What is a Single-Layer PCB?
A Single-Layer PCB, also known as a single-sided PCB, is a printed circuit board that has conductive copper traces on only one side of the board. The other side of the board is usually left bare or covered with a solder mask to protect the copper traces from oxidation and short circuits.
Single-Layer PCBs are the simplest and most cost-effective type of PCB available. They are typically used for low-density designs with few components and simple routing requirements. Some common applications of Single-Layer PCBs include:
- Simple electronic devices such as calculators, remote controls, and toys
- Prototyping and testing of new designs
- Educational projects and hobbyist circuits
- Low-volume production runs
Advantages of Single-Layer PCBs
Cost-Effective
Single-Layer PCBs are the most affordable type of PCB available. They require less material, fewer manufacturing steps, and simpler equipment compared to multi-layer PCBs. This makes them an ideal choice for low-budget projects and small-scale production runs.
Quick Turnaround Time
Due to their simplicity, Single-Layer PCBs can be manufactured much faster than multi-layer PCBs. The design and fabrication process is straightforward, and there are fewer opportunities for errors or defects. This means that you can get your boards back from the manufacturer in a matter of days, rather than weeks or months.
Easy to Design
Single-Layer PCBs have a simple and intuitive design process. There is only one layer of copper traces to worry about, so you don’t need to deal with complex routing algorithms or via placement. This makes them a great choice for beginners who are just starting out with PCB design.
Suitable for Low-Density Designs
If your circuit has a low component count and simple routing requirements, a Single-Layer PCB is often the best choice. There is no need to use a more complex and expensive multi-layer board if a single layer can accommodate all of your components and traces.
Disadvantages of Single-Layer PCBs
Limited Routing Options
With only one layer of copper traces available, Single-Layer PCBs have limited routing options compared to multi-layer boards. This can make it challenging to route complex circuits or high-density designs. Jumper wires may be necessary to cross over traces, which can add to the assembly time and cost.
Susceptible to Noise and Interference
Single-Layer PCBs are more susceptible to electromagnetic interference (EMI) and crosstalk compared to multi-layer boards. This is because there is no ground plane or power plane to shield the traces from external noise sources. Careful design and layout techniques can help mitigate these issues, but they may still be a concern for sensitive or high-speed circuits.
Not Suitable for High-Density Designs
If your circuit has a high component count or complex routing requirements, a Single-Layer PCB may not be sufficient. The limited space and routing options can make it difficult or impossible to fit all of the necessary components and traces on a single layer. In these cases, a multi-layer PCB may be necessary to achieve the desired functionality and performance.
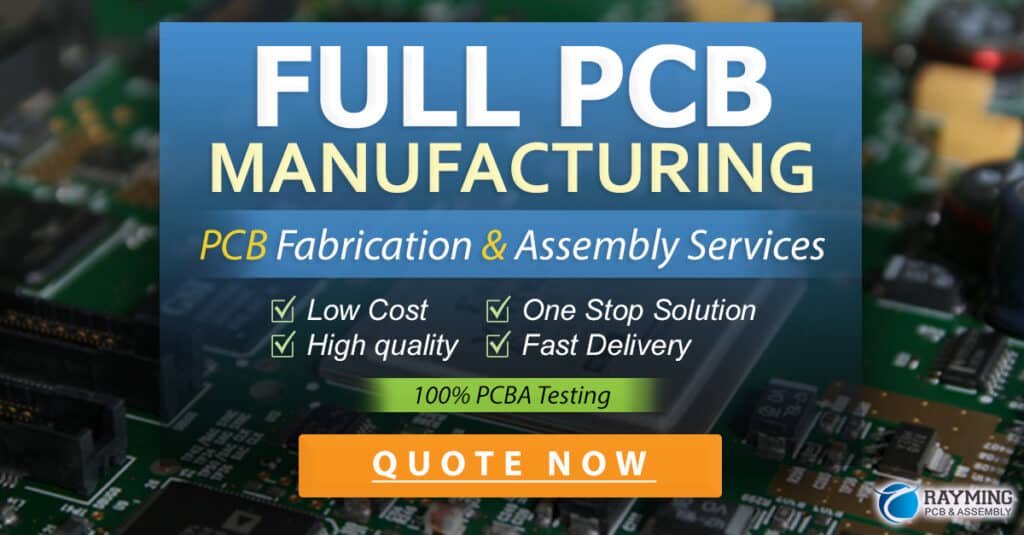
Designing a Single-Layer PCB
Schematic Design
The first step in designing a Single-Layer PCB is to create a schematic of your circuit. This is a graphical representation of the components and their connections, using standard symbols and notations. There are many software tools available for schematic design, such as KiCad, Eagle, and Altium Designer.
