Introduction to Strain Gauge Load Cells
A strain gauge load cell is a highly accurate and versatile force measurement device widely used in various industries, such as automotive, aerospace, manufacturing, and medical fields. It is designed to convert an applied force into an electrical signal, which can be easily measured and processed by a data acquisition system or a controller. Strain gauge load cells have become an essential tool for precise force measurement, weight measurement, and process control applications.
How Does a Strain Gauge Load Cell Work?
The Strain Gauge Principle
The working principle of a strain gauge load cell is based on the concept of strain, which is the deformation of a material when subjected to an external force. A strain gauge is a thin, flexible resistive element that is bonded to the surface of the load cell’s deformable body, typically made of metal. As the load cell is subjected to a force, the body deforms, causing the strain gauge to stretch or compress along with it. This change in the strain gauge’s geometry results in a change in its electrical resistance.
Wheatstone Bridge Configuration
To accurately measure the change in resistance, strain gauge load cells employ a Wheatstone bridge configuration. A Wheatstone bridge is an electrical circuit consisting of four resistive elements, one of which is the strain gauge, connected in a diamond-shaped arrangement. When a force is applied to the load cell, the resistance of the strain gauge changes, causing an imbalance in the bridge circuit. This imbalance results in a voltage output that is proportional to the applied force.
The Wheatstone bridge configuration offers several advantages, including:
- High sensitivity: The bridge circuit amplifies the small changes in resistance, making it possible to detect even the slightest forces.
- Temperature compensation: By using multiple strain gauges in the bridge circuit, the effects of temperature variations can be minimized, ensuring accurate measurements over a wide temperature range.
- Linearity: The voltage output of the Wheatstone bridge is linearly proportional to the applied force, simplifying the calibration and data interpretation process.
Construction of Strain Gauge Load Cells
Load Cell Body
The load cell body is the main structural component of a strain gauge load cell. It is designed to deform elastically when subjected to the applied force. The body is typically made of high-strength, corrosion-resistant materials, such as stainless steel or aluminum alloys, to ensure long-term stability and reliability.
The shape and dimensions of the load cell body depend on the specific application and the range of forces to be measured. Some common load cell body designs include:
-
Beam load cells: These load cells have a simple, beam-like structure with strain gauges bonded to the top and bottom surfaces. They are suitable for low to medium force ranges and are commonly used in weighing scales and material testing machines.
-
Shear beam load cells: In this design, the strain gauges are bonded to a shear-sensitive section of the load cell body, which is subjected to shear stress when a force is applied. Shear beam load cells are known for their high accuracy and resistance to off-center loading.
-
S-type load cells: These load cells have an S-shaped body with strain gauges bonded to the curved sections. They are designed to measure both tension and compression forces and are often used in hanging scale applications.
-
Pancake load cells: With a flat, disc-shaped body, pancake load cells are compact and suitable for applications with limited space. They are commonly used in industrial weighing systems and process control equipment.
Strain Gauge Bonding
The accuracy and long-term stability of a strain gauge load cell largely depend on the proper bonding of the strain gauges to the load cell body. The bonding process involves carefully cleaning the surface of the load cell body, applying a thin layer of adhesive, and positioning the strain gauges at specific locations and orientations.
The choice of adhesive is critical, as it must provide a strong, stable bond between the strain gauge and the load cell body while allowing the strain gauge to deform along with the body. Some commonly used adhesives include epoxy resins, cyanoacrylates, and polyimides.
After bonding, the strain gauges are typically protected by a coating or encapsulation to prevent damage from environmental factors such as moisture, dust, and mechanical impact.
Electrical Connections and Wiring
To interface the strain gauge load cell with a data acquisition system or controller, electrical connections must be made to the Wheatstone bridge circuit. The load cell typically has four or six wires, depending on the specific wiring configuration used.
The most common wiring configurations are:
-
Four-wire configuration: This configuration uses two wires for the excitation voltage and two wires for the output signal. It is simple and cost-effective but may be affected by lead wire resistance.
-
Six-wire configuration: In this configuration, two additional wires are used for sensing the excitation voltage directly at the load cell. This compensates for any voltage drop in the lead wires, improving the accuracy of the measurement.
The wires are usually color-coded to facilitate proper connections and are protected by a flexible cable or a conduit to prevent damage.
