Introduction to Inventory Sync
In today’s fast-paced business environment, managing your electronics inventory effectively is crucial for success. An essential aspect of efficient inventory management is ensuring that your inventory data is synchronized across all platforms, including your cloud-based system. Inventory Sync is the process of seamlessly connecting your various inventory management tools, such as your point-of-sale (POS) system, enterprise resource planning (ERP) software, and e-commerce platforms, with your cloud-based inventory management system.
By implementing Inventory Sync, you can streamline your inventory management processes, reduce errors, and improve overall efficiency. This comprehensive guide will explore the benefits of Inventory Sync, the key components of a successful implementation, and best practices for maintaining a synchronized inventory management system.
The Benefits of Inventory Sync
Improved Accuracy
One of the primary advantages of Inventory Sync is the significant improvement in inventory accuracy. By automatically updating your cloud-based inventory management system with real-time data from your various sales channels and inventory management tools, you can eliminate manual data entry and reduce the risk of human error. This ensures that your inventory levels are always accurate, enabling you to make informed decisions about stock replenishment and order fulfillment.
Enhanced Efficiency
Inventory Sync streamlines your inventory management processes, saving time and resources. With automated data synchronization, you no longer need to manually update inventory levels across multiple platforms. This frees up your staff to focus on more valuable tasks, such as customer service and sales. Additionally, a synchronized inventory management system enables you to quickly identify and address any discrepancies or issues, further improving efficiency.
Real-time Visibility
By syncing your inventory data across all platforms, you gain real-time visibility into your stock levels, sales trends, and other critical metrics. This up-to-date information empowers you to make data-driven decisions, such as adjusting stock levels based on demand, identifying top-selling products, and optimizing your pricing strategy. Real-time visibility also helps you avoid stockouts and overstocking, ensuring that you always have the right products available to meet customer demand.
Seamless Multi-channel Management
In today’s omnichannel retail landscape, managing inventory across multiple sales channels can be challenging. Inventory Sync simplifies multi-channel management by ensuring that your inventory data is consistent and up-to-date across all platforms. Whether you’re selling through your brick-and-mortar store, e-commerce website, or online marketplaces like Amazon and eBay, Inventory Sync keeps your stock levels in sync, preventing overselling and ensuring a seamless customer experience.
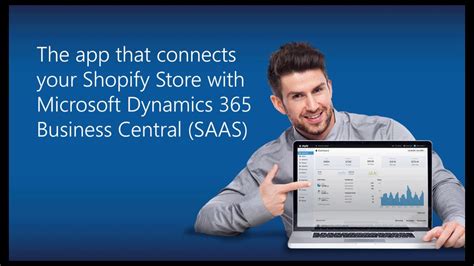
Key Components of Inventory Sync
To successfully implement Inventory Sync, it’s essential to understand the key components that make up a synchronized inventory management system.
Cloud-based Inventory Management System
At the heart of Inventory Sync is a cloud-based inventory management system. This centralized platform serves as the hub for all your inventory data, providing a single source of truth for your stock levels, sales data, and other critical metrics. A cloud-based system offers several advantages, including accessibility from anywhere with an internet connection, scalability to accommodate business growth, and automatic updates and backups.
Integration with Sales Channels and Inventory Management Tools
To achieve seamless Inventory Sync, your cloud-based inventory management system must integrate with your various sales channels and inventory management tools. This includes your POS system, ERP software, e-commerce platforms, and any other tools you use to manage your inventory and sales. Integration ensures that data flows automatically between these systems, eliminating the need for manual data entry and reducing the risk of errors.
Automated Data Synchronization
Automated data synchronization is the process of automatically updating your cloud-based inventory management system with data from your sales channels and inventory management tools. This can be achieved through APIs (Application Programming Interfaces) or other integration methods, depending on the systems you’re using. Automated data synchronization ensures that your inventory data is always up-to-date, providing you with real-time visibility into your stock levels and sales trends.
Data Security and Backup
When implementing Inventory Sync, it’s crucial to ensure the security and integrity of your inventory data. Your cloud-based inventory management system should employ robust security measures, such as encryption, access controls, and regular backups, to protect your data from unauthorized access and potential data loss. Additionally, it’s essential to choose a reputable cloud service provider that adheres to industry-standard security practices and offers reliable uptime and support.
