What is Solder Mask and Why is it Important?
Solder mask, also known as solder resist or solder stop mask, is a thin protective layer applied to the copper traces of a printed circuit board (PCB). This layer serves multiple purposes, including protecting the copper from oxidation, preventing solder bridges from forming between closely spaced traces, and providing electrical insulation. Solder mask is a crucial component in the manufacturing of high-quality, reliable PCBs.
The Composition of Solder Mask
Solder mask is typically composed of a polymer material that is applied as a liquid or film to the PCB surface. The most common types of solder mask materials are:
-
Liquid Photoimageable Solder Mask (LPSM): This type of solder mask is applied as a liquid and then exposed to UV light through a photomask to cure and harden in the desired pattern.
-
Dry Film Photoimageable Solder Mask (DFSM): This solder mask is applied as a dry film and then exposed to UV light through a photomask to cure and harden in the desired pattern.
-
Liquid Photoimageable Ink (LPI): This is a newer type of solder mask that is applied using an inkjet printer and then exposed to UV light to cure and harden.
The choice of solder mask material depends on factors such as the desired thickness, flexibility, and environmental resistance of the final PCB.
The Application Process of Solder Mask
The application of solder mask involves several steps:
-
Surface preparation: The PCB surface is cleaned and any oxides or contaminants are removed to ensure proper adhesion of the solder mask.
-
Solder mask application: The chosen solder mask material is applied to the PCB surface using a screen printing, curtain coating, or spraying process.
-
Curing: The solder mask is exposed to UV light or heat to cure and harden the material.
-
Developing: For photoimageable solder masks, the unexposed areas are removed using a developer solution, leaving behind the desired solder mask pattern.
-
Final curing: The PCB undergoes a final curing process to ensure the solder mask is fully hardened and adhered to the surface.
The Benefits of Using Solder Mask
Solder mask offers several key benefits in PCB manufacturing:
-
Protection from oxidation: Solder mask prevents the copper traces from oxidizing, which can lead to reduced conductivity and reliability issues.
-
Prevention of solder bridges: By covering the spaces between closely spaced traces, solder mask prevents solder from accidentally bridging the gaps and causing short circuits.
-
Electrical insulation: Solder mask provides electrical insulation between traces, helping to prevent signal interference and leakage.
-
Improved aesthetics: Solder mask can be pigmented in various colors, allowing for improved visual appeal and easier component identification.
-
Enhanced durability: Solder mask helps to protect the PCB from physical damage, such as scratches and abrasions, as well as from environmental factors like moisture and chemicals.
The Different Types of Solder Mask
There are several types of solder mask available, each with its own unique properties and advantages.
Liquid Photoimageable Solder Mask (LPSM)
LPSM is the most widely used type of solder mask in PCB manufacturing. It is applied as a liquid and then exposed to UV light through a photomask to cure and harden in the desired pattern. LPSM offers several advantages:
- High resolution and accuracy
- Excellent adhesion to the PCB surface
- Good resistance to chemicals and solvents
- Available in a wide range of colors
Dry Film Photoimageable Solder Mask (DFSM)
DFSM is applied as a dry film and then exposed to UV light through a photomask to cure and harden in the desired pattern. DFSM offers some unique advantages compared to LPSM:
- Easier to handle and apply
- More consistent thickness across the PCB surface
- Better suited for high-volume production
However, DFSM may not offer the same level of resolution and accuracy as LPSM.
Liquid Photoimageable Ink (LPI)
LPI is a newer type of solder mask that is applied using an inkjet printer and then exposed to UV light to cure and harden. LPI offers several advantages:
- High resolution and accuracy
- Ability to create very thin layers
- Reduced waste compared to other methods
- Faster application process
However, LPI may not be as durable or resistant to chemicals and solvents as other types of solder mask.
Comparison of Solder Mask Types
Property | LPSM | DFSM | LPI |
---|---|---|---|
Resolution and accuracy | High | Medium | High |
Thickness consistency | Medium | High | High |
Adhesion to PCB surface | High | Medium | Medium |
Chemical resistance | High | Medium | Low |
Application speed | Medium | Low | High |
Choosing the Right Solder Mask for Your PCB
When selecting a solder mask for your PCB, there are several factors to consider:
- The desired resolution and accuracy of the solder mask pattern
- The required thickness and consistency of the solder mask layer
- The environmental conditions the PCB will be exposed to (e.g., chemicals, moisture, temperature)
- The production volume and speed requirements
- The available budget for the project
By carefully evaluating these factors and consulting with your PCB manufacturer, you can choose the solder mask type that best suits your specific needs.
