Introduction to Power Supply Filters
Switching power supplies have become ubiquitous in modern electronic devices due to their high efficiency, compact size, and versatility. However, the switching nature of these power supplies introduces unwanted noise and ripple in the output voltage, which can adversely affect the performance of the connected load. To mitigate these issues, output filters are employed to smooth the voltage and reduce the ripple to acceptable levels.
In this article, we will delve into the design and simulation of output filters for switching power supplies. We will explore the various types of filters, their characteristics, and the key considerations for selecting the appropriate filter for a given application. Additionally, we will discuss the simulation techniques and tools used to analyze and optimize the filter design.
Types of Power Supply Filters
There are several types of filters commonly used in switching power supply output stages. Each type has its own advantages and limitations, and the choice depends on factors such as the required attenuation, cost, size, and complexity. Let’s examine the most common types of power supply filters:
1. LC Filters
LC filters, also known as low-pass filters, consist of an inductor (L) and a capacitor (C) connected in a specific configuration. The inductor acts as a high-impedance element for high-frequency noise, while the capacitor provides a low-impedance path to ground for the same frequencies. The combination of these two components effectively attenuates the high-frequency ripple and noise.
The cutoff frequency (fc) of an LC filter is determined by the values of the inductor and capacitor, as given by the following equation:
fc = 1 / (2π√(LC))
By selecting appropriate values for L and C, the filter can be designed to attenuate frequencies above the desired cutoff frequency while allowing the desired DC voltage to pass through with minimal attenuation.
2. π Filters
π filters, also called pi filters, are an extension of the basic LC filter. They consist of two capacitors and an inductor arranged in a π-shaped configuration. The additional capacitor provides improved high-frequency attenuation compared to a single-stage LC filter.
The cutoff frequency of a π filter is determined by the values of the inductor and the capacitors, as given by the following equation:
fc = 1 / (2π√(LC/2))
π filters offer better noise suppression and ripple reduction compared to LC filters, but at the cost of increased component count and size.
3. Multistage Filters
Multistage filters are formed by cascading multiple LC or π filter stages. Each stage provides additional attenuation, resulting in improved overall filtering performance. The number of stages depends on the required attenuation and the acceptable trade-offs in terms of size, cost, and complexity.
The cutoff frequency of a multistage filter is determined by the values of the inductors and capacitors in each stage. The overall transfer function of the filter is the product of the transfer functions of the individual stages.
Multistage filters offer the highest level of noise and ripple reduction but come with increased component count, size, and cost.
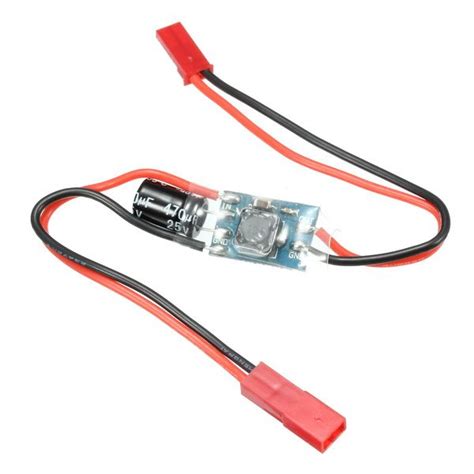
Filter Design Considerations
When designing an output filter for a switching power supply, several key factors need to be considered to ensure optimal performance and reliability. These include:
1. Ripple and Noise Requirements
The first step in filter design is to determine the acceptable level of ripple and noise at the output of the power supply. This is typically specified by the load requirements or the applicable standards. The filter must be designed to attenuate the ripple and noise to levels below the specified limits.
2. Load Characteristics
The load characteristics, such as the maximum current draw, dynamic behavior, and sensitivity to voltage variations, play a crucial role in filter design. The filter must be capable of handling the maximum load current without significant voltage drop or overheating. Additionally, the filter should have minimal impact on the load’s dynamic behavior and provide a stable voltage under varying load conditions.
3. Inductor Selection
The inductor is a critical component in the filter design. It must be selected based on factors such as the required inductance value, current rating, DC resistance (DCR), and saturation current. The inductor should have low DCR to minimize power losses and a high saturation current to prevent core saturation under peak load conditions.
The inductance value is determined by the desired cutoff frequency and the capacitance value. Higher inductance values provide better noise attenuation but also result in larger size and higher cost.
4. Capacitor Selection
The capacitor selection is equally important in filter design. The capacitor must have a low equivalent series resistance (ESR) to minimize power losses and provide effective high-frequency bypassing. The capacitance value is determined by the desired cutoff frequency and the inductance value.
Ceramic capacitors are commonly used in power supply filters due to their low ESR and high ripple current handling capability. However, for high-capacitance values, electrolytic or tantalum capacitors may be used, albeit with higher ESR.
