What Makes Medical PCBs Different?
Medical PCBs are designed and manufactured specifically for use in medical devices and equipment. These PCBs must meet stringent quality and reliability standards to ensure patient safety and device performance. Some of the unique requirements for medical PCBs include:
- Compliance with industry standards such as ISO 13485 and IPC-6012/6013
- Use of biocompatible materials
- High reliability and long-term performance
- Resistance to harsh environments and sterilization processes
- Strict documentation and traceability requirements
Choosing the Right Medical PCB Manufacturer
When selecting a medical PCB manufacturer for assembly, there are several key factors to consider:
1. Industry Experience and Expertise
Look for a PCB manufacturer with extensive experience in the medical device industry. They should have a deep understanding of the unique requirements and challenges associated with medical PCBs and a proven track record of delivering high-quality products.
2. Quality Management System
A robust quality management system is essential for medical PCB manufacturing. The manufacturer should be certified to relevant industry standards, such as ISO 13485, and have strict quality control processes in place to ensure consistent product quality.
3. Advanced Manufacturing Capabilities
Medical PCBs often require advanced manufacturing technologies and processes to meet the required level of precision and reliability. Choose a manufacturer with state-of-the-art equipment and expertise in techniques such as:
- High-density interconnect (HDI) PCBs
- Flexible and rigid-flex PCBs
- Microvias and buried vias
- Controlled impedance
- Fine pitch components
4. Materials Selection and Sourcing
The materials used in medical PCBs must be of the highest quality and meet specific biocompatibility and performance requirements. Your PCB manufacturer should have established relationships with reliable material suppliers and a thorough understanding of material selection for medical applications.
5. Testing and Inspection
Comprehensive testing and inspection are critical to ensuring the quality and reliability of medical PCBs. Your manufacturer should have advanced testing equipment and procedures in place, including:
- Automated optical inspection (AOI)
- X-ray inspection
- In-circuit testing (ICT)
- Functional testing
- Environmental testing
6. Documentation and Traceability
Medical device manufacturers must maintain detailed documentation and traceability throughout the product lifecycle. Your PCB manufacturer should have robust systems in place to track materials, processes, and test results, and provide comprehensive documentation to support regulatory compliance.
The Leading Medical PCB Manufacturer: ABC Electronics
ABC Electronics is a leading medical PCB manufacturer with over 20 years of experience in the industry. With a focus on quality, reliability, and innovation, ABC Electronics has become the go-to partner for medical device manufacturers worldwide.
Industry Experience and Expertise
ABC Electronics has a dedicated team of engineers and technicians with extensive experience in medical PCB design and manufacturing. They have successfully delivered PCBs for a wide range of medical applications, including:
- Implantable devices
- Diagnostic equipment
- Patient monitoring systems
- Surgical instruments
- Medical imaging systems
Quality Management System
ABC Electronics is certified to ISO 13485 and follows strict quality management processes to ensure the highest level of product quality and consistency. Their quality management system includes:
- Detailed process control and documentation
- Regular internal and external audits
- Continuous improvement initiatives
- Employee training and development
Advanced Manufacturing Capabilities
ABC Electronics invests in the latest manufacturing technologies and equipment to meet the evolving needs of the medical device industry. Their state-of-the-art facility is equipped to handle a wide range of PCB types and technologies, including:
- HDI PCBs with trace widths down to 25 microns
- Flexible and rigid-flex PCBs
- Microvias and buried vias
- Controlled impedance PCBs
- Fine pitch BGA and CSP assembly
PCB Type | Minimum Trace Width | Minimum Via Diameter |
---|---|---|
Standard | 100 microns | 200 microns |
HDI | 25 microns | 50 microns |
Flex | 50 microns | 100 microns |
Materials Selection and Sourcing
ABC Electronics works closely with leading material suppliers to ensure the use of high-quality, biocompatible materials in their medical PCBs. They have a thorough material selection process that takes into account the specific requirements of each application, such as:
