Types of SMT Machines
1. Pick and Place Machines
Pick and place machines are the most common type of SMT machine used in electronics manufacturing. These machines are designed to pick up components from feeders and place them accurately onto PCBs. They come in various sizes and configurations, depending on the production volume and component types being used.
1.1 High-Speed Pick and Place Machines
High-speed pick and place machines are designed for high-volume production environments. They feature multiple placement heads and can place thousands of components per hour with exceptional accuracy. These machines are ideal for manufacturers producing large quantities of PCBs with a high component density.
1.2 Flexible Pick and Place Machines
Flexible pick and place machines are designed for small to medium-sized production runs and can handle a wide variety of component types and sizes. These machines often feature interchangeable heads and feeders, allowing for quick changeovers between different PCB designs.
2. Reflow Soldering Machines
Reflow soldering machines are used to permanently attach components to PCBs by melting solder paste applied to the board before component placement. These machines use a controlled heating process to ensure that the solder melts evenly and forms strong connections between the components and the PCB.
2.1 Convection Reflow Soldering Machines
Convection reflow soldering machines use forced hot air to heat the PCB and melt the solder. These machines offer excellent temperature uniformity and are suitable for a wide range of PCB sizes and component types.
2.2 Infrared Reflow Soldering Machines
Infrared reflow soldering machines use infrared radiation to heat the PCB and melt the solder. These machines offer fast heating times and are well-suited for high-volume production environments.
3. Solder Paste Inspection Machines
Solder paste inspection (SPI) machines are used to inspect the quality and consistency of solder paste deposits on PCBs before component placement. These machines use advanced imaging technology to detect any defects or inconsistencies in the solder paste, helping to prevent issues during the reflow soldering process.
4. Automated Optical Inspection Machines
Automated optical inspection (AOI) machines are used to inspect the quality of assembled PCBs after the reflow soldering process. These machines use high-resolution cameras and advanced image processing algorithms to detect any defects or issues with component placement, solder joints, and overall PCB quality.
Features of Excellent SMT Machines
When selecting an SMT machine for your manufacturing needs, there are several key features to consider that distinguish excellent machines from average ones.
1. High Accuracy and Precision
Excellent SMT machines offer high accuracy and precision in component placement and soldering. This ensures that components are placed correctly on the PCB and that solder joints are strong and reliable. Look for machines with advanced vision systems, closed-loop feedback control, and high-resolution positioning systems to achieve the best results.
2. Fast Cycle Times
In high-volume production environments, fast cycle times are essential for maximizing throughput and minimizing production costs. Excellent SMT machines feature optimized motion control systems, high-speed placement heads, and efficient feeder systems to minimize cycle times and increase overall production speed.
3. Flexibility and Adaptability
As product designs and manufacturing requirements evolve, it’s important to have SMT machines that can adapt to changing needs. Excellent machines offer flexibility in terms of component types and sizes, PCB dimensions, and production volumes. Look for machines with interchangeable heads, adjustable feeders, and Modular designs that allow for easy reconfiguration and expansion.
4. User-Friendly Interface and Programming
To maximize efficiency and minimize operator training time, excellent SMT machines feature user-friendly interfaces and intuitive programming tools. Look for machines with touch-screen displays, graphical user interfaces, and built-in libraries of component data and placement algorithms. These features make it easier for operators to set up and run the machine, reducing the risk of errors and improving overall productivity.
5. Robust Construction and Reliability
SMT machines are a significant investment, and it’s essential to choose machines that are built to last. Excellent machines feature robust construction, with high-quality materials and precision-engineered components. They also offer reliable performance, with minimal downtime and low maintenance requirements. Look for machines with proven track records of durability and reliability in demanding production environments.
6. Integration with Other Manufacturing Systems
In modern manufacturing environments, SMT machines are often part of a larger ecosystem of automation and data management systems. Excellent machines offer seamless integration with other manufacturing systems, such as material handling systems, traceability software, and manufacturing execution systems (MES). This integration enables real-time monitoring and control of the production process, as well as data collection and analysis for continuous improvement.
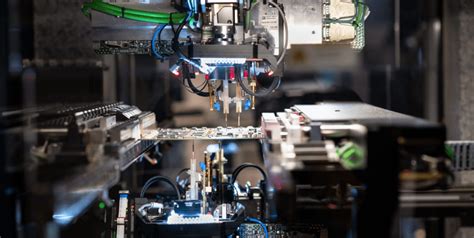
Frequently Asked Questions (FAQ)
1. What is the difference between SMT and through-hole technology?
SMT (Surface Mount Technology) involves placing components directly onto the surface of a PCB, while through-hole technology involves inserting component leads through holes in the PCB and soldering them on the opposite side. SMT allows for smaller component sizes, higher component density, and faster assembly compared to through-hole technology.
2. How do I choose the right SMT machine for my manufacturing needs?
When selecting an SMT machine, consider factors such as your production volume, the types and sizes of components you will be using, the size and complexity of your PCBs, and your budget. Work with a reputable SMT machine supplier to assess your needs and recommend the best machine for your specific requirements.
