Introduction to PCB Panel Sizes
When it comes to manufacturing printed circuit boards (PCBs), one of the key factors to consider is the PCB panel size. The panel size refers to the dimensions of the large board that contains multiple individual PCBs. Choosing the right panel size is crucial for optimizing the production process, minimizing waste, and ensuring the quality of the final product. In this article, we’ll dive into the world of standard PCB panel sizes and provide you with everything you need to know to make informed decisions for your PCB projects.
Understanding the Importance of PCB Panel Size
Optimizing Manufacturing Efficiency
The PCB panel size plays a significant role in the efficiency of the manufacturing process. By selecting an appropriate panel size, you can maximize the number of individual PCBs that can be produced on a single panel. This optimization reduces the overall production time and cost, as fewer panels need to be processed to achieve the desired quantity of PCBs. Additionally, using standard panel sizes that are compatible with the manufacturing equipment ensures smoother operations and minimizes the need for custom setups.
Minimizing Material Waste
Another key benefit of choosing the right PCB panel size is the reduction of material waste. When the individual PCBs are arranged efficiently on the panel, there is less unused space between them. This optimization leads to better material utilization and minimizes the amount of excess material that needs to be trimmed away after the manufacturing process. By reducing waste, you can lower the overall material costs and contribute to a more environmentally friendly production process.
Ensuring PCB Quality
The PCB panel size also has an impact on the quality of the manufactured PCBs. Larger panel sizes can be more prone to warping and dimensional instability during the manufacturing process, especially if the panel is not properly supported. This can lead to issues such as misalignment of layers, poor registration, and reduced reliability of the final product. By selecting an appropriate panel size and considering factors such as the PCB thickness and copper weight, you can mitigate these risks and ensure the highest quality of your PCBs.
Standard PCB Panel Sizes
Common Panel Sizes
There are several standard PCB panel sizes commonly used in the industry. These sizes have been established to accommodate various PCB designs and to be compatible with standard manufacturing equipment. Some of the most common panel sizes include:
Panel Size | Dimensions (mm) | Dimensions (inches) |
---|---|---|
Small | 100 x 100 | 3.94 x 3.94 |
Medium | 200 x 200 | 7.87 x 7.87 |
Large | 300 x 300 | 11.81 x 11.81 |
Extra Large | 450 x 450 | 17.72 x 17.72 |
These standard sizes provide a range of options to accommodate different PCB designs and quantities. Smaller panel sizes are suitable for low-volume prototypes or designs with smaller individual PCBs, while larger panel sizes are ideal for high-volume production runs or larger PCB designs.
Factors Affecting Panel Size Selection
When selecting the appropriate PCB panel size for your project, there are several factors to consider:
-
PCB Dimensions: The dimensions of your individual PCBs will influence the panel size selection. You need to ensure that the panel size can accommodate multiple copies of your PCB design while leaving sufficient space for tooling, registration marks, and other necessary elements.
-
Quantity: The required quantity of PCBs also plays a role in panel size selection. If you need a high volume of PCBs, using a larger panel size can be more efficient and cost-effective. However, for smaller quantities or prototypes, a smaller panel size may be more suitable to avoid excessive waste.
-
Manufacturing Capabilities: It’s essential to consider the capabilities of your PCB manufacturer when choosing a panel size. Some manufacturers may have limitations on the maximum panel size they can handle or may require specific panel dimensions to be compatible with their equipment. Discussing your requirements with the manufacturer can help you make an informed decision.
-
Cost Considerations: The panel size can impact the overall cost of your PCB project. Larger panel sizes may offer economies of scale, reducing the per-unit cost of each PCB. However, if you have a smaller quantity requirement, using a larger panel size may result in higher costs due to material waste. Striking a balance between panel size and cost-efficiency is crucial.
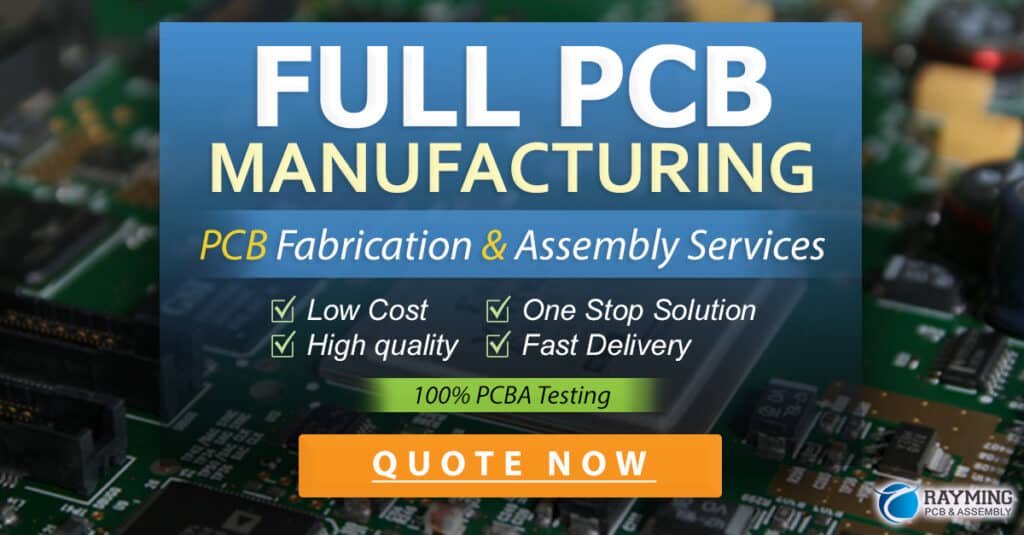
Designing for Panel Optimization
Panelization Techniques
To make the most of your chosen PCB panel size, it’s important to implement effective panelization techniques. Panelization involves arranging multiple individual PCBs on a single panel in a way that maximizes space utilization and minimizes waste. Some common panelization techniques include:
-
Tab Routing: This technique involves creating tabs or break-off points between individual PCBs on the panel. After the manufacturing process, the tabs are broken or cut to separate the individual boards. Tab routing allows for efficient use of panel space and easy separation of PCBs.
