Introduction
The Internet of Things (IoT) has revolutionized the manufacturing industry, ushering in the era of Industry 4.0. This new era is characterized by the integration of advanced technologies such as IoT, artificial intelligence (AI), and machine learning (ML) into the manufacturing process. IoT-enabled devices and sensors collect vast amounts of data, which can be analyzed to optimize operations, reduce costs, and improve product quality. In this article, we will explore the 10 best IoT Industry 4.0 use cases for manufacturing.
1. Predictive Maintenance
What is Predictive Maintenance?
Predictive maintenance is a technique that uses IoT sensors to monitor the condition of equipment in real-time. By analyzing the data collected by these sensors, manufacturers can predict when equipment is likely to fail and schedule maintenance accordingly. This approach reduces downtime, extends equipment lifespan, and minimizes maintenance costs.
How Does Predictive Maintenance Work?
IoT sensors are attached to critical equipment components, such as motors, bearings, and pumps. These sensors collect data on various parameters, such as vibration, temperature, and pressure. The data is then transmitted to a central system, where it is analyzed using AI and ML algorithms. These algorithms identify patterns and anomalies that indicate potential equipment failure, allowing manufacturers to schedule maintenance before a breakdown occurs.
Benefits of Predictive Maintenance
- Reduced downtime
- Extended equipment lifespan
- Lower maintenance costs
- Improved overall equipment effectiveness (OEE)
2. Asset Tracking and Management
What is Asset Tracking and Management?
Asset tracking and management involve using IoT devices to monitor the location and status of assets in real-time. This includes raw materials, work-in-progress inventory, finished goods, and equipment. By tracking assets throughout the manufacturing process, companies can optimize inventory levels, reduce waste, and improve efficiency.
How Does Asset Tracking and Management Work?
IoT devices, such as RFID tags and GPS trackers, are attached to assets. These devices transmit data on the location and status of the assets to a central system. The system analyzes the data to provide real-time visibility into the movement of assets throughout the manufacturing process. This allows manufacturers to identify bottlenecks, optimize inventory levels, and ensure that the right materials and equipment are available when needed.
Benefits of Asset Tracking and Management
- Real-time visibility into asset location and status
- Optimized inventory levels
- Reduced waste and obsolescence
- Improved efficiency and productivity
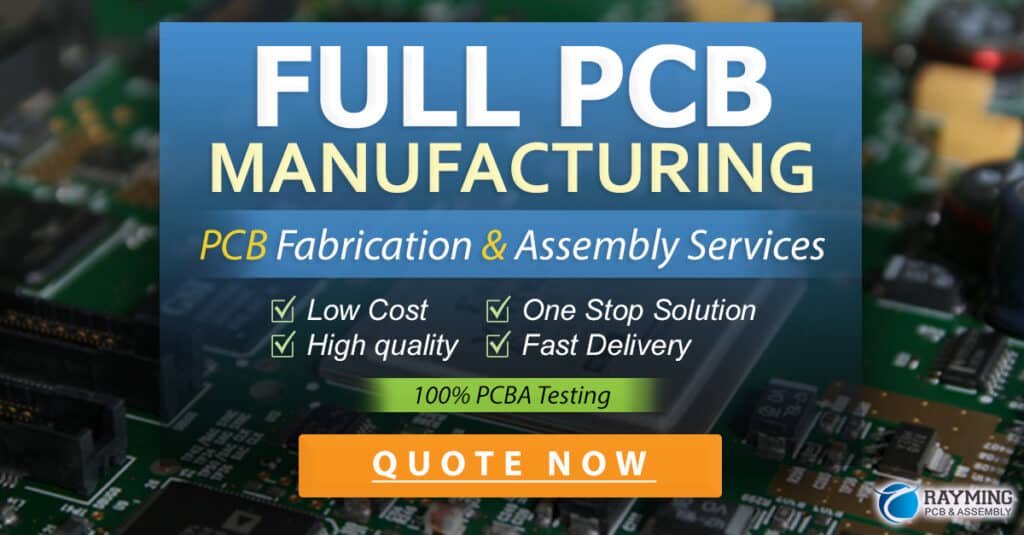
3. Quality Control and Inspection
What is Quality Control and Inspection?
Quality control and inspection involve using IoT sensors to monitor the quality of products throughout the manufacturing process. By detecting defects and anomalies in real-time, manufacturers can identify and address quality issues before they result in customer complaints or product recalls.
How Does Quality Control and Inspection Work?
IoT sensors are integrated into the manufacturing process to collect data on various quality parameters, such as dimensions, weight, and surface finish. The data is analyzed using AI and ML algorithms to identify patterns and anomalies that indicate potential quality issues. When an issue is detected, the system alerts operators, who can take corrective action before the defective product reaches the customer.