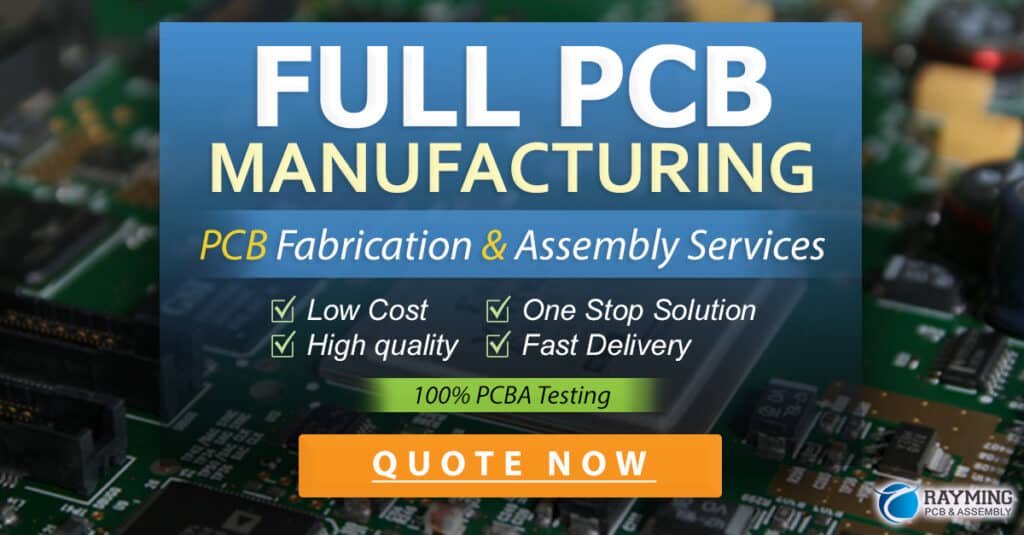
Types of Strain Gauge Load Cells
Strain gauge load cells are available in various types, each designed for specific applications and force ranges. Some common types include:
-
Compression load cells: These load cells are designed to measure compressive forces and are commonly used in weighing systems, material testing machines, and process control equipment.
-
Tension load cells: Designed to measure tensile forces, tension load cells are used in applications such as cable tension monitoring, overload protection, and hanging scale systems.
-
Universal load cells: Also known as tension-compression load cells, these versatile devices can measure both tensile and compressive forces. They are often used in material testing, aerospace, and automotive applications.
-
Miniature load cells: With their compact size and high sensitivity, miniature load cells are suitable for applications with limited space or low force ranges, such as medical devices, robotics, and precision instruments.
-
Submersible load cells: Designed for use in harsh environments, submersible load cells are hermetically sealed and can operate underwater or in other corrosive fluids. They are commonly used in offshore weighing systems and marine applications.
Calibration and Accuracy
To ensure accurate force measurements, strain gauge load cells must be properly calibrated. Calibration involves applying known forces to the load cell and adjusting the output signal to match the corresponding force values. This process establishes a linear relationship between the applied force and the output voltage, which can be used to interpret the measured data.
Calibration is typically performed using a reference load cell or a dead-weight tester. The calibration procedure should cover the full range of forces expected in the application and should be repeated periodically to account for any drift or changes in the load cell’s performance over time.
The accuracy of a strain gauge load cell depends on several factors, including:
- Linearity: The degree to which the output signal is proportional to the applied force.
- Hysteresis: The difference in the output signal between loading and unloading cycles.
- Repeatability: The ability of the load cell to produce consistent results under the same loading conditions.
- Creep: The change in the output signal over time when a constant force is applied.
- Temperature effects: The influence of temperature variations on the load cell’s performance.
High-quality strain gauge load cells can achieve accuracies of 0.1% to 0.25% of the full-scale output, making them suitable for a wide range of precision force measurement applications.
Applications of Strain Gauge Load Cells
Strain gauge load cells find applications in numerous industries and fields, including:
-
Industrial weighing systems: Load cells are used in platform scales, tank weighing systems, and belt weighers for monitoring and controlling production processes.
-
Automotive and aerospace testing: Load cells are employed in crash testing, fatigue testing, and wind tunnel testing to measure forces acting on vehicles and aircraft components.
-
Medical devices: Miniature load cells are used in medical equipment such as infusion pumps, prosthetics, and rehabilitation devices to monitor and control forces.
-
Material testing: Universal testing machines and other material testing equipment rely on load cells to measure the mechanical properties of materials, such as strength, elasticity, and fracture toughness.
-
Structural monitoring: Load cells are used to monitor the loads and stresses acting on bridges, buildings, and other structures to ensure their safety and integrity.
-
Robotics and automation: Load cells are integrated into robotic grippers, force-feedback systems, and assembly lines to control and optimize processes.
Advantages of Strain Gauge Load Cells
Strain gauge load cells offer several advantages over other force measurement technologies:
-
High accuracy and repeatability: With proper calibration, strain gauge load cells can provide highly accurate and consistent force measurements.
-
Wide force range: Strain gauge load cells are available in a wide range of capacities, from a few grams to several thousand tons, making them suitable for diverse applications.
-
Excellent linearity: The output signal of a strain gauge load cell is linearly proportional to the applied force, simplifying data interpretation and control.
-
Versatility: Strain gauge load cells can be designed to measure various types of forces, including compression, tension, and shear, and can be adapted to different environmental conditions.
-
Durability: With proper protection and maintenance, strain gauge load cells can provide reliable performance over an extended period, even in harsh industrial environments.
