What is Solder Mask?
Solder mask, also known as solder resist or solder stop, is a thin layer of polymer applied to the copper traces of a printed circuit board (PCB). Its primary purpose is to protect the copper traces from oxidation, prevent solder bridges from forming between closely spaced pads, and provide electrical insulation. Solder mask also serves as a barrier against environmental contaminants and helps improve the overall durability of the PCB.
Types of Solder Mask
There are two main types of solder mask:
- Liquid Photoimageable Solder Mask (LPISM)
- Dry Film Photoimageable Solder Mask (DFISM)
Liquid Photoimageable Solder Mask (LPISM)
LPISM is the most common type of solder mask used in the PCB industry. It is applied as a liquid coating and then exposed to UV light through a photomask to cure and harden the desired areas. The uncured areas are then removed using a developer solution, leaving the copper pads exposed for soldering.
Advantages of LPISM:
- Provides excellent adhesion to the PCB surface
- Offers high resolution and fine feature definition
- Allows for easy repair and rework
Disadvantages of LPISM:
- Requires a longer processing time compared to DFISM
- Can be prone to pinholes and other defects if not applied properly
Dry Film Photoimageable Solder Mask (DFISM)
DFISM is a solid film that is laminated onto the PCB surface using heat and pressure. Like LPISM, it is exposed to UV light through a photomask and then developed to remove the uncured areas.
Advantages of DFISM:
- Faster processing time compared to LPISM
- Provides a more uniform coating thickness
- Less prone to pinholes and other defects
Disadvantages of DFISM:
- Can be more difficult to repair and rework
- May not adhere as well to the PCB surface compared to LPISM
Solder Mask Application Process
The solder mask application process typically involves the following steps:
- Surface Preparation
- Solder Mask Application
- Exposure
- Development
- Curing
- Inspection
Surface Preparation
Before applying the solder mask, the PCB surface must be cleaned and prepared to ensure proper adhesion. This typically involves:
- Cleaning the PCB to remove any contaminants or debris
- Roughening the surface using a chemical or mechanical process to improve adhesion
- Applying a primer or adhesion promoter to further enhance adhesion
Solder Mask Application
The solder mask is then applied to the PCB surface using either the LPISM or DFISM method. For LPISM, the liquid solder mask is typically applied using a screen printing or spraying process. For DFISM, the solid film is laminated onto the PCB surface using heat and pressure.
Exposure
Once the solder mask is applied, it is exposed to UV light through a photomask. The photomask contains the desired pattern of the solder mask, with the areas to be exposed to UV light being transparent and the areas to be protected being opaque. The exposure time and intensity vary depending on the type of solder mask and the specific requirements of the PCB.
Development
After exposure, the unexposed areas of the solder mask are removed using a developer solution. This typically involves immersing the PCB in the developer solution for a specific amount of time and then rinsing it with water to remove any remaining unexposed solder mask.
Curing
The remaining solder mask is then cured to fully harden and crosslink the polymer. This is typically done using heat, either in an oven or using infrared lamps. The curing temperature and time vary depending on the type of solder mask and the specific requirements of the PCB.
Inspection
Finally, the PCB is inspected to ensure that the solder mask has been applied correctly and that there are no defects or issues. This may involve visual inspection, electrical testing, or other specialized inspection methods.
Solder Mask Properties and Specifications
When selecting a solder mask for a PCB, there are several key properties and specifications to consider:
Color
Solder mask is available in a variety of colors, with green being the most common. Other colors include red, blue, yellow, black, and white. The choice of color is often based on aesthetic preferences or to aid in visual inspection.
Thickness
The thickness of the solder mask can vary depending on the specific requirements of the PCB. Typical thicknesses range from 0.5 to 2.0 mils (0.0127 to 0.0508 mm).
Dielectric Strength
Dielectric strength is a measure of the solder mask’s ability to withstand electrical breakdown. It is typically measured in volts per mil (V/mil) and can range from 500 to 1500 V/mil.
