What is SMT Assembly?
SMT assembly is a process in which electronic components are mounted directly onto the surface of a PCB. This is in contrast to through-hole assembly, where component leads are inserted into holes drilled in the PCB and soldered on the opposite side. SMT components are smaller and have shorter leads, allowing for higher component density and smaller PCB sizes.
Advantages of SMT Assembly
SMT assembly offers several advantages over through-hole assembly, including:
- Smaller component sizes
- Higher component density
- Faster assembly speeds
- Lower production costs
- Improved reliability
- Better high-frequency performance
SMT Assembly Process
The SMT assembly process typically involves the following steps:
-
Solder Paste Application: Solder paste, a mixture of tiny solder balls and flux, is applied to the PCB’s pads using a stencil or screen printing process.
-
Component Placement: SMT components are placed onto the solder paste-coated pads using a pick-and-place machine or by hand.
-
Reflow Soldering: The PCB is heated in a reflow oven, causing the solder paste to melt and form a permanent connection between the components and the PCB.
-
Inspection and Testing: The assembled PCB undergoes visual inspection and electrical testing to ensure proper functionality and quality.
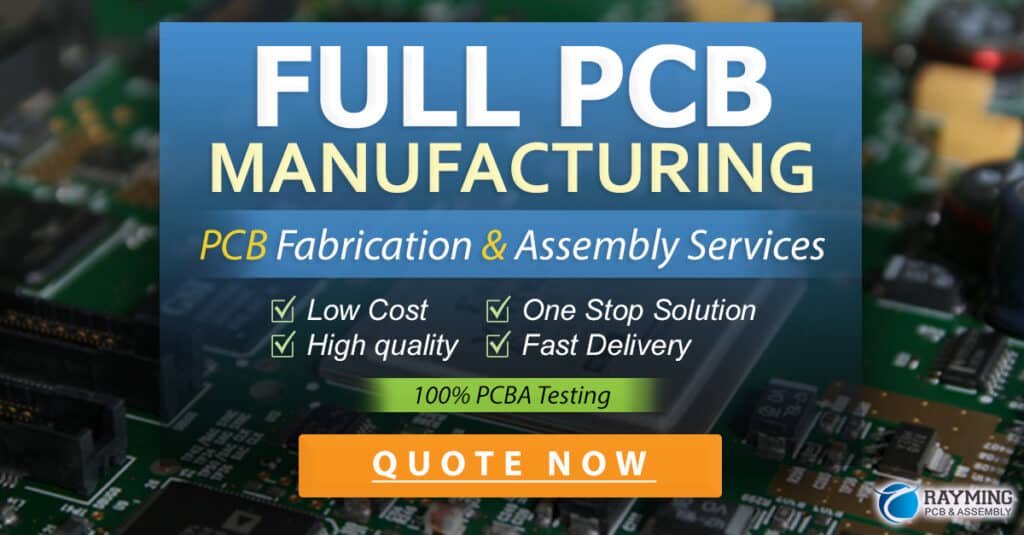
Common SMT Components
SMT components come in various packages, each with its own set of advantages and disadvantages. Some common SMT component packages include:
Package | Description | Advantages | Disadvantages |
---|---|---|---|
Chip | Small, rectangular components with no leads | Low cost, high density | Difficult to handle and place |
SOT | Small-Outline Transistor, a compact package for transistors and diodes | Space-saving, good thermal performance | Limited power handling |
QFP | Quad Flat Pack, a square package with leads on all four sides | High lead count, good thermal performance | Large footprint, more expensive |
BGA | Ball Grid Array, a package with solder balls on the bottom | High lead count, small footprint | Difficult to inspect and rework |
PCB Design Considerations for SMT
When designing a PCB for SMT assembly, several factors must be considered to ensure manufacturability and reliability:
-
Component selection: Choose components that are compatible with SMT assembly and have appropriate package sizes and lead pitches.
-
Pad sizing and spacing: Ensure that component pads are sized and spaced appropriately to accommodate the solder paste and prevent short circuits.
-
Thermal management: Consider the thermal requirements of components and design the PCB to provide adequate heat dissipation.
-
Soldermask and silkscreen: Use soldermask to prevent solder bridging and silkscreen to label components and provide assembly instructions.
Stencil Design and Solder Paste Application
Proper stencil design and solder paste application are critical for successful SMT assembly. The stencil thickness, aperture size, and shape must be carefully chosen based on the component package and pad dimensions. Solder paste should be applied evenly and consistently, with the right amount of paste deposited on each pad.
Pick-and-Place Machine Setup
Pick-and-place machines are used to automatically place SMT components onto the PCB. Proper machine setup is essential for accurate and reliable component placement. The machine’s parameters, such as nozzle size, placement pressure, and placement speed, must be adjusted based on the component package and PCB design.
Reflow Soldering Profile
The reflow soldering profile is a critical factor in SMT assembly, as it determines the quality and reliability of the solder joints. The profile must be carefully designed to ensure that the solder paste melts and flows properly without damaging the components or the PCB. The profile typically includes four stages: preheat, soak, reflow, and cooling.
Inspection and Testing Methods
After SMT assembly, the PCB must undergo thorough inspection and testing to ensure proper functionality and quality. Some common inspection and testing methods include:
-
Visual inspection: Manual or automated visual inspection of the solder joints and component placement.
-
X-ray inspection: Non-destructive inspection of solder joints under BGA and other hidden components.
-
In-circuit testing: Electrical testing of individual components and circuits using a bed-of-nails fixture.
-
Functional testing: Testing the assembled PCB’s overall functionality and performance.
Frequently Asked Questions (FAQ)
1. What is the difference between SMT and through-hole assembly?
SMT components are mounted directly onto the surface of the PCB, while through-hole components have leads that are inserted into holes drilled in the PCB and soldered on the opposite side. SMT allows for smaller components and higher density, while through-hole is more suitable for larger components and higher power applications.
2. Can SMT and through-hole components be used on the same PCB?
Yes, it is possible to use both SMT and through-hole components on the same PCB, a technique known as mixed assembly. However, this may increase the complexity and cost of the assembly process.
3. What are the most common defects in SMT assembly?
Common defects in SMT assembly include solder bridging, tombstoning (when a component stands up on one end), insufficient or excessive solder, and component misalignment.
4. How can I ensure the reliability of SMT assembled PCBs?
To ensure reliability, follow best practices in PCB design, component selection, stencil design, solder paste application, pick-and-place setup, and reflow soldering. Conduct thorough inspection and testing to identify and correct any defects.
5. What is the future of SMT assembly?
As electronic devices continue to become smaller and more complex, SMT assembly will likely continue to evolve. Advances in materials, equipment, and processes, such as 3D printing and flexible electronics, may lead to new opportunities and challenges in SMT assembly.
In conclusion, SMT assembly is a critical process in the production of modern electronic devices. By understanding the key aspects of SMT assembly, from component selection and PCB design to inspection and testing, engineers and manufacturers can ensure the quality, reliability, and performance of their products.
No responses yet