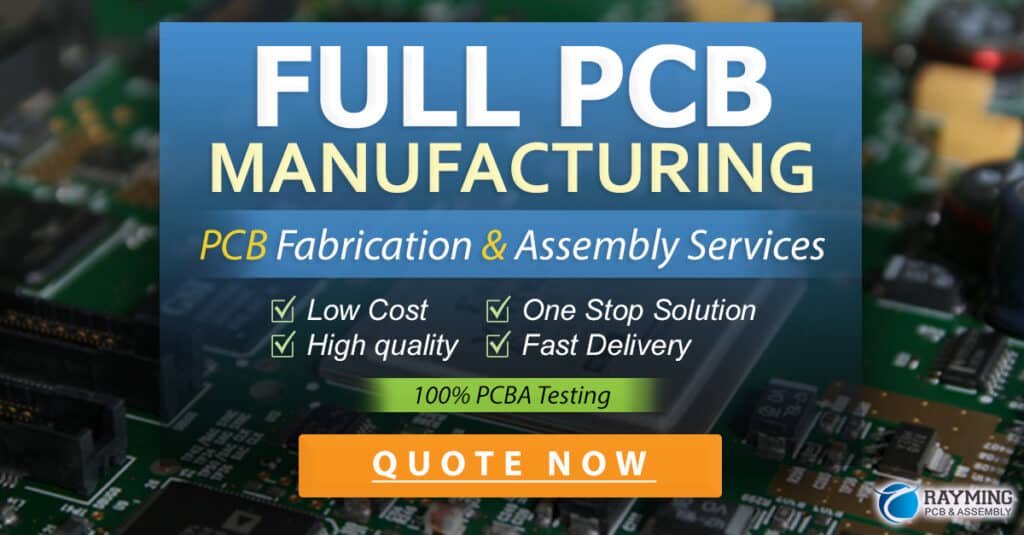
Best Practices for Maintaining Inventory Sync
To ensure the ongoing success of your Inventory Sync implementation, consider the following best practices:
Regular System Audits
Conduct regular audits of your inventory management system to ensure that your data is accurate and up-to-date. This involves comparing your physical inventory levels with the data in your cloud-based system and investigating any discrepancies. Regular audits help you identify and address any issues before they become significant problems, ensuring the ongoing accuracy and reliability of your inventory data.
Staff Training and Adoption
Ensure that your staff is properly trained on using your synchronized inventory management system. This includes understanding how to access and interpret inventory data, as well as how to handle any issues that may arise. Encourage staff adoption by highlighting the benefits of Inventory Sync, such as increased efficiency and reduced workload. Regularly gather feedback from your team to identify areas for improvement and ensure that everyone is comfortable with the system.
Continuous Improvement
Continuously monitor and optimize your Inventory Sync implementation to ensure that it remains effective and efficient. This may involve updating your integrations as new features become available, fine-tuning your data synchronization processes, or exploring new tools and technologies to further streamline your inventory management. By embracing a culture of continuous improvement, you can ensure that your Inventory Sync implementation remains a valuable asset to your business.
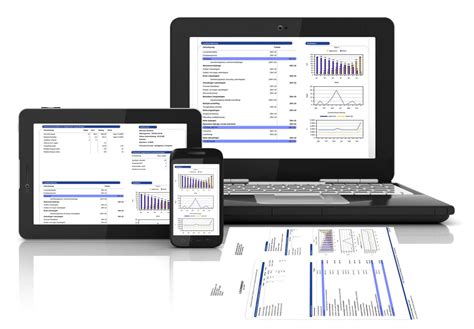
Inventory Sync Implementation: A Step-by-Step Guide
Now that we’ve explored the benefits and key components of Inventory Sync, let’s dive into the step-by-step process of implementing a synchronized inventory management system.
