s examine a few case studies and examples.
High-Speed Digital Design
In a high-speed digital design project, a multilayer PCB was required to route several high-frequency signals between a processor and memory modules. To minimize signal integrity issues, the design team implemented the following techniques:
- Controlled impedance routing: The traces were designed to maintain a consistent characteristic impedance, minimizing reflections and ensuring proper signal termination.
- Differential pairs: Critical high-speed signals were routed as differential pairs, which helped to cancel out electromagnetic interference and reduce crosstalk.
- Ground planes: Dedicated ground planes were incorporated into the board stackup to provide a low-impedance return path for the signals and shield them from external noise.
As a result of these design optimizations, the multilayer PCB successfully met the signal integrity requirements and performed reliably in the final application.
High-Density PCB Design
In another project, a complex electronic device required a high-density multilayer PCB to accommodate a large number of components in a limited space. To overcome the manufacturing challenges and achieve the desired board density, the following strategies were employed:
- HDI technology: The board utilized microvias and fine-pitch traces to maximize the routing density and minimize the layer count.
- Embedded components: Passive components, such as resistors and capacitors, were embedded into the PCB substrate, freeing up space on the surface layers for other components.
- DFM analysis: The design underwent thorough DFM analysis to identify and resolve any potential manufacturing issues, such as insufficient clearances or trace widths.
By leveraging these advanced technologies and design techniques, the high-density multilayer PCB was successfully manufactured and assembled, meeting the stringent requirements of the electronic device.
Thermal Management in Power Electronics
In a power electronics application, a multilayer PCB was used to interconnect several high-power components, such as MOSFETs and diodes. To ensure effective thermal management and prevent overheating, the following techniques were implemented:
- Thermal vias: The board incorporated a large number of thermal vias to transfer heat from the power components to dedicated copper layers for heat spreading.
- Copper pours: Large copper areas were used on the top and bottom layers of the board to improve thermal conductivity and distribute heat more evenly.
- External heatsink: A custom-designed heatsink was attached to the board to provide additional cooling capacity and maintain acceptable operating temperatures.
Through the use of these thermal management techniques, the multilayer PCB was able to efficiently dissipate heat from the power components, ensuring reliable operation and preventing thermal-related failures.
Frequently Asked Questions (FAQ)
-
Q: What is the maximum number of layers that can be used in a multilayer PCB?
A: The maximum number of layers in a multilayer PCB is not strictly defined and can vary depending on the manufacturer’s capabilities and the specific requirements of the application. However, most commercial PCB fabrication facilities can produce boards with up to 40 layers or more. Beyond that, specialized high-layer-count technologies, such as sequential lamination, can be used to create PCBs with even more layers, although this comes with increased complexity and cost. -
Q: How can signal integrity be maintained in high-speed multilayer PCBs?
A: To maintain signal integrity in high-speed multilayer PCBs, several design techniques can be employed, such as: - Using controlled impedance routing to ensure consistent characteristic impedance and minimize reflections.
- Implementing differential pairs for critical high-speed signals to reduce electromagnetic interference and crosstalk.
- Incorporating dedicated ground planes to provide a low-impedance return path and shielding for the signals.
-
Utilizing advanced simulation tools to analyze and optimize the board layout for signal integrity.
-
Q: What are some strategies for addressing thermal management in multilayer PCBs?
A: Effective thermal management in multilayer PCBs can be achieved through various strategies, including: - Incorporating thermal vias to transfer heat from hot components to other layers or external heatsinks.
- Using large copper pours on the board to spread heat and improve thermal conductivity.
- Implementing external heatsinks, fans, or other cooling solutions to actively dissipate heat from the board and its components.
-
Optimizing the board layout to minimize thermal hotspots and ensure even heat distribution.
-
Q: How can manufacturing challenges be overcome in high-density multilayer PCBs?
A: To overcome manufacturing challenges in high-density multilayer PCBs, several approaches can be taken, such as: - Employing HDI (High-Density Interconnect) technology, which utilizes microvias and fine-pitch traces to maximize routing density and minimize layer count.
- Embedding passive components into the PCB substrate to free up space on the surface layers for other components.
- Conducting thorough DFM (Design for Manufacturability) analysis to identify and resolve potential manufacturing issues early in the design process.
-
Collaborating closely with the PCB fabrication facility to ensure that the design meets their manufacturing capabilities and guidelines.
-
Q: Are there any advanced materials that can help address the limitations of multilayer PCBs?
A: Yes, several advanced materials can be used to improve the performance and manufacturability of multilayer PCBs, such as: - Low-loss dielectrics with low dielectric constant and dissipation factor to minimize signal loss and improve signal integrity.
- High-temperature laminates that can withstand elevated operating temperatures and reduce the risk of thermal-related failures.
- Embedded component materials that allow for the integration of passive components directly into the PCB substrate, improving board density and reducing the need for surface-mounted components.
- Advanced coatings and finishes that enhance the durability, reliability, and environmental resistance of the PCB.
By leveraging these advanced materials and technologies, designers can effectively address the limitations of multilayer PCBs and create boards that meet the demanding requirements of modern electronic applications.
Conclusion
Multilayer PCB boards offer numerous advantages in terms of accommodating complex circuitry and achieving high component density. However, they also come with certain limitations, such as signal integrity issues, manufacturing challenges, and thermal management concerns. By understanding these limitations and employing appropriate solutions, such as improved design techniques, advanced materials and technologies, and effective thermal management strategies, it is possible to overcome the challenges associated with multilayer PCBs and create high-performance, reliable electronic products.
As demonstrated through the case studies and examples, the successful implementation of these solutions can lead to significant improvements in board performance, manufacturability, and thermal management. By staying up-to-date with the latest advancements in PCB technology and continually refining their design and manufacturing processes, engineers and manufacturers can push the boundaries of what is possible with multilayer PCBs and meet the ever-increasing demands of the electronics industry.
No responses yet