What is Current Diversion?
Current diversion, also known as current crowding or current hogging, is an electrical phenomenon that occurs when the flow of electric current is unevenly distributed across a printed circuit board (PCB). This uneven distribution can lead to localized areas of high current density, which can cause damage to the PCB and its components.
Current diversion is often caused by differences in the resistance of different paths on the PCB. When there are multiple paths for current to flow, the current will naturally take the path of least resistance. If one path has significantly lower resistance than the others, it will draw a disproportionate amount of current, leading to current crowding in that area.
Causes of Low Resistance on PCBs
There are several factors that can contribute to low resistance on a PCB, making it more susceptible to current diversion:
Improper PCB Design
One of the most common causes of low resistance on a PCB is improper design. If the traces on the PCB are too narrow or too thin, they will have higher resistance than intended, which can lead to current crowding. Similarly, if the spacing between traces is too small, it can create opportunities for short circuits or arcing, which can also cause current diversion.
Manufacturing Defects
Manufacturing defects can also contribute to low resistance on a PCB. If the copper traces are not etched properly, or if there are voids or inconsistencies in the copper plating, it can create areas of low resistance that can lead to current diversion.
Environmental Factors
Environmental factors such as temperature, humidity, and contamination can also affect the resistance of a PCB. High temperatures can cause the copper traces to expand, which can lead to increased resistance and current crowding. Humidity can cause corrosion on the PCB, which can create low resistance paths for current to flow. Contamination from dust, dirt, or other particles can also create short circuits or low resistance paths on the PCB.
Effects of Current Diversion on PCBs
Current diversion can have several negative effects on a PCB and its components:
Overheating
One of the most immediate effects of current diversion is overheating. When current is concentrated in a small area of the PCB, it can generate a significant amount of heat. This heat can damage the PCB substrate, causing delamination or warping. It can also damage the components on the PCB, causing them to fail prematurely.
Voltage Drop
Current diversion can also cause voltage drop across the PCB. When current is flowing through a high resistance path, it can cause a voltage drop across that path. This voltage drop can affect the performance of the components on the PCB, causing them to operate outside of their specified voltage range.
Electromagnetic Interference (EMI)
Current diversion can also cause electromagnetic interference (EMI) on the PCB. When current is flowing through a high resistance path, it can generate electromagnetic fields that can interfere with other components on the PCB or with nearby electronic devices.
PCB Damage
Over time, current diversion can cause physical damage to the PCB. The repeated heating and cooling cycles caused by current crowding can cause the copper traces to crack or delaminate from the PCB substrate. This damage can lead to open circuits or short circuits on the PCB, which can cause the entire system to fail.
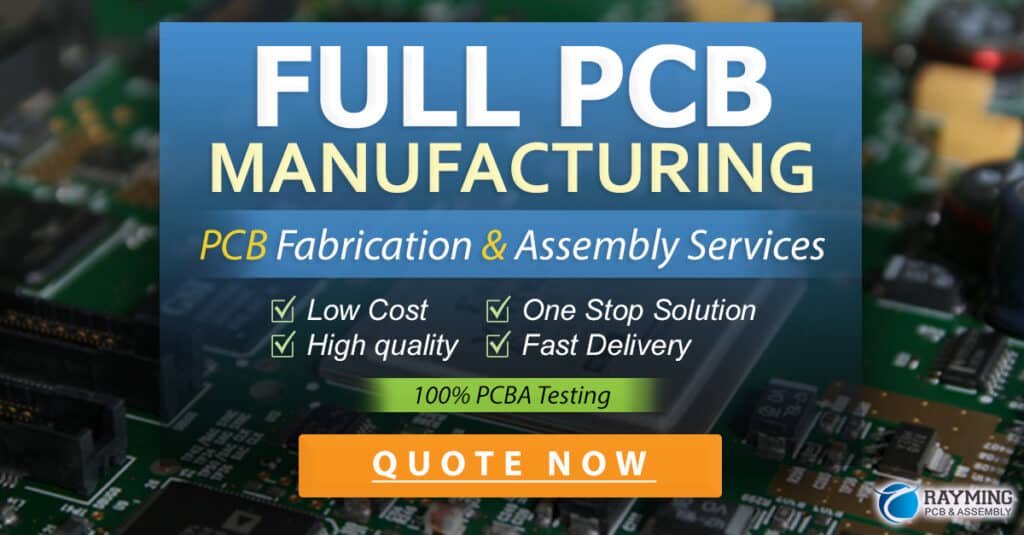
Preventing Current Diversion on PCBs
There are several steps that can be taken to prevent current diversion on PCBs:
Proper PCB Design
The most effective way to prevent current diversion is to ensure that the PCB is properly designed from the outset. This means using appropriate trace widths and thicknesses for the expected current levels, and ensuring that there is adequate spacing between traces to prevent short circuits or arcing.
