Advantages of Using Power MOSFETs in Parallel
Increased Current-Handling Capacity
The primary reason for using power MOSFETs in parallel is to increase the current-handling capacity of the system. By distributing the current among multiple MOSFETs, the overall current capability is increased, allowing for higher power applications.
Reduced On-State Resistance
When power MOSFETs are connected in parallel, the effective on-state resistance (RDS(on)) is reduced. The total RDS(on) of N MOSFETs in parallel is given by:
RDS(on)_total = RDS(on) / N
This reduction in on-state resistance leads to lower conduction losses and improved efficiency.
Improved Thermal Performance
Parallel power MOSFETs can also improve thermal performance by spreading the heat dissipation across multiple devices. Each MOSFET handles a portion of the total current, reducing the individual device’s power dissipation and junction temperature. This can lead to a more reliable system and extended device lifetime.
Challenges of Using Power MOSFETs in Parallel
Current Sharing
One of the main challenges in using power MOSFETs in parallel is ensuring proper current sharing among the devices. Due to variations in device parameters, such as threshold voltage and on-state resistance, the current may not distribute evenly among the parallel MOSFETs. This can lead to one or more devices carrying a disproportionate amount of current, potentially causing overheating and device failure.
Temperature Dependence of RDS(on)
The on-state resistance of a MOSFET is temperature-dependent, typically increasing with rising junction temperature. In parallel configurations, this can lead to a phenomenon called “thermal runaway.” As one MOSFET carries more current, its temperature increases, causing its RDS(on) to increase. This, in turn, leads to even more current flowing through that device, further increasing its temperature. If left unchecked, thermal runaway can cause device failure and potentially damage the entire system.
Gate Drive Requirements
Parallel power MOSFETs require careful consideration of gate drive requirements. The gate driver must be able to supply sufficient current to charge and discharge the input capacitance of all parallel devices simultaneously. Inadequate gate drive can lead to uneven switching, increased switching losses, and potential device failure.
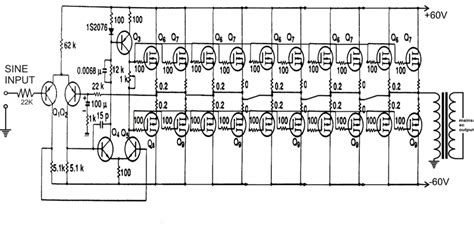
Best Practices for Using Power MOSFETs in Parallel
Device Selection
When selecting power MOSFETs for parallel operation, it is essential to choose devices with closely matched parameters. Key parameters to consider include:
- Threshold voltage (VGS(th))
- On-state resistance (RDS(on))
- Transconductance (gfs)
- Gate charge (Qg)
Using devices from the same manufacturing lot can help ensure better parameter matching.
Layout Considerations
Proper layout is crucial for the successful implementation of parallel power MOSFETs. The following guidelines should be followed:
- Minimize trace inductance by using wide, short traces and a symmetrical layout
- Ensure equal trace lengths from the gate driver to each MOSFET gate
- Use a single-point ground connection for all MOSFETs
- Place MOSFETs close together to minimize thermal gradients
Current Balancing Techniques
To promote equal current sharing among parallel MOSFETs, several techniques can be employed:
1. Source Ballast Resistors
Adding small resistors (typically in the range of 10-100 mΩ) in series with the source of each MOSFET can help balance the current. The voltage drop across these resistors provides negative feedback, compensating for variations in device parameters. The value of the ballast resistor should be carefully chosen to minimize power dissipation while still providing adequate current balancing.
2. Active Current Balancing
Active current balancing involves using a dedicated circuit to monitor and adjust the current through each MOSFET. This can be achieved using current sense resistors and operational amplifiers to control the gate voltage of each device independently. While more complex than passive techniques, active current balancing offers better performance and can adapt to changing operating conditions.
