Introduction to Backplane Simulations
In modern electronic systems, backplanes play a crucial role in interconnecting various components and enabling high-speed data transmission. As the demand for faster data rates and higher bandwidths continues to grow, ensuring signal integrity in backplane bus connectors becomes increasingly critical. Backplane simulations are essential tools for analyzing and optimizing the performance of these interconnects, allowing designers to identify and mitigate potential signal integrity issues before the physical implementation of the system.
What are Backplane Bus Connectors?
Backplane bus connectors are specialized connectors used to interface printed circuit boards (PCBs) with a backplane in an electronic system. These connectors are designed to handle high-speed signals and provide reliable connections between the PCBs and the backplane. They come in various form factors and configurations, such as press-fit, surface mount, and edge connectors, each with their own advantages and considerations for signal integrity.
Importance of Signal Integrity in Backplanes
Signal integrity is a critical aspect of backplane design, as it directly impacts the reliability and performance of the entire electronic system. Poor signal integrity can lead to issues such as signal distortion, crosstalk, reflections, and jitter, which can compromise the functionality and stability of the system. By conducting thorough backplane simulations, designers can identify and address these issues early in the design process, ensuring optimal signal quality and system performance.
Backplane Simulation Techniques
Time-Domain Simulations
Time-domain simulations are widely used in backplane analysis to evaluate the transient response of the system. These simulations involve solving the governing equations of the interconnect in the time domain, allowing designers to observe the waveforms and assess the signal integrity at various points along the backplane. Time-domain simulations can help identify issues such as overshoot, undershoot, ringing, and eye closure, providing valuable insights into the system’s performance.
Frequency-Domain Simulations
Frequency-domain simulations are another important technique in backplane analysis, particularly for evaluating the frequency response and transfer characteristics of the interconnect. These simulations involve transforming the time-domain equations into the frequency domain using techniques such as Fourier analysis. By examining the frequency response, designers can identify resonances, impedance mismatches, and bandwidth limitations, enabling them to optimize the backplane design for the desired frequency range.
3D Electromagnetic Simulations
As backplane designs become more complex and high-speed, 3D electromagnetic (EM) simulations become increasingly important for accurate signal integrity analysis. These simulations solve Maxwell’s equations in three dimensions, taking into account the geometrical and material properties of the backplane and connectors. 3D EM simulations can provide detailed insights into the electromagnetic fields, current distributions, and coupling effects, allowing designers to identify and mitigate issues such as crosstalk, radiation, and mode conversion.
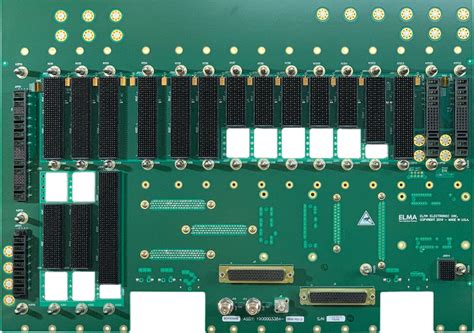
Backplane Simulation Parameters
Transmission Line Characteristics
Transmission line characteristics are fundamental parameters in backplane simulations, as they describe the electrical properties of the interconnect. These characteristics include impedance, propagation delay, attenuation, and velocity of propagation. Accurate modeling of transmission line characteristics is essential for predicting the signal behavior and identifying potential impedance mismatches or discontinuities along the backplane.
Parameter | Description | Typical Values |
---|---|---|
Impedance | The ratio of voltage to current in a transmission line | 50 Ω, 75 Ω, 100 Ω |
Propagation Delay | The time taken for a signal to travel from one end of the line to the other | ps/mm, ps/inch |
Attenuation | The reduction in signal amplitude as it propagates along the line | dB/mm, dB/inch |
Velocity of Propagation | The speed at which a signal travels along the transmission line | m/s, % of speed of light |
Material Properties
The material properties of the backplane and connectors play a significant role in signal integrity performance. These properties include dielectric constant, loss tangent, and conductivity. Accurate modeling of material properties is necessary to capture the frequency-dependent losses and dispersion effects in the backplane. Designers often use material libraries or measured data to incorporate realistic material properties into their simulations.
Material | Dielectric Constant | Loss Tangent | Conductivity (S/m) |
---|---|---|---|
FR-4 | 4.3 – 4.7 | 0.02 – 0.03 | N/A |
Rogers 4003C | 3.38 | 0.0027 | N/A |
Copper | N/A | N/A | 5.8 × 10^7 |
Connector Models
Connector models are essential components of backplane simulations, as they represent the interface between the PCBs and the backplane. Accurate modeling of connectors requires capturing their geometry, pin assignments, and electrical characteristics. Connector manufacturers often provide SPICE or IBIS models that can be integrated into backplane simulations. These models include parameters such as pin capacitance, inductance, and resistance, as well as crosstalk and reflection coefficients.
