Introduction to IoT-based Electronics Manufacturing Monitoring
The Internet of Things (IoT) has revolutionized various industries, including electronics manufacturing. IoT-based monitoring systems have become increasingly popular in university lab environments, where they enable real-time monitoring and control of manufacturing processes. By incorporating sensors and connected devices, these systems provide valuable insights into the performance of equipment, quality of products, and overall efficiency of the manufacturing process.
In this article, we will explore the concept of sensor-based IoT monitoring in the context of electronics manufacturing in a university lab setting. We will discuss the benefits, challenges, and key components of such a system, as well as provide examples of its implementation.
Benefits of IoT-based Electronics Manufacturing Monitoring
- Real-time data collection and analysis
- Improved quality control and defect detection
- Enhanced equipment performance and maintenance
- Increased efficiency and productivity
- Cost reduction through optimized resource utilization
Challenges in Implementing IoT-based Monitoring Systems
- Integration with existing infrastructure
- Data security and privacy concerns
- Scalability and interoperability issues
- Technical expertise and training requirements
- Initial investment and ongoing maintenance costs
Key Components of an IoT-based Electronics Manufacturing Monitoring System
Sensors and Data Acquisition
Sensors are the foundation of any IoT-based monitoring system. In electronics manufacturing, various types of sensors are employed to collect data on different aspects of the process, such as:
- Temperature sensors
- Humidity sensors
- Pressure sensors
- Vibration sensors
- Current and voltage sensors
These sensors are strategically placed on equipment, production lines, and even on the products themselves to gather real-time data.
Data Communication and Networking
Once the data is collected by the sensors, it needs to be transmitted to a central system for processing and analysis. This is achieved through various communication protocols and networking technologies, such as:
- Wi-Fi
- Bluetooth
- Zigbee
- LoRaWAN
- Ethernet
The choice of communication technology depends on factors such as the distance between devices, power consumption, and data transmission requirements.
Data Processing and Analytics
The data collected by the sensors is processed and analyzed using advanced algorithms and machine learning techniques. This enables the system to:
- Detect anomalies and potential issues
- Predict equipment failures and maintenance needs
- Optimize production processes
- Generate reports and visualizations for decision-making
User Interface and Visualization
A user-friendly interface is essential for effectively monitoring and controlling the electronics manufacturing process. This typically includes:
- Real-time dashboards
- Alert and notification systems
- Mobile applications
- Historical data and trend analysis
Implementation of IoT-based Electronics Manufacturing Monitoring in University Labs
Case Study 1: Smart Soldering Station Monitoring
In this case study, an IoT-based monitoring system was implemented for a smart soldering station in a university electronics lab. The system consisted of the following components:
- Temperature sensors embedded in the soldering iron tip
- Current and voltage sensors to monitor power consumption
- Wi-Fi module for data transmission
- Cloud-based data processing and analytics platform
- Mobile app for real-time monitoring and control
The system enabled the lab technicians to:
- Monitor the temperature and power consumption of the soldering station in real-time
- Receive alerts when the temperature exceeded a certain threshold
- Remotely control the soldering station using the mobile app
- Analyze historical data to optimize the soldering process and predict maintenance needs
Case Study 2: PCB Assembly Line Monitoring
In this case study, an IoT-based monitoring system was implemented for a PCB assembly line in a university electronics manufacturing lab. The system consisted of the following components:
