Introduction to PCB Design
Printed Circuit Board (PCB) design is a crucial aspect of modern electronics, enabling the creation of compact, reliable, and efficient devices. In recent years, the demand for more advanced and innovative PCB designs has grown significantly, particularly in the realm of sporty and high-performance applications. One key development in this field is the incorporation of 3D component model drivers into the layout process, which allows designers to create more accurate and optimized PCBs.
In this article, we will explore the concept of sporty 3D component model drivers layout PCB design, discussing its benefits, challenges, and best practices. We will also delve into the various tools and techniques used in this approach, as well as its applications in different industries.
The Benefits of 3D Component Model Drivers in PCB Design
Improved Accuracy and Precision
One of the primary advantages of using 3D component model drivers in PCB design is the enhanced accuracy and precision it offers. By incorporating detailed 3D models of components into the layout process, designers can ensure that their PCBs are optimized for performance, reliability, and manufacturability.
Traditional 2D PCB design methods often rely on simplified representations of components, which can lead to issues such as incorrect component placement, insufficient clearance, and potential interference. In contrast, 3D component model drivers provide a more realistic and comprehensive view of the PCB, allowing designers to identify and resolve potential problems early in the design process.
Faster Design Iteration and Prototyping
Another significant benefit of using 3D component model drivers in PCB design is the ability to iterate and prototype designs more quickly. With accurate 3D models of components, designers can simulate and test their PCBs virtually, reducing the need for physical prototypes and saving time and resources.
This virtual prototyping process allows designers to experiment with different layouts, component placements, and routing strategies, enabling them to optimize their designs for performance and manufacturability. By catching and resolving issues early in the design process, designers can avoid costly redesigns and delays later on.
Enhanced Collaboration and Communication
3D component model drivers also facilitate better collaboration and communication among design teams and stakeholders. By providing a more visually engaging and intuitive representation of the PCB, 3D models can help bridge the gap between technical and non-technical team members, enabling more effective decision-making and problem-solving.
Moreover, 3D models can be easily shared and reviewed by remote team members, fostering a more collaborative and efficient design process. This is particularly valuable in today’s globalized economy, where design teams are often distributed across different locations and time zones.
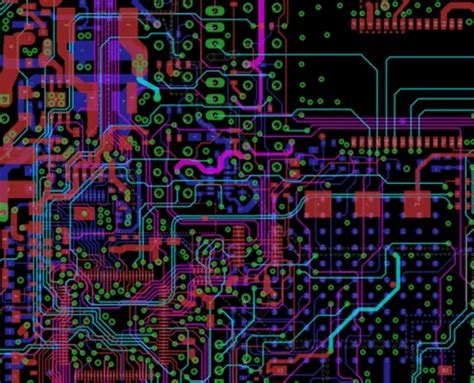
Challenges and Considerations in 3D Component Model Drivers Layout PCB Design
Compatibility and Interoperability
One of the main challenges in implementing 3D component model drivers in PCB design is ensuring compatibility and interoperability between different software tools and formats. While many PCB design software packages now support 3D component models, there can still be issues with file formats, model quality, and consistency across different platforms.
To mitigate these challenges, it is essential to establish clear standards and guidelines for 3D component model creation and exchange. This may involve working closely with component manufacturers and suppliers to ensure that their models are accurate, up-to-date, and compatible with your design tools.
Computational Resources and Performance
Another consideration when using 3D component model drivers in PCB design is the increased computational resources and performance required. Compared to traditional 2D design methods, working with 3D models can be more demanding on computer hardware and software, particularly when dealing with complex and high-density designs.
To address this issue, designers may need to invest in more powerful workstations and optimize their design tools and workflows for 3D performance. This may involve using techniques such as model simplification, layer management, and selective loading of components to reduce the computational burden and improve overall performance.
Learning Curve and Skill Development
Adopting 3D component model drivers in PCB design also requires a certain level of skill development and a learning curve for designers. While many of the fundamental principles of PCB design remain the same, working with 3D models introduces new tools, techniques, and considerations that designers must master.
To support this transition, organizations may need to invest in training and education programs for their design teams, as well as establish best practices and guidelines for 3D PCB design. This may involve partnering with software vendors, industry associations, and educational institutions to access the latest resources and expertise in this field.
