Introduction to Substrate Integrated Waveguide (SIW) Technology
Substrate Integrated Waveguide (SIW) is an emerging technology that has gained significant attention in the field of high-frequency electronic circuits, particularly for millimeter-wave (mmWave) applications. SIW combines the advantages of traditional waveguides and planar transmission lines, offering a low-loss, high-performance, and cost-effective solution for routing signals on printed circuit boards (PCBs) at mmWave frequencies.
What is Substrate Integrated Waveguide?
SIW is a planar waveguide structure that is fabricated using standard PCB manufacturing techniques. It consists of a dielectric substrate with two parallel rows of metallic vias that act as the sidewalls of the waveguide, and the top and bottom metal layers of the PCB serve as the waveguide’s upper and lower walls. This configuration allows the propagation of electromagnetic waves within the substrate, similar to a conventional rectangular waveguide.
Advantages of SIW Technology
SIW offers several advantages over traditional waveguide and planar transmission line technologies:
-
Low Loss: SIW exhibits lower loss compared to microstrip and coplanar waveguide (CPW) transmission lines, especially at higher frequencies. This is because the electromagnetic energy is confined within the dielectric substrate, minimizing radiation and conductor losses.
-
High Quality Factor: SIW resonators and filters have high-quality factors (Q-factors), which is essential for designing low-loss, narrow-band filters and oscillators at mmWave frequencies.
-
Compact Size: SIW structures can be fabricated on a single layer of the PCB, making them more compact compared to traditional waveguides. This is particularly advantageous for miniaturizing mmWave circuits and systems.
-
Easy Integration: SIW can be easily integrated with other planar transmission lines and active components on the same PCB, simplifying the overall circuit design and manufacturing process.
-
Cost-Effective: SIW circuits can be manufactured using standard PCB fabrication techniques, making them more cost-effective compared to traditional waveguide-based solutions.
Design Considerations for SIW-based mmWave PCBs
When designing SIW-based mmWave PCBs, several key factors need to be considered to ensure optimal performance and manufacturability.
Substrate Material Selection
The choice of substrate material is crucial for SIW-based mmWave PCBs. The substrate should have low dielectric loss, high thermal stability, and good mechanical properties. Some commonly used substrate materials for mmWave applications include:
-
Rogers RO4000 Series: These hydrocarbon ceramic laminates offer excellent high-frequency performance, low loss, and good thermal stability.
-
Taconic RF-35: This low-loss, glass-reinforced PTFE composite is suitable for mmWave applications up to 77 GHz.
-
LTCC (Low Temperature Co-fired Ceramic): LTCC is a multilayer ceramic substrate technology that provides high-density integration and good high-frequency performance.
Via Hole Size and Spacing
The size and spacing of the metallic vias in SIW structures play a critical role in determining the waveguide’s cutoff frequency and loss characteristics. The via diameter (d) and spacing (p) should be carefully chosen to minimize leakage loss and ensure proper waveguide operation. A general rule of thumb is to keep d/p ≤ 0.5 and p/λ ≤ 0.25, where λ is the wavelength at the operating frequency.
Waveguide Width and Height
The width (a) and height (b) of the SIW determine its characteristic impedance and cutoff frequency. The width is typically chosen to be half the guided wavelength (λg) at the center frequency of operation, while the height is determined by the substrate thickness. It is essential to maintain a consistent waveguide cross-section throughout the PCB to avoid impedance mismatches and reflections.
Transition Design
Proper transition design is crucial for efficiently coupling energy between SIW and other planar transmission lines, such as microstrip or CPW. Tapered transitions, where the width of the planar transmission line gradually changes to match the SIW width, are commonly used. The taper length should be optimized to minimize reflection and insertion loss over the desired frequency band.
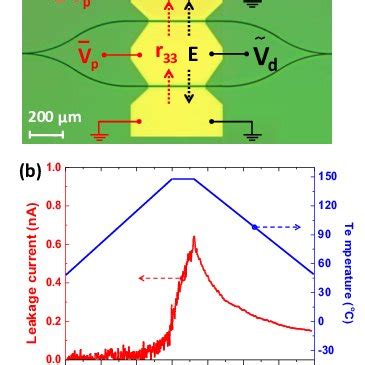
SIW Components and Building Blocks
SIW technology enables the realization of various passive components and building blocks that are essential for mmWave circuit design.
