Introduction to Reflow Soldering and Profiles
Reflow soldering is a process used to mount electronic components onto printed circuit boards (PCBs) by melting solder paste applied to the board. The eC-reflow-mate is a compact reflow oven designed for this purpose. Achieving a proper solder joint requires precisely controlling the temperature profile the PCB and components are exposed to. This reflow profile consists of several stages:
-
Preheat: The board is slowly heated to evaporate solvents in the solder paste and prevent thermal shock. Typical preheat temperatures are 150-180°C.
-
Soak/Thermal Equalization: The board temperature is held steady to ensure all components reach an even temperature. Soak duration is usually 60-120 seconds.
-
Reflow: The board is quickly heated above the melting point of the solder (217°C for tin-lead solder, 240°C for lead-free) for 30-90 seconds to form the solder joints. Peak temperature is typically 20-40°C above the melting point.
-
Cooling: The board is cooled to solidify the solder joints. Cooling rate must be controlled to prevent warping or thermal shock. Less than 4°C/sec is recommended.
Precise reflow oven parameters are essential to follow the reflow profile. Key settings of the eC-reflow-mate include:
- Zone temperatures (up to 3)
- Belt speed
- Recirculated airflow
- Cooling rate
These are configured to shape the reflow profile for the specific solder paste and PCB Design. Each solder has a datasheet specifying acceptable ranges for the profile stages.
eC-reflow-mate Oven Specifications
The eC-reflow-mate is a tabletop reflow oven with the following specs:
Specification | Value |
---|---|
Max Temp | 300°C |
Heating Zones | 3 |
Max PCB Size | 300 x 260 mm |
Belt Speed | 10-100 cm/min |
Temperature Stability | ±2°C |
Airflow | Recirculated |
Cooling | 2 fans |
Power | 3.2 kW |
The 3 heating zones allow shaping the reflow profile by setting individual temperatures. Airflow recirculation provides even heating. Cooling fans enable a controlled ramp down.
Determining the Reflow Profile
The correct reflow profile depends on the solder paste and PCB characteristics. Consult the solder paste datasheet for the recommended profile. Example parameters for a lead-free solder are:
Profile Stage | Acceptable Range |
---|---|
Preheat Ramp Rate | 0.5-2°C/sec |
Preheat Temp | 150-200°C |
Soak/Equalization Time | 60-120 sec |
Peak Temp | 245-260°C |
Time Above 217°C | 60-150 sec |
Cooling Rate | 1-4°C/sec |
The specific PCB size, density, and component types will further dictate the profile. Larger, denser boards absorb more heat and may need a slower ramp rate or longer soak. Temperature-sensitive components may require a lower peak. Multiple profiles are often tested to optimize for quality.
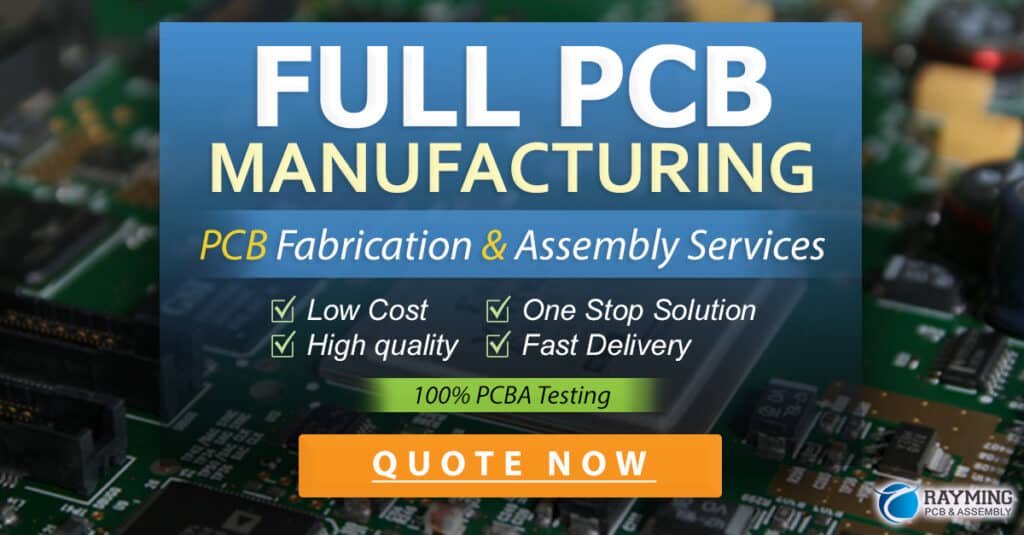
Configuring eC-reflow-mate Settings
With the target reflow profile determined, the eC-reflow-mate parameters can be set:
-
Zone Temperatures: Set the 3 zone temperatures to create the desired profile shape. A typical configuration is:
- Zone 1: 180°C (Preheat)
- Zone 2: 240°C (Soak)
- Zone 3: 265°C (Reflow)
-
Belt Speed: Adjust the speed to control the duration in each zone and total cycle time. For the above temperatures, a speed of 30 cm/min yields:
- Preheat Duration: ~45 sec
- Soak Duration: ~75 sec
- Peak Duration: ~30 sec
- Total Cycle Time: ~5 min
-
Airflow: Set the recirculated airflow to high for even heating. Reduce if temperature-sensitive parts are present.
