Introduction to Temperature Sensors
Temperature sensors are essential components in various industries, including automotive, aerospace, manufacturing, and consumer electronics. They play a crucial role in monitoring and controlling temperature-sensitive processes, ensuring optimal performance, and maintaining safety. Among the different types of temperature sensors available, Resistance Temperature Detectors (RTDs) stand out for their accuracy, stability, and wide temperature range.
What are Resistance Temperature Detectors (RTDs)?
Resistance Temperature Detectors (RTDs) are temperature sensors that rely on the principle of thermal expansion to measure temperature. They consist of a metal sensing element, typically made of platinum, nickel, or copper, whose electrical resistance changes with temperature. As the temperature increases, the metal expands, causing an increase in its electrical resistance. By measuring this change in resistance, the temperature can be accurately determined.
Advantages of RTDs
RTDs offer several advantages over other types of temperature sensors:
-
High accuracy: RTDs provide highly accurate temperature measurements, typically within ±0.1°C to ±0.2°C, making them suitable for applications that require precise temperature monitoring.
-
Wide temperature range: RTDs can operate over a wide temperature range, from -200°C to +850°C, depending on the type of metal used for the sensing element.
-
Excellent stability: RTDs exhibit excellent long-term stability, with minimal drift over time, ensuring reliable measurements throughout their lifespan.
-
Linearity: RTDs have a relatively linear relationship between resistance and temperature, simplifying the calibration process and enabling easy integration with control systems.
-
Interchangeability: RTDs are often interchangeable, meaning that they can be replaced without the need for recalibration, reducing maintenance costs and downtime.
Types of RTDs
There are several types of RTDs available, each with its own characteristics and suitable applications.
Platinum RTDs (PT100, PT1000)
Platinum RTDs are the most commonly used type of RTD due to their high accuracy, stability, and wide temperature range. They are available in two main variants: PT100 and PT1000.
-
PT100: PT100 RTDs have a nominal resistance of 100 ohms at 0°C and are widely used in industrial applications. They offer a temperature range of -200°C to +850°C and an accuracy of ±0.1°C to ±0.2°C.
-
PT1000: PT1000 RTDs have a nominal resistance of 1000 ohms at 0°C and are preferred in applications that require longer cable runs or improved noise immunity. They have a similar temperature range and accuracy to PT100 RTDs.
Nickel RTDs (Ni120)
Nickel RTDs, also known as Ni120 RTDs, have a nominal resistance of 120 ohms at 0°C. They are less expensive than platinum RTDs and offer a temperature range of -60°C to +250°C. However, they have lower accuracy (±0.5°C) and stability compared to platinum RTDs.
Copper RTDs (Cu10)
Copper RTDs, or Cu10 RTDs, have a nominal resistance of 10 ohms at 0°C. They are the least expensive type of RTD and are suitable for applications that require a narrow temperature range, typically -50°C to +150°C. Copper RTDs have lower accuracy (±1°C) and stability compared to platinum and nickel RTDs.
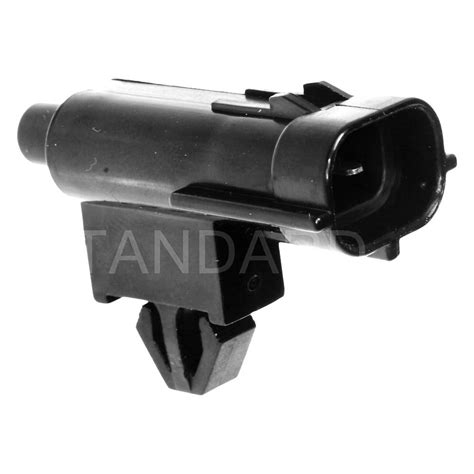
RTD Construction and Configuration
RTDs are constructed using different methods and configurations to suit various application requirements.
Wire-Wound RTDs
Wire-wound RTDs consist of a small coil of fine wire, typically platinum or nickel, wound around a ceramic or glass core. The wire is usually protected by a metal sheath or a ceramic tube. Wire-wound RTDs offer high accuracy and stability but have a relatively large size and slower response time compared to other types of RTDs.
Thin-Film RTDs
Thin-film RTDs are constructed by depositing a thin layer of platinum or nickel onto a ceramic substrate using techniques such as sputtering or chemical vapor deposition. The sensing element is then laser-trimmed to achieve the desired resistance value. Thin-film RTDs have a smaller size and faster response time than wire-wound RTDs but may have slightly lower accuracy and stability.
RTD Configurations
RTDs can be configured in different ways to suit specific application needs:
-
2-Wire Configuration: In a 2-wire configuration, the RTD is connected to the measuring instrument using two wires. This configuration is simple and cost-effective but can introduce measurement errors due to lead wire resistance.