Benefits of Quality Control and Inspection
- Early detection and correction of quality issues
- Reduced scrap and rework
- Improved customer satisfaction
- Lower warranty and recall costs
4. Energy Management
What is Energy Management?
Energy management involves using IoT sensors to monitor and optimize energy consumption in manufacturing facilities. By identifying areas of waste and inefficiency, manufacturers can reduce energy costs and improve sustainability.
How Does Energy Management Work?
IoT sensors are installed throughout the manufacturing facility to collect data on energy consumption, such as electricity, gas, and water usage. The data is analyzed to identify patterns and anomalies that indicate areas of waste or inefficiency. Based on this analysis, manufacturers can implement energy-saving measures, such as adjusting equipment settings, optimizing production schedules, and upgrading to more efficient equipment.
Benefits of Energy Management
- Reduced energy costs
- Improved sustainability
- Enhanced regulatory compliance
- Increased competitiveness
5. Supply Chain Optimization
What is Supply Chain Optimization?
Supply chain optimization involves using IoT devices to monitor and optimize the flow of materials and products throughout the supply chain. By improving visibility and coordination between suppliers, manufacturers, and customers, companies can reduce lead times, minimize inventory, and improve customer service.
How Does Supply Chain Optimization Work?
IoT devices, such as sensors and trackers, are attached to materials and products throughout the supply chain. These devices collect data on the location, condition, and status of the materials and products, which is transmitted to a central system. The system analyzes the data to provide real-time visibility into the supply chain, allowing manufacturers to identify bottlenecks, optimize inventory levels, and ensure that the right materials and products are available when needed.
Benefits of Supply Chain Optimization
- Improved visibility and coordination throughout the supply chain
- Reduced lead times and inventory levels
- Enhanced customer service and satisfaction
- Increased competitiveness and profitability
6. Workforce Management
What is Workforce Management?
Workforce management involves using IoT devices to monitor and optimize the performance of the manufacturing workforce. By tracking employee location, activity, and productivity, manufacturers can identify areas for improvement and ensure that the right skills and resources are available when needed.
How Does Workforce Management Work?
IoT devices, such as wearables and badges, are issued to employees. These devices collect data on employee location, activity, and productivity, which is transmitted to a central system. The system analyzes the data to identify patterns and anomalies that indicate areas for improvement, such as training needs, process bottlenecks, and resource allocation issues. Based on this analysis, manufacturers can implement measures to optimize workforce performance, such as providing targeted training, reallocating resources, and improving work processes.
Benefits of Workforce Management
- Improved workforce productivity and efficiency
- Enhanced employee safety and well-being
- Reduced labor costs and turnover
- Increased competitiveness and profitability
7. Remote Monitoring and Control
What is Remote Monitoring and Control?
Remote monitoring and control involve using IoT devices to monitor and control manufacturing equipment and processes from a remote location. By enabling real-time visibility and control of operations, manufacturers can improve efficiency, reduce downtime, and ensure consistent product quality.
How Does Remote Monitoring and Control Work?
IoT sensors and actuators are installed on manufacturing equipment and processes. These devices collect data on various parameters, such as temperature, pressure, and speed, which is transmitted to a central system. The system analyzes the data to provide real-time visibility into operations, allowing manufacturers to identify issues and make adjustments remotely. In addition, the system can be configured to automatically adjust equipment settings based on predefined rules and thresholds.
Benefits of Remote Monitoring and Control
- Real-time visibility into manufacturing operations
- Reduced downtime and maintenance costs
- Improved product quality and consistency
- Enhanced flexibility and agility
8. Digital Twin
What is a Digital Twin?
A digital twin is a virtual representation of a physical asset or process, created using data collected by IoT sensors. By simulating the behavior of the physical asset or process in real-time, manufacturers can optimize performance, predict maintenance needs, and test new configurations without disrupting operations.
How Does a Digital Twin Work?
IoT sensors are installed on the physical asset or process to collect data on various parameters, such as temperature, pressure, and vibration. The data is transmitted to a central system, where it is used to create a virtual model of the asset or process. The virtual model is then used to simulate the behavior of the physical asset or process under different conditions and scenarios. Based on the simulation results, manufacturers can identify opportunities for optimization, predict maintenance needs, and test new configurations before implementing them in the physical world.
Benefits of Digital Twin
- Improved asset performance and reliability
- Predictive maintenance and reduced downtime
- Optimized process design and configuration
- Enhanced safety and compliance
9. Additive Manufacturing
What is Additive Manufacturing?
Additive manufacturing, also known as 3D printing, involves using IoT-enabled printers to create complex parts and products directly from digital designs. By enabling on-demand production and customization, additive manufacturing can reduce lead times, minimize inventory, and improve product innovation.
