Introduction to PCB Heatsinks
In the world of electronics, heat management is a crucial aspect of designing reliable and efficient printed circuit boards (PCBs). As electronic components become more powerful and compact, the need for effective thermal management solutions grows. One of the most common methods for dissipating heat from PCBs is through the use of heatsinks. In this comprehensive guide, we will dive into the essential aspects of PCB heatsink design and selection, providing you with the knowledge needed to make informed decisions when dealing with thermal challenges in your PCB projects.
Understanding the Importance of PCB Heatsinks
Why Thermal Management Matters
Thermal management is a critical consideration in PCB design for several reasons:
-
Component Reliability: Excessive heat can cause electronic components to degrade or fail prematurely, leading to reduced system reliability and increased maintenance costs.
-
Performance Optimization: High temperatures can negatively impact the performance of electronic components, resulting in slower processing speeds, increased power consumption, and potential signal integrity issues.
-
Safety Concerns: In extreme cases, inadequate thermal management can lead to overheating, causing potential fire hazards or posing risks to users.
The Role of PCB Heatsinks
PCB heatsinks play a vital role in thermal management by providing a pathway for heat to be dissipated away from heat-generating components. They work by increasing the surface area available for heat transfer and promoting airflow around the components. By effectively removing excess heat, PCB heatsinks help maintain optimal operating temperatures, ensuring the reliability and performance of the electronic system.
Factors Affecting PCB Heatsink Selection
When selecting a PCB heatsink, several key factors must be considered to ensure optimal thermal performance. These factors include:
Thermal Resistance
Thermal resistance is a measure of a heatsink’s ability to dissipate heat. It is expressed in units of °C/W (degrees Celsius per Watt) and represents the temperature rise of the heatsink per unit of power dissipated. A lower thermal resistance indicates better heat dissipation capabilities. When selecting a PCB heatsink, it is essential to choose one with a thermal resistance that is appropriate for the specific application and the amount of heat generated by the components.
Material Properties
The choice of material for a PCB heatsink can significantly impact its thermal performance. Common materials used for heatsinks include:
-
Aluminum: Aluminum is a popular choice due to its excellent thermal conductivity, lightweight nature, and cost-effectiveness. It is suitable for a wide range of applications.
-
Copper: Copper offers even better thermal conductivity than aluminum but comes at a higher cost and weight. It is often used in high-performance applications where maximum heat dissipation is required.
-
Composite Materials: Some heatsinks are made from composite materials, such as aluminum with embedded copper or graphite fibers. These materials combine the benefits of different materials to achieve optimal thermal performance and weight reduction.
Surface Finish
The surface finish of a PCB heatsink can affect its thermal performance and compatibility with other components. Common surface finishes include:
-
Anodizing: Anodizing is an electrochemical process that creates a protective oxide layer on the heatsink surface. It enhances corrosion resistance and can be colored for aesthetic purposes.
-
Nickel Plating: Nickel plating provides a smooth, corrosion-resistant finish and improves solderability for heatsinks that need to be attached to the PCB.
-
Bare Metal: Some heatsinks are left with a bare metal finish, which can provide better thermal conductivity but may be more susceptible to corrosion.
Heatsink Geometry and Size
The geometry and size of a PCB heatsink play a crucial role in its thermal performance. Heatsinks come in various shapes and sizes, including:
-
Extruded Heatsinks: Extruded heatsinks are manufactured by pushing molten metal through a die to create a profile with fins. They offer good thermal performance and are available in various sizes and fin configurations.
-
Stamped Heatsinks: Stamped heatsinks are made by stamping metal sheets to create fins. They are cost-effective and suitable for applications with moderate heat dissipation requirements.
-
Bonded Fin Heatsinks: Bonded fin heatsinks consist of a base plate with fins bonded to it. They offer excellent thermal performance and can be customized for specific applications.
When selecting a heatsink, consider the available space on the PCB, the height constraints of the enclosure, and the orientation of the heatsink relative to the airflow direction. Larger heatsinks with more surface area generally provide better heat dissipation but may not always be feasible due to space limitations.
Attachment Methods
The method used to attach a heatsink to a PCB can impact its thermal performance and mechanical stability. Common attachment methods include:
-
Thermal Adhesive: Thermal adhesive is a specialized epoxy that provides a strong bond between the heatsink and the component. It offers good thermal conductivity and is suitable for applications where mechanical stress is not a concern.
-
Mechanical Fasteners: Mechanical fasteners, such as screws or clips, can be used to securely attach the heatsink to the PCB. They provide a robust connection and allow for easy removal if necessary.
-
Push Pins: Push pins are plastic fasteners that snap into place, holding the heatsink securely to the PCB. They are quick and easy to install but may not provide as much mechanical stability as other methods.
