Introduction to Robot Chassis Design
Designing a robot chassis is a crucial step in the development of any robotic system. The chassis serves as the foundation for all other components, providing structure, support, and protection. With the advent of advanced software tools, the process of designing a robot chassis has become more efficient and precise. In this article, we will explore the various software options available for designing robot chassis and discuss their features, benefits, and limitations.
Key Considerations in Robot Chassis Design
Before delving into the software tools, it is essential to understand the key considerations in robot chassis design. These include:
-
Material selection: The choice of material depends on factors such as strength, weight, cost, and ease of fabrication. Common materials include aluminum, steel, plastic, and composites.
-
Structural integrity: The chassis must be able to withstand the forces and stresses imposed by the robot’s movements, payload, and environment.
-
Size and shape: The chassis dimensions and geometry should accommodate all necessary components and allow for efficient motion and maneuverability.
-
Manufacturability: The design should be feasible to manufacture using available tools and techniques, such as machining, 3D printing, or laser cutting.
-
Modularity and scalability: A Modular design allows for easy modifications and upgrades, while scalability ensures that the chassis can be adapted to different robot sizes and configurations.
CAD Software for Robot Chassis Design
Computer-Aided Design (CAD) software is the most widely used tool for designing robot chassis. CAD programs allow users to create precise 3D models, perform simulations, and generate manufacturing-ready drawings. Some popular CAD software packages for robot chassis design include:
1. SolidWorks
SolidWorks is a powerful parametric CAD software that offers a user-friendly interface and a wide range of design tools. It is well-suited for designing complex robot chassis with intricate geometries and multiple components. Key features of SolidWorks include:
- Parametric modeling: Allows for easy modifications and updates to the design by changing dimension values.
- Assembly modeling: Enables the creation of multi-part assemblies and the simulation of their interactions.
- Finite Element Analysis (FEA): Helps evaluate the structural integrity of the chassis under various loading conditions.
- Photorealistic rendering: Provides high-quality visualizations of the final design.
Feature | Benefit |
---|---|
Parametric modeling | Flexibility in design modifications |
Assembly modeling | Simulation of multi-part interactions |
FEA | Structural integrity evaluation |
Photorealistic rendering | High-quality visualizations |
2. Autodesk Fusion 360
Fusion 360 is a cloud-based CAD platform that combines design, engineering, and manufacturing tools in a single package. It offers a streamlined workflow for robot chassis design, from initial sketches to final fabrication. Notable features of Fusion 360 include:
- Freeform modeling: Allows for the creation of organic shapes and complex surfaces.
- Parametric modeling: Supports the creation of adaptable designs with adjustable dimensions.
- Simulation: Enables the testing of the chassis’ mechanical properties and performance.
- CAM integration: Provides tools for generating CNC machining toolpaths and 3D printing files.
Feature | Benefit |
---|---|
Freeform modeling | Creation of organic shapes and complex surfaces |
Parametric modeling | Adaptable designs with adjustable dimensions |
Simulation | Testing of mechanical properties and performance |
CAM integration | Generation of CNC machining toolpaths and 3D printing files |
3. OpenSCAD
OpenSCAD is a free, open-source software for creating solid 3D CAD models. It uses a programming language to define the geometry, making it well-suited for parametric design and rapid iterations. OpenSCAD is particularly useful for designing robot chassis with repetitive patterns or algorithmic features. Its main features include:
- Programmable modeling: Allows for the creation of complex geometries using a text-based language.
- Parametric design: Enables the creation of designs with adjustable variables and constraints.
- Boolean operations: Supports the combination of basic shapes using union, difference, and intersection operations.
- STL export: Generates files compatible with 3D printing and other manufacturing processes.
