Introduction to Schematic Parts Management
As an electronics enthusiast or professional, you know that creating a well-organized and efficient schematic is crucial for the success of your project. One of the most important aspects of designing a schematic is proper parts management. In this article, we will explore the best practices for managing your electronic components, from the initial planning stages to the final implementation.
Why is Schematic Parts Management Important?
Effective schematic parts management offers several benefits:
-
Time-saving: A well-organized parts library helps you quickly locate and select the components you need, reducing the time spent on searching and cross-referencing.
-
Cost-effective: By managing your parts efficiently, you can avoid ordering duplicate or unnecessary components, saving money on your project.
-
Consistency: Consistent part naming and organization ensure that your schematic is easy to read and understand, both for yourself and for others who may work on the project.
-
Error reduction: Proper parts management minimizes the chances of using the wrong component or making other errors in your schematic.
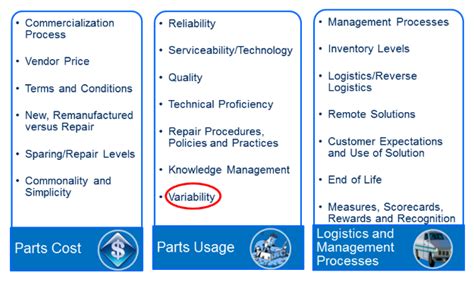
Key Components of Schematic Parts Management
To effectively manage your electronic parts, consider the following key components:
1. Part Naming Conventions
Establish a clear and consistent naming convention for your parts. This may include:
- Using a prefix to indicate the component type (e.g., “R” for resistors, “C” for capacitors)
- Including the component value or rating in the name
- Adding a unique identifier or number to distinguish between similar parts
Example part naming convention:
Prefix | Component Type | Value/Rating | Unique Identifier |
---|---|---|---|
R | Resistor | 100k | 01 |
C | Capacitor | 10uF | 02 |
Q | Transistor | 2N3904 | 01 |
2. Part Libraries
Create and maintain a well-organized part library. This can be done using:
- Schematic design software with built-in part libraries
- Custom libraries created specifically for your projects
- Spreadsheets or databases to store part information
When creating or using part libraries, consider:
- Categorizing parts by type, function, or project
- Including relevant information such as part numbers, manufacturers, and datasheets
- Regularly updating and maintaining your libraries to ensure accuracy
3. Supplier Management
Establish relationships with reliable suppliers and maintain a list of preferred vendors. This helps ensure:
- Consistent part quality and availability
- Competitive pricing
- Efficient ordering and delivery processes
Keep track of supplier information, including:
- Contact details
- Ordering procedures
- Lead times
- Minimum order quantities
4. Inventory Management
Implement an inventory management system to keep track of your electronic components. This may involve:
- Using inventory management software or tools
- Regularly updating your inventory records as parts are used or restocked
- Setting up a physical organization system, such as labeled storage bins or drawers
Effective inventory management helps you:
- Avoid running out of essential components
- Identify excess or obsolete parts
- Plan for future projects based on available resources
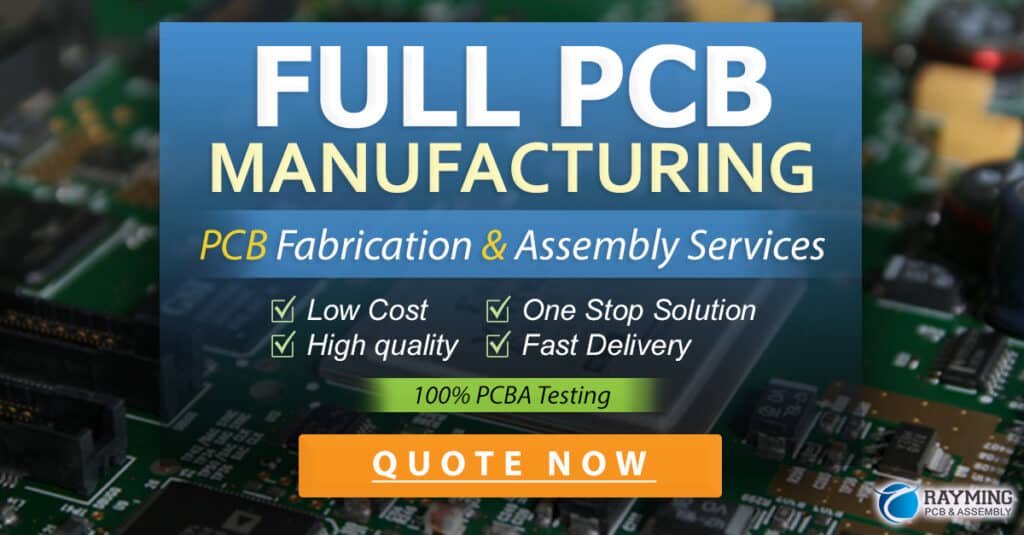
Best Practices for Schematic Parts Management
To optimize your schematic parts management process, consider the following best practices:
-
Plan ahead: Before starting your schematic, take the time to plan your parts list and ensure you have all the necessary components on hand.
