Introduction to Switching Regulator Layout
Switching regulators are an essential component in modern electronic systems, providing efficient power conversion and regulation. The layout of a switching regulator circuit plays a crucial role in its performance, stability, and electromagnetic compatibility (EMC). In this article, we will explore the key considerations and best practices for designing switching regulator layouts on one or two layers.
The Importance of Proper Layout in Switching Regulators
A well-designed layout is critical for achieving optimal performance in switching regulators. Poor layout can lead to various issues, such as:
- Increased electromagnetic interference (EMI)
- Degraded efficiency
- Instability and oscillations
- Excessive noise and ripple
- Thermal management problems
By following best practices and considering the specific requirements of your application, you can minimize these issues and ensure reliable operation of your switching regulator.
Key Components in a Switching Regulator
Before diving into layout considerations, let’s briefly discuss the key components found in a typical switching regulator:
- Power inductor
- Input and output capacitors
- Switching MOSFETs
- Diode (for non-synchronous regulators)
- Control IC
- Feedback network components (resistors, capacitors)
Each of these components plays a specific role in the operation of the switching regulator, and their placement and routing are critical for optimal performance.
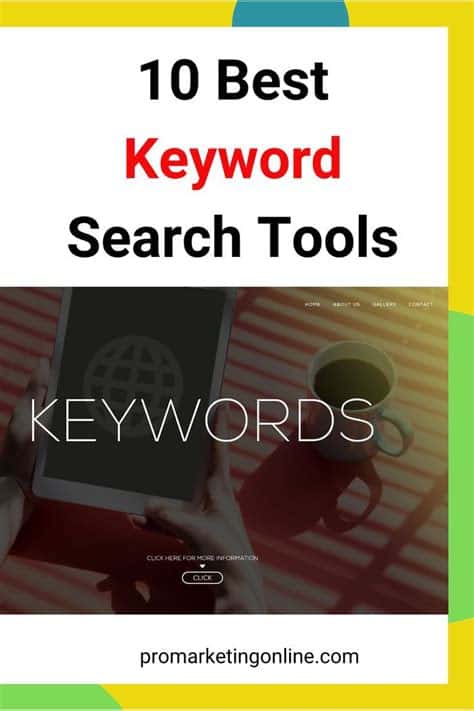
General Layout Guidelines
When designing a switching regulator layout, there are several general guidelines to keep in mind:
- Minimize loop areas: Reduce the area of high-frequency current loops to minimize EMI and improve efficiency.
- Separate noisy and sensitive traces: Keep high-current switching traces away from sensitive analog and control traces to prevent interference.
- Use wide traces for power paths: Ensure that power traces are sufficiently wide to handle the required current and minimize resistive losses.
- Provide adequate grounding: Use a solid ground plane or dedicated ground traces to provide a low-impedance return path for currents.
- Minimize trace lengths: Keep critical traces as short as possible to reduce parasitic inductance and resistance.
- Consider thermal management: Place components in a way that allows for proper heat dissipation and thermal management.
By following these general guidelines, you can create a foundation for a robust and efficient switching regulator layout.
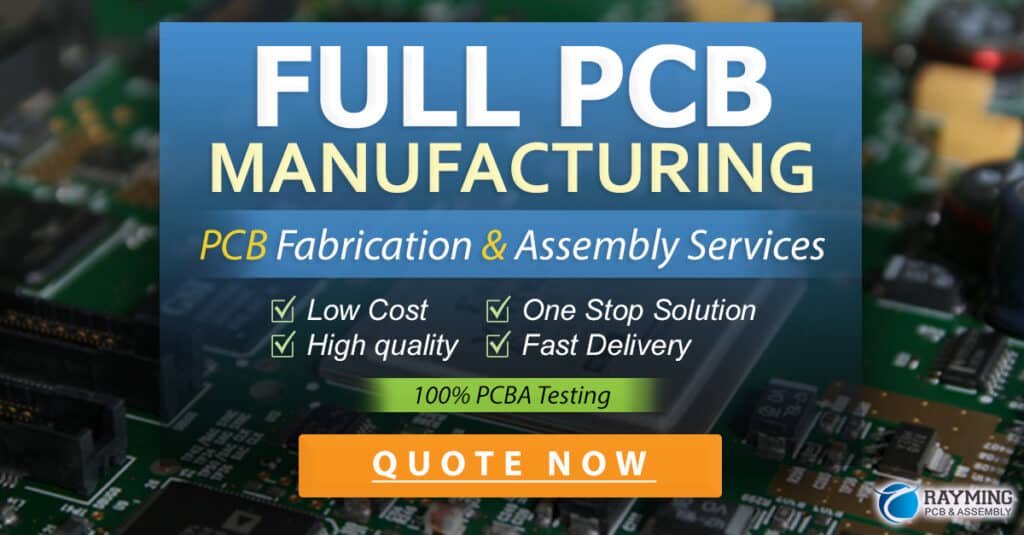
Layout Considerations for One-Layer Designs
Designing a switching regulator on a single layer can be challenging due to limited routing space and increased risk of interference. However, with careful planning and optimization, it is possible to achieve good performance. Here are some specific considerations for one-layer designs:
- Component placement: Arrange components to minimize the distance between the power inductor, input/output capacitors, and switching MOSFETs. This helps reduce loop areas and improve efficiency.
