What is Signal Integrity?
Signal integrity (SI) is a crucial aspect of PCB design that ensures the quality and reliability of electronic signals transmitted through the board. It involves analyzing and optimizing the electrical characteristics of the PCB to minimize signal distortion, crosstalk, and other issues that can affect the performance of the circuit.
Factors Affecting Signal Integrity
Several factors can impact signal integrity in PCB design, including:
- Impedance mismatch
- Reflections
- Crosstalk
- Electromagnetic interference (EMI)
- Power distribution network (PDN) noise
Why is Signal Integrity Important in PCB Design?
Maintaining signal integrity is essential for several reasons:
- Ensures reliable data transmission
- Prevents data loss or corruption
- Reduces electromagnetic interference (EMI)
- Improves overall system performance
- Helps meet regulatory compliance requirements
How to Achieve Signal Integrity in PCB Design?
1. Impedance Matching
Impedance matching is the process of ensuring that the characteristic impedance of the transmission line matches the impedance of the source and load. This minimizes reflections and ensures efficient power transfer. To achieve impedance matching:
- Choose appropriate PCB materials with consistent dielectric properties
- Control the width and spacing of traces to maintain the desired characteristic impedance
- Use termination resistors to match the impedance of the source and load
2. Minimizing Reflections
Reflections occur when there is an impedance mismatch along the transmission line, causing a portion of the signal to be reflected back to the source. To minimize reflections:
- Avoid abrupt changes in trace width or layer transitions
- Use chamfered or mitered bends instead of 90-degree angles
- Implement proper termination techniques, such as series termination or parallel termination
3. Reducing Crosstalk
Crosstalk is the unwanted coupling of signals between adjacent traces, which can lead to signal distortion and noise. To reduce crosstalk:
- Increase the spacing between adjacent traces
- Use guard traces or ground planes to isolate sensitive signals
- Route critical traces on different layers with proper shielding
- Minimize parallel runs of traces and avoid long coupling lengths
4. Managing EMI
Electromagnetic interference (EMI) can disrupt the operation of the PCB and cause signal integrity issues. To manage EMI:
- Use proper grounding techniques, such as a solid ground plane
- Implement shielding for sensitive components or traces
- Filter power supply lines to reduce high-frequency noise
- Follow EMC design guidelines and regulations
5. Optimizing Power Distribution Network (PDN)
The power distribution network (PDN) is responsible for delivering clean and stable power to the components on the PCB. A poorly designed PDN can introduce noise and affect signal integrity. To optimize the PDN:
- Use decoupling capacitors near power pins of ICs to reduce high-frequency noise
- Implement proper power plane design with low impedance
- Minimize the inductance of power traces and vias
- Use separate power planes for analog and digital circuits
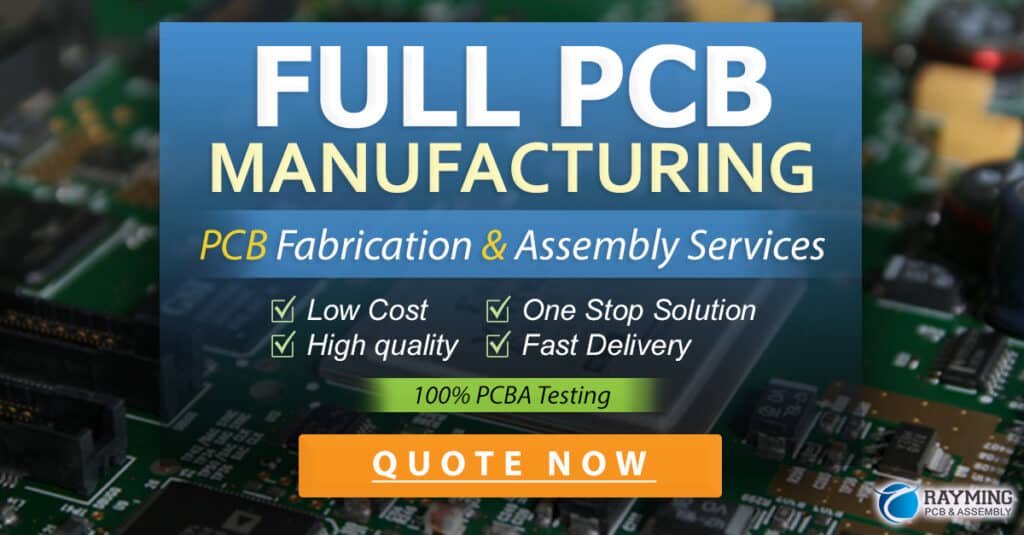
Signal Integrity Analysis Techniques
To ensure signal integrity in PCB design, various analysis techniques can be employed:
Technique | Description |
---|---|
Time-Domain Reflectometry (TDR) | Measures impedance discontinuities and reflections along the transmission line |
Time-Domain Transmission (TDT) | Measures the quality of the transmitted signal at the receiver end |
S-Parameter Analysis | Characterizes the frequency-dependent behavior of the PCB and its components |
