Introduction to Taconic PCB
Taconic PCB, also known as Taconic Printed Circuit Boards, is a specialized type of PCB that utilizes high-performance materials manufactured by Taconic, a leading company in the electronics industry. Taconic PCBs are renowned for their exceptional electrical properties, thermal stability, and mechanical strength, making them ideal for demanding applications in various sectors, including aerospace, defense, telecommunications, and high-speed digital electronics.
What Makes Taconic PCBs Unique?
Taconic PCBs stand out from traditional PCBs due to the use of advanced substrate materials developed by Taconic. These materials exhibit superior characteristics, such as:
- Low dielectric constant and dissipation factor
- Excellent thermal stability and conductivity
- High resistance to moisture absorption
- Excellent dimensional stability
- Superior signal integrity and reduced signal loss
These properties enable Taconic PCBs to deliver optimal performance in high-frequency and high-speed applications, where signal integrity and reliability are critical.
Taconic PCB Materials
Taconic offers a wide range of PCB materials, each designed to cater to specific application requirements. Some of the most popular Taconic PCB materials include:
RF-35
RF-35 is a low-loss, high-frequency laminate material that offers excellent electrical properties up to 40 GHz. It features a low dielectric constant (3.5) and a low dissipation factor (0.0018), making it suitable for applications such as wireless communications, radar systems, and satellite receivers.
TLY
TLY is a low-loss, high-performance material designed for high-speed digital applications. It offers a low dielectric constant (2.2) and a low dissipation factor (0.0009), ensuring minimal signal loss and optimal signal integrity. TLY is commonly used in high-speed networking, data centers, and telecom equipment.
TLX
TLX is an ultra-low-loss material that provides exceptional performance up to 77 GHz. With a dielectric constant of 2.45 and a dissipation factor of 0.0019, TLX is ideal for demanding applications such as automotive radar, 5G telecommunications, and millimeter-wave systems.
TSM
TSM is a high-performance, low-loss material designed for multilayer PCBs. It offers a low dielectric constant (3.0) and a low dissipation factor (0.0025), making it suitable for applications that require a balance between electrical performance and cost-effectiveness.
Material | Dielectric Constant | Dissipation Factor | Typical Applications |
---|---|---|---|
RF-35 | 3.5 | 0.0018 | Wireless communications, radar systems, satellite receivers |
TLY | 2.2 | 0.0009 | High-speed networking, data centers, telecom equipment |
TLX | 2.45 | 0.0019 | Automotive radar, 5G telecommunications, millimeter-wave systems |
TSM | 3.0 | 0.0025 | Multilayer PCBs, cost-sensitive applications |
Designing with Taconic PCBs
When designing Taconic PCBs, several considerations must be taken into account to ensure optimal performance and reliability.
Material Selection
Choosing the appropriate Taconic material is crucial for achieving the desired electrical and mechanical properties. Factors such as operating frequency, signal integrity requirements, thermal management, and cost should be considered when selecting the material.
Impedance Control
Maintaining precise impedance control is essential for high-speed and high-frequency applications. Taconic materials offer stable dielectric constants, allowing for accurate impedance calculations and controlled impedance designs. Designers should work closely with PCB fabricators to ensure that the desired impedance values are achieved.
Layout and Routing
Proper layout and routing techniques are critical for minimizing signal integrity issues, such as crosstalk, reflections, and electromagnetic interference (EMI). Some best practices include:
- Minimizing trace lengths and avoiding unnecessary bends
- Maintaining consistent trace widths and spacing
- Using ground planes and shielding to reduce EMI
- Implementing proper termination and matching techniques
Thermal Management
Taconic PCBs often handle high-power and high-frequency signals, generating significant amounts of heat. Effective thermal management strategies should be employed to dissipate heat and prevent performance degradation. This can include the use of thermal vias, heat sinks, and advanced cooling techniques, such as liquid cooling or heat pipes.
