What are PTC Thermistors?
PTC (Positive Temperature Coefficient) thermistors are temperature sensing devices whose resistance increases with increasing temperature. They are made from polycrystalline ceramic materials such as barium titanate (BaTiO3) or lead titanate (PbTiO3) which have been doped with small amounts of rare earth elements or metals to enhance their electrical properties.
PTC thermistors exhibit a highly nonlinear resistance-temperature characteristic. At low temperatures, their resistance remains relatively low and constant. However, when the temperature reaches a critical point called the Curie or switching temperature, the resistance increases sharply by several orders of magnitude over a narrow temperature range. This steep positive temperature coefficient of resistance makes PTC thermistors useful for many applications.
How Do PTC Thermistors Work?
The unique behavior of PTC thermistors arises from their polycrystalline structure and the ferroelectric properties of barium titanate. Below the Curie temperature (~ 120°C for pure BaTiO3), the crystal structure is tetragonal and the material exhibits spontaneous polarization, allowing charge carriers to move easily through the grain boundaries resulting in low electrical resistance.
As the temperature rises above the Curie point, the crystal structure changes to a cubic centrosymmetric phase and becomes paraelectric, losing its ferroelectric properties. This phase transition impedes the flow of charge carriers across the grain boundaries, causing a sharp increase in resistance. The Curie temperature can be adjusted between -50°C to 200°C by modifying the composition.
The resistance-temperature characteristic of a typical PTC thermistor is shown below:
Temperature (°C) | Resistance (Ω) |
---|---|
-50 | 100 |
0 | 95 |
50 | 85 |
100 | 75 |
120 | 100 |
130 | 5000 |
140 | 50000 |
150 | 100000 |
As seen, the resistance remains relatively constant up to 100°C, increases by a factor of 50 between 120-130°C, and continues rising exponentially. This behavior is described by the Steinhart-Hart equation:
1/T = A + B ln(R) + C [ln(R)]³
Where T is the absolute temperature (K), R is the thermistor resistance (Ω), and A, B, C are the Steinhart coefficients specific to the thermistor material and geometry.
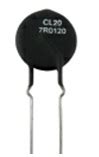
Characteristics of PTC Thermistors
The key characteristics that define a PTC thermistor include:
Curie or Switching Temperature (Ts)
The temperature at which the resistance starts increasing sharply, typically by a factor of 10-100 per °C. It depends on the composition.
Resistance-Temperature Coefficient (α)
Quantifies the percentage change in resistance per °C change in temperature. For PTCs, α is positive and very high, on the order of 10-100 %/°C above Ts.
α = (1/R) * (dR/dT)
Reference Resistance (Rref)
The resistance at a specified reference temperature, typically 25°C. It ranges from 10 Ω to 10 kΩ.
Maximum Voltage and Current
The maximum voltage and current the PTC can withstand continuously without damage. Exceeding these limits may cause irreversible changes.
Thermal Time Constant (τ)
The time required for the thermistor to change 63.2% of the difference from its initial to final body temperature when subjected to a step change in ambient temperature. A small τ means faster response.
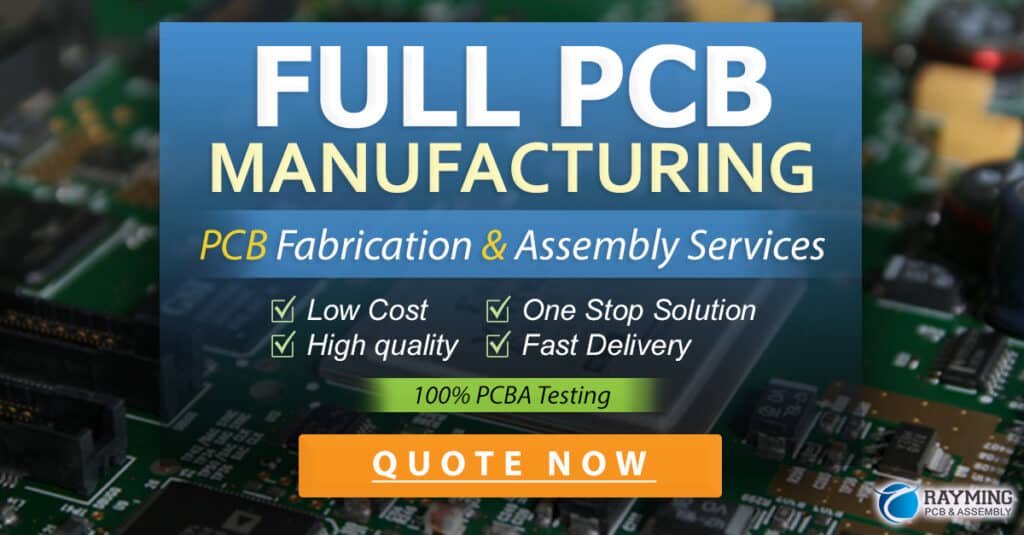
PTC Thermistor Construction and Packaging
PTC thermistors are manufactured by pressing and sintering titanate ceramic powders into the desired shape, applying electrodes, and providing leads or terminals for electrical connection. The dimensions, geometry, and electrode configuration influence the resistance and heat capacity.
PTCs are available in various packages to suit different applications:
-
Disc or coin type: Flat cylindrical elements with tinned copper leads. Diameters range from 2-40 mm.
-
Chip or SMD type: Rectangular or square chips with metallized surface electrodes for surface mounting. EIA size codes like 0805, 1206 etc are used.