-
Use consistent symbols: Maintain consistency in your schematic symbols to make your drawings easy to read and understand.
-
Document your design: Include clear and concise notes in your schematic to explain any unique or complex aspects of your design.
-
Collaborate effectively: If working with a team, establish clear guidelines for parts management and communication to ensure everyone is on the same page.
-
Regularly review and update: Periodically review your parts management system to identify areas for improvement and make necessary updates.
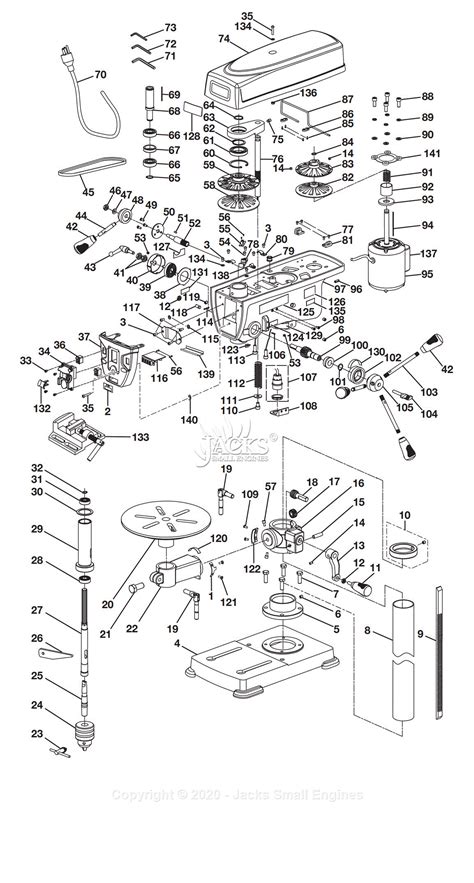
Tools for Schematic Parts Management
There are several tools available to help streamline your schematic parts management process, including:
-
Schematic design software: Many schematic design programs, such as KiCad, Eagle, and Altium Designer, offer built-in part libraries and management features.
-
Spreadsheets: Use spreadsheet software like Microsoft Excel or Google Sheets to create and maintain custom parts lists and inventory records.
-
Inventory management software: Dedicated inventory management tools, such as PartKeepr or InvenTree, can help you track and organize your electronic components.
-
Version control systems: If collaborating with others, consider using a version control system like Git to manage changes to your schematic and parts lists.
Frequently Asked Questions (FAQ)
-
Q: How do I choose the right part naming convention for my project?
A: The best part naming convention depends on your specific needs and preferences. Consider factors such as clarity, consistency, and ease of use. A good starting point is to use a prefix to indicate the component type, followed by the value or rating, and a unique identifier if needed. -
Q: What should I include in my part libraries?
A: Your part libraries should include all the relevant information about your electronic components, such as part numbers, manufacturers, datasheets, and any notes on usage or compatibility. Organize your libraries in a logical manner, such as by component type or project. -
Q: How often should I update my inventory records?
A: It’s a good practice to update your inventory records whenever parts are used or restocked. This helps ensure that your records remain accurate and up to date. The frequency of updates may vary depending on the scale of your projects and the rate at which you use components. -
Q: Can I use multiple tools for schematic parts management?
A: Yes, you can use a combination of tools to manage your electronic parts. For example, you might use schematic design software for creating your schematics, a spreadsheet for maintaining your parts lists, and inventory management software for tracking your physical components. -
Q: How can I ensure consistency in my schematic symbols?
A: To ensure consistency in your schematic symbols, establish a standard library of symbols and stick to it throughout your project. Many schematic design programs offer built-in symbol libraries that follow industry standards. If creating your own symbols, make sure they are clear, easy to understand, and consistent with the rest of your design.
Conclusion
Effective schematic parts management is essential for the success of any electronics project. By establishing clear naming conventions, maintaining organized part libraries, managing suppliers and inventory, and following best practices, you can streamline your design process, save time and money, and reduce the risk of errors. Remember to regularly review and update your parts management system to ensure it continues to meet your needs as your projects evolve.
No responses yet