5. PCB Layout Considerations
The PCB layout plays a significant role in the filter’s performance. Proper layout techniques must be employed to minimize parasitic inductance and resistance, which can degrade the filter’s effectiveness. The filter components should be placed close to the power supply output and the load to minimize trace lengths and loop areas.
Ground planes should be used to provide a low-impedance return path for the high-frequency currents. Proper grounding techniques, such as star grounding or split ground planes, should be employed to prevent ground loops and minimize noise coupling.
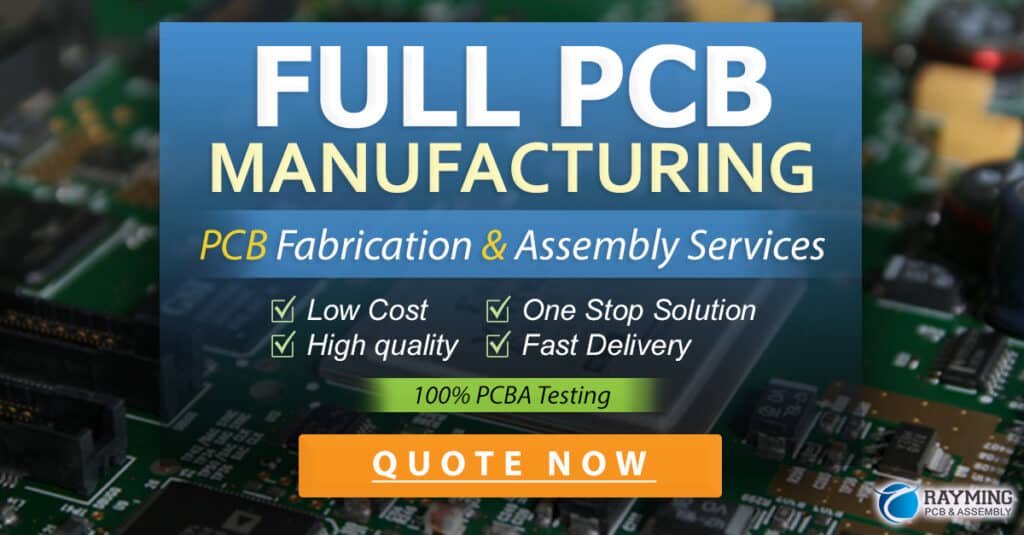
Simulation and Analysis
Simulation is an essential tool in the design and optimization of power supply output filters. It allows designers to evaluate the filter’s performance, identify potential issues, and optimize the component values before physical implementation.
1. Simulation Tools
There are several simulation tools available for power supply filter design, including:
- SPICE (Simulation Program with Integrated Circuit Emphasis)
- LTspice (Linear Technology SPICE)
- PSIM (Power Electronics Simulation)
- MATLAB/Simulink
These tools provide a graphical user interface for schematic capture and simulation setup, as well as extensive libraries of models for passive and active components.
2. Frequency Response Analysis
Frequency response analysis is used to evaluate the filter’s attenuation characteristics over a range of frequencies. The simulation tool sweeps the input frequency and measures the output voltage, allowing the designer to plot the filter’s transfer function.
The frequency response plot provides valuable information about the filter’s cutoff frequency, attenuation slope, and any resonant peaks or valleys. The designer can adjust the component values to achieve the desired frequency response and ensure adequate attenuation of the switching noise and ripple.
3. Time-Domain Analysis
Time-domain analysis is used to evaluate the filter’s performance under transient conditions, such as load step changes or power supply startup. The simulation tool applies a time-varying stimulus to the filter and measures the output voltage and current waveforms.
Time-domain analysis helps identify any voltage overshoots, undershoots, or ringing that may occur during transient events. The designer can optimize the filter components and damping techniques to minimize these effects and ensure stable operation.
4. Monte Carlo Analysis
Monte Carlo analysis is a statistical simulation technique used to evaluate the filter’s performance under component variations. The simulation tool randomly varies the component values within specified tolerance ranges and performs multiple simulation runs.
Monte Carlo analysis helps assess the filter’s robustness and sensitivity to component variations. The designer can identify the critical components that have the most significant impact on the filter’s performance and specify tighter tolerances or use higher-quality components for those critical parts.
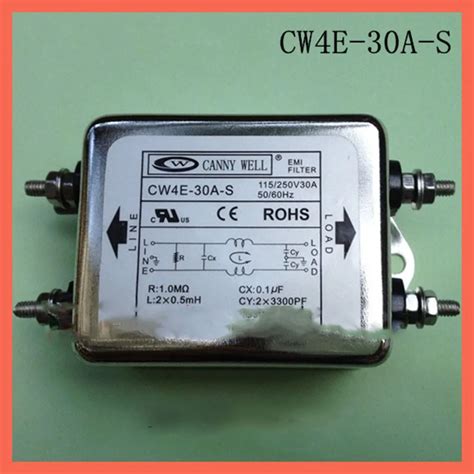
Practical Implementation
Once the filter design has been simulated and optimized, it is time to implement it in hardware. The following considerations should be taken into account during practical implementation:
1. Component Selection
The components used in the filter should be selected based on the simulation results and the specified tolerances. High-quality components with tight tolerances should be used for critical parts, such as the inductor and capacitors, to ensure consistent performance.