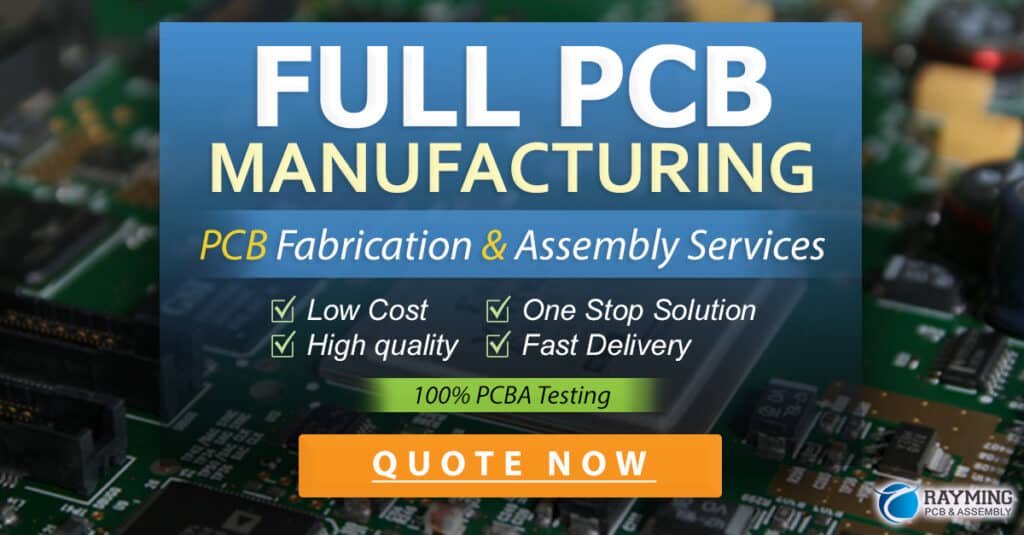
PCB Heatsink Design Considerations
Thermal Interface Materials
Thermal interface materials (TIMs) are used to fill the gaps between the heatsink and the heat-generating component, improving thermal conductivity. Common TIMs include:
-
Thermal Grease: Thermal grease is a paste-like material that is applied between the heatsink and the component. It fills microscopic air gaps and enhances heat transfer.
-
Thermal Pads: Thermal pads are pre-cut, thermally conductive materials that are placed between the heatsink and the component. They are easy to install and provide good thermal conductivity.
-
Phase Change Materials: Phase change materials are specialized TIMs that change from solid to liquid at a specific temperature, allowing them to conform to the surfaces and improve thermal contact.
Airflow and Heatsink Orientation
The orientation of the PCB heatsink relative to the airflow direction can significantly impact its thermal performance. When designing the PCB layout, consider the following:
-
Airflow Direction: Orient the heatsink fins parallel to the airflow direction to maximize heat transfer. If the fins are perpendicular to the airflow, the heatsink’s effectiveness will be reduced.
-
Component Placement: Position heat-generating components strategically to take advantage of natural convection or forced airflow. Avoid placing components in stagnant air regions or near other heat sources.
-
Clearance: Ensure adequate clearance around the heatsink to allow for proper airflow. Avoid obstructing the airflow path with other components or structures.
Thermal Simulation and Testing
To ensure the effectiveness of a PCB heatsink design, thermal simulation and testing are essential. Thermal simulation software can help predict the temperature distribution and identify potential hot spots on the PCB. It allows designers to evaluate different heatsink configurations and optimize the design before physical prototyping.
Once the PCB is manufactured, thermal testing should be conducted to validate the heatsink’s performance under real-world conditions. This can involve using thermocouples or infrared cameras to measure the temperature at various points on the PCB and heatsink. Testing should be performed under different operating scenarios and environmental conditions to ensure the heatsink meets the required thermal specifications.
PCB Heatsink Selection Process
Step 1: Determine the Thermal Requirements
The first step in selecting a PCB heatsink is to determine the thermal requirements of the system. This involves calculating the amount of heat generated by the components and determining the maximum allowable temperature rise. Consider factors such as ambient temperature, power dissipation of the components, and the desired operating temperature range.
Step 2: Evaluate the Available Space
Assess the available space on the PCB and the enclosure for heatsink placement. Consider the height constraints, component clearances, and any other mechanical limitations. This will help narrow down the heatsink options based on size and form factor.
Step 3: Select the Heatsink Material
Choose the appropriate heatsink material based on the thermal requirements, cost considerations, and weight constraints. Aluminum is a common choice for most applications, while copper may be preferred for high-performance systems.