-
Cooling: Turn on the cooling fans and open the oven hood for rapid, controlled cooling. Target less than 4°C/sec.
Run test boards instrumented with thermocouples and adjust settings to further dial in the profile. Be sure the measured temperatures fall within the solder specifications.
Best Practices for Reflow Soldering
In addition to the oven settings, proper preparation and handling are vital for quality reflow soldering:
-
Solder Paste: Use high quality paste suitable for the components and alloy. Printing should be even and consistent. Insufficient paste can cause opens while excess leads to shorts.
-
Component Placement: Components should be seated flat on their pads, not tilted or tombstoned. Check for missing or misaligned parts before reflowing.
-
Board Support: Support the PCB to prevent warping, especially for larger or thinner boards. Warped boards can stress and crack solder joints.
-
Moisture Sensitivity: Bake moisture-sensitive components before reflowing to avoid damage from outgassing. Refer to the component datasheet for baking conditions.
-
Profiling: Regularly measure the actual board temperatures to verify the reflow profile stays within specification. This catches issues like oven drift or changes in thermal mass.
-
Inspection: Visually check solder joints after reflowing for good wetting, shape, and the absence of defects like opens, shorts, or voids. X-ray inspection may be needed for hidden joints like BGAs.
Troubleshooting Common Reflow Issues
Even with a well-defined profile, problems can occur. Some common reflow defects and their likely causes are:
-
Open Joints: Insufficient heat, solder paste volume, or wetting. Increase peak temp, lengthen duration, or check paste printing.
-
Solder Bridges: Excess solder paste, component misalignment, or insufficient time above liquidus. Reduce paste volume, realign parts, or lengthen peak duration.
-
Component Shifting: Rapid heating, vibration, or uneven paste. Decrease ramp rate, check oven for vibration, or adjust solder and placement.
-
Tombstoning: Uneven heating or wetting causing one side of a chip component to pull up vertically. Adjust oven zones for more uniform temperatures.
-
Damaged Components: Excessive temperature or moisture vaporization. Lower the peak temperature or prebake moisture-sensitive parts.
-
Solder Balls: Contamination, excess flux, or rapid cooling. Verify board cleanliness, optimize paste, or reduce cooling rate.
Careful inspection and iteration are keys to resolving reflow problems. Cross-section analysis of solder joints can provide valuable insight into the actual joint formation.
Frequently Asked Questions
What is the difference between tin-lead and lead-free solder profiles?
Lead-free solders have higher melting points than tin-lead, typically 217°C vs 183°C. This means lead-free profiles use higher peak temperatures, often 240-250°C, compared to 205-220°C for tin-lead. Lead-free solders also require tighter control as they are less forgiving of temperature deviations.
How do I know if my reflow profile is correct?
The surest way is to instrument a test board with thermocouples to measure the actual temperatures reached during reflow. Compare this profile against the solder paste specifications. Visual inspection and cross-sectioning of the reflowed solder joints can further validate the profile by examining joint quality.
Can I use the same reflow profile for all my PCBs?
A profile may work for multiple PCBs if they use the same solder paste and have similar size, density, and component types. However, each design’s unique thermal characteristics mean a profile should be optimized per board. Even small changes can impact the ideal profile.
What is the best way to inspect solder joints after reflow?
Visual inspection under magnification is the first step, checking for consistent solder wetting, shape, and the absence of bridges, opens, or voids. For more complex PCBs with hidden joints, x-ray inspection provides a non-destructive way to check joint structure and defects. Cross-sectioning and microscopy offer the most detail but are time-consuming and destroy the board.
How often should I profile my reflow oven?
Reflow ovens can drift over time, altering the profile. Quarterly profiling is typical but the exact frequency depends on usage and quality requirements. At a minimum, profile when setting up a new oven, when running a new board design, and if defects or process indicators change. Continuous monitoring systems can catch shifts in real-time.
Conclusion
Achieving a high-quality reflow solder profile is essential for manufacturing reliable electronic assemblies. The eC-reflow-mate oven offers the necessary controls to optimize the profile for a given PCB design and solder paste. By understanding the key stages of a reflow profile and best practices for reflow soldering, you can configure the eC-reflow-mate parameters to consistently produce ideal solder joints. Regular profiling and inspection further ensure ongoing reflow process control and quality.
No responses yet