What is a Single Layer PCB?
A single layer PCB, also known as a single-sided PCB, is a printed circuit board that has conductive copper traces on only one side of the board. The other side of the board is typically left bare or covered with a solder mask to protect the copper traces from oxidation and short circuits.
Single layer PCBs are the simplest and most basic type of PCB. They are commonly used in low-complexity electronic devices, such as:
- Simple consumer electronics (e.g. toys, calculators, remote controls)
- Low-power and low-frequency applications
- Prototypes and hobbyist projects
- Educational and training purposes
Despite their simplicity, single layer PCBs can still be used to create functional and reliable electronic circuits. They offer several advantages over more complex multi-layer PCBs, including:
- Lower cost and faster production times
- Easier to design and manufacture
- More accessible for beginners and hobbyists
- Suitable for low-density layouts and larger components
However, single layer PCBs also have some limitations compared to multi-layer PCBs, such as:
- Limited routing options and circuit complexity
- Higher susceptibility to electromagnetic interference (EMI)
- Lower power and signal integrity
- Difficulty in achieving high-density layouts
In the following sections, we will explore the design, fabrication, and applications of single layer PCBs in more detail.
How are Single Layer PCBs Made?
The manufacturing process for single layer PCBs involves several steps, including:
-
Design: The first step is to create a schematic diagram and PCB layout using CAD software. The design must follow the design rules and guidelines for single layer PCBs, such as minimum trace width, spacing, and hole size.
-
PCB Fabrication: Once the design is finalized, the PCB fabrication process begins. The most common methods for fabricating single layer PCBs are:
-
Etching: The copper-clad board is coated with a photoresist layer, which is then exposed to UV light through a photomask containing the PCB layout. The unexposed areas of the photoresist are removed, exposing the copper to be etched away by a chemical solution, leaving only the desired copper traces.
-
Milling: A CNC machine is used to mechanically remove the unwanted copper from the board, leaving only the desired traces. This method is suitable for low-volume production and prototyping.
-
Drilling: Holes are drilled through the board to accommodate through-hole components and vias. The holes are typically drilled using a CNC machine or a drill press.
-
Solder Mask Application: A solder mask layer is applied to the PCB to protect the copper traces from oxidation and prevent solder bridging. The solder mask is typically green in color but can also be red, blue, or black.
-
Silkscreen Printing: A silkscreen layer is printed on the PCB to add text, logos, and component identifiers. The silkscreen is typically white in color but can also be black or yellow.
-
Surface Finish: A surface finish, such as HASL (Hot Air Solder Leveling), ENIG (Electroless Nickel Immersion Gold), or OSP (Organic Solderability Preservative), is applied to the exposed copper to prevent oxidation and improve solderability.
-
Testing and Inspection: The finished PCB undergoes various tests and inspections to ensure its quality and functionality, such as visual inspection, continuity testing, and electrical testing.
The entire manufacturing process for single layer PCBs can be completed in a matter of days, depending on the complexity of the design and the volume of production.
