What is an SPDT Relay?
An SPDT relay, which stands for Single Pole Double Throw relay, is an electromechanical switch that uses an electromagnet to mechanically operate a switch. It allows a low power control signal to switch a much higher power circuit on and off.
SPDT relays have one common terminal and two switchable terminals, referred to as Normally Open (NO) and Normally Closed (NC). When the relay coil is not energized, the common terminal connects to the NC terminal. When the relay coil is energized by applying the rated voltage, the common switches from the NC to the NO terminal.
Some key characteristics of SPDT relays include:
- One common terminal
- Two switchable terminals (NO and NC)
- Switches state when coil energized
- Allows low power circuit to control high power load
- Available in various sizes, ratings, and coil voltages
How Does an SPDT Relay Work?
An SPDT relay consists of an electromagnet (called the relay coil), a movable armature, a spring, and two sets of electrical contacts (NO and NC). Here’s a step-by-step of how it operates:
-
In the unenergized state (relay coil off), the spring holds the armature so the common terminal connects to the NC (normally closed) contact.
-
When voltage is applied to the relay coil, it creates a magnetic field that attracts the armature. The armature pivots, disconnecting the common from the NC contact.
-
As the armature pivots, it also connects the common terminal to the NO (normally open) contact.
-
When voltage is removed from the relay coil, the magnetic field collapses and the spring snaps the armature back to its original position. This disconnects the common from NO and reconnects it to NC.
The relay’s switching action is quick – generally around 5-10 milliseconds to open or close after the coil is energized or de-energized.
Relay Contact Arrangements
The NO and NC contact arrangements are a key part of understanding SPDT relays. These refer to the relay’s state when the coil is not powered:
-
NO (Normally Open): Has an open circuit when the relay is unenergized. Closes when energized.
-
NC (Normally Closed): Has a closed circuit when the relay is unenergized. Opens when energized.
An SPDT relay will have one of each type of contact, allowing it to switch one common terminal between two different circuits. This table summarizes the possible connection states:
Coil | Common Terminal |
---|---|
Unenergized | Connected to NC |
Energized | Connected to NO |
SPDT Relay Parameters and Ratings
When selecting an SPDT relay for an application, there are several key parameters to consider. Choosing the right ratings is critical for the relay to operate reliably and safely.
Coil Voltage
This is the rated voltage required to energize the relay coil and switch the contacts. Common coil voltages include 5V, 12V, 24V DC and 120V, 240V AC. Always use the specified voltage – too low and the relay won’t switch, too high and you risk damaging the coil.
Contact Voltage Rating
The maximum voltage that can safely be switched by the relay contacts. Must be higher than the voltage of the circuit being switched.
Contact Current Rating
The maximum current the relay contacts can handle. Choose a rating well above your expected load current to avoid overheating and welding the contacts. Note that ratings are often given for both resistive and inductive loads.
Power Rating
The maximum power the relay contacts can switch. Equal to the product of the voltage and current ratings.
Operate and Release Time
The time it takes for the relay contacts to open or close after the coil is energized or de-energized. Typically in the 5-10ms range but can vary by model.
This table summarizes some standard SPDT relay ratings:
Parameter | Common Ratings |
---|---|
Coil Voltage | 5V, 12V, 24V DC; 120V, 240V AC |
Contact Voltage | 125V AC, 250V AC, 30V DC |
Contact Current | 5A, 10A, 20A, 30A |
Power | 1250VA, 2500VA |
Operate/Release Time | 5ms, 10ms |
Always refer to the relay’s datasheet for its exact specifications.
