Introduction to TDR Measurements
Time-domain reflectometry (TDR) is a measurement technique used to determine the characteristics of electrical lines by observing reflected waveforms. It can be used to locate and characterize faults, discontinuities, and impedance variations in transmission lines, cables, connectors, and other conductors.
TDR works by sending a fast rise time pulse along the conductor and then analyzing the reflections that return from any impedance discontinuities along the line. By measuring the time delay and amplitude of the reflected waveforms, the distance to the fault and the nature of the impedance change (open, short, resistive, inductive, or capacitive) can be determined.
TDR has become an invaluable tool for maintenance, troubleshooting, quality control, and failure analysis of wired communication and power distribution systems. Some key applications of TDR include:
- Locating cable faults such as opens, shorts, crimps, kinks, and partial discharge
- Detecting water ingress and degradation in cable insulation and jackets
- Measuring the length of cables and the distance to splices and connectors
- Verifying cable impedance, velocity factor, and dielectric constant
- Analyzing the impedance profile along a line to identify structural return loss
- Evaluating connectors, splices, and other components for proper installation
- Optimizing cable systems for high-frequency signal integrity
In this article, we will delve into the principles of TDR, the setup and execution of TDR measurements, and the interpretation of TDR traces to determine the nature and location of faults in transmission lines. We will also discuss some advanced TDR techniques and provide guidance on selecting the right TDR instrument for your application.
Principles of Time Domain Reflectometry
Transmission Line Theory
To understand how TDR works, it is helpful to first review some basic concepts of transmission line theory. A transmission line is a specialized cable or conductor designed to carry high-frequency electrical signals with minimal loss and distortion. Coaxial cable, twisted pair, and parallel wire are common types of transmission lines used in communications and electronics.
An ideal transmission line has the following properties:
- Uniform cross-section and material along its length
- Constant characteristic impedance (Z0)
- Lossless (no attenuation)
- Linear (no distortion)
The characteristic impedance of a transmission line is determined by its geometry and the dielectric properties of its insulating material. For a coaxial cable, the characteristic impedance is given by:
Z0 = (138 / √εr) × log10(D/d)
Where:
– εr is the relative dielectric constant of the insulating material
– D is the inner diameter of the outer conductor
– d is the outer diameter of the inner conductor
When a voltage is applied to one end of a transmission line, an electromagnetic wave propagates along the line at a velocity determined by the dielectric constant of the insulating material. The velocity factor (VF) of a transmission line is the ratio of the propagation velocity to the speed of light in a vacuum (c = 3×108 m/s).
VF = 1 / √εr
For common dielectric materials used in coaxial cables, the velocity factor ranges from 0.66 (polyethylene) to 0.88 (foam polyethylene).
If the transmission line is terminated with a load impedance (ZL) equal to its characteristic impedance (Z0), the electromagnetic wave is completely absorbed by the load and no reflection occurs. This is known as a matched termination.
However, if the load impedance differs from the characteristic impedance, a portion of the incident wave is reflected back towards the source. The reflection coefficient (ρ) is a measure of the fraction of the incident voltage that is reflected by the load.
ρ = (ZL – Z0) / (ZL + Z0)
The reflection coefficient ranges from -1 (short circuit) to +1 (open circuit), with 0 indicating a matched load.
TDR Fundamentals
In a TDR measurement, a fast rise time voltage step (typically < 1 ns) is launched into the transmission line under test. As the incident wave encounters impedance discontinuities along the line, a portion of the voltage is reflected back towards the source while the remaining voltage continues to propagate forward.
By measuring the time delay between the incident and reflected waves, and knowing the propagation velocity of the cable, the distance to the impedance discontinuity can be calculated:
Distance = (Velocity × Time) / 2
The factor of 2 accounts for the round trip travel time of the wave.
The amplitude and polarity of the reflected wave provide information about the nature of the impedance discontinuity. For example:
- An open circuit (ZL = ∞) results in a positive reflection coefficient and a reflected wave with the same polarity as the incident wave.
- A short circuit (ZL = 0) results in a negative reflection coefficient and a reflected wave with opposite polarity to the incident wave.