-
V-Scoring: V-scoring involves creating V-shaped grooves between individual PCBs on the panel. These grooves allow for easy separation of the boards after manufacturing. V-scoring is suitable for thinner PCBs and provides a clean and precise separation method.
-
Mousebites: Mousebites are small, perforated holes placed between individual PCBs on the panel. These holes create weak points that allow for easy snapping or breaking of the PCBs from the panel. Mousebites are commonly used for smaller PCBs or when a large number of boards need to be separated quickly.
Design Considerations for Panelization
When designing your PCBs for panelization, there are several factors to keep in mind:
-
Spacing: Ensure that there is sufficient spacing between individual PCBs on the panel. This spacing, known as the tooling strip or breakaway tab, allows for the placement of tooling holes, fiducial marks, and other necessary elements. Adequate spacing also prevents damage to the individual PCBs during the separation process.
-
Fiducial Marks: Include fiducial marks on your panel design. These marks serve as reference points for the manufacturing equipment to ensure accurate alignment and registration of the layers. Fiducial marks are especially crucial when dealing with high-density designs or tight tolerances.
-
Tooling Holes: Incorporate tooling holes in your panel design. These holes are used to secure the panel during the manufacturing process and ensure precise alignment. The size and placement of tooling holes should be based on the specifications provided by your PCB manufacturer.
-
Panelization Software: Utilize panelization software tools to optimize your panel layout. These tools can automatically arrange your individual PCBs on the panel, considering factors such as spacing, tooling holes, and fiducial marks. They can also generate the necessary output files for manufacturing, saving time and reducing the risk of errors.
Frequently Asked Questions (FAQ)
-
Q: What is the most common PCB panel size?
A: The most common PCB panel size is 18″ x 24″ (457 mm x 610 mm). This size is widely used in the industry and is compatible with most manufacturing equipment. -
Q: Can I use custom panel sizes for my PCB project?
A: Yes, it is possible to use custom panel sizes. However, it’s important to discuss your requirements with your PCB manufacturer to ensure that they can accommodate your specific panel size and to understand any potential impact on cost and lead time. -
Q: How does the panel size affect the cost of PCB manufacturing?
A: The panel size can impact the cost of PCB manufacturing in several ways. Larger panel sizes may offer economies of scale, reducing the per-unit cost of each PCB. However, if you have a smaller quantity requirement, using a larger panel size may result in higher costs due to material waste. It’s important to find a balance between panel size and cost-efficiency based on your specific project requirements. -
Q: What is the minimum spacing required between individual PCBs on a panel?
A: The minimum spacing required between individual PCBs on a panel depends on various factors, such as the PCB thickness, copper weight, and the manufacturing capabilities of your PCB manufacturer. As a general guideline, a minimum spacing of 2-3 mm is often recommended, but it’s best to consult with your manufacturer for their specific requirements. -
Q: How do I choose the right panelization technique for my PCB project?
A: The choice of panelization technique depends on factors such as the PCB thickness, the required separation method, and the manufacturing capabilities of your PCB manufacturer. Tab routing is a common technique that allows for efficient use of panel space and easy separation of PCBs. V-scoring is suitable for thinner PCBs and provides a clean and precise separation method. Mousebites are often used for smaller PCBs or when a large number of boards need to be separated quickly. Discuss your specific requirements with your manufacturer to determine the most suitable panelization technique for your project.
Conclusion
Understanding standard PCB panel sizes is essential for optimizing your PCB manufacturing process, minimizing waste, and ensuring the quality of your final product. By considering factors such as PCB dimensions, quantity, manufacturing capabilities, and cost, you can select the appropriate panel size for your project. Implementing effective panelization techniques and following design considerations for panelization will help you make the most of your chosen panel size.
Remember to work closely with your PCB manufacturer throughout the process to ensure that your panel size and design requirements are compatible with their capabilities. By collaborating with your manufacturer and leveraging their expertise, you can achieve successful and cost-effective PCB production.
With this comprehensive guide to standard PCB panel sizes, you are now equipped with the knowledge needed to make informed decisions for your PCB projects. By optimizing your panel size selection and design, you can streamline your manufacturing process, reduce costs, and deliver high-quality PCBs that meet your specific requirements.
No responses yet