Current Level (A) | Trace Width (mm) | Trace Thickness (oz) |
---|---|---|
0-1 | 0.25 | 1 |
1-2 | 0.5 | 1 |
2-4 | 1.0 | 2 |
4-6 | 1.5 | 2 |
6-10 | 2.5 | 3 |
Table 1: Recommended trace widths and thicknesses for different current levels
Use of Current-Limiting Devices
Another way to prevent current diversion is to use current-limiting devices such as fuses or circuit breakers. These devices can be placed in series with high-current paths on the PCB to limit the amount of current that can flow through them. If the current exceeds a certain threshold, the fuse will blow or the circuit breaker will trip, preventing damage to the PCB.
Proper Manufacturing Processes
Proper manufacturing processes can also help to prevent current diversion on PCBs. This includes ensuring that the copper traces are etched properly, with no voids or inconsistencies, and that the copper plating is of consistent thickness across the entire PCB.
Environmental Control
Controlling the environment in which the PCB operates can also help to prevent current diversion. This means keeping the PCB away from sources of heat, humidity, and contamination, and ensuring that it is properly ventilated to dissipate any heat generated by current crowding.
Detecting Current Diversion on PCBs
Even with proper design and manufacturing processes, current diversion can still occur on PCBs. It is important to be able to detect current diversion early, before it causes significant damage to the PCB or its components.
Visual Inspection
One of the simplest ways to detect current diversion is through visual inspection of the PCB. Look for areas of the PCB that appear discolored or charred, as this can indicate overheating caused by current crowding. Also look for any cracks or delamination in the PCB substrate, as this can indicate physical damage caused by repeated heating and cooling cycles.
Thermal Imaging
Thermal imaging can also be used to detect current diversion on PCBs. By using a thermal camera to image the PCB while it is in operation, areas of high temperature can be identified, indicating areas of high current density.
Current Measurement
Measuring the current flowing through different paths on the PCB can also help to detect current diversion. By comparing the measured current to the expected current based on the PCB design, areas of high current density can be identified.
Repairing PCBs Damaged by Current Diversion
If a PCB has been damaged by current diversion, it may be possible to repair it, depending on the extent of the damage.
Trace Repair
If the damage is limited to a single trace or a small area of the PCB, it may be possible to repair the trace using a conductive epoxy or a small piece of wire. This can be a delicate process, however, and may require specialized equipment and expertise.
Component Replacement
If the damage has affected the components on the PCB, it may be necessary to replace them. This can be a time-consuming and expensive process, particularly if the components are no longer available or if they are difficult to source.
PCB Replacement
In some cases, the damage to the PCB may be too extensive to repair, and the entire PCB may need to be replaced. This can be a costly and time-consuming process, particularly if the PCB is part of a larger system or if it is a custom design.
FAQ
What is the difference between current diversion and voltage drop?
Current diversion refers to the uneven distribution of current across a PCB, while voltage drop refers to the decrease in voltage across a high resistance path on the PCB. Current diversion can cause voltage drop, but voltage drop can also occur without current diversion.
Can current diversion cause a PCB to catch fire?
In extreme cases, current diversion can generate enough heat to cause a PCB to catch fire. This is more likely to occur if the PCB is not properly designed or manufactured, or if it is exposed to environmental factors such as high temperatures or contamination.
How can I tell if a PCB has been damaged by current diversion?
Signs of PCB damage caused by current diversion include discoloration or charring of the PCB substrate, cracks or delamination in the substrate, and premature failure of components on the PCB. Thermal imaging and current measurement can also be used to detect areas of high current density on the PCB.
Can current diversion be prevented entirely?
While proper PCB design and manufacturing processes can help to minimize the risk of current diversion, it cannot be prevented entirely. Environmental factors and other variables can still cause current diversion to occur, even on a well-designed PCB.
How much does it cost to repair a PCB damaged by current diversion?
The cost of repairing a PCB damaged by current diversion can vary widely depending on the extent of the damage and the complexity of the PCB. In some cases, it may be more cost-effective to replace the entire PCB rather than attempting to repair it. A professional PCB repair service can provide an estimate based on the specific circumstances of the damage.
Conclusion
Current diversion is a serious problem that can cause significant damage to PCBs and their components. By understanding the causes and effects of current diversion, and by taking steps to prevent it through proper PCB design and manufacturing processes, the risk of PCB damage can be minimized. If a PCB has been damaged by current diversion, it may be possible to repair it, but in some cases, replacement may be necessary. Regardless of the approach taken, it is important to address current diversion as soon as it is detected to prevent further damage and ensure the reliable operation of the PCB and the system it is a part of.
No responses yet