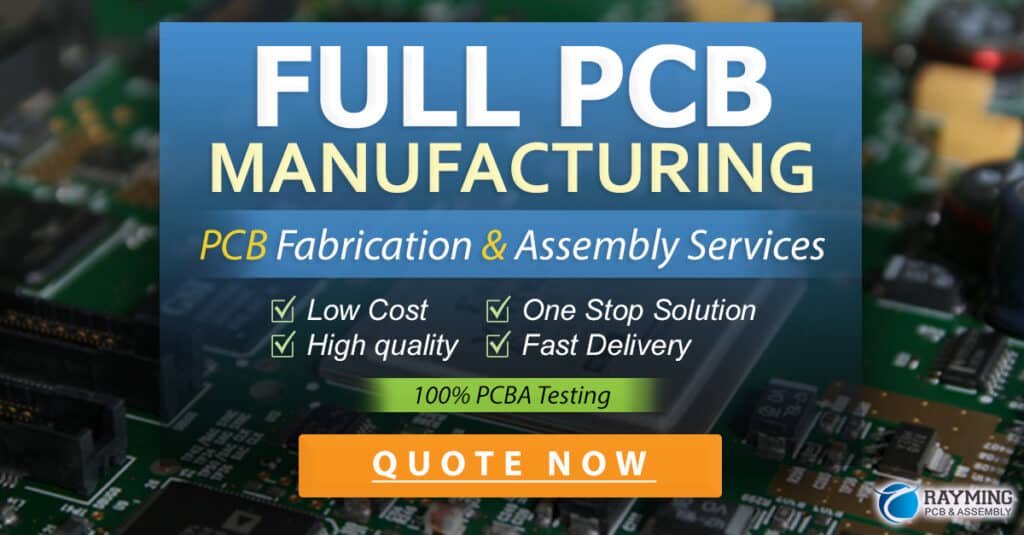
Manufacturing Taconic PCBs
Manufacturing Taconic PCBs requires specialized expertise and equipment due to the unique properties of Taconic materials. It is essential to partner with a reputable PCB fabricator experienced in handling Taconic materials to ensure the highest quality and reliability.
Fabrication Process
The fabrication process for Taconic PCBs generally follows these steps:
- Material preparation and cutting
- Drilling and plating of through-holes and vias
- Patterning and etching of conductive layers
- Lamination of multiple layers (for multilayer PCBs)
- Surface finish application (e.g., ENIG, HASL, or OSP)
- Electrical testing and quality inspection
Quality Control
Stringent quality control measures should be implemented throughout the manufacturing process to ensure that Taconic PCBs meet the required specifications and performance standards. This includes:
- Visual inspection for defects and workmanship issues
- Electrical testing to verify signal integrity and functionality
- Dimensional and mechanical checks to ensure conformance to design specifications
- Thermal and environmental testing to validate reliability under various operating conditions
Applications of Taconic PCBs
Taconic PCBs find applications in a wide range of industries and sectors, where high performance, reliability, and signal integrity are paramount. Some of the most common applications include:
Aerospace and Defense
Taconic PCBs are extensively used in aerospace and defense systems, such as radar, navigation, and communication equipment. The low-loss and high-frequency capabilities of Taconic materials make them ideal for these demanding applications.
Telecommunications
The proliferation of 5G networks and high-speed data transmission has driven the adoption of Taconic PCBs in telecommunications equipment, such as base stations, antennas, and signal processing units.
Automotive Electronics
Advanced driver assistance systems (ADAS), automotive radar, and in-vehicle infotainment systems rely on Taconic PCBs for their high-frequency performance and reliability in harsh automotive environments.
Medical Devices
Taconic PCBs are used in medical imaging systems, such as MRI and CT scanners, where high-frequency signal processing and low-loss properties are essential for accurate diagnostics.
Industrial Automation
High-speed data acquisition, motion control, and industrial networking applications benefit from the superior signal integrity and reliability offered by Taconic PCBs.
Frequently Asked Questions (FAQ)
-
What are the advantages of using Taconic PCBs over traditional PCBs?
Taconic PCBs offer superior electrical properties, such as low dielectric constant, low dissipation factor, and excellent signal integrity, making them ideal for high-frequency and high-speed applications. They also exhibit excellent thermal stability, mechanical strength, and resistance to moisture absorption. -
Can Taconic PCBs be used for multilayer designs?
Yes, Taconic materials, such as TSM, are specifically designed for multilayer PCB applications. They offer low-loss properties and good dimensional stability, enabling the fabrication of complex, high-density multilayer boards. -
Are Taconic PCBs more expensive than traditional PCBs?
Due to the advanced materials and specialized manufacturing processes involved, Taconic PCBs are generally more expensive than traditional PCBs. However, the superior performance and reliability offered by Taconic PCBs often justify the added cost in demanding applications. -
How do I select the appropriate Taconic material for my application?
Selecting the appropriate Taconic material depends on various factors, such as operating frequency, signal integrity requirements, thermal management needs, and cost constraints. It is recommended to consult with Taconic or an experienced PCB designer to determine the most suitable material for your specific application. -
Can Taconic PCBs be manufactured by any PCB fabricator?
While many PCB fabricators can handle Taconic materials, it is essential to partner with a reputable fabricator that has experience and expertise in working with Taconic PCBs. This ensures that the PCBs are manufactured to the highest quality standards and meet the required specifications.
Conclusion
Taconic PCBs offer a superior solution for demanding applications that require exceptional electrical performance, signal integrity, and reliability. By leveraging advanced Taconic materials and proper design and manufacturing techniques, engineers and designers can create PCBs that push the boundaries of high-frequency and high-speed electronics.
When considering Taconic PCBs for your next project, it is crucial to carefully evaluate your application requirements, select the appropriate Taconic material, and partner with an experienced PCB fabricator. By doing so, you can unlock the full potential of Taconic PCBs and deliver cutting-edge products that meet the ever-increasing demands of modern electronics.
No responses yet