Introduction to Averatek ASAP
Averatek ASAP (Advanced Semiadditive Process) is a groundbreaking technology that enables the fabrication of sub 25 micron traces on printed circuit boards (PCBs). This innovative process allows for the creation of high-density interconnects, which are essential for the development of advanced electronic devices in various industries, such as telecommunications, aerospace, and medical equipment.
Benefits of Averatek ASAP Technology
- Finer trace widths: Averatek ASAP enables the creation of traces as small as 15 microns, which is significantly smaller than the traditional PCB manufacturing processes.
- Improved signal integrity: The reduced trace widths and spacing minimize crosstalk and signal loss, resulting in improved signal integrity and overall performance of the electronic device.
- Increased design flexibility: With the ability to create finer traces, designers have more freedom to create complex and compact PCB layouts, enabling the development of smaller and more advanced electronic devices.
- Cost-effective: Averatek ASAP is a cost-effective solution for high-density PCB fabrication compared to other advanced manufacturing techniques, such as modified semi-additive process (mSAP) or subtractive etching.
How Averatek ASAP Works
The Semiadditive Process
Averatek ASAP is based on the semiadditive process, which involves the following steps:
- Substrate preparation
- Seed layer deposition
- Photoresist application and patterning
- Electroplating
- Photoresist removal
- Seed layer etching
Substrate Preparation
The process begins with the preparation of the substrate, which is typically a dielectric material such as FR-4, polyimide, or liquid crystal polymer (LCP). The substrate is cleaned and treated to ensure proper adhesion of the subsequent layers.
Seed Layer Deposition
A thin conductive seed layer, usually copper, is deposited onto the substrate using physical vapor deposition (PVD) techniques such as sputtering or evaporation. This seed layer serves as a conductive base for the subsequent electroplating process.
Photoresist Application and Patterning
A photoresist layer is applied onto the seed layer and patterned using photolithography. The photoresist is exposed to light through a photomask, which contains the desired trace pattern. The exposed areas of the photoresist are then developed and removed, leaving behind a negative image of the trace pattern.
Electroplating
The exposed seed layer is electroplated with copper, which grows within the openings of the photoresist pattern. The electroplating process is carefully controlled to achieve the desired trace thickness and uniformity.
Photoresist Removal
After electroplating, the remaining photoresist is stripped away, revealing the plated copper traces on the seed layer.
Seed Layer Etching
Finally, the exposed seed layer is etched away using a selective etchant, leaving behind the final sub 25 micron copper traces on the substrate.
Advantages of Averatek ASAP over Traditional PCB Manufacturing
Feature | Averatek ASAP | Traditional PCB Manufacturing |
---|---|---|
Minimum Trace Width | 15 microns | 75 microns |
Minimum Spacing | 15 microns | 75 microns |
Aspect Ratio (Depth/Width) | 1:1 | 1:3 |
Signal Integrity | High | Moderate |
Design Flexibility | High | Moderate |
Cost | Moderate | Low |
Averatek ASAP offers several advantages over traditional PCB manufacturing processes, as shown in the table above. The ability to create finer traces and spacing, higher aspect ratios, and improved signal integrity makes Averatek ASAP a superior choice for high-density PCB fabrication.
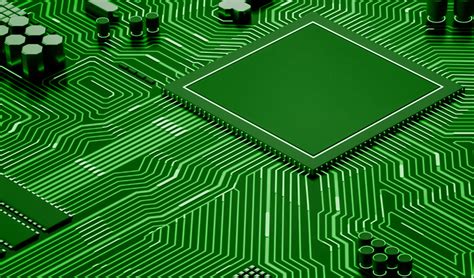
Applications of Averatek ASAP
The sub 25 micron trace capability of Averatek ASAP technology enables the development of advanced electronic devices in various industries, including:
- Telecommunications
- 5G devices
- High-speed networking equipment
-
Satellite communication systems
-
Aerospace and Defense
- Avionics systems
- Radar and guidance systems
-
Unmanned aerial vehicles (UAVs)
-
Medical Devices
- Implantable devices
- Wearable health monitors
-
Diagnostic equipment
-
Consumer Electronics
- Smartphones and tablets
- Wearable devices
-
Internet of Things (IoT) devices
-
Automotive Electronics
- Advanced driver assistance systems (ADAS)
- In-vehicle infotainment systems
- Electric vehicle power electronics
Case Study: Averatek ASAP in 5G Devices
The deployment of 5G networks requires the development of high-performance electronic devices capable of handling the increased data rates and reduced latency. Averatek ASAP technology plays a crucial role in enabling the fabrication of compact, high-density PCBs for 5G devices.
By utilizing Averatek ASAP, 5G device manufacturers can:
- Miniaturize device footprints
- Improve signal integrity and reduce signal loss
- Integrate more functionality into a single device
- Reduce power consumption and improve battery life
The sub 25 micron traces made possible by Averatek ASAP allow for the design of complex antenna arrays, high-frequency filters, and advanced RF front-end modules, which are essential components in 5G devices.