The inductor should have a low DCR and high saturation current rating to minimize losses and prevent saturation under peak load conditions. The capacitors should have a low ESR and high ripple current rating to minimize losses and provide effective high-frequency bypassing.
2. PCB Layout
The PCB layout should follow the guidelines discussed earlier to minimize parasitic inductance and resistance. The filter components should be placed close to the power supply output and the load, with short and wide traces to minimize impedance.
Ground planes should be used to provide a low-impedance return path for the high-frequency currents. Proper grounding techniques, such as star grounding or split ground planes, should be employed to prevent ground loops and minimize noise coupling.
3. Testing and Verification
After the filter is assembled, it should be thoroughly tested to verify its performance against the simulation results and the specified requirements. The following tests should be performed:
-
Frequency response measurement: The filter’s frequency response should be measured using a network analyzer or a frequency response analyzer. The measured response should match the simulated response within acceptable tolerances.
-
Ripple and noise measurement: The output voltage ripple and noise should be measured using an oscilloscope or a spectrum analyzer. The measured values should be below the specified limits.
-
Load transient response: The filter’s response to load step changes should be measured using an oscilloscope. The output voltage should remain stable with minimal overshoot or undershoot.
-
Thermal performance: The filter components should be monitored for temperature rise under full load conditions. The temperature should remain within the specified limits to ensure reliable operation and prevent component damage.
Conclusion
Switching power supply output filter design is a critical aspect of ensuring clean and stable power delivery to the load. By understanding the various types of filters, their characteristics, and the key design considerations, engineers can design effective filters that meet the specified requirements.
Simulation and analysis play a vital role in filter design, allowing designers to evaluate and optimize the filter’s performance before physical implementation. Practical implementation requires careful component selection, proper PCB layout, and thorough testing and verification.
By following the guidelines and techniques discussed in this article, engineers can design robust and reliable power supply output filters that provide clean and stable power to the connected load, ensuring optimal system performance and reliability.
Frequently Asked Questions (FAQ)
1. What is the purpose of a power supply output filter?
A power supply output filter is designed to attenuate the high-frequency ripple and noise generated by the switching action of the power supply. It smooths the output voltage and reduces the ripple to acceptable levels, ensuring clean and stable power delivery to the connected load.
2. What are the common types of power supply output filters?
The common types of power supply output filters include:
– LC filters: Consist of an inductor and a capacitor, providing basic low-pass filtering.
– π filters: An extension of the LC filter with an additional capacitor, offering improved high-frequency attenuation.
– Multistage filters: Formed by cascading multiple LC or π filter stages, providing the highest level of noise and ripple reduction.
3. What factors should be considered when selecting components for a power supply output filter?
When selecting components for a power supply output filter, the following factors should be considered:
– Inductor: The inductor should have a low DC resistance (DCR) to minimize power losses and a high saturation current rating to prevent core saturation under peak load conditions.
– Capacitor: The capacitor should have a low equivalent series resistance (ESR) to minimize power losses and provide effective high-frequency bypassing. The capacitance value should be chosen based on the desired cutoff frequency and the inductance value.
4. How does the PCB layout affect the performance of a power supply output filter?
The PCB layout plays a crucial role in the filter’s performance. Proper layout techniques should be employed to minimize parasitic inductance and resistance, which can degrade the filter’s effectiveness. The filter components should be placed close to the power supply output and the load to minimize trace lengths and loop areas. Ground planes should be used to provide a low-impedance return path for the high-frequency currents, and proper grounding techniques should be employed to prevent ground loops and minimize noise coupling.
5. What are the key tests performed to verify the performance of a power supply output filter?
The key tests performed to verify the performance of a power supply output filter include:
– Frequency response measurement: The filter’s frequency response is measured using a network analyzer or a frequency response analyzer to ensure it matches the simulated response within acceptable tolerances.
– Ripple and noise measurement: The output voltage ripple and noise are measured using an oscilloscope or a spectrum analyzer to ensure they are below the specified limits.
– Load transient response: The filter’s response to load step changes is measured using an oscilloscope to ensure the output voltage remains stable with minimal overshoot or undershoot.
– Thermal performance: The filter components are monitored for temperature rise under full load conditions to ensure reliable operation and prevent component damage.
No responses yet