-
3-Wire Configuration: A 3-wire configuration uses three wires to connect the RTD to the measuring instrument. This configuration compensates for lead wire resistance by using a Wheatstone Bridge circuit, improving measurement accuracy.
-
4-Wire Configuration: In a 4-wire configuration, two pairs of wires are used to connect the RTD to the measuring instrument. One pair carries the excitation current, while the other pair measures the voltage drop across the RTD. This configuration eliminates the effects of lead wire resistance, providing the highest accuracy.
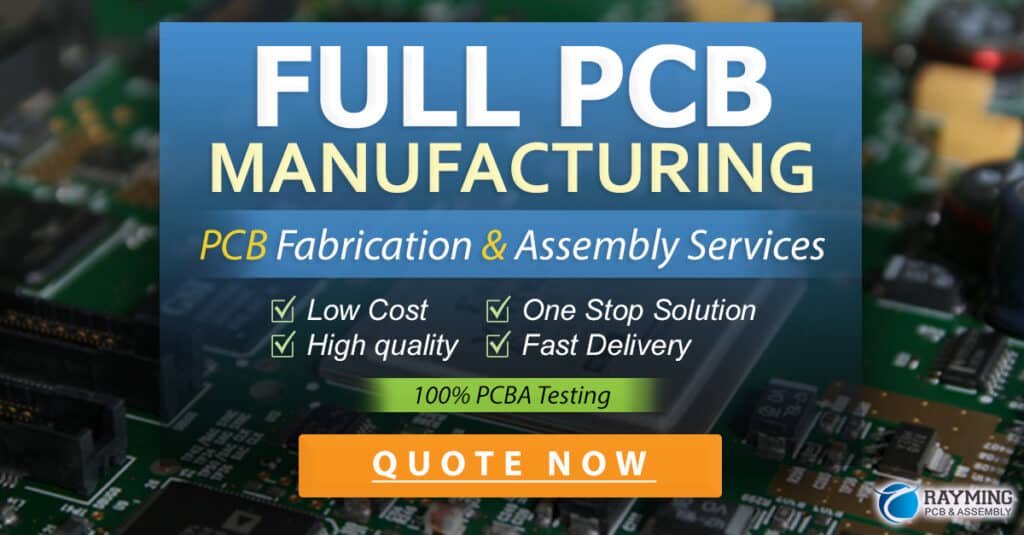
RTD Signal Conditioning and Measurement
To accurately measure temperature using RTDs, proper signal conditioning and measurement techniques are essential.
Wheatstone Bridge Circuit
RTDs are commonly used in combination with a Wheatstone bridge circuit for accurate temperature measurement. The Wheatstone bridge consists of four resistors, one of which is the RTD. By applying a known excitation voltage to the bridge and measuring the output voltage, the resistance of the RTD can be determined, and the corresponding temperature can be calculated.
Excitation Current
The excitation current used to measure the resistance of an RTD should be carefully selected to minimize self-heating effects. Self-heating occurs when the excitation current passing through the RTD generates heat, causing an increase in the sensor’s temperature and introducing measurement errors. Typical excitation currents range from 0.1 mA to 1 mA, depending on the type of RTD and the desired accuracy.
Linearization
While RTDs have a relatively linear relationship between resistance and temperature, some non-linearity exists, particularly at high temperatures. To achieve the highest accuracy, linearization techniques are employed to correct for this non-linearity. Linearization can be performed using lookup tables, polynomial equations, or dedicated integrated circuits (ICs) designed for RTD signal conditioning.
Temperature Calculation
Once the resistance of the RTD is measured, the corresponding temperature can be calculated using the Callendar-Van Dusen equation:
R(t) = R₀ [1 + At + Bt² + C(t-100)t³]
Where:
– R(t) is the resistance at temperature t
– R₀ is the resistance at 0°C
– A, B, and C are constants specific to the type of RTD
For most practical applications, a simplified linear approximation can be used:
R(t) = R₀ (1 + αt)
Where:
– α is the temperature coefficient of resistance, typically 0.00385 Ω/Ω/°C for platinum RTDs
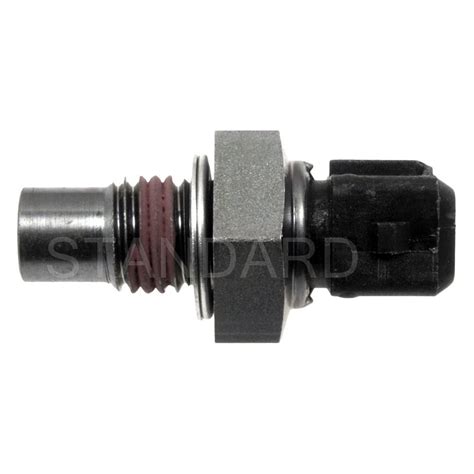
RTD Applications
RTDs find widespread use in various industries and applications due to their accuracy, stability, and wide temperature range.