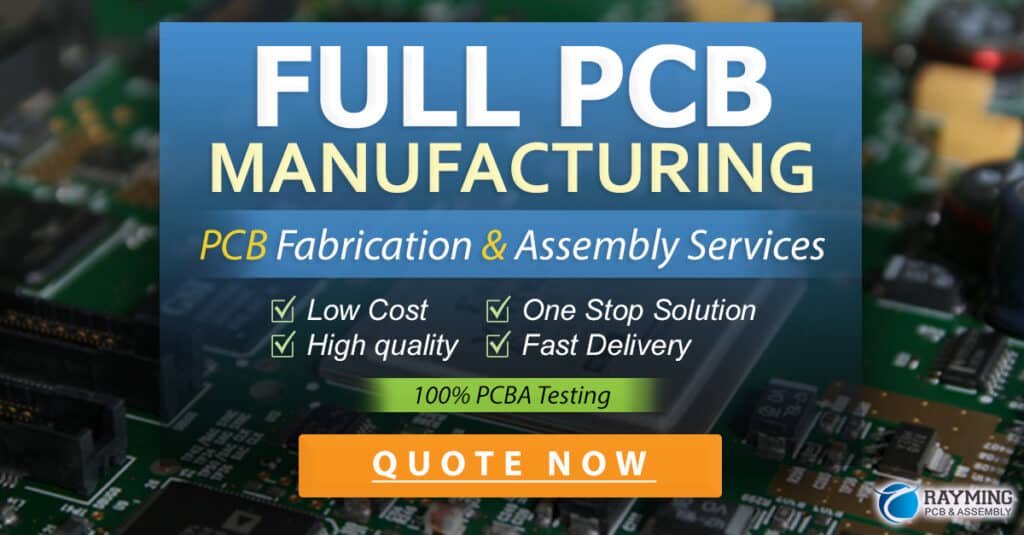
The Importance of Proper Solder Mask Application
Proper application of solder mask is critical to ensuring the reliability and performance of the final PCB. Some key considerations for solder mask application include:
-
Surface preparation: Ensuring the PCB surface is clean and free of contaminants before applying the solder mask.
-
Solder mask thickness: Applying the solder mask at the appropriate thickness to provide adequate protection without compromising the functionality of the PCB.
-
Alignment and registration: Ensuring the solder mask pattern is properly aligned and registered with the underlying copper traces.
-
Curing and post-processing: Following the correct curing and post-processing procedures to ensure the solder mask is fully hardened and adhered to the PCB surface.
Failure to properly apply solder mask can lead to issues such as poor adhesion, incomplete coverage, or misalignment, which can negatively impact the performance and reliability of the final PCB.
Troubleshooting Common Solder Mask Issues
Despite careful application and processing, issues can sometimes arise with solder mask. Some common problems and their potential solutions include:
-
Poor adhesion: This can be caused by inadequate surface preparation or incompatible materials. Ensure the PCB surface is clean and free of contaminants, and choose a solder mask material that is compatible with the PCB substrate.
-
Incomplete coverage: This can be caused by insufficient solder mask thickness or poor application technique. Ensure the solder mask is applied at the appropriate thickness and using the correct method for the chosen material.
-
Misalignment: This can be caused by improper registration or alignment during the application process. Ensure the solder mask pattern is properly aligned with the copper traces and use registration marks to maintain alignment throughout the process.
-
Bubbles or voids: This can be caused by trapped air or solvents during the application process. Ensure the solder mask is applied in a controlled environment and allow sufficient time for any trapped air or solvents to escape before curing.
By understanding the potential issues that can arise with solder mask and taking steps to prevent or address them, you can ensure the highest quality and reliability of your final PCB.
FAQ
1. What is the difference between solder mask and conformal coating?
Solder mask is a thin, protective layer applied to the copper traces of a PCB to prevent oxidation, solder bridging, and provide electrical insulation. Conformal coating, on the other hand, is a protective layer applied over the entire PCB assembly, including components, to provide additional protection against moisture, dust, and other environmental factors.
2. Can solder mask be removed from a PCB?
Yes, solder mask can be removed from a PCB using chemical or mechanical methods. However, removing solder mask can be a delicate process and may cause damage to the underlying copper traces if not done carefully. It is generally not recommended unless absolutely necessary for repairs or modifications.
3. What colors are available for solder mask?
Solder mask is available in a wide range of colors, with green being the most common. Other popular colors include red, blue, yellow, black, and white. The choice of color is often based on aesthetic preferences or to aid in component identification.
4. How does solder mask affect the impedance of a PCB?
Solder mask can have a slight effect on the impedance of a PCB, as it acts as a dielectric material between the copper traces and the surrounding environment. However, this effect is typically minimal and can be accounted for during the PCB design process by adjusting trace widths and spacing.
5. What is the typical thickness of a solder mask layer?
The typical thickness of a solder mask layer ranges from 0.0005 to 0.002 inches (0.0127 to 0.0508 mm). The exact thickness will depend on the specific solder mask material and application method used, as well as the requirements of the PCB design.
In conclusion, solder mask is a critical component in the manufacturing of high-quality, reliable PCBs. By understanding the different types of solder mask available, the application process, and the potential issues that can arise, you can make informed decisions and ensure the best possible performance and longevity of your PCB designs.
No responses yet