- A resistive termination (ZL > Z0) results in a positive reflection coefficient and a reflected wave with reduced amplitude compared to the incident wave.
- An inductive termination results in a positive reflection coefficient and a reflected wave with a trailing edge.
- A capacitive termination results in a negative reflection coefficient and a reflected wave with a leading edge.
By analyzing the shape, amplitude, and timing of the reflected waveforms, the type and location of impedance discontinuities along the transmission line can be determined.
TDR Measurement Setup and Execution
Instrument Selection
To perform TDR measurements, a specialized instrument called a time domain reflectometer is required. TDR instruments typically consist of a fast rise time pulse generator, a sampling oscilloscope, and a display for viewing the reflected waveforms.
Key specifications to consider when selecting a TDR instrument include:
- Pulse rise time: Determines the spatial resolution and ability to detect small discontinuities. Rise times of 100 ps to 1 ns are typical.
- Vertical resolution: Determines the ability to measure small changes in impedance. 8 to 16 bits is typical.
- Record length: Determines the maximum cable length that can be tested. Longer record lengths allow for testing of longer cables.
- Noise floor: Determines the minimum detectable reflection amplitude. Lower noise floors allow for detection of smaller faults.
- Input impedance: Should match the characteristic impedance of the cable under test (50, 75, or 100 Ω).
- Connectivity: USB, Ethernet, or wireless interfaces allow for remote control and data transfer.
Some additional features that can be useful for TDR measurements include:
- Dual cursors for measuring distance and time intervals
- Zoom and pan functions for analyzing waveform details
- Waveform averaging and smoothing to reduce noise
- Cable template libraries for quick setup and fault identification
- Reporting and documentation tools
Cable Connection and Setup
To connect the TDR instrument to the cable under test, a coaxial adapter or test probe is used. The adapter should have the same connector type and impedance as the cable.
It is important to ensure a good electrical connection between the adapter and cable, as any gaps or misalignment can create unwanted reflections. A calibration standard, such as an open, short, or matched load, can be used to verify the proper operation of the adapter and TDR instrument.
The far end of the cable should be left open or terminated with a known load impedance. If the cable is part of a larger system, it may be necessary to disconnect it from other components to avoid interference or damage.
Measurement Settings and Techniques
Before starting a TDR measurement, the following settings should be configured on the instrument:
- Vertical scale: Set to display the expected range of impedance variations, typically ±50% of the cable impedance.
- Horizontal scale: Set to display the expected length of the cable, typically 1-2 times the physical length.
- Pulse width: Set to achieve the desired spatial resolution, typically 1-10 ns.
- Averaging: Set to reduce noise and improve repeatability, typically 16-256 waveforms.
Once the settings are configured, the TDR measurement can be initiated by pressing the “Start” or “Single” button on the instrument. The incident pulse and reflected waveforms will be displayed on the screen.
To analyze the waveforms, the following techniques can be used:
- Cursor measurements: Use the vertical cursors to measure the impedance at specific points along the waveform. Use the horizontal cursors to measure the distance between two points.
- Zoom and pan: Use the zoom and pan functions to examine specific regions of the waveform in more detail.
- Waveform comparison: Use the instrument’s memory or reference functions to compare the current waveform to a previously stored or ideal waveform.
- Multi-segment testing: For long cables or cables with multiple sections, use the instrument’s gating or windowing functions to isolate and test each section separately.