- Vision sensors for quality inspection
- Vibration sensors to monitor equipment health
- RFID tags for tracking PCBs throughout the assembly process
- LoRaWAN network for data transmission
- Edge computing devices for local data processing
- Cloud-based analytics platform for advanced insights
The system enabled the lab managers to:
- Monitor the quality of PCBs in real-time and detect defects
- Track the progress of individual PCBs through the assembly process
- Receive alerts when equipment showed signs of potential failure
- Optimize the assembly line based on real-time data and historical trends
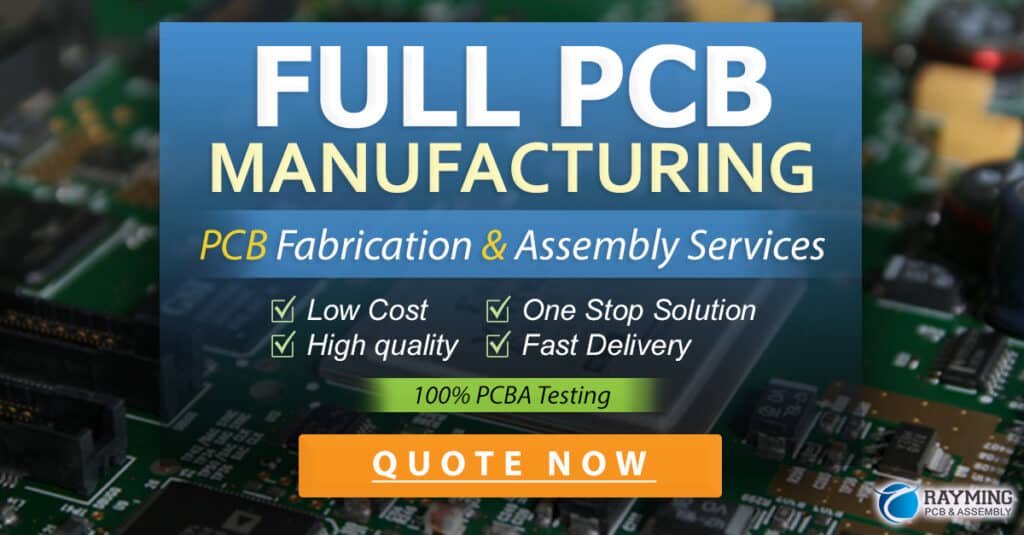
Best Practices for Implementing IoT-based Electronics Manufacturing Monitoring
- Conduct a thorough assessment of the manufacturing process to identify key monitoring points
- Choose sensors and communication technologies that are reliable, accurate, and suitable for the specific environment
- Ensure data security and privacy by implementing appropriate encryption and access control measures
- Provide adequate training to staff on the use and maintenance of the IoT-based monitoring system
- Regularly review and update the system to incorporate new technologies and address evolving needs
Future Trends in IoT-based Electronics Manufacturing Monitoring
- Increased adoption of 5G networks for faster and more reliable data transmission
- Integration of artificial intelligence (AI) and machine learning for predictive maintenance and process optimization
- Development of blockchain-based solutions for secure data sharing and supply chain transparency
- Emergence of digital twins for virtual representation and simulation of manufacturing processes
- Growing focus on sustainability and energy efficiency in electronics manufacturing
Frequently Asked Questions (FAQ)
-
Q: What are the main benefits of implementing an IoT-based monitoring system in an electronics manufacturing lab?
A: The main benefits include real-time data collection and analysis, improved quality control, enhanced equipment performance, increased efficiency, and cost reduction. -
Q: What types of sensors are commonly used in IoT-based electronics manufacturing monitoring?
A: Common sensors include temperature, humidity, pressure, vibration, current, and voltage sensors, among others. -
Q: How is data transmitted from sensors to the central system in an IoT-based monitoring setup?
A: Data is typically transmitted using wireless communication protocols such as Wi-Fi, Bluetooth, Zigbee, or LoRaWAN, depending on the specific requirements of the system. -
Q: What role does data analytics play in IoT-based electronics manufacturing monitoring?
A: Data analytics enables the detection of anomalies, prediction of equipment failures, optimization of production processes, and generation of reports and visualizations for decision-making. -
Q: What are some best practices for implementing an IoT-based monitoring system in a university electronics manufacturing lab?
A: Best practices include conducting a thorough assessment of the manufacturing process, choosing reliable and suitable sensors and communication technologies, ensuring data security and privacy, providing staff training, and regularly reviewing and updating the system.
Conclusion
IoT-based monitoring systems have the potential to revolutionize electronics manufacturing in university lab environments. By leveraging sensors, data communication, and analytics, these systems enable real-time monitoring, quality control, and process optimization. While there are challenges to implementation, such as integration with existing infrastructure and data security concerns, the benefits of increased efficiency, reduced costs, and improved product quality make IoT-based monitoring an attractive solution for university labs.
As technology continues to advance, we can expect to see further developments in IoT-based electronics manufacturing monitoring, such as the integration of AI, blockchain, and digital twins. By staying informed about these trends and adopting best practices for implementation, university labs can remain at the forefront of electronics manufacturing innovation.
No responses yet