When creating your schematic, keep in mind the limitations of a Single-Layer PCB. Avoid using too many components or complex routing paths that may be difficult to implement on a single layer. Use jumper wires sparingly, as they can add to the assembly time and cost.
Board Layout
Once your schematic is complete, the next step is to create a board layout. This involves placing the components on the board and routing the copper traces between them. Again, there are many software tools available for board layout, often integrated with the schematic design tools.
When laying out your board, keep the following tips in mind:
- Place components strategically to minimize the length and complexity of traces
- Use a grid system to ensure proper alignment and spacing of components and traces
- Keep traces as short and straight as possible to minimize resistance and inductance
- Avoid crossing traces if possible, or use jumper wires if necessary
- Provide adequate clearance between traces and components to avoid short circuits
- Use a consistent trace width and spacing to ensure manufacturability and reliability
Design Rule Check
Before sending your board design to the manufacturer, it is important to perform a design rule check (DRC). This is an automated process that checks your design against a set of predefined rules and constraints, such as minimum trace width, clearance, and hole size.
Most PCB design software includes a built-in DRC tool that can identify potential issues and suggest fixes. It is important to carefully review and address any DRC errors or warnings before proceeding with manufacturing, as they can lead to functional or reliability issues down the line.
Manufacturing a Single-Layer PCB
PCB Fabrication
Once your design is complete and has passed the DRC, it is time to send it to a PCB manufacturer for fabrication. There are many PCB fabrication services available, ranging from small-scale prototyping shops to large-scale production facilities.
When selecting a PCB fabricator, consider the following factors:
- Turnaround time and cost
- Minimum order quantity and panel size
- Supported materials and finishes
- Quality control and testing procedures
- Customer support and communication
Most PCB fabricators will require you to provide your design files in a standard format, such as Gerber or ODB++. They may also provide a set of design guidelines and specifications to ensure that your board meets their manufacturing capabilities and requirements.
PCB Assembly
After your boards have been fabricated, the next step is to assemble the components onto them. This can be done manually by hand, or automatically using pick-and-place machines and reflow ovens.
For Single-Layer PCBs, manual assembly is often the most cost-effective option, especially for low-volume production runs. However, it can be time-consuming and prone to human error, so careful planning and quality control measures are necessary.
If you choose to use an automated assembly service, make sure to provide them with a comprehensive bill of materials (BOM) and assembly instructions. This will ensure that the correct components are placed in the correct locations and orientations on the board.
Testing and Debugging a Single-Layer PCB
Visual Inspection
Once your boards have been assembled, the first step in testing and debugging is to perform a visual inspection. This involves carefully examining the board for any visible defects or issues, such as:
- Misaligned or missing components
- Solder bridges or short circuits
- Damaged or lifted traces
- Incomplete or excessive solder joints
A magnifying glass or microscope can be helpful for identifying small defects that may not be visible to the naked eye. If any issues are found, they should be corrected before proceeding with further testing.
Continuity Testing
The next step is to perform a continuity test to ensure that all of the necessary connections are present and intact. This can be done using a multimeter or a dedicated continuity tester.
