Understanding the PCB Supply Chain
The PCB supply chain consists of all the processes, materials, and partners involved in transforming a design into a finished circuit board. This includes:
- Component sourcing
- PCB fabrication
- Assembly and testing
- Logistics and delivery
Each stage presents its own challenges and opportunities for optimization. As a designer, you have the most influence over component selection, but your choices can impact the entire downstream supply chain.
Importance of Supply Chain Strategy
An effective PCB supply chain strategy offers numerous benefits:
- Ensures availability of components and materials
- Reduces lead times and improves time-to-market
- Lowers costs through volume discounts and operational efficiencies
- Mitigates risks of supply disruptions or quality issues
- Supports scalability as demand grows
Conversely, a poorly designed supply chain can lead to delays, cost overruns, and disappointed customers. By being proactive and strategic, you can avoid these pitfalls.
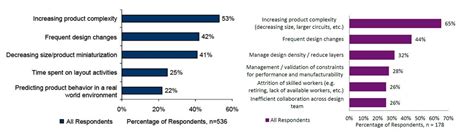
Key Elements of a PCB Supply Chain Strategy
1. Component Selection
Your component choices have far-reaching supply chain implications. Some key considerations include:
-
Availability: Choose components with ample market supply and avoid parts that are nearing end-of-life. Pay attention to product change notices (PCNs) from manufacturers.
-
Multiple Sourcing: Where possible, specify components that are available from multiple manufacturers. This reduces risk of supply disruptions.
-
Standardization: Using common parts across designs provides economies of scale. Create an approved vendor list (AVL) of preferred components.
-
Compliance: Ensure components meet relevant regulatory and environmental standards, such as RoHS.
Component Availability Tiers
Tier | Description | Risk |
---|---|---|
1 | High availability from multiple suppliers | Low |
2 | Medium availability, limited suppliers | Moderate |
3 | Low availability, single source | High |
Aim for Tier 1 components in your AVL to minimize supply risk.
2. Supplier Management
Building strong relationships with key suppliers is essential. Some best practices:
-
Strategic Partnerships: Forge long-term relationships with suppliers who understand your business and can support your growth. Share roadmaps and collaborate on planning.
-
Performance Metrics: Establish clear metrics for quality, delivery, and cost. Regularly review supplier scorecards and work together on continuous improvement.
-
Diversification: Maintain a mix of large and small suppliers for flexibility. Don’t over-rely on a single supplier for critical parts.
-
Communication: Keep lines of communication open. Provide rolling forecasts to help suppliers plan production. Alert them promptly of any design changes.
Example Supplier Scorecard
Metric | Target | Supplier A | Supplier B |
---|---|---|---|
On-Time Delivery | 95% | 98% | 92% |
Quality (Defect Rate) | <1000 PPM | 500 PPM | 1200 PPM |
Cost Reduction | 3% YoY | 4% | 2% |
Regularly review scorecards with suppliers and collaborate on improvements.
3. Risk Management
Supply chains are vulnerable to various risks, from natural disasters to geopolitical events. Robust risk management is critical. Some key tactics:
-
Supply Chain Mapping: Understand your full supply chain, including sub-tier suppliers. Identify potential bottlenecks and single points of failure.
-
Buffer Inventory: Maintain safety stock of critical components to weather short-term disruptions. Use analytics to optimize inventory levels.
-
Contingency Planning: Develop backup plans for key suppliers and logistics routes. Conduct periodic drills to test resilience.
-
Monitoring: Keep tabs on leading risk indicators, from weather patterns to market trends. Use AI and big data for predictive insights.
Risk Management Matrix
Risk | Likelihood | Impact | Mitigation |
---|---|---|---|
Supplier bankruptcy | Low | High | Dual sourcing, financial monitoring |
Natural disaster | Medium | Medium | Geographic diversification, safety stock |
Trade war | High | Medium | Scenario planning, localization |
Regularly review and update your risk management matrix as conditions change.