Signal Integrity Metrics
Signal integrity metrics are used to quantify the quality of the signals in the backplane and assess the overall performance of the system. Common signal integrity metrics include:
- Eye Diagram: A graphical representation of the superimposed waveforms, showing the opening of the eye pattern and indicating the signal quality and timing margin.
- Bit Error Rate (BER): The ratio of the number of erroneous bits to the total number of bits transmitted, indicating the reliability of the communication link.
- Jitter: The variation in the timing of the signal transitions, which can impact the sampling point and lead to data errors.
- Crosstalk: The unwanted coupling of signals between adjacent traces or pins, which can cause interference and degrade signal quality.
By evaluating these metrics through backplane simulations, designers can assess the overall signal integrity performance and make informed decisions about design optimizations.
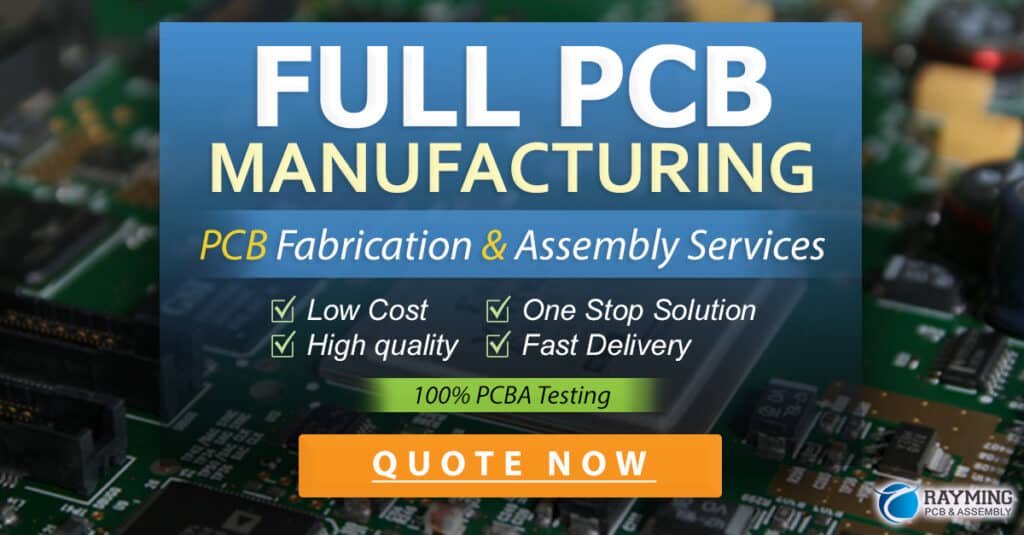
Backplane Simulation Workflow
Pre-Layout Simulations
Pre-layout simulations are conducted in the early stages of backplane design, before the physical layout is finalized. These simulations are based on schematic-level models and ideal transmission line representations. Pre-layout simulations allow designers to explore different architectures, evaluate the impact of design parameters, and identify potential signal integrity issues early in the design process. They provide a quick and efficient way to iterate on the design and optimize the system performance.
Post-Layout Simulations
Post-layout simulations are performed after the physical layout of the backplane is complete. These simulations incorporate the actual geometry, routing, and material properties of the backplane, providing a more accurate representation of the system. Post-layout simulations enable designers to assess the impact of layout-related effects, such as crosstalk, reflections, and losses, on the signal integrity performance. They help identify and resolve any issues that may have arisen during the layout process and validate the final design before manufacturing.
Simulation Tools and Methodologies
There are various simulation tools and methodologies available for backplane simulations, each with their own strengths and capabilities. Some commonly used tools include:
- SPICE: A widely used circuit simulation tool that can model the electrical behavior of interconnects and components.
- IBIS: A behavioral modeling standard that captures the input/output characteristics of devices and enables system-level simulations.
- 3D EM Simulators: Tools that solve Maxwell’s equations in three dimensions, such as Ansys HFSS, Keysight EMPro, and CST Studio Suite.
- Channel Modeling Tools: Specialized tools for modeling and analyzing high-speed channels, such as Keysight ADS and Cadence Sigrity.
Designers often use a combination of these tools and methodologies to conduct comprehensive backplane simulations and ensure the signal integrity of the system.
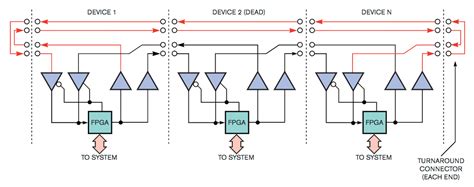
Best Practices for Backplane Simulations
Model Accuracy and Validation
Ensuring the accuracy of the models used in backplane simulations is crucial for obtaining reliable results. This involves validating the models against measured data or reference designs to assess their fidelity. Designers should use accurate material properties, connector models, and device models to capture the real-world behavior of the system. Regular model updates and calibration against hardware measurements can help maintain the accuracy of the simulations.