Design Considerations for Single Layer PCBs
Designing a single layer PCB requires careful consideration of several factors to ensure optimal performance and manufacturability. Some of the key design considerations for single layer PCBs include:
Component Placement
Component placement is critical in single layer PCB design, as it affects the routing of traces and the overall board size. When placing components on a single layer PCB, designers should consider the following:
- Group related components together to minimize trace lengths and reduce EMI
- Place larger components first, followed by smaller components
- Avoid placing components too close to the board edges or mounting holes
- Consider the orientation of components for easier soldering and assembly
- Leave enough space between components for routing traces and vias
Trace Routing
Routing traces on a single layer PCB can be challenging, as there is only one conductive layer available. Designers must carefully plan the trace routing to ensure signal integrity and avoid interference. Some tips for routing traces on a single layer PCB include:
- Use wider traces for power and ground connections to reduce resistance and improve current carrying capacity
- Use thinner traces for signal connections to reduce capacitance and improve signal integrity
- Avoid sharp angles or sudden changes in trace direction, which can cause reflections and signal degradation
- Use vias sparingly, as they can add cost and complexity to the board
- Follow the manufacturer’s design rules and guidelines for minimum trace width, spacing, and clearance
Power and Ground Distribution
Proper power and ground distribution is essential for the reliable operation of a single layer PCB. Designers should consider the following when designing power and ground distribution:
- Use separate power and ground planes or traces to reduce noise and improve signal integrity
- Use decoupling capacitors near power-hungry components to reduce voltage fluctuations and noise
- Use star or grid topology for power and ground distribution to minimize voltage drops and ensure even distribution
- Use wide traces or copper pours for power and ground connections to reduce resistance and improve current carrying capacity
EMI and Noise Reduction
Single layer PCBs are more susceptible to electromagnetic interference (EMI) and noise compared to multi-layer PCBs. Designers can use various techniques to reduce EMI and noise, such as:
- Keeping signal traces as short as possible to minimize antenna effects
- Avoiding long parallel traces, which can cause crosstalk and interference
- Using ground planes or traces to shield sensitive signals from EMI
- Using filters, ferrites, or shielding components to suppress high-frequency noise
- Following good grounding and shielding practices, such as using shielded cables and connectors
Design Tools and Software
There are various CAD tools and software available for designing single layer PCBs, ranging from simple and free to complex and expensive. Some of the popular PCB design software include:
- KiCad: A free and open-source PCB design suite that supports schematic capture, PCB layout, and 3D visualization
- Eagle: A popular PCB design software that offers a free version for non-commercial use and a paid version for professional use
- Altium Designer: A high-end PCB design software that offers advanced features and integration with mechanical CAD tools
- OrCAD: A comprehensive PCB design solution that includes schematic capture, simulation, and PCB layout tools
Designers should choose the software that best suits their needs and budget, and invest time in learning the software’s features and capabilities.
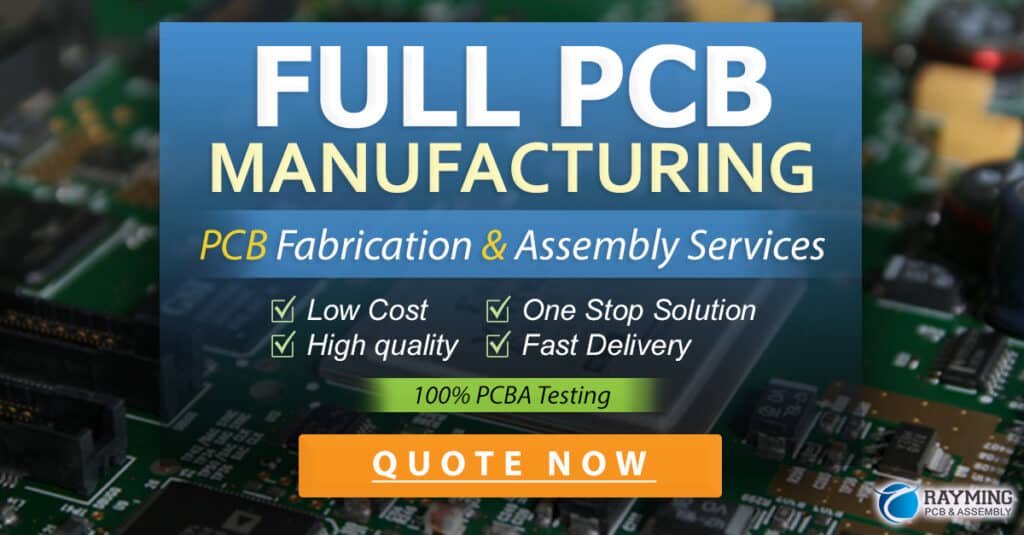
Assembly and Soldering Techniques for Single Layer PCBs
Once the single layer PCB is fabricated, the next step is to assemble and solder the components onto the board. There are two main methods for assembling single layer PCBs:
Through-Hole Assembly
Through-hole assembly involves inserting the component leads through the holes in the PCB and soldering them to the copper pads on the other side of the board. This method is suitable for larger components, such as resistors, capacitors, and connectors, and is easier for manual soldering.