Step 1: Assess Your Current Inventory Management System
Before implementing Inventory Sync, it’s essential to assess your current inventory management system to identify areas for improvement and determine the specific requirements for your synchronized system. This assessment should include:
- Identifying your current inventory management tools and sales channels
- Evaluating the accuracy and efficiency of your current processes
- Determining the key metrics and data points you need to track
- Assessing your current data security and backup measures
Step 2: Choose a Cloud-based Inventory Management System
Based on your assessment, select a cloud-based inventory management system that meets your specific needs. Consider factors such as:
- Scalability to accommodate future growth
- Integration capabilities with your existing tools and sales channels
- User-friendliness and ease of adoption
- Data security and backup features
- Customer support and resources
Some popular cloud-based inventory management systems include:
System | Key Features | Pricing |
---|---|---|
TradeGecko | – Robust integration capabilities – Automated order fulfillment – Detailed reporting and analytics |
Starting at $79/month |
Zoho Inventory | – Multi-channel sales management – Batch and serial number tracking – Customizable workflows |
Starting at $59/month |
Cin7 | – Advanced demand forecasting – Warehouse management – B2B eCommerce platform |
Custom pricing based on business needs |
Step 3: Integrate Your Sales Channels and Inventory Management Tools
Once you’ve chosen your cloud-based inventory management system, it’s time to integrate your existing sales channels and inventory management tools. This process will vary depending on the specific systems you’re using but typically involves the following steps:
- Identify the integration methods available for your systems (e.g., APIs, pre-built connectors, or custom integrations)
- Set up the necessary connections and authenticate your accounts
- Map your data fields to ensure that information is accurately transferred between systems
- Test the integration to ensure that data is flowing correctly and address any issues that arise
Step 4: Configure Your Data Synchronization Settings
With your integrations in place, configure your data synchronization settings to ensure that your inventory data is updating at the appropriate intervals. This may involve setting up real-time synchronization for critical data points, such as stock levels and sales transactions, while using scheduled synchronization for less time-sensitive data, such as product information and customer details.
Step 5: Train Your Staff and Launch Your Synchronized System
Before launching your synchronized inventory management system, ensure that your staff is properly trained on how to use the new tools and processes. Provide comprehensive training sessions, user guides, and ongoing support to ensure a smooth transition. Once your team is comfortable with the new system, launch your Inventory Sync implementation and begin enjoying the benefits of streamlined, accurate inventory management.
Frequently Asked Questions (FAQ)
-
Q: How long does it typically take to implement Inventory Sync?
A: The implementation timeline for Inventory Sync varies depending on the complexity of your existing systems and the specific requirements of your business. On average, the process can take anywhere from a few weeks to several months, depending on factors such as the number of integrations required, the volume of data to be synchronized, and the resources available for the project. -
Q: Can I synchronize my inventory data across multiple warehouses or locations?
A: Yes, most cloud-based inventory management systems support multi-warehouse and multi-location inventory management. By setting up separate stock locations within your system and configuring your data synchronization settings accordingly, you can ensure that your inventory data is accurate and up-to-date across all your warehouses and sales channels. -
Q: What happens if there’s a discrepancy between my physical inventory levels and the data in my synchronized system?
A: If you notice a discrepancy between your physical inventory levels and the data in your synchronized system, it’s essential to investigate the issue promptly. Start by conducting a physical inventory count to verify the actual stock levels and compare them with the data in your system. If the discrepancy persists, review your data synchronization settings and integrations to identify any potential issues, such as incorrect data mapping or delayed updates. Regular system audits can help prevent and detect such discrepancies early on. -
Q: Can I integrate my custom-built inventory management tools with a cloud-based system?
A: In most cases, yes. Many cloud-based inventory management systems offer APIs and custom integration capabilities that allow you to connect your custom-built tools and databases. However, the complexity of the integration process will depend on the specific requirements of your custom tools and the available documentation and support from your cloud-based system provider. It’s essential to thoroughly assess the integration capabilities of your chosen system and consult with their support team to determine the feasibility of integrating your custom tools. -
Q: How much does it cost to implement Inventory Sync?
A: The cost of implementing Inventory Sync varies depending on several factors, including the size of your business, the complexity of your existing systems, and the specific cloud-based inventory management system you choose. In addition to the monthly or annual subscription costs for your chosen system, you may also incur expenses related to integration development, data migration, and staff training. To get an accurate estimate of the total cost of implementation, consult with your chosen system provider and consider the long-term benefits of Inventory Sync, such as increased efficiency, accuracy, and cost savings.
Conclusion
Implementing Inventory Sync is a crucial step in optimizing your electronics inventory management processes. By connecting your various sales channels and inventory management tools with a cloud-based system, you can improve accuracy, enhance efficiency, gain real-time visibility, and streamline multi-channel management.
To ensure a successful implementation, follow the step-by-step guide outlined in this article, which includes assessing your current system, choosing the right cloud-based solution, integrating your existing tools and channels, configuring your data synchronization settings, and training your staff.
By adopting best practices such as regular system audits, continuous improvement, and ongoing staff training, you can maintain the long-term effectiveness and reliability of your synchronized inventory management system.
Embrace the power of Inventory Sync to take your electronics inventory management to the next level, driving growth, profitability, and customer satisfaction in an increasingly competitive market.
No responses yet