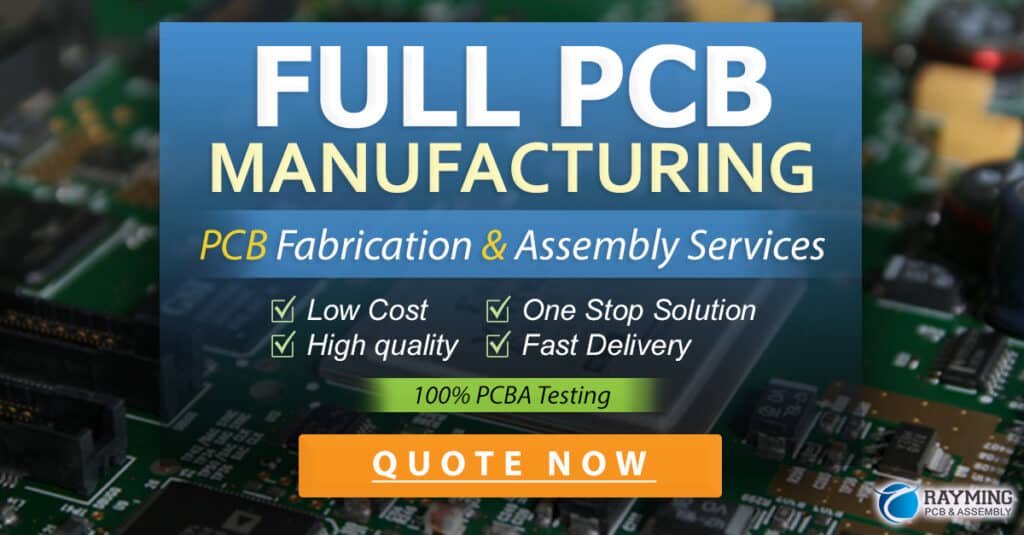
SPDT Relay Applications
SPDT relays are one of the most common types due to their versatility in switching between two circuits. Some typical applications include:
Switching Loads On/Off
The most basic use – energizing the relay coil switches a load on or off. For example, using a low voltage MCU GPIO pin to control a higher voltage device.
Switching Between Power Sources
The relay can switch a load between two power supplies for redundancy. The NC contact connects to the primary supply, NO to the backup. If the primary fails, the relay switches to the backup.
Reversing Polarity
Connecting a DC motor to the NO and NC contacts allows reversing its direction by energizing the relay.
Lighting Control
Relays can switch lights on/off based on sensors or timers. A common setup is having a photocell switch a relay to turn on lights at dusk.
HVAC Control
Thermostats use relays to switch heating or cooling equipment on and off based on temperature set points.
Driving an SPDT Relay
Driving an SPDT relay refers to switching the relay on and off by energizing its coil. This can be done with mechanical switches, transistors, or microcontrollers.
Mechanical Switching
The simplest method. A toggle or push button switch applies power to the relay coil. Easy but manual control only.
Transistor Switching
An NPN or N-channel FET transistor controlled by a lower voltage digital signal can switch the higher voltage relay coil. Allows automation or remote operation.
Include a flyback diode across the relay coil to protect the transistor from voltage spikes when the coil is de-energized.
Microcontroller Switching
GPIO pins can directly drive small relays or switch a transistor for larger ones. Allows software control based on sensors, timers, communications etc.
Typical wiring with an Arduino or Raspberry Pi:
- GPIO pin to transistor base/gate
- Transistor collector/drain to relay coil
- Relay coil to power supply
- Flyback diode across relay coil
- Common terminal to load
- NO/NC terminals to power sources
Here are some best practices when driving SPDT relays:
-
Always use a relay module or driver circuit. Connecting directly to a microcontroller risks damage from the coil’s kickback voltage.
-
Include a flyback diode across the relay coil to suppress voltage spikes.
-
Use a transistor or driver IC rated for 2-3x the relay coil current.
-
Ensure your control signal fully saturates the transistor or driver.
-
Keep high voltage wiring away from the low voltage control side.
SPDT Relay vs DPDT and Other Types
While SPDTs are a common and versatile relay, there are other contact arrangements for different switching needs. The main types are:
SPST – Single Pole Single Throw
The simplest type, a basic on-off switch. One common terminal and one NO or NC contact.
SPDT – Single Pole Double Throw
As described in this article, switches one common terminal between a NO and NC contact.