To solder through-hole components, follow these steps:
- Insert the component leads through the holes in the PCB, ensuring that the component is seated firmly against the board.
- Bend the leads slightly outward to hold the component in place.
- Apply a small amount of solder to the tip of the soldering iron.
- Touch the soldering iron to the pad and the lead simultaneously, allowing the solder to flow and form a joint.
- Remove the soldering iron and let the joint cool for a few seconds.
- Trim the excess leads with wire cutters.
Surface Mount Assembly
Surface mount assembly involves soldering the components directly onto the copper pads on the PCB, without the need for holes. This method is suitable for smaller components, such as resistors, capacitors, and ICs, and allows for higher component density and faster assembly.
To solder surface-mount components, follow these steps:
- Apply a small amount of solder paste to the pads on the PCB using a stencil or syringe.
- Place the components onto the pads, ensuring that they are aligned correctly.
- Heat the board and components using a reflow oven or hot air gun, allowing the solder paste to melt and form a joint.
- Let the board cool for a few seconds, and inspect the joints for any defects or misalignments.
Soldering Tools and Equipment
To solder single layer PCBs efficiently and reliably, it is essential to have the right tools and equipment. Some of the essential soldering tools include:
- Soldering iron: A temperature-controlled soldering iron with a fine tip is recommended for precise soldering.
- Solder wire: Use a high-quality solder wire with a suitable diameter and alloy composition for the application.
- Solder paste: Use a solder paste with a suitable particle size and flux type for surface mount assembly.
- Flux: Use a flux to remove oxides and improve solderability, either in the form of a paste or a pen.
- Tweezers: Use tweezers to handle and place small components accurately.
- Wire cutters: Use wire cutters to trim the excess leads after soldering.
- Solder wick: Use a solder wick to remove excess solder or rework faulty joints.
- Magnifying glass or microscope: Use a magnifying glass or microscope to inspect the solder joints for any defects or anomalies.
Testing and Debugging Single Layer PCBs
After assembling the single layer PCB, it is crucial to test and debug the board to ensure its functionality and reliability. There are several techniques and tools for testing and debugging single layer PCBs, including:
Visual Inspection
The first step in testing a single layer PCB is to perform a visual inspection of the board and components. Look for any obvious defects, such as:
- Misaligned or missing components
- Solder bridges or shorts
- Cold or incomplete solder joints
- Damaged or lifted pads or traces
- Incorrect component values or orientations
Use a magnifying glass or microscope to inspect the solder joints and traces closely, and rework any defects as necessary.
Continuity Testing
Continuity testing involves checking the electrical connectivity between various points on the PCB, such as pads, traces, and vias. Use a multimeter or a dedicated continuity tester to perform continuity testing, following these steps:
- Set the multimeter to the continuity or resistance mode.
- Touch one probe to a pad or trace, and the other probe to another pad or trace that should be connected.
- If the multimeter beeps or shows a low resistance, the connection is good. If not, there may be an open circuit or a high resistance.
- Repeat the test for all the critical connections on the board, referring to the schematic diagram and PCB layout.
Power-On Testing
Power-on testing involves applying power to the PCB and measuring the voltage levels at various points on the board. Use a multimeter or an oscilloscope to perform power-on testing, following these steps:
- Double-check the power supply connections and polarity before applying power.
- Apply power to the board and measure the voltage levels at the power input, voltage regulators, and other critical points.
- Compare the measured voltages with the expected values from the schematic diagram and datasheets.
- If the voltages are incorrect or unstable, there may be a short circuit, an open circuit, or a faulty component.
Functional Testing
Functional testing involves verifying that the PCB performs its intended function, such as generating signals, processing data, or controlling external devices. Use a variety of test equipment and techniques, depending on the specific application and requirements, such as:
- Logic analyzers: To capture and analyze digital signals and buses
- Oscilloscopes: To measure and display analog signals and waveforms
- Signal generators: To inject test signals and patterns into the board
- Spectrum analyzers: To measure the frequency and amplitude of signals and noise
- Software debuggers: To monitor and control the firmware and software running on the board
Compare the measured results with the expected results from the design specifications and test plans, and debug any discrepancies or anomalies.