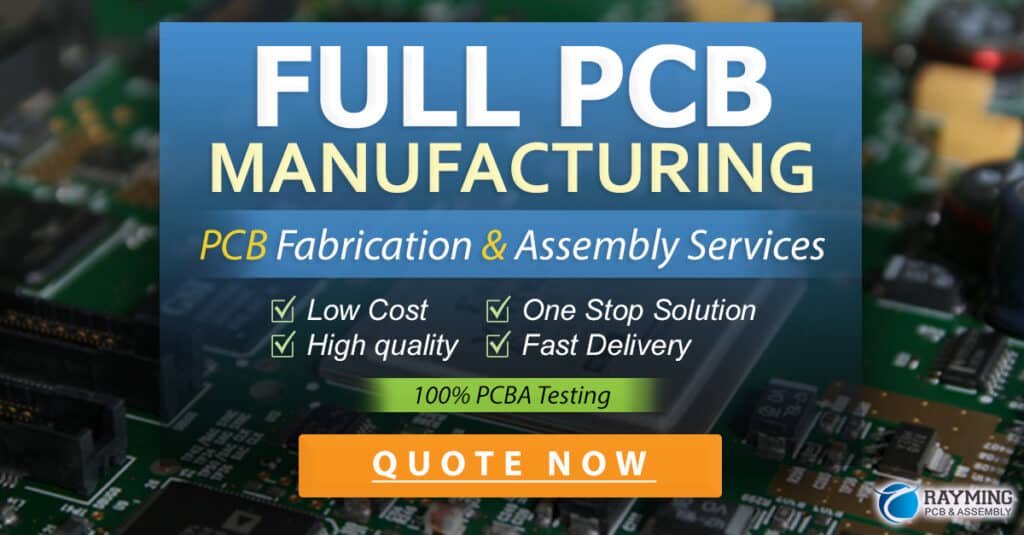
Challenges and Future Developments
Despite the numerous benefits of Averatek ASAP technology, there are still some challenges that need to be addressed:
-
Substrate compatibility: Not all substrate materials are suitable for the semiadditive process used in Averatek ASAP. Further research is needed to expand the range of compatible substrates.
-
Scalability: While Averatek ASAP is a cost-effective solution for high-density PCB fabrication, the process needs to be further optimized for large-scale production to meet the growing demand for advanced electronic devices.
-
Design tools and guidelines: The adoption of Averatek ASAP technology requires the development of new design tools and guidelines to help engineers and designers take full advantage of the sub 25 micron trace capability.
As the demand for high-density PCBs continues to grow, Averatek ASAP technology is expected to evolve and improve. Future developments may include:
- Further reduction in trace widths and spacing
- Improved substrate compatibility
- Faster and more efficient fabrication processes
- Integration with other advanced manufacturing techniques, such as 3D printing or embedded components
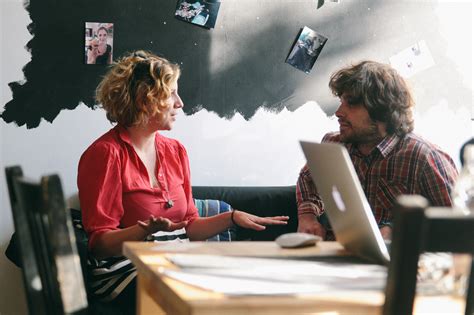
Frequently Asked Questions (FAQ)
- What is the minimum trace width achievable with Averatek ASAP technology?
-
Averatek ASAP technology can achieve trace widths as small as 15 microns.
-
How does Averatek ASAP differ from traditional PCB manufacturing processes?
-
Averatek ASAP uses a semiadditive process that allows for the creation of finer traces and spacing, higher aspect ratios, and improved signal integrity compared to traditional subtractive etching processes.
-
What industries can benefit from Averatek ASAP technology?
-
Averatek ASAP technology can benefit various industries, including telecommunications, aerospace, medical devices, consumer electronics, and automotive electronics.
-
Are there any limitations to Averatek ASAP technology?
-
Averatek ASAP technology may have limitations in terms of substrate compatibility and scalability for large-scale production. However, ongoing research and development efforts aim to address these challenges.
-
How can designers and engineers take advantage of Averatek ASAP technology?
- Designers and engineers can take advantage of Averatek ASAP technology by utilizing new design tools and guidelines specifically developed for sub 25 micron trace PCB fabrication, enabling them to create more compact and advanced electronic devices.
Conclusion
Averatek ASAP technology represents a significant advancement in PCB manufacturing, enabling the fabrication of sub 25 micron traces. This innovative process offers numerous benefits, including finer trace widths, improved signal integrity, increased design flexibility, and cost-effectiveness compared to other advanced manufacturing techniques.
As the demand for high-performance electronic devices continues to grow across various industries, Averatek ASAP technology will play a crucial role in enabling the development of compact, high-density PCBs. While there are still some challenges to be addressed, ongoing research and development efforts aim to further improve and expand the capabilities of this groundbreaking technology.
By embracing Averatek ASAP technology, designers and engineers can push the boundaries of electronic device design, creating smaller, faster, and more advanced products that meet the ever-increasing demands of today’s technology-driven world.
No responses yet