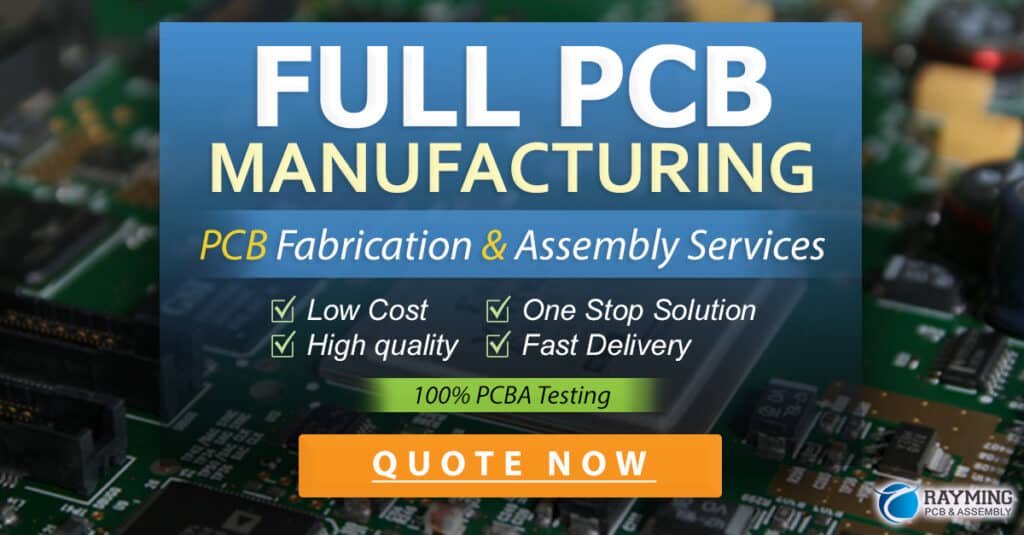
Best Practices for Sporty 3D Component Model Drivers Layout PCB Design
Choosing the Right Components and Models
One of the key best practices in sporty 3D component model drivers layout PCB design is selecting the right components and models for your project. This involves carefully evaluating the performance, reliability, and compatibility of different components, as well as ensuring that their 3D models are accurate and up-to-date.
When sourcing components and models, it is important to work with reputable suppliers and manufacturers who have a proven track record of quality and reliability. This may involve establishing long-term partnerships and collaborations to ensure a steady supply of high-quality components and models.
Optimizing Layout and Routing
Another critical best practice in 3D PCB design is optimizing the layout and routing of your components and traces. This involves carefully considering factors such as component placement, clearance, and signal integrity to ensure that your PCB performs optimally and reliably.
When laying out your components in 3D, it is important to consider not only their physical dimensions but also their thermal and electromagnetic properties. This may involve using simulation tools to analyze the thermal and EMI performance of your design, as well as employing techniques such as shielding, grounding, and filtering to mitigate potential issues.
Similarly, when routing your traces in 3D, it is important to consider factors such as impedance matching, crosstalk, and signal reflections. This may involve using advanced routing algorithms and techniques such as differential pairs, controlled impedance, and length matching to ensure optimal signal integrity and performance.
Validating and Testing Your Design
Finally, a crucial best practice in sporty 3D component model drivers layout PCB design is validating and testing your design thoroughly before manufacturing. This involves using a range of simulation, analysis, and verification tools to ensure that your PCB meets all performance, reliability, and regulatory requirements.
Some key validation and testing activities may include:
- Signal integrity analysis
- Thermal simulation
- EMI/EMC analysis
- Design rule checking (DRC)
- Manufacturing feasibility analysis
By investing time and resources in rigorous validation and testing, you can catch and resolve potential issues early in the design process, reducing the risk of costly redesigns and delays later on.
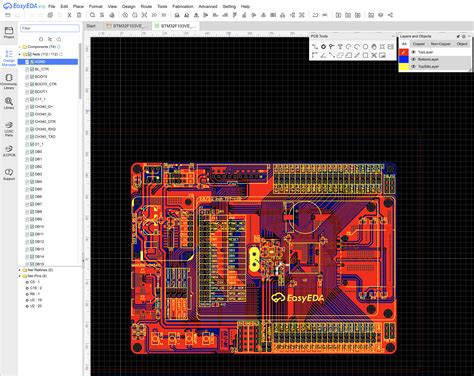
Applications and Industries
Sporty 3D component model drivers layout PCB design has a wide range of applications across different industries and sectors. Some key areas where this approach is particularly valuable include:
Automotive Electronics
In the automotive industry, PCBs are used in a wide range of applications, from engine control units and infotainment systems to advanced driver assistance systems (ADAS) and autonomous driving technologies. By using 3D component model drivers in PCB design, automotive engineers can create more compact, reliable, and high-performance electronics that can withstand the harsh operating conditions of the automotive environment.