Feature | Benefit |
---|---|
Programmable modeling | Creation of complex geometries using a text-based language |
Parametric design | Designs with adjustable variables and constraints |
Boolean operations | Combination of basic shapes using union, difference, and intersection |
STL export | Generation of files compatible with 3D printing and other manufacturing processes |
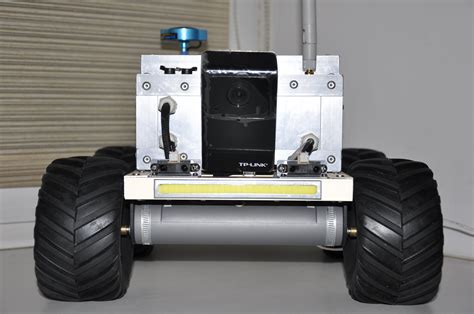
Simulation Software for Robot Chassis Design
In addition to CAD software, simulation tools play a crucial role in validating and optimizing robot chassis designs. These tools allow designers to test the chassis’ performance under various conditions, identify potential issues, and make necessary improvements before physical prototyping. Some popular simulation software packages for robot chassis design include:
1. ANSYS
ANSYS is a comprehensive engineering simulation platform that offers a wide range of tools for analyzing the structural, thermal, and electromagnetic properties of robot chassis. Its key features include:
- Finite Element Analysis (FEA): Enables the simulation of stress, deformation, and vibration under various loading scenarios.
- Topology optimization: Helps identify the optimal material distribution for maximum strength and minimum weight.
- Multiphysics simulation: Allows for the coupling of different physics domains, such as structural and thermal analysis.
- Parametric studies: Supports the exploration of design alternatives by varying input parameters and evaluating their impact on performance.
Feature | Benefit |
---|---|
FEA | Simulation of stress, deformation, and vibration |
Topology optimization | Identification of optimal material distribution |
Multiphysics simulation | Coupling of different physics domains |
Parametric studies | Exploration of design alternatives |
2. Adams
Adams is a multibody dynamics simulation software that specializes in analyzing the motion and forces in mechanical systems, including robot chassis. It allows designers to create virtual prototypes and study their behavior under realistic operating conditions. Key features of Adams include:
- Rigid and flexible body modeling: Supports the simulation of both rigid and deformable components.
- Contact modeling: Enables the simulation of contact forces and friction between components.
- Co-simulation: Allows for the integration of Adams with other software tools, such as control systems or hydraulic simulations.
- Animation and visualization: Provides tools for creating high-quality animations and visualizations of the simulated motion.
Feature | Benefit |
---|---|
Rigid and flexible body modeling | Simulation of both rigid and deformable components |
Contact modeling | Simulation of contact forces and friction |
Co-simulation | Integration with other software tools |
Animation and visualization | Creation of high-quality animations and visualizations |
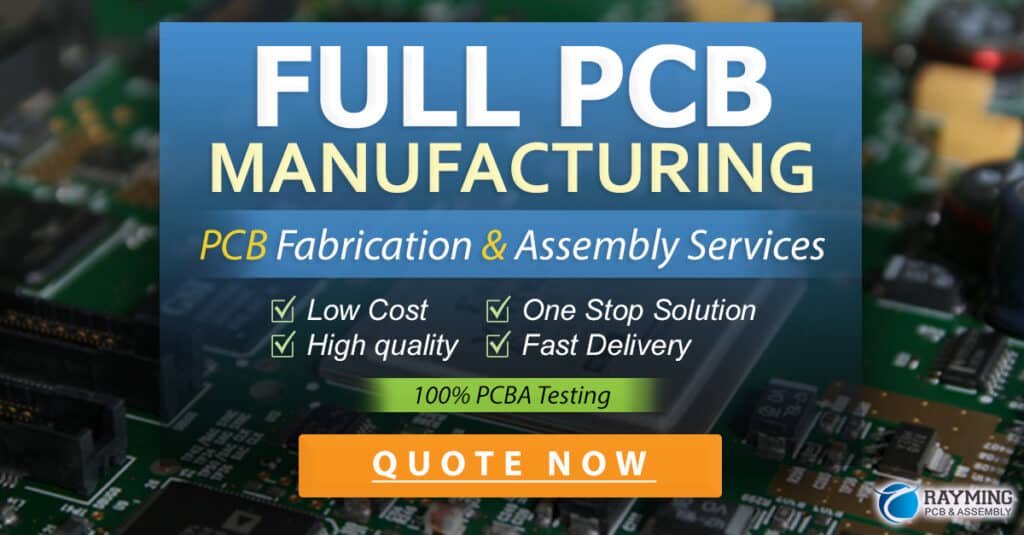
Specialized Software for Robot Chassis Design
In addition to general-purpose CAD and simulation software, there are also specialized tools specifically designed for robot chassis design. These tools often include pre-built components, libraries, and templates that streamline the design process and ensure compatibility with common robotic systems. Some examples of specialized software for robot chassis design include:
1. RobotBuilder
RobotBuilder is a web-based platform for designing and simulating robot chassis. It offers a drag-and-drop interface for assembling pre-designed components, as well as tools for customizing and optimizing the design. RobotBuilder’s main features include:
- Component library: Provides a wide selection of pre-designed components, such as wheels, motors, and brackets.