Eye Diagram Analysis | Assesses the quality of the received signal by analyzing the opening of the eye pattern |
Electromagnetic Simulation | Simulates the electromagnetic behavior of the PCB to identify potential SI issues |
Best Practices for Signal Integrity in PCB Design
- Plan the PCB stackup carefully, considering the dielectric properties and layer arrangement
- Route critical signals on inner layers, away from potential sources of interference
- Use differential signaling for high-speed and noise-sensitive signals
- Minimize the use of vias, especially for high-speed signals
- Implement proper termination techniques to minimize reflections and ringing
- Follow the 3W rule for trace spacing: keep the spacing between traces at least 3 times the trace width
- Use ground planes to provide a low-impedance return path and shield signals
- Decouple power supplies using appropriate capacitor values and placement
- Perform signal integrity simulations and analysis to identify and resolve issues early in the design process
- Adhere to industry standards and guidelines, such as IPC-2141 (Controlled Impedance Circuit Boards and High-Speed Logic Design)
FAQs
1. What is the difference between single-ended and differential signaling?
Single-ended signaling uses one signal trace referenced to a ground plane, while differential signaling uses a pair of complementary signals. Differential signaling is less susceptible to noise and EMI, making it suitable for high-speed and noise-sensitive applications.
2. How do I calculate the characteristic impedance of a trace?
The characteristic impedance of a trace depends on various factors, including the trace width, thickness, and the dielectric properties of the PCB material. You can use online calculators or PCB design software to calculate the characteristic impedance based on these parameters.
3. What is the purpose of a termination resistor?
A termination resistor is used to match the impedance of the source or load to the characteristic impedance of the transmission line. This minimizes reflections and ensures efficient power transfer, improving signal integrity.
4. How can I reduce crosstalk between adjacent traces?
To reduce crosstalk, you can increase the spacing between traces, use guard traces or ground planes to isolate sensitive signals, route critical traces on different layers, and minimize parallel runs of traces. Additionally, using differential signaling can help reduce the impact of crosstalk.
5. What is the role of decoupling capacitors in maintaining signal integrity?
Decoupling capacitors are used to reduce high-frequency noise on power supply lines. They provide a local source of charge near the power pins of ICs, minimizing the impact of power supply fluctuations on signal integrity. Proper selection and placement of decoupling capacitors are essential for maintaining a clean and stable power supply.
Conclusion
Signal integrity is a critical aspect of PCB design that ensures the reliable transmission of electronic signals. By understanding the factors affecting signal integrity and implementing best practices such as impedance matching, minimizing reflections, reducing crosstalk, managing EMI, and optimizing the power distribution network, designers can create robust and high-performance PCBs. Employing signal integrity analysis techniques and adhering to industry standards further helps in identifying and resolving signal integrity issues early in the design process. By prioritizing signal integrity in PCB design, engineers can develop reliable and efficient electronic systems that meet the demanding requirements of modern applications.
No responses yet