Aerospace and Defense
In the aerospace and defense sector, PCBs are used in a variety of mission-critical applications, from avionics and communications systems to radar and electronic warfare technologies. By using 3D component model drivers in PCB design, aerospace and defense engineers can create more robust, reliable, and high-performance electronics that can operate in extreme environments and withstand the rigors of military and aerospace applications.
Consumer Electronics
In the consumer electronics industry, PCBs are used in a wide range of products, from smartphones and tablets to wearables and smart home devices. By using 3D component model drivers in PCB design, consumer electronics manufacturers can create more innovative, compact, and high-performance products that meet the ever-changing needs and expectations of consumers.
Medical Devices
In the medical device industry, PCBs are used in a variety of applications, from diagnostic equipment and patient monitoring systems to implantable devices and prosthetics. By using 3D component model drivers in PCB design, medical device manufacturers can create more reliable, accurate, and safe electronics that meet the stringent regulatory requirements of the healthcare industry.
Frequently Asked Questions (FAQ)
1. What are the benefits of using 3D component model drivers in PCB design?
Using 3D component model drivers in PCB design offers several benefits, including improved accuracy and precision, faster design iteration and prototyping, and enhanced collaboration and communication among design teams and stakeholders.
2. What are some of the challenges in implementing 3D component model drivers in PCB design?
Some of the main challenges in implementing 3D component model drivers in PCB design include ensuring compatibility and interoperability between different software tools and formats, managing increased computational resources and performance requirements, and supporting the learning curve and skill development of designers.
3. What are some best practices for selecting components and models in 3D PCB design?
When selecting components and models in 3D PCB design, it is important to carefully evaluate their performance, reliability, and compatibility, as well as ensure that their 3D models are accurate and up-to-date. Working with reputable suppliers and manufacturers who have a proven track record of quality and reliability is also crucial.
4. How can designers optimize the layout and routing of components and traces in 3D PCB design?
To optimize the layout and routing of components and traces in 3D PCB design, designers should consider factors such as component placement, clearance, signal integrity, thermal and electromagnetic properties, and advanced routing techniques such as differential pairs, controlled impedance, and length matching.
5. What are some key validation and testing activities in sporty 3D component model drivers layout PCB design?
Some key validation and testing activities in sporty 3D component model drivers layout PCB design include signal integrity analysis, thermal simulation, EMI/EMC analysis, design rule checking (DRC), and manufacturing feasibility analysis. By investing time and resources in rigorous validation and testing, designers can catch and resolve potential issues early in the design process.
Conclusion
Sporty 3D component model drivers layout PCB design represents a significant advancement in the field of electronics design, enabling the creation of more accurate, reliable, and high-performance PCBs for a wide range of applications and industries. By incorporating detailed 3D models of components into the layout process, designers can optimize their designs for performance, manufacturability, and innovation, while also facilitating better collaboration and communication among team members and stakeholders.
While there are certainly challenges and considerations to be addressed in implementing this approach, the benefits of 3D component model drivers in PCB design are clear and compelling. By adopting best practices such as careful component selection, layout optimization, and rigorous validation and testing, designers can unlock the full potential of this powerful methodology and create PCBs that push the boundaries of performance, reliability, and innovation.
As the demands for more advanced and sophisticated electronics continue to grow across industries such as automotive, aerospace, consumer electronics, and medical devices, the importance of sporty 3D component model drivers layout PCB design will only continue to increase. By staying at the forefront of this exciting field and embracing its tools, techniques, and best practices, designers and organizations can position themselves for success in the fast-paced and ever-evolving world of electronics design.
Advantage | Description |
---|---|
Improved Accuracy and Precision | 3D component model drivers provide a more realistic and comprehensive view of the PCB, allowing designers to identify and resolve potential problems early in the design process. |
Faster Design Iteration and Prototyping | With accurate 3D models of components, designers can simulate and test their PCBs virtually, reducing the need for physical prototypes and saving time and resources. |
Enhanced Collaboration and Communication | 3D models can help bridge the gap between technical and non-technical team members, enabling more effective decision-making and problem-solving. |
Challenge | Description |
---|---|
Compatibility and Interoperability | Ensuring compatibility and interoperability between different software tools and formats can be a challenge when implementing 3D component model drivers in PCB design. |
Computational Resources and Performance | Working with 3D models can be more demanding on computer hardware and software, particularly when dealing with complex and high-density designs. |
Learning Curve and Skill Development | Adopting 3D component model drivers in PCB design requires a certain level of skill development and a learning curve for designers. |
No responses yet