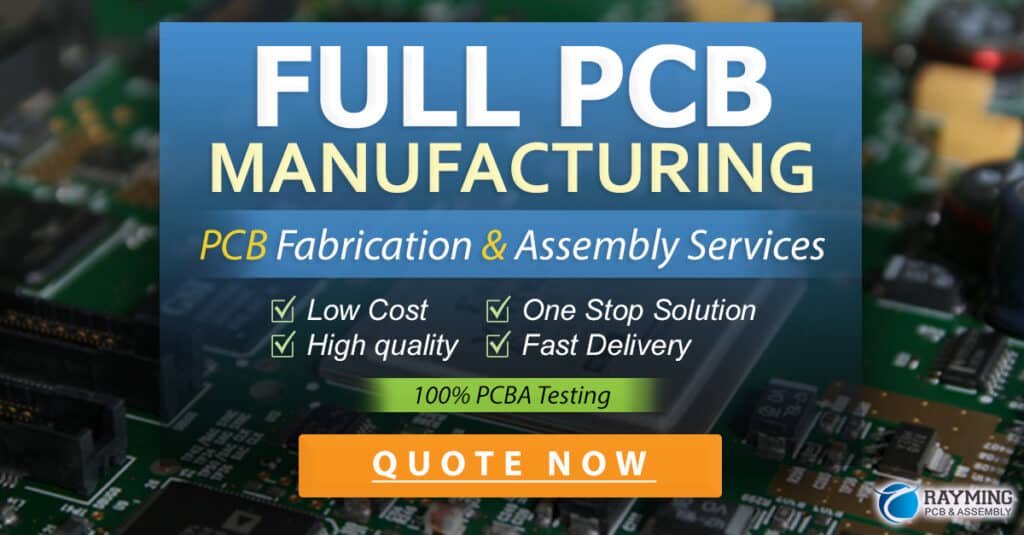
Designing for Supply Chain Efficiency
As a PCB designer, you can make choices that optimize your supply chain:
1. Design for Manufacturability (DFM)
Designing boards that are easy to fabricate and assemble streamlines production and reduces costs. Some DFM best practices:
- Adhere to manufacturer capabilities and guidelines
- Use standard component sizes and pitches
- Provide clear assembly instructions and markup
- Allow ample spacing for pick-and-place machines
2. Design for Testing (DFT)
Boards that are easy to test require less time and specialized equipment, speeding up production. Some DFT tactics:
- Provide test points for key signals
- Use boundary scan for complex digital circuits
- Leverage built-in self-test (BIST) where possible
- Avoid redundant testing of proven sub-circuits
3. Design for Logistics (DFL)
Optimizing your PCBs for packing and shipping can reduce costs and damages. Some DFL considerations:
- Use standard board sizes that fit efficiently in packaging
- Provide clear handling and orientation instructions
- Reinforce high-stress areas to prevent transit damage
- Use moisture barrier bags for sensitive components
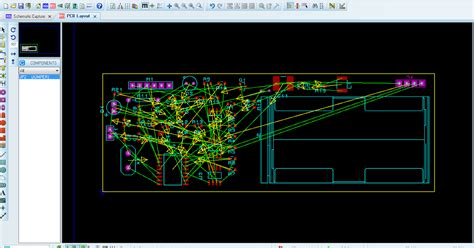
Collaborating Across the Supply Chain
Effective supply chain management requires close collaboration among all stakeholders, including:
- PCB designers
- Component engineers
- Procurement specialists
- Contract manufacturers
- Logistics providers
Some ways to foster collaboration:
-
Co-location: Physically locating cross-functional teams together promotes communication and problem-solving.
-
Data Sharing: Provide supply chain partners with visibility into your design data, forecasts, and inventory levels. Use secure portals and data exchange standards.
-
Joint Planning: Involve key suppliers in your product development and capacity planning processes. Solicit their input on design and manufacturability.
-
Performance Reviews: Regularly review supply chain performance with all stakeholders. Celebrate successes and jointly tackle improvement opportunities.
Leveraging Technology
Various digital tools can help you optimize your PCB supply chain:
-
PLM (Product Lifecycle Management): Manages product data and processes across the lifecycle. Ensures all stakeholders are working with up-to-date information.
-
SCM (Supply Chain Management): Provides visibility and control over supply chain operations, from order management to logistics. Enables data-driven decision making.
-
ERP (Enterprise Resource Planning): Integrates supply chain data with other business functions like finance and HR. Supports holistic optimization.