How Does Additive Manufacturing Work?
IoT-enabled 3D printers are connected to a central system, which receives digital designs from engineers and customers. The system analyzes the designs to ensure that they are compatible with the printer’s capabilities and materials. Once the design is approved, the printer creates the part or product layer by layer, using materials such as plastic, metal, or ceramic. The printer collects data on the printing process, which is transmitted back to the central system for analysis and optimization.
Benefits of Additive Manufacturing
- Reduced lead times and inventory levels
- Improved product customization and innovation
- Enhanced supply chain flexibility and agility
- Lower production costs and waste
10. Augmented Reality (AR) and Virtual Reality (VR)
What are AR and VR?
AR and VR are technologies that use IoT devices to create immersive digital experiences. AR overlays digital information onto the physical world, while VR creates a completely digital environment. In manufacturing, AR and VR can be used for training, product design, and remote collaboration.
How Do AR and VR Work?
IoT devices, such as smart glasses and headsets, are used to create AR and VR experiences. These devices are connected to a central system, which provides the digital content and processing power needed to create the immersive experiences. For example, in AR-based training, IoT sensors can track the movement of the user and provide real-time feedback and guidance. In VR-based product design, engineers can collaborate remotely in a virtual environment, using digital models and simulations to test and refine designs.
Benefits of AR and VR
- Improved training effectiveness and safety
- Enhanced product design and innovation
- Increased remote collaboration and communication
- Reduced travel and prototyping costs
Frequently Asked Questions (FAQ)
1. What is the difference between IoT and Industry 4.0?
IoT refers to the network of connected devices that collect and exchange data, while Industry 4.0 refers to the broader trend of digitalization and automation in manufacturing, which includes IoT as well as other technologies such as AI, ML, and robotics.
2. How does IoT improve manufacturing efficiency?
IoT improves manufacturing efficiency by providing real-time visibility into operations, enabling predictive maintenance, optimizing asset utilization, and reducing waste and downtime.
3. What are the challenges of implementing IoT in manufacturing?
The challenges of implementing IoT in manufacturing include data security and privacy concerns, integration with legacy systems, lack of standardization, and the need for specialized skills and expertise.
4. How does IoT enable predictive maintenance?
IoT enables predictive maintenance by collecting data from sensors installed on equipment, which is then analyzed using AI and ML algorithms to predict when maintenance is needed before a failure occurs.
5. What is the future of IoT in manufacturing?
The future of IoT in manufacturing is expected to involve greater integration with other technologies such as AI, ML, and blockchain, as well as the development of new use cases such as autonomous factories and personalized production.
Conclusion
IoT is transforming the manufacturing industry, enabling new levels of efficiency, flexibility, and innovation. From predictive maintenance and asset tracking to quality control and workforce management, the use cases for IoT in manufacturing are vast and diverse. As the technology continues to evolve, we can expect to see even more advanced applications and benefits emerge, driving the industry towards a more connected, intelligent, and sustainable future.
Use Case | Description | Benefits |
---|---|---|
Predictive Maintenance | Using IoT sensors to monitor equipment condition and predict maintenance needs | Reduced downtime, extended equipment lifespan, lower maintenance costs |
Asset Tracking and Management | Using IoT devices to monitor the location and status of assets in real-time | Real-time visibility, optimized inventory levels, reduced waste |
Quality Control and Inspection | Using IoT sensors to monitor product quality and detect defects in real-time | Early detection and correction of quality issues, reduced scrap and rework |
Energy Management | Using IoT sensors to monitor and optimize energy consumption in manufacturing facilities | Reduced energy costs, improved sustainability, enhanced regulatory compliance |
Supply Chain Optimization | Using IoT devices to monitor and optimize the flow of materials and products throughout the supply chain | Improved visibility and coordination, reduced lead times and inventory levels |
Workforce Management | Using IoT devices to monitor and optimize the performance of the manufacturing workforce | Improved workforce productivity and efficiency, enhanced employee safety and well-being |
Remote Monitoring and Control | Using IoT devices to monitor and control manufacturing equipment and processes from a remote location | Real-time visibility into operations, reduced downtime and maintenance costs |
Digital Twin | Creating a virtual representation of a physical asset or process using data collected by IoT sensors | Improved asset performance and reliability, predictive maintenance, optimized process design |
Additive Manufacturing | Using IoT-enabled printers to create complex parts and products directly from digital designs | Reduced lead times and inventory levels, improved product customization and innovation |
AR and VR | Using IoT devices to create immersive digital experiences for training, product design, and remote collaboration | Improved training effectiveness and safety, enhanced product design and innovation |
No responses yet