- Trace routing: Route power traces on the top layer, keeping them as short and wide as possible. Use the bottom layer for ground and sensitive traces, if necessary.
- Grounding: Create a dedicated ground plane or use wide ground traces to provide a low-impedance return path. Connect the ground pins of the input and output capacitors directly to the ground plane or traces.
- Feedback network: Place feedback network components close to the control IC to minimize the length of sensitive traces and prevent noise pickup.
- EMI mitigation: Implement EMI mitigation techniques, such as adding snubber circuits or ferrite beads, to reduce high-frequency noise and interference.
Example 1: One-Layer Switching Regulator Layout
Component | Placement | Trace Width |
---|---|---|
Power Inductor | Close to input capacitor and switching MOSFET | 2.5 mm |
Input Capacitor | Close to power inductor and switching MOSFET | 2.0 mm |
Output Capacitor | Close to power inductor and load | 2.0 mm |
Switching MOSFET | Close to power inductor and input capacitor | 2.5 mm |
Control IC | Near feedback network components | 0.5 mm |
In this example, the key components are placed close together to minimize loop areas, and wide traces are used for power paths. The control IC is placed near the feedback network components to ensure short, sensitive traces.
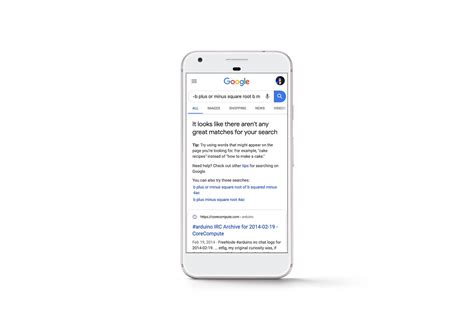
Layout Considerations for Two-Layer Designs
Two-layer designs offer more flexibility and better performance compared to one-layer designs. With an additional layer, you can dedicate one layer for power routing and the other for ground and sensitive traces. Here are some specific considerations for two-layer designs:
- Layer assignment: Assign the top layer for power routing and component placement, and use the bottom layer for ground and sensitive traces.
- Power inductor placement: Place the power inductor on the top layer, close to the input capacitor and switching MOSFET. Minimize the loop area formed by the inductor, capacitor, and MOSFET.
- Ground plane: Create a solid ground plane on the bottom layer to provide a low-impedance return path for currents. Connect the ground pins of the input and output capacitors directly to the ground plane using vias.
- Switching node: Route the switching node (the connection between the inductor, MOSFET, and diode) on the top layer, keeping it as short as possible to minimize parasitic inductance.
- Feedback network: Place feedback network components on the top layer, close to the control IC. Route sensitive traces on the bottom layer, shielded by the ground plane.
Example 2: Two-Layer Switching Regulator Layout
Component | Layer | Placement | Trace Width |
---|---|---|---|
Power Inductor | Top | Close to input capacitor and switching MOSFET | 3.0 mm |
Input Capacitor | Top | Close to power inductor and switching MOSFET | 2.5 mm |
Output Capacitor | Top | Close to power inductor and load | 2.5 mm |
Switching MOSFET | Top | Close to power inductor and input capacitor | 3.0 mm |
Control IC | Top | Near feedback network components | 0.5 mm |
Ground Plane | Bottom | Covers the entire layer | N/A |
Feedback Network | Top/Bottom | Close to control IC, sensitive traces on bottom layer | 0.3 mm |
In this example, the power components are placed on the top layer, with wide traces for power paths. The bottom layer is dedicated to a solid ground plane, providing a low-impedance return path. Feedback network components are placed close to the control IC, with sensitive traces routed on the bottom layer for shielding.
Thermal Management Considerations
Proper thermal management is crucial for the reliable operation and longevity of switching regulators. Poor thermal design can lead to component overheating, reduced efficiency, and even device failure. Here are some thermal management considerations for switching regulator layouts:
- Component selection: Choose components with appropriate power ratings and thermal characteristics for your application. Consider the maximum junction temperature and thermal resistance of the components.
- Copper pours: Use copper pours on the top and bottom layers to improve heat dissipation. These pours act as heat spreaders, distributing heat more evenly across the PCB.
- Thermal vias: Use thermal vias to transfer heat from the top layer to the bottom layer and to the ground plane. Place thermal vias under power components, such as the switching MOSFETs and diode.
- Airflow: Consider the airflow in your enclosure and place components in a way that allows for optimal airflow and heat dissipation. Avoid placing heat-generating components in stagnant air pockets.