To perform a continuity test, simply touch the probes of the tester to the two points that you want to test. If there is a continuous electrical path between the two points, the tester will indicate a low resistance or a closed circuit. If there is no continuity, the tester will indicate an open circuit or high resistance.
It is important to test all of the critical connections on the board, such as power and ground pins, signal traces, and component leads. Any open or short circuits should be investigated and repaired before proceeding.
Functional Testing
The final step in testing and debugging a Single-Layer PCB is to perform a functional test to ensure that the board is performing as expected. This involves applying power to the board and measuring the output signals or behaviors of the various components.
Functional testing can be performed using a variety of tools and techniques, depending on the specific requirements of the board. Some common methods include:
- Oscilloscope measurements of signal waveforms and timing
- Logic analyzer captures of digital data streams
- Current and voltage measurements using a multimeter or power supply
- Thermal imaging to identify hot spots or thermal issues
- Automated test equipment (ATE) for high-volume production testing
Any discrepancies or anomalies in the functional test results should be carefully investigated and debugged. This may involve checking component values, tracing signal paths, or modifying the board design if necessary.
FAQs
Q: What is the maximum size of a Single-Layer PCB?
A: The maximum size of a Single-Layer PCB is typically limited by the size of the manufacturing equipment and the panel size used by the PCB fabricator. Most fabricators can accommodate boards up to 18 inches by 24 inches, although larger sizes may be possible with specialized equipment.
Q: Can I use surface-mount components on a Single-Layer PCB?
A: Yes, surface-mount components can be used on Single-Layer PCBs, although they may require more careful placement and routing compared to through-hole components. SMD components are typically smaller and have a lower profile, which can help to reduce the overall size and thickness of the board.
Q: How much does it cost to manufacture a Single-Layer PCB?
A: The cost of manufacturing a Single-Layer PCB depends on a variety of factors, such as the size and complexity of the board, the number of boards ordered, and the specific fabrication and assembly services required. In general, small-scale prototyping runs can cost anywhere from $50 to $500, while larger production runs can cost several thousand dollars or more.
Q: What is the typical turnaround time for a Single-Layer PCB?
A: The turnaround time for a Single-Layer PCB depends on the specific fabrication and assembly services used, as well as the complexity and quantity of the boards ordered. In general, small-scale prototyping runs can be completed in 1-2 weeks, while larger production runs may take several weeks or months.
Q: Can I design and manufacture a Single-Layer PCB myself?
A: Yes, it is possible to design and manufacture a Single-Layer PCB yourself, although it requires some specialized knowledge and equipment. There are many online resources and tutorials available for learning PCB design and fabrication, as well as DIY fabrication methods such as etching and milling. However, for most commercial and industrial applications, it is recommended to use a professional PCB fabrication and assembly service to ensure the highest quality and reliability.
Parameter | Value |
---|---|
Number of Layers | 1 |
Material | FR-4 |
Thickness | 1.6 mm |
Copper Weight | 1 oz |
Minimum Trace Width | 0.2 mm |
Minimum Clearance | 0.2 mm |
Minimum Hole Size | 0.3 mm |
Solder Mask | Green |
Silkscreen | White |
Surface Finish | HASL |
Table 1: Example specifications for a Single-Layer PCB
Conclusion
Single-Layer PCBs are a simple and cost-effective solution for low-density electronic designs. They offer several advantages over multi-layer boards, such as lower cost, faster turnaround time, and easier design and assembly. However, they also have some limitations, such as limited routing options and susceptibility to noise and interference.
When designing a Single-Layer PCB, it is important to carefully consider the schematic design, board layout, and design rule checks to ensure a manufacturable and reliable board. Proper testing and debugging techniques, such as visual inspection, continuity testing, and functional testing, are also essential for identifying and resolving any issues before final production.
Overall, Single-Layer PCBs are a valuable tool in the electronics designer’s toolkit, offering a simple and affordable way to bring low-complexity designs to life. With careful planning and execution, they can provide reliable and cost-effective solutions for a wide range of applications.
No responses yet