Thermal Management
Proper thermal management is essential for reliable operation of parallel power MOSFETs. The following strategies can be employed:
- Use a heatsink with sufficient thermal capacity and surface area
- Ensure proper thermal coupling between MOSFETs and the heatsink using thermal interface materials
- Monitor MOSFET temperatures using thermistors or integrated temperature sensors
- Implement thermal shutdown or current limiting to protect against overtemperature conditions
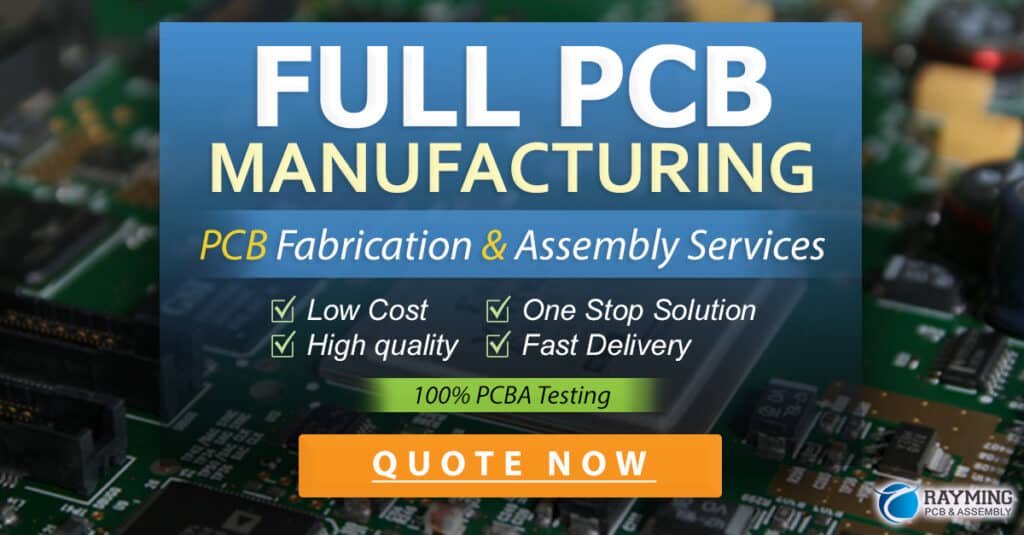
FAQ
1. How many power MOSFETs can be connected in parallel?
The number of power MOSFETs that can be connected in parallel depends on various factors, such as the device ratings, application requirements, and the effectiveness of current balancing techniques employed. In practice, it is common to see 2-8 MOSFETs in parallel. However, some applications may use even more devices, provided that proper design considerations are made.
2. Can I mix different MOSFET models when paralleling?
It is generally not recommended to mix different MOSFET models when paralleling. Each MOSFET model may have different parameters, such as RDS(on), VGS(th), and thermal characteristics. Mixing models can lead to uneven current sharing and potential device failure. It is best to use identical MOSFETs from the same manufacturer and, if possible, from the same production lot.
3. How do I select the appropriate gate driver for parallel MOSFETs?
When selecting a gate driver for parallel MOSFETs, consider the following factors:
- Total gate charge (Qg) of all parallel MOSFETs
- Required gate drive voltage and current
- Switching frequency
- Available power supplies
The gate driver should be capable of supplying sufficient current to quickly charge and discharge the input capacitance of all parallel MOSFETs. Specialized gate drivers designed for parallel operation, such as those with adjustable gate resistors or active current balancing, can help ensure optimal performance.
4. What is the impact of paralleling on switching performance?
Paralleling power MOSFETs can impact switching performance due to increased gate capacitance and potential differences in device parameters. The increased gate capacitance may lead to slower switching times and higher switching losses. Uneven current sharing during switching can also cause additional stress on individual devices. Proper gate drive design and layout techniques can help mitigate these issues and ensure optimal switching performance.
5. Can I parallel power MOSFETs with different voltage ratings?
It is not recommended to parallel power MOSFETs with different voltage ratings. MOSFETs with higher voltage ratings typically have higher RDS(on) and may not share current evenly with lower voltage devices. Additionally, if the applied voltage exceeds the rating of the lower voltage MOSFET, it may fail and cause a short circuit, potentially damaging the other devices in parallel. Always use MOSFETs with the same voltage rating when paralleling.
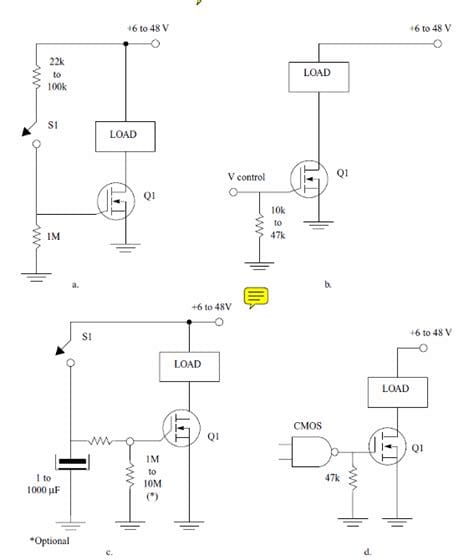
Conclusion
Using power MOSFETs in parallel can be an effective solution for increasing current-handling capacity, reducing on-state resistance, and improving thermal performance in high-power applications. However, designers must carefully consider the challenges associated with current sharing, temperature dependence, and gate drive requirements.
By following best practices such as proper device selection, layout considerations, current balancing techniques, and thermal management, engineers can successfully implement parallel power MOSFET configurations. With careful design and attention to detail, parallel power MOSFETs can enable efficient, reliable, and high-performance power electronic systems.
As power electronics continue to advance, the use of parallel power MOSFETs will likely remain an important technique for achieving higher power levels and improved system performance. By understanding the principles and best practices outlined in this article, designers can effectively harness the benefits of parallel power MOSFETs in their applications.
No responses yet