DPST – Double Pole Single Throw
Switches two separate commons between two NO or two NC contacts. Basically two SPST relays actuated by a single coil.
DPDT – Double Pole Double Throw
The most flexible. Each of two common terminals can be switched between their own NO and NC contacts. Allows simultaneously switching two circuits between two states each.
This table summarizes the key differences:
Type | Poles | Throws | Circuits | Description |
---|---|---|---|---|
SPST | 1 | 1 | 1 | On/Off |
SPDT | 1 | 2 | 2 | Switches between two circuits |
DPST | 2 | 1 | 2 | Two SPST switches, one coil |
DPDT | 2 | 2 | 4 | Two SPDT switches, one coil |
SPDT Relay Selection Tips
With so many options available, selecting the right SPDT relay for a project can seem daunting. Here are some key things to consider:
Coil Voltage
Choose a coil voltage that matches your control circuit. 5V or 12V for microcontrollers, 24V for industrial control, 120/240V for direct mains switching.
Contact Ratings
The contact ratings must exceed your load’s voltage, current, and power. Use AC ratings for AC loads, DC for DC. Contacts rated for 10A can typically handle a 1HP motor or 1500W heater.
Mechanical Durability
If the relay will be switched frequently, look for a high mechanical life rating. General purpose relays are often rated for 10-50 million cycles.
Mounting
Ensure the relay’s physical size and terminal layout are compatible with your PCB or enclosure. Common formats are through-hole, surface mount, and panel mount.
Extra Features
Some relays include extra features for protection or ease of use:
- Status LEDs to indicate coil power
- Kickback diodes for coil surge suppression
- Magnetic shielding to prevent interference
- Plug-in sockets for easy replacement
- Contact materials like AgSnO2 for better arc suppression
Cost vs. Reliability
Like most components, relays span a range of prices. While it’s tempting to use the cheapest, investing in quality from reputable brands can pay off long term, especially for critical applications.
Frequently Asked Questions
1. What does SPDT stand for in relays?
SPDT stands for Single Pole Double Throw. It refers to a relay with one common terminal that can connect to two other terminals, labeled NO (normally open) and NC (normally closed).
2. How can you tell if a relay is SPDT?
An SPDT relay will have 5 terminals in total:
– Two for the coil
– One common
– One NO (normally open)
– One NC (normally closed)
The schematic symbol also shows the contact arrangement – one common arrow switching between two terminals.
3. What is the difference between an SPDT and DPDT relay?
An SPDT relay has one common terminal that switches between an NO and NC contact. A DPDT relay has two common terminals, each with their own NO and NC contacts. So a DPDT is basically two SPDT switches actuated by a single coil.
4. How do you wire an SPDT relay?
Wiring an SPDT relay depends on the application, but in general:
- Connect the two coil terminals to your control voltage
- Connect the common terminal to your load
- Connect the NO and NC terminals to the two power sources or circuits you want to switch between
- Include a flyback diode across the coil terminals to protect your control circuit from voltage spikes
Always refer to the relay’s datasheet for specific instructions and ratings.
5. Can an SPDT relay be used for switching AC loads?
Yes, SPDT relays are available with contact ratings suitable for switching AC voltages like 120V or 240V. However, always check that the relay’s ratings exceed your load requirements. AC switching can create more arcing than DC, so a higher rated relay or one with specialized contact materials may be necessary.
Conclusion
SPDT relays are a versatile and common choice for switching electrical loads. By understanding their basic operation, contact arrangement, ratings, and application considerations, you can effectively utilize them in your projects.
When selecting an SPDT relay, always ensure the coil voltage matches your control signal, and the contact ratings comfortably exceed your load requirements. Proper wiring, including flyback diodes, is essential for reliable operation and circuit protection.
While SPDTs are useful for many switching applications, other relay types like DPDT may be more suitable for complex multi-circuit switching. As with any component, investing in quality relays from reputable suppliers is recommended for critical applications.
By following these guidelines and best practices, you can harness the power of SPDT relays to add reliable, high power switching to your electrical projects.
No responses yet