SIW Filters
SIW filters are widely used in mmWave systems for frequency selection and rejection. They offer high Q-factors, low loss, and good selectivity. Some common SIW filter topologies include:
-
Cavity Filters: These filters consist of SIW resonators coupled through irises or apertures. They provide excellent stopband rejection and can be designed for narrow or wide bandwidths.
-
Combline Filters: SIW combline filters are compact and offer good selectivity and stopband performance. They are formed by loading SIW resonators with metallic posts or stubs.
-
Quasi-Elliptic Filters: These filters employ cross-coupling between non-adjacent resonators to create transmission zeros, resulting in sharp roll-off and improved selectivity.
SIW Couplers and Power Dividers
SIW couplers and power dividers are used for power splitting and combining in mmWave circuits. They offer low loss, good isolation, and wide bandwidth. Some common SIW coupler and power divider designs include:
-
Riblet Coupler: This is a compact, high-directivity coupler that consists of two SIW sections connected by a series of coupling slots.
-
Moreno Crossover: The Moreno crossover is a wideband, low-loss power divider that uses a combination of SIW and microstrip sections.
-
Multiway Power Dividers: SIW multiway power dividers, such as the Wilkinson divider, can be designed for equal or unequal power splitting ratios.
SIW Antennas
SIW technology is also used to design high-gain, directive antennas for mmWave applications. SIW antennas offer low loss, good radiation efficiency, and can be easily integrated with other SIW components on the same PCB. Some popular SIW antenna configurations include:
-
SIW Slot Antennas: These antennas consist of radiating slots cut into the top metal layer of the SIW. They can be designed for linear or circular polarization and can be arranged in arrays for higher gain.
-
SIW Horn Antennas: SIW horn antennas are flared sections of the waveguide that provide good directivity and wide bandwidth. They can be integrated with SIW feeding networks for antenna array applications.
-
SIW Patch Antennas: SIW cavity-backed patch antennas offer low profile, good radiation efficiency, and can be designed for dual-band or circular polarization operation.
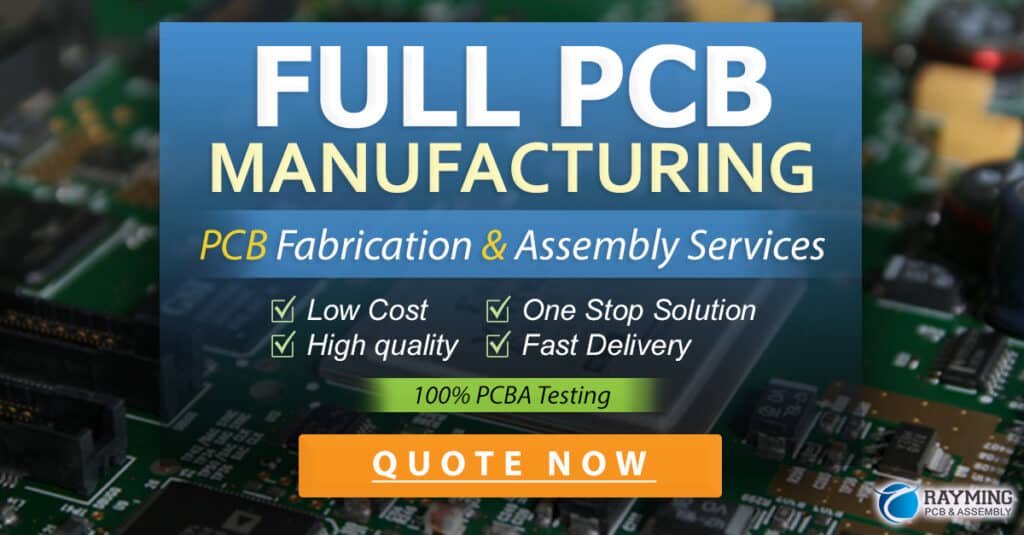
SIW Circuit Integration and Packaging
Integrating SIW components with active devices and packaging mmWave circuits are critical aspects of SIW-based PCB design.
Active Device Integration
Integrating active devices, such as monolithic microwave integrated circuits (MMICs), with SIW circuits requires careful consideration of the transition between the chip and the PCB. Wire bonding and flip-chip bonding are two common techniques used for this purpose. The bond wire or bump inductance should be minimized to reduce parasitic effects and maintain good high-frequency performance.