Step 4: Determine the Heatsink Geometry
Select the heatsink geometry that best suits the application. Consider factors such as fin configuration, surface area, and orientation relative to the airflow direction. Use thermal simulation software to evaluate different heatsink designs and optimize for thermal performance.
Step 5: Choose the Attachment Method
Decide on the appropriate attachment method for the heatsink based on the mechanical requirements and ease of assembly. Thermal adhesives, mechanical fasteners, or push pins can be used depending on the specific application and manufacturing process.
Step 6: Evaluate Thermal Interface Materials
Select the appropriate thermal interface material to ensure efficient heat transfer between the heatsink and the heat-generating component. Consider factors such as thermal conductivity, ease of application, and long-term reliability.
Step 7: Conduct Thermal Testing
Once the PCB heatsink is designed and manufactured, perform thermal testing to validate its performance. Use thermocouples or infrared cameras to measure the temperature at critical points on the PCB and heatsink. Ensure that the heatsink meets the required thermal specifications under various operating conditions.
Common PCB Heatsink Applications
PCB heatsinks are used in a wide range of electronic applications, including:
-
Power Electronics: Heatsinks are essential for managing heat in power electronic devices such as voltage regulators, power amplifiers, and motor controllers.
-
High-Performance Computing: Heatsinks are used to cool processors, graphics cards, and other high-performance components in computers and servers.
-
Telecommunications: Heatsinks are employed in telecom equipment, such as base stations and routers, to ensure reliable operation and prevent overheating.
-
Automotive Electronics: Heatsinks are used in various automotive electronic systems, including engine control units, infotainment systems, and power converters.
-
Industrial Automation: Heatsinks are essential for cooling electronic components in industrial automation systems, such as programmable logic controllers (PLCs) and motor drives.
PCB Heatsink Selection and Design Tips
To optimize the performance of PCB heatsinks, consider the following tips:
-
Maximize surface area: Increase the surface area of the heatsink by using fins or other features to enhance heat dissipation.
-
Optimize airflow: Ensure proper airflow around the heatsink by orienting it correctly and providing adequate clearance for air circulation.
-
Use thermal simulations: Employ thermal simulation software to evaluate and optimize heatsink designs before physical prototyping.
-
Consider thermal interface materials: Use appropriate thermal interface materials to minimize thermal resistance between the heatsink and the heat-generating component.
-
Test and validate: Conduct thorough thermal testing to validate the heatsink’s performance under real-world conditions.
FAQ
1. What is the purpose of a PCB heatsink?
A PCB heatsink is designed to dissipate heat away from heat-generating components on a printed circuit board, helping to maintain optimal operating temperatures and ensure the reliability and performance of the electronic system.
2. What materials are commonly used for PCB heatsinks?
Common materials used for PCB heatsinks include aluminum, copper, and composite materials such as aluminum with embedded copper or graphite fibers. The choice of material depends on factors such as thermal conductivity, cost, and weight.
3. How do I select the right size and shape of a PCB heatsink?
When selecting the size and shape of a PCB heatsink, consider factors such as the available space on the PCB, the height constraints of the enclosure, the amount of heat generated by the components, and the orientation of the heatsink relative to the airflow direction. Thermal simulation software can help evaluate different heatsink designs and optimize for thermal performance.
4. What are the common methods for attaching a PCB heatsink?
Common methods for attaching a PCB heatsink include using thermal adhesives, mechanical fasteners (such as screws or clips), or push pins. The choice of attachment method depends on the specific application, mechanical requirements, and ease of assembly.
5. How can I ensure proper airflow around a PCB heatsink?
To ensure proper airflow around a PCB heatsink, consider the following:
- Orient the heatsink fins parallel to the airflow direction to maximize heat transfer.
- Position heat-generating components strategically to take advantage of natural convection or forced airflow.
- Provide adequate clearance around the heatsink to allow for proper air circulation and avoid obstructing the airflow path with other components or structures.
Conclusion
PCB heatsink design and selection play a crucial role in ensuring the reliability, performance, and safety of electronic systems. By understanding the factors affecting heatsink performance, considering design best practices, and following a systematic selection process, designers can effectively manage thermal challenges in their PCB projects.
This comprehensive guide has covered the essential aspects of PCB heatsink design and selection, including the importance of thermal management, factors influencing heatsink performance, design considerations, and the selection process. By applying the knowledge and tips provided, designers can make informed decisions when dealing with thermal management in PCBs.
As electronic systems continue to advance and become more complex, the importance of effective thermal management will only increase. By staying up to date with the latest techniques and technologies in PCB heatsink design, designers can ensure that their projects meet the evolving thermal requirements and deliver reliable, high-performance electronic solutions.
No responses yet