-
AI and Analytics: Advanced tools can provide predictive insights and recommendations, from forecasting demand to identifying risk.
The key is to choose tools that integrate well and provide a unified view of your supply chain.
Measuring Success
To continually improve your PCB supply chain, it’s important to track key performance indicators (KPIs). Some common ones include:
- On-Time Delivery: Percentage of orders delivered on or before promised date.
- Lead Time: Average time from order placement to delivery.
- Inventory Turns: Number of times inventory is sold and replaced over a period.
- Defect Rate: Percentage of units that fail quality inspection.
- Cost Savings: Reduction in unit costs over time.
Regularly review your KPIs and benchmark against industry peers to identify opportunities for improvement.
Continuous Improvement
Supply chain optimization is an ongoing journey. Some ways to drive continuous improvement:
-
Kaizen Events: Conduct regular workshops to identify and eliminate waste in your supply chain processes.
-
Benchmarking: Compare your performance to industry best practices and adapt accordingly.
-
Training: Invest in your team’s supply chain skills and knowledge. Take advantage of industry certifications and conferences.
-
Innovation: Stay up to date on emerging trends and technologies. Be open to new ideas and approaches.
Remember, small improvements can compound over time to deliver significant results.
Conclusion
Developing an effective PCB supply chain strategy requires careful planning, close collaboration, and continuous improvement. By making smart component choices, partnering with the right suppliers, and leveraging digital tools, you can create a supply chain that is both efficient and resilient. As a PCB designer, you play a critical role in this process by designing for manufacturability, testability, and logistics. By taking a strategic approach to supply chain management, you can deliver better boards faster and at lower cost – delighting your customers and fueling your company’s growth.
Frequently Asked Questions
What is the most important aspect of PCB supply chain strategy?
While many factors are critical, component selection is arguably the most important. Your component choices have cascading effects throughout the supply chain, impacting availability, cost, and lead times. By specifying readily available, multi-sourced components, you can mitigate many downstream risks.
How can I reduce my PCB supply chain costs?
There are several ways to drive cost savings in your PCB supply chain:
– Standardize components to gain volume discounts
– Design for manufacturability to reduce production costs
– Optimize inventory to minimize carrying costs
– Negotiate strategic supplier agreements
– Continuously improve processes to eliminate waste
The key is to take a holistic view of your supply chain and attack costs from multiple angles.
How do I manage supply chain risk as my business grows?
As your volumes increase, your supply chain risk profile changes. Some ways to manage risk at scale:
– Diversify your supplier base to reduce over-reliance on single sources
– Increase buffer inventory to weather larger disruptions
– Invest in more sophisticated risk monitoring and prediction tools
– Develop localized supply chains to serve key markets
– Continuously stress-test your supply chain resilience
The goal is to proactively identify and mitigate risks before they impact your business.
What are some emerging trends in PCB supply chain management?
Some key trends to watch include:
– Digitalization of supply chain processes for greater visibility and agility
– Use of AI and machine learning for predictive insights and automation
– Adoption of additive manufacturing (3D printing) for rapid prototyping and low-volume production
– Increased focus on sustainability and circular economy principles
– Nearshoring of production to reduce geopolitical risk and improve responsiveness
Staying abreast of these trends can help you adapt your strategy to changing market conditions.
How can I ensure my PCB supply chain is ethical and sustainable?
As consumers and regulators place increasing emphasis on corporate social responsibility, ensuring an ethical and sustainable supply chain is critical. Some key steps:
– Develop a supplier code of conduct aligned with your values
– Conduct regular audits to verify compliance
– Trace material sourcing to ensure responsible extraction
– Design products for recyclability and minimal waste
– Collaborate with suppliers on sustainability initiatives
– Report transparently on your supply chain impacts
By embedding ethics and sustainability into your supply chain strategy, you can not only mitigate risk but also create positive social and environmental impact.
[H2-H4 Keywords: PCB design supply chain, supply chain strategy, component selection, supplier management, risk management, design for manufacturability, design for testability, design for logistics, supply chain collaboration, supply chain technology, supply chain KPIs, supply chain continuous improvement, PCB supply chain FAQ]
No responses yet