-
Bead type: Tiny spherical elements with thin lead wires, used for point sensing and faster response. Diameters from 0.5-2 mm.
-
Probe or radial leaded type: Disc or rod elements encapsulated in epoxy or glass body with axial leads. Used for immersion sensing.
-
Strap or blade type: Flat elongated elements for easy insertion and high power handling.
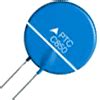
Applications of PTC Thermistors
The sharp switching characteristic and high temperature coefficient of PTC thermistors make them ideal for many applications:
Temperature Sensing and Control
PTCs can provide precise temperature measurement and control in HVAC systems, industrial processes, automotive sensors, and household appliances. Their high sensitivity allows detecting small temperature changes.
Overcurrent Protection
PTCs act as resettable fuses to protect circuits from damage due to overcurrent. When the current exceeds a threshold, the PTC heats up and its resistance increases sharply, limiting the current. It resets automatically once the fault is removed. Used in power supplies, motors, batteries etc.
Inrush Current Limiting
PTCs can limit the high inrush current drawn by capacitive and inductive loads during startup. The initial low resistance allows current flow, but as the PTC heats up, its resistance increases gradually to the steady state value, reducing the current. Used in switching power supplies, transformers, motor drives etc.
Heater Control
The self-heating effect of PTCs can be used to maintain a constant temperature in small heaters, deicers, and heater-sensors. As the temperature drops, the PTC resistance decreases allowing more current and heating. At the desired temperature, the resistance increases reducing the power.
Liquid Level Sensing
PTCs can detect the presence or absence of liquids based on their cooling effect. A self-heated PTC immersed in liquid will have lower resistance than in air or gas. The resistance change can indicate the liquid level.
Time Delay and Thermal Relay
By combining a PTC with a heating element and using its switching behavior, thermal time delay relays can be designed. The delay depends on the heating rate and PTC characteristics.
Advantages of PTC Thermistors
- High temperature coefficient and sensitivity
- Sharp, adjustable switching temperature
- Resettable and self-regulating behavior
- Simple, reliable and cost-effective
- Wide resistance and temperature range
- Variety of shapes, sizes and packaging
- Fast thermal response
- Excellent long term stability
Limitations of PTC Thermistors
- Nonlinear resistance-temperature characteristic
- Limited operating temperature range (-50 to 200°C)
- Hysteresis and self-heating effects
- Resistance tolerance and interchangeability
- Fragile and sensitive to mechanical shock
- Thermal lags and gradients
- Susceptible to environmental factors like humidity
Choosing the Right PTC Thermistor
Selecting the appropriate PTC thermistor for an application involves considering several factors:
- Operating temperature range and switching temperature
- Base resistance and maximum resistance change required
- Voltage, current and power rating
- Accuracy, stability and repeatability needed
- Response time and thermal time constant
- Mounting style, dimensions and terminations
- Environmental factors like vibration, humidity, chemicals
- Cost, availability and reliability
Manufacturers provide detailed datasheets specifying the characteristics, ratings, and performance curves of PTC thermistors. It’s essential to refer to these while designing the circuit and to test the PTC under actual operating conditions.
Frequently Asked Questions (FAQ)
1. What is the main difference between PTC and NTC thermistors?
PTC thermistors have a positive temperature coefficient, meaning their resistance increases with increasing temperature, while NTC (Negative Temperature Coefficient) thermistors have a resistance that decreases with increasing temperature. PTCs exhibit a sharp increase in resistance above a critical temperature, while NTCs have a more gradual change over a wider range.
2. Can PTC thermistors be used as temperature sensors?
Yes, PTC thermistors can be used as precision temperature sensors, especially for detecting small temperature changes around the switching point. Their high sensitivity and fast response make them suitable for temperature control applications. However, their nonlinear characteristic and narrow usable range need to be considered.
3. How do PTC thermistors provide overcurrent protection?
When the current through a PTC thermistor exceeds a certain level, the self-heating effect causes its temperature to rise above the switching point. This results in a sharp increase in resistance, which limits the current to a safe value. Once the fault is removed and the PTC cools down, its resistance returns to the low value, restoring normal operation. This resettable behavior is useful for protecting circuits from overcurrent damage.
4. What is the typical switching temperature range of PTC thermistors?
The switching temperature (Ts) of PTC thermistors can be customized between -50°C to 200°C by adjusting the composition of the ceramic material. The most common BaTiO3-based PTCs have a Ts around 120-130°C, while doped varieties can have lower or higher values. The choice depends on the specific application requirements.
5. Are PTC thermistors interchangeable with other types of temperature sensors?
PTC thermistors have unique characteristics that make them suitable for specific applications like switching, protection, and control. While they can be used for temperature sensing, they are not direct replacements for other sensors like RTDs, thermocouples, or NTC thermistors, which have different resistance-temperature characteristics, ranges, accuracies, and output signals. The choice of sensor depends on factors like temperature range, sensitivity, linearity, stability, and cost.
Conclusion
PTC thermistors are versatile temperature-sensitive devices with a wide range of applications in sensing, control, and protection. Their positive temperature coefficient and sharp switching behavior make them ideal for detecting temperature changes, regulating current, and providing thermal safety. Understanding their characteristics, advantages, and limitations is crucial for selecting and applying them effectively in various circuits and systems. With ongoing research and development in materials and manufacturing, PTC thermistors continue to evolve and find new uses in emerging technologies.
No responses yet