What is a Stepper Motor?
A stepper motor is a brushless DC motor that divides a full rotation into a number of equal steps. It moves in precise increments or steps when electrical pulses are applied to it in the proper sequence. The motor’s position can be commanded to move and hold at one of these steps without any feedback sensor (an open-loop controller), as long as the motor is carefully sized to the application in respect to torque and speed.
Key Characteristics of Stepper Motors
- Precise positioning and repeatability
- High torque at low speeds
- Low speed stability
- Open-loop control (no feedback required)
- Holds position when not energized
What is a DC Motor?
A DC motor is an electric motor that runs on direct current (DC) electricity. It converts electrical energy into mechanical energy through the interaction between the motor’s magnetic field and the electric current in a wire winding. DC motors can be further classified into brushed DC motors and brushless DC motors, depending on their commutation method.
Key Characteristics of DC Motors
- High speed operation
- Continuous rotation
- Simple speed control
- Requires feedback for precise positioning
- Relatively inexpensive
Differences between Stepper Motors and DC Motors
Now that we have a basic understanding of stepper motors and DC motors, let’s compare their key differences in various aspects.
1. Motion Control
Stepper motors excel in applications requiring precise positioning and repeatability. They move in discrete steps, allowing for accurate control of position and speed. The number of steps per revolution depends on the motor’s design and can range from a few steps to several hundred. This makes stepper motors ideal for applications such as 3D printers, CNC machines, and robotics.
On the other hand, DC motors provide continuous rotation and are better suited for applications requiring high speed and smooth motion. They can easily achieve high rotational speeds, but precise positioning requires additional feedback mechanisms like encoders or hall sensors.
2. Torque
Stepper motors have high holding torque, meaning they can maintain their position even when external forces are applied. They also have high torque at low speeds, making them suitable for applications requiring high force at low velocities, such as in valve control or door locks.
DC motors, particularly brushed DC motors, have a more linear torque-speed relationship. They offer high starting torque and can achieve high speeds, but their torque decreases as the speed increases. Brushless DC motors offer a flatter torque-speed curve, providing a wider operating range.
3. Speed Control
Controlling the speed of a stepper motor is straightforward. By adjusting the frequency of the input pulses, you can easily control the motor’s rotation speed. However, stepper motors typically operate at lower speeds compared to DC motors.
DC motors offer simple speed control through voltage regulation. By varying the voltage applied to the motor, you can adjust its speed. Additionally, pulse-width modulation (PWM) can be used for more precise speed control.
4. Efficiency
Stepper motors have lower efficiency compared to DC motors, particularly at high speeds. This is because stepper motors draw current even when holding a position, resulting in power dissipation as heat.
DC motors, especially brushless DC motors, have higher efficiency. They only draw current when rotating and have lower power losses due to their design and commutation method.
5. Cost
Stepper motors are generally more expensive than DC motors due to their more complex construction and control requirements. They often require dedicated driver circuits to handle the precise sequencing of pulses.
DC motors, particularly brushed DC motors, are relatively inexpensive and widely available. Brushless DC motors are more expensive than brushed motors but offer higher efficiency and longer life spans.