Industrial Process Control
RTDs are extensively used in industrial process control applications, such as:
- Chemical processing plants
- Food and beverage manufacturing
- Pharmaceutical production
- Oil and gas refineries
In these applications, RTDs are used to monitor and control the temperature of fluids, gases, and surfaces to ensure optimal process conditions and product quality.
HVAC Systems
RTDs are commonly used in heating, ventilation, and air conditioning (HVAC) systems to monitor and control the temperature of air, water, and refrigerant. They are used in:
- Air handling units
- Chilled water systems
- Boilers and heat exchangers
- Room temperature monitoring
RTDs help maintain comfortable indoor environments and optimize energy efficiency in HVAC applications.
Automotive Industry
In the automotive industry, RTDs are used for various temperature sensing applications, including:
- Engine coolant temperature monitoring
- Exhaust gas temperature measurement
- Transmission fluid temperature sensing
- Cabin temperature control
RTDs help ensure optimal engine performance, emissions control, and passenger comfort in automotive applications.
Medical and Scientific Instrumentation
RTDs are used in medical and scientific instrumentation for accurate temperature measurement in applications such as:
- Laboratory equipment
- Sterilization processes
- Incubators and ovens
- Cryogenic systems
The high accuracy and stability of RTDs make them suitable for these demanding applications.
RTD Selection Considerations
When selecting an RTD for a specific application, several factors should be considered:
-
Temperature Range: Choose an RTD with a temperature range that covers the expected operating conditions of the application.
-
Accuracy and Stability: Consider the required accuracy and long-term stability of the temperature measurements, and select an RTD that meets those requirements.
-
Response Time: Evaluate the response time needed for the application and choose an RTD with a suitable time constant.
-
Vibration and Shock Resistance: In applications with high vibration or shock levels, select an RTD with appropriate mechanical construction and packaging.
-
Chemical Compatibility: Ensure that the RTD materials are compatible with the media being measured and the environment in which it will be installed.
-
Cost: Consider the overall cost of the RTD, including the sensor itself, signal conditioning equipment, and installation costs.
Frequently Asked Questions (FAQ)
1. What is the difference between an RTD and a thermocouple?
RTDs and thermocouples are both temperature sensors, but they operate on different principles. RTDs measure temperature by sensing changes in electrical resistance, while thermocouples measure temperature by generating a voltage due to the thermoelectric effect. RTDs generally offer higher accuracy and stability than thermocouples but have a more limited temperature range and slower response times.
2. Can RTDs be used in hazardous environments?
Yes, RTDs can be designed for use in hazardous environments, such as those with explosive atmospheres or corrosive media. In these cases, the RTD is typically housed in a protective enclosure or sheath made of materials suitable for the specific environment, such as stainless steel or Inconel.
3. How often should RTDs be calibrated?
The calibration frequency of RTDs depends on the specific application requirements, the criticality of the measurements, and the operating conditions. In general, RTDs should be calibrated at least once a year to ensure accurate temperature measurements. However, in some cases, more frequent calibration may be necessary, such as in applications with strict regulatory requirements or harsh operating conditions.
4. Can RTDs be used for surface temperature measurement?
Yes, RTDs can be used for surface temperature measurement by using specially designed surface-mount sensors. These sensors are typically constructed with a flat or curved sensing element that can be attached to the surface of interest using adhesives or mechanical fasteners. When using RTDs for surface temperature measurement, it is important to ensure good thermal contact between the sensor and the surface to minimize measurement errors.
5. How do I choose the right RTD configuration for my application?
The choice of RTD configuration (2-wire, 3-wire, or 4-wire) depends on the desired accuracy, the distance between the sensor and the measuring instrument, and the potential sources of measurement error. For short distances and less critical applications, a 2-wire configuration may be sufficient. For longer distances or applications requiring higher accuracy, a 3-wire or 4-wire configuration is recommended to compensate for lead wire resistance. In general, a 4-wire configuration provides the highest accuracy but also requires more wiring and a compatible measuring instrument.
Conclusion
Resistance Temperature Detectors (RTDs) are highly accurate and stable temperature sensors that are widely used in various industries and applications. By understanding the principles of operation, types, construction, and signal conditioning techniques of RTDs, engineers and technicians can effectively select and implement these sensors in their temperature measurement projects.
When designing an RTD-based temperature measurement system, it is important to consider factors such as temperature range, accuracy, stability, response time, and environmental conditions. Proper selection and installation of RTDs, along with appropriate signal conditioning and calibration, ensure reliable and precise temperature measurements.
As technology advances, RTDs continue to evolve, with ongoing developments in materials, construction techniques, and signal conditioning methods. These advancements aim to further improve the accuracy, stability, and reliability of RTDs, making them an indispensable tool in temperature measurement applications.
No responses yet