Insulation Resistance
Insulation resistance is a measure of the solder mask’s ability to resist current flow between conductors. It is typically measured in megaohms (MΩ) and can range from 10^6 to 10^12 MΩ.
Flammability
Flammability is a measure of the solder mask’s resistance to ignition and flame spread. Solder mask is typically rated according to the UL 94 flammability standard, with ratings ranging from V-0 (best) to HB (worst).
Thermal Shock Resistance
Thermal shock resistance is a measure of the solder mask’s ability to withstand rapid changes in temperature without cracking or delaminating. It is typically tested by subjecting the PCB to alternating cycles of high and low temperature.
Chemical Resistance
Chemical resistance is a measure of the solder mask’s ability to withstand exposure to various chemicals without degradation. This is important for PCBs that will be used in harsh environments or exposed to cleaning agents.
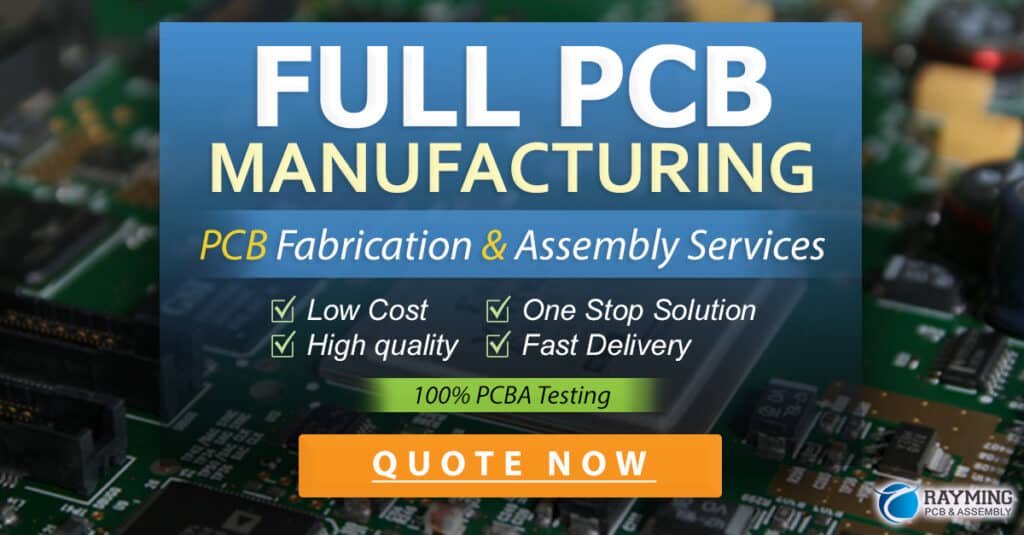
Solder Mask Design Considerations
When designing a PCB with solder mask, there are several key considerations to keep in mind:
Pad Size and Spacing
The size and spacing of the pads on the PCB must be carefully designed to ensure proper coverage by the solder mask. The solder mask opening should be slightly larger than the pad to allow for proper solder wetting and to account for any registration errors.
Solder Mask Sliver
Solder mask sliver refers to the distance between the edge of a pad and the edge of the solder mask opening. It is important to maintain a minimum solder mask sliver to prevent solder bridging and to ensure proper insulation between pads.
Solder Mask Expansion
Solder mask expansion refers to the amount that the solder mask opening grows during the exposure and development process. It is important to account for solder mask expansion when designing the PCB to ensure proper coverage and to prevent any issues with solder mask encroachment onto pads.
Via Tenting
Via tenting refers to the practice of covering vias with solder mask to prevent solder from flowing into them during the assembly process. Via tenting can help improve the reliability of the PCB and reduce the risk of solder joint defects.
Solder Mask Dams
Solder mask dams are barriers of solder mask placed between closely spaced pads to prevent solder bridging. They are typically used in areas where the pad spacing is too tight to allow for proper solder mask sliver.