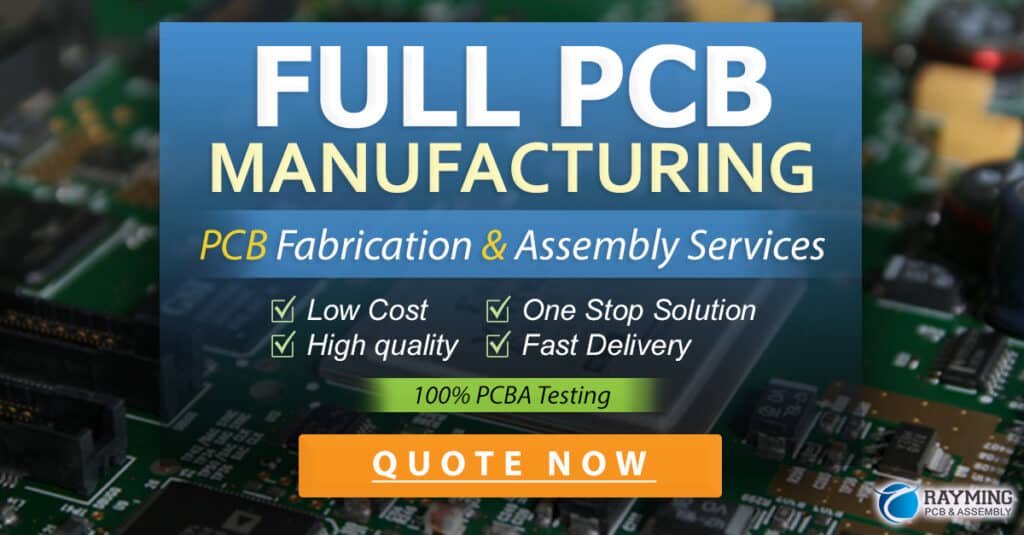
Comparison Table
Characteristic | Stepper Motor | DC Motor |
---|---|---|
Motion Control | Precise positioning, discrete steps | Continuous rotation, requires feedback for precision |
Torque | High holding torque, high torque at low speeds | High starting torque, torque decreases with speed |
Speed Control | Controlled by input pulse frequency | Controlled by voltage or PWM |
Efficiency | Lower efficiency, power dissipation when holding position | Higher efficiency, especially brushless DC motors |
Cost | More expensive, requires dedicated driver circuits | Relatively inexpensive, brushless motors are pricier |
Applications
Stepper motors and DC motors find applications in various fields, each excelling in specific areas based on their characteristics.
Stepper Motor Applications
- 3D printers
- CNC machines
- Robotics
- Valve control
- Positioning systems
- Autofocus mechanisms in cameras
- Textile machinery
DC Motor Applications
- Industrial automation
- Electric vehicles
- Pumps and compressors
- Fans and blowers
- Conveyor systems
- Power tools
- Toys and hobby projects
FAQ
1. Can a stepper motor be used in place of a DC motor?
In some cases, a stepper motor can be used as an alternative to a DC motor, particularly when precise positioning or low-speed torque is required. However, stepper motors may not be suitable for applications demanding high speeds or continuous rotation.
2. How do I choose between a stepper motor and a DC motor for my project?
The choice between a stepper motor and a DC motor depends on your project’s specific requirements. Consider factors such as the need for precise positioning, speed range, torque requirements, and budget. Stepper motors are ideal for applications prioritizing accuracy and repeatability, while DC motors are better suited for high-speed and continuous rotation applications.
3. Can I control a stepper motor with a simple DC motor driver?
No, stepper motors require dedicated stepper motor drivers that can generate the necessary sequence of pulses to control the motor’s movement. Using a simple DC motor driver with a stepper motor will not provide the desired stepping behavior and may even damage the motor.
4. Are there any hybrid motors that combine the features of stepper motors and DC motors?
Yes, there are hybrid stepper motors that combine the best features of both stepper motors and DC motors. These motors have a permanent magnet rotor and a wound stator, offering the precise positioning of stepper motors along with the high torque and speed capabilities of DC motors. However, they are more complex and expensive compared to standard stepper or DC motors.
5. How do I ensure smooth motion with a stepper motor?
To achieve smooth motion with a stepper motor, you can employ microstepping, which divides each full step into smaller micro-steps. This results in smoother rotation and reduces vibration. Additionally, proper motor sizing, load matching, and acceleration/deceleration profiles can help optimize the motor’s performance and minimize jerkiness.
Conclusion
Stepper motors and DC motors are two distinct types of electric motors with unique characteristics and applications. Stepper motors offer precise positioning and high torque at low speeds, making them suitable for applications requiring accuracy and repeatability. On the other hand, DC motors provide continuous rotation and high-speed operation, finding use in a wide range of industrial and consumer applications.
When selecting between a stepper motor and a DC motor, it is essential to consider the specific requirements of your project, such as positioning accuracy, speed range, torque demands, and budget constraints. Understanding the strengths and limitations of each motor type will help you make an informed decision and ensure optimal performance in your application.
No responses yet