Applications and Examples of Single Layer PCBs
Single layer PCBs are used in a wide range of applications, from simple consumer electronics to complex industrial systems. Some of the common applications and examples of single layer PCBs include:
Consumer Electronics
- Remote controls
- Calculators
- Toys and games
- LED lighting
- Battery chargers
Industrial Controls
- Sensors and transducers
- Relays and switches
- Motor controllers
- Power supplies
- HVAC systems
Automotive Electronics
- Dashboard instruments
- Lighting controls
- Infotainment systems
- Keyless entry systems
- Parking sensors
Medical Devices
- Glucometers
- Blood pressure monitors
- Pulse oximeters
- Thermometers
- Hearing aids
IoT and Wearables
- Fitness trackers
- Smartwatches
- Beacons and tags
- Sensors and actuators
- Wireless modules
In each of these applications, single layer PCBs offer a cost-effective and reliable solution for implementing the electronic circuits and functions. However, the specific design and manufacturing requirements may vary depending on the application, such as:
- Environmental conditions (temperature, humidity, vibration, etc.)
- Power and voltage levels
- Signal frequencies and bandwidths
- Size and form factor constraints
- Regulatory and safety standards
Designers must carefully consider these requirements and choose the appropriate components, materials, and manufacturing processes for each application.
FAQs
Q1: What is the difference between a single layer PCB and a double layer PCB?
A: A single layer PCB has copper traces on only one side of the board, while a double layer PCB has copper traces on both sides of the board. Double layer PCBs offer more routing options and higher component density, but are more expensive and complex to manufacture than single layer PCBs.
Q2: Can single layer PCBs have through-hole components?
A: Yes, single layer PCBs can have through-hole components, such as resistors, capacitors, and connectors. The component leads are inserted through the holes in the board and soldered to the copper pads on the other side.
Q3: What is the minimum trace width and spacing for single layer PCBs?
A: The minimum trace width and spacing for single layer PCBs depend on the manufacturing process and the design rules of the PCB fabricator. Typically, the minimum trace width is 0.2-0.3 mm, and the minimum spacing between traces is 0.2-0.3 mm. However, these values may vary depending on the specific application and requirements.
Q4: How can I reduce EMI and noise in single layer PCBs?
A: There are several techniques for reducing EMI and noise in single layer PCBs, such as:
- Keeping signal traces as short as possible
- Avoiding long parallel traces
- Using ground planes or traces to shield sensitive signals
- Using filters, ferrites, or shielding components
- Following good grounding and shielding practices
Q5: What are the typical lead times and costs for manufacturing single layer PCBs?
A: The lead times and costs for manufacturing single layer PCBs depend on the complexity of the design, the quantity of boards, and the specific requirements of the application. Typically, the lead times for single layer PCBs are shorter than for multi-layer PCBs, ranging from a few days to a few weeks. The costs for single layer PCBs are also lower than for multi-layer PCBs, but may vary depending on the size, material, and finish of the board. It is recommended to get quotes from multiple PCB fabricators and compare the prices and lead times before placing an order.
Conclusion
Single layer PCBs are a fundamental building block of electronic circuits, offering a simple and cost-effective solution for a wide range of applications. By understanding the design, fabrication, assembly, and testing techniques for single layer PCBs, designers and engineers can create reliable and functional electronic products that meet the specific requirements of each application.
However, single layer PCBs also have some limitations and challenges, such as limited routing options, higher susceptibility to EMI and noise, and lower power and signal integrity compared to multi-layer PCBs. Designers must carefully consider these factors and choose the appropriate design strategies and components to optimize the performance and reliability of single layer PCBs.
As technology advances and electronic devices become more complex and miniaturized, the role of single layer PCBs may evolve and adapt to new applications and requirements. However, the fundamental principles and techniques for designing and manufacturing single layer PCBs will remain relevant and essential for the foreseeable future.
No responses yet