Packaging Considerations
Packaging mmWave circuits is challenging due to the high frequencies involved and the need for hermetic sealing to protect the components from environmental factors. Some key considerations for packaging SIW-based mmWave PCBs include:
-
Material Selection: The package material should have low dielectric loss, good thermal conductivity, and a coefficient of thermal expansion (CTE) matched to the PCB substrate to minimize stress and warpage.
-
Interconnects: The package interconnects, such as pins or balls, should have low inductance and good high-frequency performance. Coaxial or waveguide-based feed-throughs are often used for mmWave applications.
-
Shielding: Proper shielding is essential to minimize electromagnetic interference (EMI) and crosstalk between different parts of the circuit. Metallic shields or absorbing materials can be used to isolate sensitive components.
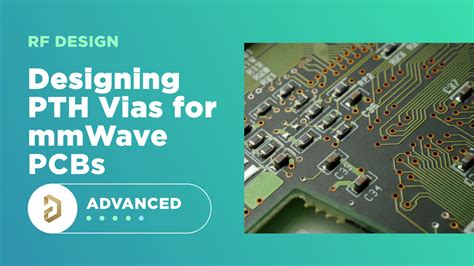
Applications of SIW-based mmWave PCBs
SIW technology has found widespread applications in various mmWave systems, including:
-
5G Wireless Communications: SIW is used in the design of filters, couplers, and antennas for 5G base stations and mobile devices operating in the 28, 39, and 60 GHz bands.
-
Automotive Radar: SIW components are used in automotive radar systems for advanced driver assistance systems (ADAS) and autonomous vehicles, operating at 24 and 77 GHz.
-
Wireless HDMI: SIW is employed in the design of 60 GHz wireless HDMI transmitters and receivers for high-bandwidth video streaming applications.
-
Internet of Things (IoT): SIW-based mmWave circuits are used in IoT devices for short-range, high-data-rate wireless communications.
-
Imaging and Sensing: SIW technology is utilized in the development of mmWave imaging systems for security screening, non-destructive testing, and medical applications.
Frequently Asked Questions (FAQ)
-
Q: What are the main advantages of using SIW for mmWave PCB design?
A: SIW offers low loss, high-quality factors, compact size, easy integration with planar circuits, and cost-effective manufacturing using standard PCB techniques. -
Q: How does the choice of substrate material affect SIW performance?
A: The substrate material should have low dielectric loss, high thermal stability, and good mechanical properties to ensure optimal performance at mmWave frequencies. Materials such as Rogers RO4000 series, Taconic RF-35, and LTCC are commonly used. -
Q: What are the key design parameters for SIW structures?
A: The key design parameters include the via hole size and spacing, waveguide width and height, and transition design. These parameters should be carefully chosen to minimize loss, ensure proper waveguide operation, and maintain consistent impedance throughout the PCB. -
Q: What types of passive components can be realized using SIW technology?
A: SIW technology enables the realization of filters, couplers, power dividers, and antennas with high performance and compact size. -
Q: What are the challenges in packaging SIW-based mmWave circuits?
A: Packaging mmWave circuits requires careful consideration of material selection, interconnects, and shielding to minimize loss, ensure good high-frequency performance, and protect the components from environmental factors.
Conclusion
Substrate Integrated Waveguide (SIW) technology has emerged as a powerful solution for routing mmWave signals on PCBs, offering low loss, high performance, and cost-effective manufacturing. By combining the advantages of traditional waveguides and planar transmission lines, SIW enables the realization of compact, high-quality passive components and antennas for various mmWave applications.
When designing SIW-based mmWave PCBs, careful consideration must be given to substrate material selection, via hole size and spacing, waveguide dimensions, and transition design to ensure optimal performance and manufacturability. Additionally, proper integration of active devices and packaging techniques are crucial for the successful implementation of SIW circuits in practical systems.
As the demand for high-bandwidth, short-range wireless communications continues to grow, SIW technology is poised to play a significant role in the development of next-generation mmWave systems, including 5G networks, automotive radar, wireless HDMI, IoT devices, and imaging applications. With ongoing research and advancements in materials, manufacturing processes, and design tools, SIW-based mmWave PCBs are expected to become increasingly prevalent in the electronics industry.
No responses yet