Understanding the Basics of PCB Layout Design
Before diving into specific strategies, it’s crucial to grasp the fundamentals of PCB layout design. A PCB, or printed circuit board, is a platform that mechanically supports and electrically connects electronic components using conductive tracks, pads, and other features etched from copper sheets laminated onto a non-conductive substrate.
Key Elements of a PCB Layout
Element | Description |
---|---|
Component placement | Arranging components on the board for optimal performance and manufacturability |
Routing | Creating conductive paths to connect components electrically |
Layers | Utilizing multiple layers to accommodate complex designs and minimize interference |
Vias | Connecting different layers through plated holes |
Copper pour | Adding large areas of copper to improve EMI shielding and power distribution |
Design Considerations
When designing a PCB layout, consider the following factors:
- Signal integrity
- Power integrity
- Electromagnetic compatibility (EMC)
- Thermal management
- Manufacturing constraints
By addressing these considerations early in the design process, you can avoid costly revisions and ensure a successful end product.
Planning Your PCB Layout
Proper planning is essential for creating an efficient and effective PCB layout. Follow these steps to streamline your design process:
Create a Block Diagram
Start by creating a high-level block diagram of your system, identifying the major functional blocks and their interconnections. This helps you visualize the overall structure and identify critical signal paths.
Develop a Schematic
Translate your block diagram into a detailed schematic, specifying components, their values, and connections. Use a schematic capture tool to ensure accuracy and consistency.
Define Design Constraints
Establish design constraints based on your project’s requirements, such as:
- Board size and shape
- Layer stack-up
- Manufacturing capabilities
- Component availability
- Cost targets
Documenting these constraints early on helps guide your design decisions and prevents scope creep.
Component Placement Strategies
Optimal component placement is crucial for achieving a high-performance PCB layout. Consider these strategies:
Functional Grouping
Arrange components based on their functional relationships, keeping related components close together to minimize signal path lengths and improve signal integrity.
Signal Flow
Place components in a logical sequence following the signal flow, from inputs to outputs. This helps minimize crossovers and simplifies routing.
Thermal Considerations
Position heat-generating components, such as power regulators and high-speed processors, away from temperature-sensitive components and provide adequate thermal relief.
Mechanical Constraints
Account for mechanical constraints, such as connector locations, mounting holes, and component heights, to ensure proper fit and assembly.
Placement Example
Here’s an example of a good component placement strategy:
Component Group | Placement Strategy |
---|---|
Power supply | Near the power input connector, away from sensitive analog circuits |
High-speed digital | Grouped together, away from analog and power components |
Analog | Separated from digital components, with sensitive circuits shielded |
Connectors | Along board edges for easy access and cable management |
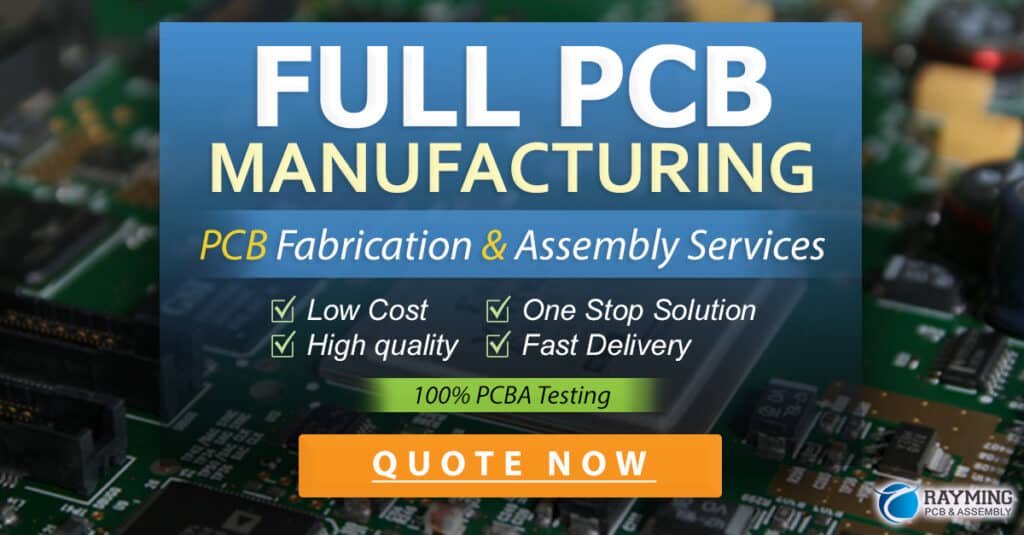
Routing Strategies
Efficient routing is essential for maintaining signal integrity, minimizing crosstalk, and ensuring manufacturability. Follow these guidelines:
Signal Integrity
- Route critical signals first, using the shortest possible path
- Avoid sharp corners and maintain consistent trace widths
- Use appropriate spacing between traces to minimize crosstalk
- Employ differential pair routing for high-speed signals
Power Integrity
- Use wide traces or copper pours for power distribution
- Decouple power supplies with appropriate capacitors near power pins