Limitations and Challenges
Despite their numerous advantages, strain gauge load cells also have some limitations and challenges:
-
Sensitivity to temperature: Changes in temperature can affect the resistance of the strain gauges and the properties of the load cell body, leading to measurement errors. Temperature compensation techniques, such as using multiple strain gauges and specialized alloys, can help mitigate these effects.
-
Creep and hysteresis: Under constant loading, the output signal of a strain gauge load cell may drift over time (creep) or exhibit different values during loading and unloading cycles (hysteresis). These effects can be minimized by using high-quality materials and proper load cell design.
-
Overloading and damage: Excessive forces beyond the load cell’s rated capacity can cause permanent deformation or damage to the strain gauges and the load cell body. Proper selection of the load cell capacity and the use of overload protection devices can help prevent such damage.
-
Electrical noise and interference: The low-level output signals from strain gauge load cells can be affected by electrical noise and interference from nearby equipment. Proper shielding, grounding, and signal conditioning techniques are essential to ensure accurate and stable measurements.
Future Developments and Trends
As technology advances, strain gauge load cells continue to evolve and improve. Some recent developments and trends include:
-
Wireless load cells: The integration of wireless communication technology allows load cells to transmit data without the need for physical connections, simplifying installation and maintenance.
-
Smart load cells: Equipped with built-in signal conditioning, data processing, and communication capabilities, smart load cells can provide direct digital output and enable remote monitoring and control.
-
Miniaturization: Advances in manufacturing techniques and materials enable the development of smaller and more compact load cells, expanding their applications in fields such as robotics, medical devices, and wearable technology.
-
Integration with IoT and Industry 4.0: As the Internet of Things (IoT) and Industry 4.0 gain traction, strain gauge load cells are becoming increasingly connected and integrated into larger systems for real-time monitoring, predictive maintenance, and process optimization.
FAQ
-
What is the difference between a strain gauge load cell and a hydraulic load cell?
A strain gauge load cell uses a resistive element (strain gauge) to convert the applied force into an electrical signal, while a hydraulic load cell uses a fluid-filled chamber and a pressure sensor to measure the force. Strain gauge load cells are more common, offer better accuracy and linearity, and are suitable for a wider range of applications. -
Can a strain gauge load cell measure both tension and compression forces?
Yes, certain types of strain gauge load cells, such as universal or tension-compression load cells, are designed to measure both tensile and compressive forces. However, some load cells are specifically designed for either compression or tension measurements only. -
How often should a strain gauge load cell be calibrated?
The calibration frequency depends on factors such as the application, the operating conditions, and the required accuracy. In general, load cells should be calibrated at least once a year or more frequently if they are subjected to harsh environments or critical applications. It is also recommended to recalibrate the load cell after any overloading or mechanical damage. -
Can a strain gauge load cell be used in underwater applications?
Yes, specially designed submersible load cells are available for underwater applications. These load cells are hermetically sealed and constructed using corrosion-resistant materials to withstand the harsh underwater environment. They are commonly used in offshore weighing systems, marine research, and subsea monitoring applications. -
What is the purpose of the Wheatstone bridge configuration in a strain gauge load cell?
The Wheatstone bridge configuration is used to accurately measure the small changes in resistance of the strain gauge when a force is applied. It consists of four resistive elements, including the strain gauge, connected in a diamond-shaped arrangement. This configuration amplifies the small resistance changes, provides temperature compensation, and ensures a linear relationship between the applied force and the output voltage.
Conclusion
Strain gauge load cells are essential force measurement devices used in a wide range of industries and applications. By converting applied forces into electrical signals, they enable precise monitoring, control, and analysis of mechanical systems. The working principle of strain gauge load cells is based on the deformation of a resistive element (strain gauge) bonded to a load cell body, which is typically arranged in a Wheatstone bridge configuration for accurate and linear force measurement.
The construction of strain gauge load cells involves the proper design of the load cell body, the bonding of strain gauges, and the establishment of electrical connections. Various types of strain gauge load cells, such as compression, tension, universal, miniature, and submersible load cells, are available to cater to different application requirements and environmental conditions.
Proper calibration and consideration of factors affecting accuracy, such as linearity, hysteresis, repeatability, creep, and temperature effects, are crucial for ensuring reliable force measurements. While strain gauge load cells offer numerous advantages, including high accuracy, wide force range, and versatility, they also face challenges related to temperature sensitivity, creep, hysteresis, and electrical interference.
As technology progresses, strain gauge load cells continue to evolve, with developments in wireless communication, smart sensors, miniaturization, and integration with IoT and Industry 4.0. These advancements further expand the potential applications and benefits of strain gauge load cells in various fields, from industrial weighing systems and automotive testing to medical devices and structural monitoring.
By understanding the working principles, construction, types, and applications of strain gauge load cells, engineers and researchers can effectively utilize these powerful force measurement tools to optimize processes, ensure safety, and drive innovation across diverse industries.
No responses yet