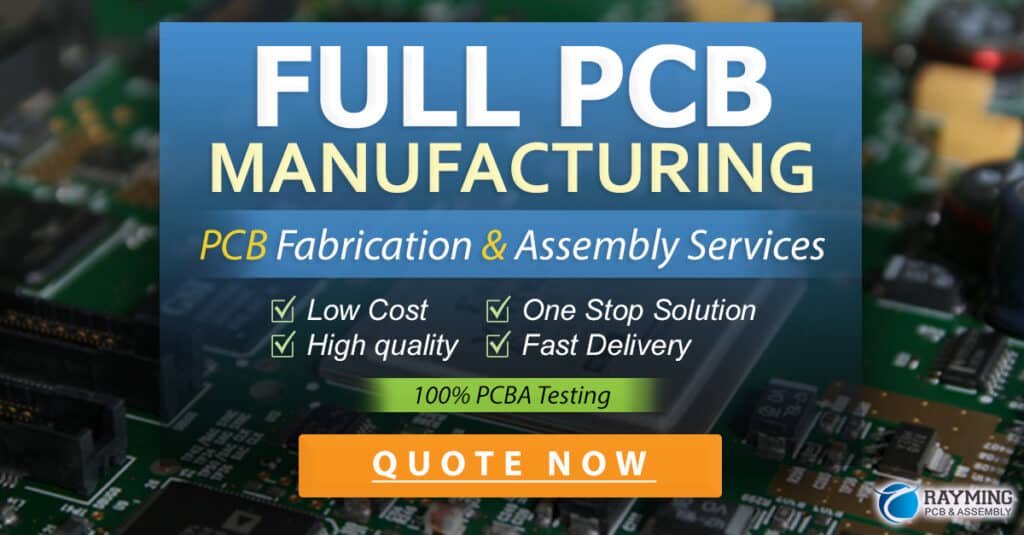
Interpreting TDR Traces
Identifying Common Faults
By analyzing the shape, amplitude, and timing of the reflected waveforms, common faults in transmission lines can be identified:
Fault Type | TDR Signature |
---|---|
Open | Positive reflection, same polarity as incident wave |
Short | Negative reflection, opposite polarity as incident wave |
Resistive | Positive or negative reflection, reduced amplitude |
Inductive | Positive reflection with trailing edge |
Capacitive | Negative reflection with leading edge |
Impedance mismatch | Positive or negative reflection at impedance change |
Partial open | Positive reflection with reduced amplitude |
Partial short | Negative reflection with reduced amplitude |
Water ingress | Negative reflection with reduced amplitude and increased loss |
Crushed or kinked cable | Positive or negative reflection with increased loss and possible reflections from sharp bends |
Locating Faults
To determine the location of a fault, the time delay between the incident and reflected waveforms is measured using the horizontal cursors on the TDR display. This time delay is then converted to distance using the propagation velocity of the cable.
For example, suppose a TDR measurement on a 50 m coaxial cable with a velocity factor of 0.66 shows a positive reflection at 25 ns after the incident pulse. The distance to the fault can be calculated as:
Distance = (0.66 × 3×108 m/s × 25×10-9 s) / 2 = 24.75 m
This indicates that the fault is located approximately 24.75 m from the TDR connection point.
It is important to note that the accuracy of fault location depends on several factors, including:
- The accuracy of the cable’s velocity factor and length
- The rise time and sampling rate of the TDR instrument
- The presence of multiple reflections or attenuation in the cable
- The type and size of the fault
In some cases, it may be necessary to use additional techniques, such as time-frequency analysis or signal processing, to improve the accuracy and resolution of fault location.
Advanced TDR Techniques
While basic TDR measurements can identify and locate many common faults in transmission lines, some faults may require more advanced techniques to detect and characterize. Some examples of advanced TDR techniques include:
-
Time-frequency analysis: By applying signal processing techniques such as wavelet transforms or short-time Fourier transforms to the TDR waveforms, the frequency content of the reflections can be analyzed. This can help to identify faults that have a specific frequency signature, such as partial discharge or high-frequency attenuation.
-
Noise reduction: By using waveform averaging, filtering, or deconvolution techniques, the noise level in the TDR waveforms can be reduced. This can help to detect smaller or more subtle faults that may be masked by noise.
-
Impedance deconvolution: By applying inverse filtering techniques to the TDR waveforms, the impedance profile along the cable can be reconstructed. This can help to identify the location and magnitude of impedance variations, even in the presence of multiple reflections or attenuation.
-
Time-domain transmission (TDT): By measuring the transmission characteristics of the cable in addition to the reflection characteristics, the effects of attenuation and dispersion can be analyzed. This can help to identify faults that cause frequency-dependent losses or phase shifts.
FAQ
What is the maximum length of cable that can be tested with TDR?
The maximum length of cable that can be tested with TDR depends on the specifications of the TDR instrument, particularly the record length and pulse width. Longer cables require longer record lengths to capture the entire reflected waveform, while shorter pulses are needed to resolve closely spaced faults.