- Parametric modeling: Allows for the adjustment of component dimensions and properties to suit specific requirements.
- Simulation: Enables the testing of the chassis’ motion, stability, and payload capacity.
- Collaboration: Supports real-time collaboration and sharing of designs with team members.
Feature | Benefit |
---|---|
Component library | Wide selection of pre-designed components |
Parametric modeling | Adjustment of component dimensions and properties |
Simulation | Testing of motion, stability, and payload capacity |
Collaboration | Real-time collaboration and sharing of designs |
2. ROS Robot Designer
ROS Robot Designer is an open-source software package that integrates with the Robot Operating System (ROS) to facilitate the design and simulation of robot chassis. It provides a graphical user interface for creating and configuring robot models, as well as tools for generating ROS-compatible code. Key features of ROS Robot Designer include:
- URDF modeling: Allows for the creation of Unified Robot Description Format (URDF) files, which describe the robot’s kinematic and dynamic properties.
- Gazebo simulation: Integrates with the Gazebo simulator to enable the testing of the chassis’ behavior in a virtual environment.
- ROS integration: Generates ROS-compatible code and launch files for seamless integration with the ROS ecosystem.
- Plugin architecture: Supports the development and integration of custom plugins for extended functionality.
Feature | Benefit |
---|---|
URDF modeling | Creation of URDF files describing the robot’s properties |
Gazebo simulation | Testing of the chassis’ behavior in a virtual environment |
ROS integration | Generation of ROS-compatible code and launch files |
Plugin architecture | Development and integration of custom plugins |

Choosing the Right Software for Robot Chassis Design
With the wide range of software options available for robot chassis design, it can be challenging to determine the best tool for a specific project. When selecting software, consider the following factors:
- Project requirements: Evaluate the complexity, scale, and specific needs of your robot chassis design project.
- User experience: Consider your team’s familiarity with different software packages and their learning curves.
- Integration: Assess how well the software integrates with other tools and processes in your workflow.
- Cost: Compare the costs of different software options, including upfront costs, subscription fees, and maintenance expenses.
- Community support: Look for software with active user communities, extensive documentation, and reliable technical support.
Frequently Asked Questions (FAQ)
-
Q: What is the best software for beginners in robot chassis design?
A: For beginners, RobotBuilder or Fusion 360 are good starting points due to their user-friendly interfaces and extensive learning resources. -
Q: Can I design a robot chassis using free software?
A: Yes, there are several free and open-source software options for robot chassis design, such as OpenSCAD and ROS Robot Designer. -
Q: How important is simulation in the robot chassis design process?
A: Simulation is crucial for validating the chassis’ performance, identifying potential issues, and optimizing the design before physical prototyping, saving time and resources. -
Q: Can I use the same software for both design and simulation?
A: Some software packages, like SolidWorks and Fusion 360, offer integrated simulation tools. However, specialized simulation software like ANSYS or Adams may provide more advanced capabilities. -
Q: What should I consider when choosing between different robot chassis design software?
A: When selecting software, consider factors such as project requirements, user experience, integration with other tools, cost, and community support.
Conclusion
Designing a robot chassis is a complex process that requires careful consideration of various factors, from material selection to structural integrity. The use of advanced software tools has revolutionized the way robot chassis are designed, enabling designers to create precise 3D models, perform simulations, and optimize their designs for manufacturing.
CAD software like SolidWorks, Fusion 360, and OpenSCAD offer powerful tools for creating detailed 3D models of robot chassis, while simulation software like ANSYS and Adams allow designers to test and validate their designs under realistic operating conditions. Specialized software like RobotBuilder and ROS Robot Designer provide streamlined workflows and pre-built components for efficient robot chassis design.
When choosing software for robot chassis design, it is essential to consider factors such as project requirements, user experience, integration with other tools, cost, and community support. By selecting the right software and leveraging its capabilities, designers can create robust, efficient, and innovative robot chassis that meet the demands of a wide range of applications.
As the field of robotics continues to evolve, so too will the software tools used for robot chassis design. Designers must stay up-to-date with the latest advancements in software technology and adapt their workflows accordingly to remain competitive and deliver cutting-edge robotic solutions.
No responses yet