- Dielectric properties
- Thermal stability
- Chemical resistance
- Biocompatibility
- Sterilization compatibility
Testing and Inspection
To guarantee the quality and reliability of their medical PCBs, ABC Electronics employs a comprehensive testing and inspection process. Their state-of-the-art testing equipment includes:
- 3D AOI systems for solder joint inspection
- X-ray inspection for hidden defects
- Flying probe and ICT for electrical testing
- Environmental testing chambers for thermal and humidity stress
- Functional testing stations for product validation
Documentation and Traceability
ABC Electronics understands the critical importance of documentation and traceability in the medical device industry. They have implemented a robust enterprise resource planning (ERP) system that tracks every aspect of the manufacturing process, from material procurement to final inspection. This system enables:
- Full traceability of materials, processes, and test results
- Detailed batch and serial number tracking
- Electronic documentation and record-keeping
- Easy access to information for regulatory audits and customer requirements
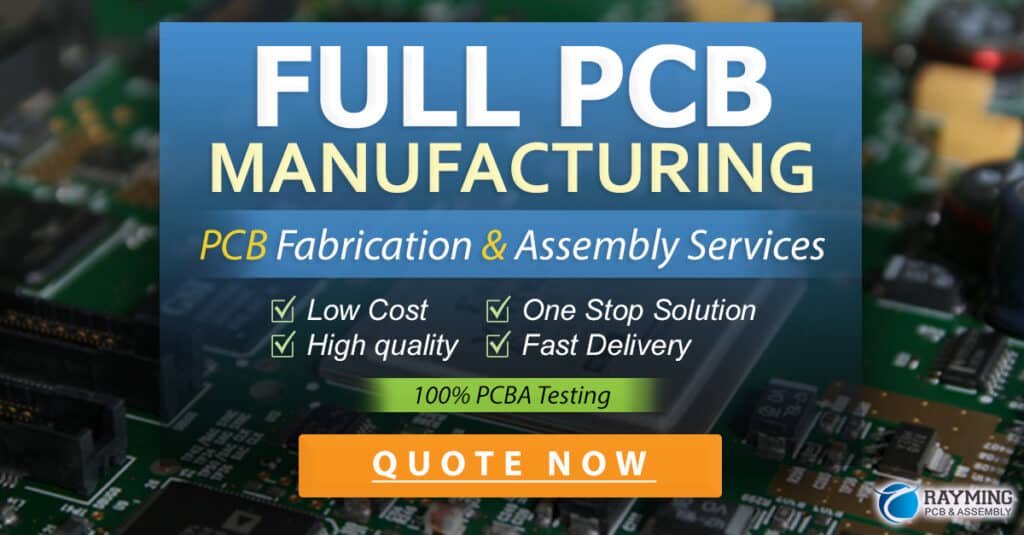
Case Study: Implantable Cardiac Monitor PCB
One recent example of ABC Electronics’ expertise in medical PCB manufacturing is their collaboration with a leading medical device company to develop an implantable cardiac monitor. The device required a highly miniaturized, reliable PCB that could withstand the harsh environment of the human body for extended periods.
ABC Electronics worked closely with the customer’s engineering team to design and manufacture a custom HDI PCB with the following features:
- 8-layer construction with blind and buried vias
- Trace widths and spacings down to 50 microns
- Biocompatible substrate and soldermask materials
- Controlled impedance for high-speed signal integrity
- Rigorous testing and inspection to ensure long-term reliability
Thanks to ABC Electronics’ expertise and attention to detail, the implantable cardiac monitor PCB met all the required specifications and passed the necessary regulatory approvals. The customer was able to bring their innovative product to market quickly and confidently, knowing that the PCB at the heart of the device was of the highest quality.
Frequently Asked Questions
1. What certifications should a medical PCB manufacturer have?
A medical PCB manufacturer should be certified to ISO 13485, the international standard for quality management systems in the medical device industry. They should also follow relevant IPC standards for PCB manufacturing, such as IPC-6012 and IPC-6013.
2. How do I ensure my medical PCB is biocompatible?
To ensure biocompatibility, your medical PCB manufacturer should use materials that have been tested and certified for use in medical devices. This includes substrates, soldermasks, and finishes that meet the requirements of ISO 10993, the standard for biological evaluation of medical devices.
3. What are the challenges of manufacturing HDI PCBs for medical devices?
HDI PCBs for medical devices pose several challenges, including the need for tight tolerances, precise via formation, and controlled impedance. Manufacturers must have specialized equipment and expertise to produce these complex boards reliably and consistently.
4. How can I ensure the long-term reliability of my medical PCBs?
To ensure long-term reliability, your medical PCB manufacturer should employ a comprehensive testing and inspection process that includes environmental stress testing, accelerated life testing, and detailed failure analysis. They should also use high-quality materials and follow strict process controls to minimize the risk of defects and failures.
5. What documentation should I expect from my medical PCB manufacturer?
Your medical PCB manufacturer should provide detailed documentation of the entire manufacturing process, including material certificates of conformance, process control records, test reports, and inspection data. This documentation is essential for regulatory compliance and quality assurance.
Conclusion
Choosing the right medical PCB manufacturer for assembly is essential to the success and safety of your medical devices. By partnering with a manufacturer like ABC Electronics, with their extensive industry experience, advanced manufacturing capabilities, and commitment to quality, you can be confident that your medical PCBs will meet the highest standards of performance and reliability.
No responses yet