Solder Mask Defects and Troubleshooting
Despite careful design and processing, solder mask defects can still occur. Some common solder mask defects include:
Pinholes
Pinholes are small holes or voids in the solder mask that can expose the underlying copper. They can be caused by contaminants on the PCB surface, air bubbles in the solder mask, or incomplete coverage during application.
Solder Mask Lifting
Solder mask lifting occurs when the solder mask separates from the PCB surface, typically around the edges of pads or traces. It can be caused by poor adhesion, contamination, or mechanical stress during processing or assembly.
Solder Mask Misregistration
Solder mask misregistration occurs when the solder mask openings are not aligned properly with the pads on the PCB. It can be caused by errors in the photomask, alignment issues during exposure, or distortion of the PCB during processing.
Solder Mask Residue
Solder mask residue refers to the presence of uncured or partially cured solder mask on the PCB surface or in the solder mask openings. It can be caused by incomplete exposure, development, or curing, or by contamination of the solder mask.
To troubleshoot solder mask defects, it is important to first identify the root cause of the issue. This may involve analyzing the PCB design, reviewing the processing parameters and conditions, or performing various tests and inspections. Once the root cause is identified, appropriate corrective actions can be taken, such as adjusting the processing parameters, modifying the PCB design, or improving the cleaning and surface preparation procedures.
FAQ
1. What is the difference between solder mask and conformal coating?
Solder mask and conformal coating are both protective coatings applied to PCBs, but they serve different purposes. Solder mask is applied before assembly and is designed to protect the copper traces and prevent solder bridging. Conformal coating is applied after assembly and is designed to protect the entire PCB from environmental factors such as moisture, dust, and chemicals.
2. Can solder mask be removed?
Yes, solder mask can be removed using various methods such as chemical stripping, laser ablation, or mechanical abrasion. However, removing solder mask can be a delicate process and should only be done when necessary, as it can potentially damage the underlying copper traces or components.
3. What is the shelf life of solder mask?
The shelf life of solder mask varies depending on the specific product and storage conditions. Most solder mask products have a shelf life of 6 to 12 months when stored in a cool, dry place away from direct sunlight. It is important to follow the manufacturer’s storage and handling guidelines to ensure optimal performance.
4. Can solder mask be used on flexible PCBs?
Yes, solder mask can be used on flexible PCBs, but it requires specialized materials and processing techniques. Flexible solder mask must be able to withstand the bending and flexing of the PCB without cracking or delaminating. It is important to work with a reputable PCB manufacturer with experience in flexible PCB fabrication to ensure proper selection and application of solder mask.
5. How does solder mask affect PCB Impedance?
Solder mask can affect PCB impedance by changing the dielectric constant of the PCB surface. The dielectric constant of solder mask is typically higher than that of air, which can lead to an increase in the impedance of the PCB traces. This effect is more pronounced at high frequencies and can be mitigated by using thinner solder mask or by adjusting the PCB design to compensate for the change in impedance.
Conclusion
Solder mask is a critical component of PCB fabrication that serves to protect the copper traces, prevent solder bridging, and provide electrical insulation. There are two main types of solder mask, LPISM and DFISM, each with its own advantages and disadvantages. The solder mask application process involves surface preparation, solder mask application, exposure, development, curing, and inspection. When selecting a solder mask, it is important to consider key properties such as color, thickness, dielectric strength, insulation resistance, flammability, thermal shock resistance, and chemical resistance. Proper PCB design, including pad size and spacing, solder mask sliver, expansion, via tenting, and dams, is essential to ensure optimal solder mask performance. Solder mask defects such as pinholes, lifting, misregistration, and residue can occur and require careful troubleshooting to identify and correct the root cause. By understanding the fundamentals of solder mask and following best practices for design and processing, PCB manufacturers can produce high-quality, reliable PCBs that meet the demands of today’s electronic applications.
No responses yet