3. What maintenance is required for SMT machines?
Regular maintenance is essential to ensure the longevity and reliability of your SMT machines. This includes cleaning and lubricating moving parts, replacing worn or damaged components, and calibrating the machine’s vision and positioning systems. Follow the manufacturer’s recommended maintenance schedule and procedures to keep your machines in top condition.
4. Can SMT machines be used for both prototyping and high-volume production?
Yes, there are SMT machines available for both prototyping and high-volume production. For prototyping and low-volume runs, look for flexible machines with quick changeover capabilities and the ability to handle a wide range of component types and sizes. For high-volume production, choose machines with fast cycle times, high accuracy, and the ability to integrate with other automation systems.
5. How can I ensure the quality of my SMT assembly process?
To ensure the quality of your SMT assembly process, implement a comprehensive quality control system that includes regular inspections, testing, and data analysis. Use solder paste inspection (SPI) and automated optical inspection (AOI) machines to detect defects and inconsistencies, and work with your SMT machine supplier to optimize your process parameters for best results. Regularly train your operators and maintain your machines to minimize the risk of errors and ensure consistent, high-quality output.
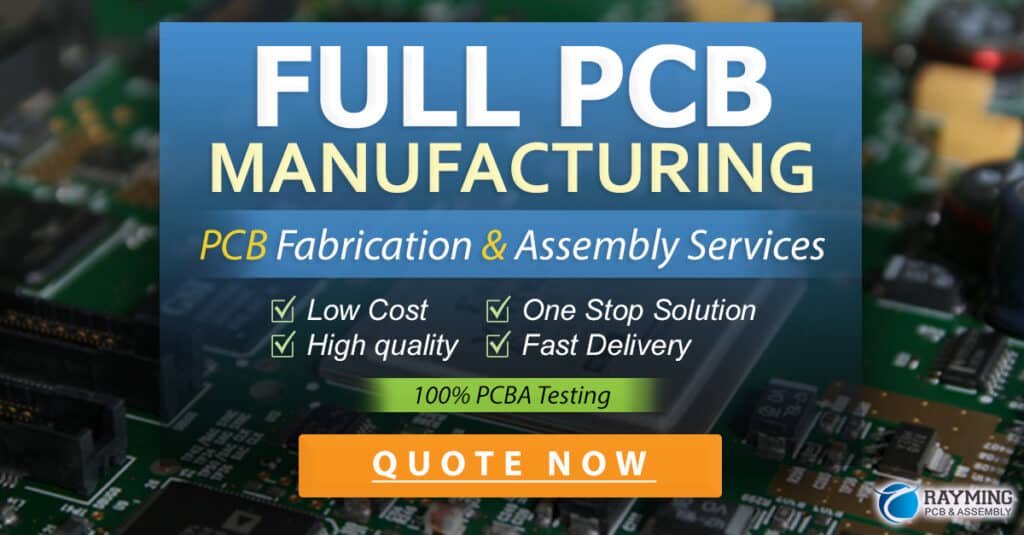
Conclusion
SMT machines are critical tools for businesses looking to streamline their electronics manufacturing processes and improve product quality. By understanding the different types of SMT machines available and the key features that distinguish excellent machines, you can make an informed decision when selecting the best machine for your manufacturing needs. With the right SMT machine and a commitment to quality and continuous improvement, you can take your electronics manufacturing to the next level and stay ahead of the competition.
Machine Type | Key Features | Ideal For |
---|---|---|
High-Speed Pick and Place | – Multiple placement heads – Fast cycle times – High accuracy |
– High-volume production – PCBs with high component density |
Flexible Pick and Place | – Interchangeable heads and feeders – Handles a wide range of component types and sizes |
– Small to medium-sized production runs – Frequent changeovers between PCB designs |
Convection Reflow Soldering | – Uses forced hot air to melt solder – Excellent temperature uniformity |
– Wide range of PCB sizes and component types |
Infrared Reflow Soldering | – Uses infrared radiation to melt solder – Fast heating times |
– High-volume production environments |
Solder Paste Inspection (SPI) | – Inspects quality and consistency of solder paste deposits – Uses advanced imaging technology |
– Preventing issues during reflow soldering process |
Automated Optical Inspection (AOI) | – Inspects quality of assembled PCBs – Uses high-resolution cameras and image processing algorithms |
– Detecting defects or issues with component placement, solder joints, and overall PCB quality |
By carefully considering the types of SMT machines available and the features that make them excellent choices, you can select the best machine for your electronics manufacturing needs and ensure the highest quality and efficiency in your production processes.
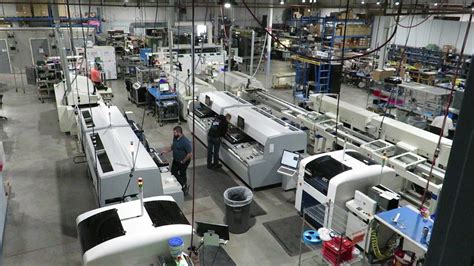
No responses yet