Simulation Boundaries and Termination
Defining appropriate simulation boundaries and termination conditions is important for accurate backplane simulations. Designers should consider the extent of the simulation domain, including the relevant portions of the PCBs and connectors. Proper termination of transmission lines, such as matched impedance or source termination, should be applied to avoid reflections and ensure accurate signal propagation. Boundary conditions, such as port impedances and loads, should be carefully defined to represent the actual system environment.
Parametric Studies and Optimization
Parametric studies involve varying design parameters and observing their impact on the signal integrity performance. By conducting parametric studies, designers can identify the sensitivity of the system to different variables and optimize the design for robustness. Optimization techniques, such as genetic algorithms or gradient-based methods, can be employed to find the optimal combination of design parameters that meet the signal integrity requirements. Parametric studies and optimization help designers make informed decisions and achieve the best possible system performance.
Collaboration and Documentation
Effective collaboration among team members is essential for successful backplane simulations. Designers should establish clear communication channels and share simulation results, models, and assumptions with relevant stakeholders. Regular design reviews and cross-functional meetings can help align the simulation efforts with the overall project goals. Comprehensive documentation of the simulation setup, assumptions, and results is crucial for maintaining traceability and facilitating future reference. Well-documented simulations also enable easier maintenance and updates as the design evolves.
Conclusion
Backplane simulations are indispensable tools for ensuring signal integrity in high-speed electronic systems. By leveraging various simulation techniques, such as time-domain, frequency-domain, and 3D EM simulations, designers can analyze and optimize the performance of backplane bus connectors. Accurate modeling of transmission line characteristics, material properties, and connector models is essential for reliable simulations. Signal integrity metrics, such as eye diagrams, BER, jitter, and crosstalk, provide quantitative measures of the system’s performance.
A well-defined simulation workflow, including pre-layout and post-layout simulations, helps identify and resolve signal integrity issues at different stages of the design process. Best practices, such as model accuracy, simulation boundaries, parametric studies, and collaboration, contribute to the effectiveness and reliability of backplane simulations.
As data rates continue to increase and systems become more complex, the importance of backplane simulations in ensuring signal integrity cannot be overstated. By investing in robust simulation methodologies and tools, designers can mitigate risks, optimize performance, and deliver reliable and high-quality electronic systems.
Frequently Asked Questions (FAQ)
-
Q: What are the main challenges in backplane simulations for high-speed systems?
A: The main challenges in backplane simulations for high-speed systems include modeling accuracy, capturing frequency-dependent effects, managing simulation complexity, and ensuring reliable results. As data rates increase, the impact of signal integrity issues becomes more significant, requiring careful consideration of transmission line effects, material properties, and connector behavior. -
Q: How do I choose the appropriate simulation tool for my backplane design?
A: The choice of simulation tool depends on various factors, such as the complexity of the design, the required accuracy, the available resources, and the designer’s familiarity with the tool. It is important to consider the specific features and capabilities of each tool, such as support for different simulation domains, model formats, and integration with other design tools. Evaluating the tool’s performance, ease of use, and customer support can also help in making an informed decision. -
Q: What are the key parameters to consider when modeling connectors in backplane simulations?
A: When modeling connectors in backplane simulations, the key parameters to consider include pin assignments, electrical characteristics (such as capacitance, inductance, and resistance), and signal integrity effects (such as crosstalk and reflections). Accurate representation of the connector geometry and material properties is also important. Connector manufacturers often provide SPICE or IBIS models that capture these parameters and can be directly integrated into the simulations. -
Q: How can I validate my backplane simulation results?
A: Validating backplane simulation results involves comparing the simulated data with measured data from hardware prototypes or reference designs. By correlating the simulation results with real-world measurements, designers can assess the accuracy of their models and assumptions. Validation can be performed at different levels, such as component-level, board-level, or system-level, depending on the available hardware and measurement capabilities. Regular validation helps build confidence in the simulation methodology and ensures reliable results. -
Q: What are the benefits of conducting parametric studies in backplane simulations?
A: Conducting parametric studies in backplane simulations offers several benefits. By varying design parameters and observing their impact on signal integrity, designers can identify the sensitivity of the system to different variables. Parametric studies help in understanding the design space and determining the optimal combination of parameters that meet the performance requirements. They enable designers to make informed decisions, trade off between different design options, and optimize the system for robustness and reliability. Parametric studies also facilitate design exploration and what-if analysis, allowing designers to assess the impact of potential changes or uncertainties in the design.
No responses yet