- Heatsinks: If necessary, use heatsinks to improve heat dissipation from power components. Select heatsinks with appropriate thermal resistance and size for your application.
By incorporating these thermal management techniques into your switching regulator layout, you can ensure that your design operates within safe temperature limits and maintains reliable performance.
EMI Mitigation Techniques
Electromagnetic interference (EMI) is a common concern in switching regulator designs. The high-frequency switching action of the regulator can generate noise that can interfere with other circuits and cause electromagnetic compatibility (EMC) issues. Here are some EMI mitigation techniques to consider in your switching regulator layout:
- Input and output filtering: Use input and output filters to attenuate high-frequency noise. Place the filters close to the noise source (e.g., the switching MOSFET) to minimize the loop area and improve effectiveness.
- Snubber circuits: Implement snubber circuits, such as RC or RCD snubbers, to dampen voltage and current spikes during switching transitions. Place snubber components close to the switching node.
- Ferrite beads: Use ferrite beads in series with power lines to suppress high-frequency noise. Select ferrite beads with appropriate impedance characteristics for your frequency range of interest.
- Shielding: If necessary, use shielding techniques, such as metal cans or shielding gaskets, to contain EMI and prevent it from radiating to other parts of the system.
- Spread-spectrum technology: Some switching regulator ICs offer spread-spectrum frequency modulation, which helps to reduce the peak EMI amplitude by spreading the energy over a wider frequency range.
By implementing these EMI mitigation techniques in your switching regulator layout, you can reduce the impact of high-frequency noise on your system and improve overall EMC performance.
Testing and Validation
After completing your switching regulator layout, it is essential to thoroughly test and validate the design to ensure that it meets the desired performance and reliability requirements. Here are some key aspects to consider during testing and validation:
- Functional testing: Verify that the switching regulator operates as expected, providing the required output voltage and current under various load conditions. Test the regulator’s response to load transients and input voltage variations.
- Efficiency measurement: Measure the efficiency of the switching regulator across the full load range. Compare the measured efficiency with the expected values based on component specifications and design calculations.
- Thermal testing: Monitor the temperature of critical components, such as the power inductor, switching MOSFETs, and diode, under worst-case operating conditions. Ensure that the temperatures remain within safe limits.
- Ripple and noise measurement: Measure the output voltage ripple and noise using an oscilloscope. Verify that the ripple and noise levels are within acceptable limits for your application.
- EMI testing: Conduct EMI testing to ensure that the switching regulator complies with relevant EMC standards and regulations. Measure conducted and radiated emissions using appropriate test equipment and setups.
- Stress testing: Perform stress tests, such as high-temperature and high-humidity tests, to evaluate the long-term reliability of the switching regulator under extreme conditions.
By conducting thorough testing and validation, you can identify and address any issues early in the development process, ensuring a robust and reliable switching regulator design.
Frequently Asked Questions (FAQ)
-
Q: What is the main difference between one-layer and two-layer switching regulator layouts?
A: The main difference is that a two-layer layout allows for better separation of power and sensitive traces, as well as the use of a dedicated ground plane. This results in improved performance, reduced noise, and better EMI mitigation compared to a one-layer layout. -
Q: How do I choose the right power inductor for my switching regulator?
A: When selecting a power inductor, consider factors such as inductance value, current rating, DC resistance (DCR), and saturation current. The inductance value is determined by the regulator’s switching frequency and desired ripple current. Choose an inductor with a current rating and saturation current higher than the maximum expected load current, and with a low DCR to minimize losses. -
Q: What is the purpose of the input and output capacitors in a switching regulator?
A: The input capacitor helps to reduce voltage ripple and spikes on the input supply, while the output capacitor filters the output voltage ripple and provides local energy storage to improve transient response. The capacitors also help to minimize the loop area and reduce EMI. -
Q: How can I reduce EMI in my switching regulator design?
A: To reduce EMI, you can implement various techniques such as input and output filtering, snubber circuits, ferrite beads, shielding, and spread-spectrum frequency modulation. Proper layout practices, such as minimizing loop areas and separating noisy and sensitive traces, also play a crucial role in EMI mitigation. -
Q: What are some common layout mistakes to avoid in switching regulator designs?
A: Common layout mistakes include poor component placement (leading to large loop areas), insufficient grounding, narrow or long power traces, and improper separation of noisy and sensitive traces. Additionally, neglecting thermal management and EMI mitigation can lead to performance and reliability issues.
Conclusion
Designing a switching regulator layout for one or two layers requires careful consideration of component placement, trace routing, grounding, thermal management, and EMI mitigation. By following best practices and guidelines, such as minimizing loop areas, using wide traces for power paths, and providing adequate grounding, you can achieve optimal performance and reliability in your switching regulator design.
Remember to thoroughly test and validate your design to ensure that it meets the desired specifications and regulatory requirements. By taking a systematic approach to layout design and validation, you can create robust and efficient switching regulators for a wide range of applications.
No responses yet