Typical TDR instruments can test cables up to several kilometers in length, with a resolution of a few centimeters to a few meters. However, the maximum length may be limited by the attenuation and dispersion of the cable, which can reduce the amplitude and clarity of the reflected waveforms.
Can TDR detect faults in live cables?
TDR measurements are typically performed on disconnected or de-energized cables to avoid interference or damage to the TDR instrument or other equipment. However, some specialized TDR instruments are designed for live cable testing, using low-voltage pulses or high-impedance probes to minimize the impact on the cable system.
Live cable testing with TDR requires careful consideration of safety hazards and potential disruption to the cable system. It is important to consult with the cable manufacturer or system operator before attempting any live testing.
How do you interpret TDR traces for complex cable systems?
Interpreting TDR traces for complex cable systems with multiple branches, splices, or impedance variations can be challenging. The reflected waveforms may contain multiple overlapping or interfering reflections, making it difficult to identify and locate specific faults.
To interpret complex TDR traces, the following strategies can be used:
- Use cable documentation or diagrams to identify the expected locations of branches, splices, or other components.
- Use the cursor and zoom functions to isolate and analyze specific regions of the waveform.
- Compare the measured waveform to a reference or baseline waveform to identify changes or anomalies.
- Use signal processing techniques such as time-frequency analysis or impedance deconvolution to separate and characterize individual reflections.
- Perform multiple measurements from different points in the cable system to triangulate the location of faults.
Interpreting complex TDR traces requires experience and expertise in transmission line theory and signal analysis. It may be necessary to consult with a qualified engineer or technician to assist with the interpretation.
How often should TDR testing be performed on transmission lines?
The frequency of TDR testing on transmission lines depends on several factors, including:
- The criticality and reliability requirements of the cable system
- The age and condition of the cables
- The environmental and operational stresses on the cables
- The history of faults or failures in the cable system
In general, TDR testing should be performed:
- During installation or commissioning of new cables to verify proper installation and performance
- Periodically as part of a preventive maintenance program to detect and track degradation over time
- After any repairs or modifications to the cable system to verify the integrity of the work
- Whenever a fault or failure occurs in the cable system to identify and locate the cause
The specific frequency of TDR testing should be determined based on a risk assessment and cost-benefit analysis of the cable system. Some industry standards and best practices provide guidance on TDR testing intervals for different types of cables and applications.
Can TDR detect faults in other types of conductors besides transmission lines?
Yes, TDR can be used to detect faults in a wide range of conductors beyond transmission lines, including:
- Power cables and distribution lines
- Communication cables and networks
- Control and instrumentation cables
- Antenna and RF feedlines
- Printed circuit board traces and vias
- Wiring harnesses and cable assemblies
The principles and techniques of TDR are applicable to any conductor that can support the propagation of electromagnetic waves. However, the specific measurement settings, fault signatures, and interpretation methods may vary depending on the type and characteristics of the conductor.
For example, TDR testing of power cables may require higher voltage pulses and longer record lengths to account for the larger conductor size and lower propagation velocity. TDR testing of printed circuit boards may require higher bandwidth pulses and smaller probes to resolve the closely spaced traces and vias.
In each case, it is important to select a TDR instrument and accessories that are appropriate for the specific conductor type and application, and to follow industry standards and best practices for safe and effective testing.
Conclusion
TDR is a powerful and versatile tool for detecting, locating, and characterizing faults in transmission lines and other conductors. By analyzing the reflected waveforms from a fast rise time pulse, TDR can provide insights into the impedance profile, discontinuities, and degradation of cables over distance and time.
Effective TDR testing requires a combination of theoretical knowledge, practical skills, and experience in transmission line theory, signal analysis, and fault interpretation. By selecting the appropriate TDR instrument and accessories, configuring the optimal measurement settings, and applying advanced signal processing techniques, TDR can help to ensure the reliability, performance, and safety of critical cable systems.
As cable systems continue to evolve in complexity and criticality, TDR will remain an essential tool for maintenance, troubleshooting, and quality assurance. By staying up-to-date with the latest TDR technologies and best practices, engineers
No responses yet