- Utilize separate power planes for analog and digital circuits
Electromagnetic Compatibility (EMC)
- Separate high-speed digital traces from sensitive analog traces
- Employ ground planes to provide shielding and reduce EMI
- Use stitching vias to connect ground planes on different layers
Manufacturing Considerations
- Adhere to your manufacturer’s design rules for trace widths, spacings, and via sizes
- Provide adequate clearances for component pads and vias
- Use teardrops to reinforce trace-to-pad connections
Layer Stack-up Strategies
An optimized layer stack-up is crucial for maintaining signal integrity and minimizing EMI. Consider these recommendations:
Signal Layers
- Route high-speed signals on inner layers, sandwiched between ground planes
- Use symmetrical stack-ups to minimize warpage and improve manufacturability
- Alternate signal layers with ground planes to provide shielding
Power Planes
- Dedicate layers for power distribution, using separate planes for different voltages
- Place power planes close to the components they serve to minimize inductance
- Use split planes for analog and digital power supplies
Example Layer Stack-up
Here’s an example of a well-designed 6-layer PCB stack-up:
Layer | Purpose |
---|---|
Top | Signal, component placement |
Ground | Shielding, signal return path |
Signal 1 | High-speed signals |
Power | Power distribution |
Signal 2 | High-speed signals |
Bottom | Signal, component placement |
Testing and Verification
To ensure your PCB layout meets performance and reliability requirements, conduct thorough testing and verification:
Design Rule Checking (DRC)
Use DRC tools to verify that your layout adheres to manufacturing constraints and design rules, such as minimum trace widths and clearances.
Signal Integrity Simulation
Perform pre-layout and post-layout signal integrity simulations to identify potential issues, such as reflections, crosstalk, and EMI.
Prototype Assembly and Testing
Assemble prototypes and conduct functional, thermal, and EMC testing to validate your design’s performance in real-world conditions.
Frequently Asked Questions (FAQ)
-
What is the importance of a ground plane in a PCB layout?
A ground plane serves as a low-impedance return path for signals, provides shielding against EMI, and helps maintain signal integrity. It also reduces ground bounce and minimizes voltage differences across the board. -
How do I choose the appropriate trace width for my PCB layout?
Trace width depends on several factors, including the current carrying requirements, the desired impedance, and the manufacturing capabilities. Use online calculators or consult your manufacturer’s design guidelines to determine the appropriate trace width for your application. -
What is the difference between through-hole and surface-mount components?
Through-hole components have leads that are inserted into holes drilled in the PCB and soldered on the opposite side. Surface-mount components are placed directly on the PCB surface and soldered to pads. Surface-mount components are generally smaller and better suited for high-density designs. -
How can I minimize crosstalk between adjacent traces?
To minimize crosstalk, increase the spacing between adjacent traces, route them on different layers, or place a ground trace between them. You can also use differential pair routing for high-speed signals to reduce crosstalk. -
What is the purpose of a via in a PCB layout?
A via is a plated hole that connects traces on different layers of a PCB. Vias are used to route signals between layers, create connections to ground or power planes, and provide thermal relief for heat-generating components.
By following these strategies and best practices, you can create high-quality PCB layouts that meet your project’s performance, reliability, and manufacturability requirements. Remember to plan carefully, consider signal and power integrity, and test thoroughly to ensure a successful end product.
No responses yet