What is a Semiconductor PCB?
A semiconductor PCB is a specialized type of printed circuit board designed to accommodate and integrate semiconductor components, such as integrated circuits (ICs), transistors, and diodes. These PCBs are engineered to provide optimal electrical and thermal performance, ensuring the proper functioning of the semiconductor devices they host.
Key Features of Semiconductor PCBs
Semiconductor PCBs possess several distinctive features that set them apart from traditional PCBs:
-
High-density interconnects (HDI): Semiconductor PCBs often incorporate HDI technology, which allows for the creation of fine-pitch traces and vias, enabling the placement of a large number of components in a compact space.
-
Thermal management: Due to the high power dissipation of semiconductor devices, semiconductor PCBs are designed with efficient thermal management solutions, such as heat sinks, thermal vias, and specialized substrate materials.
-
Controlled impedance: To ensure signal integrity and minimize signal distortion, semiconductor PCBs are manufactured with controlled impedance traces, which help maintain consistent electrical characteristics throughout the board.
-
Rigorous manufacturing standards: Semiconductor PCBs are subject to stringent manufacturing standards and undergo extensive testing to ensure reliability and performance in demanding applications.
Manufacturing Process of Semiconductor PCBs
The manufacturing process of semiconductor PCBs involves several critical steps that ensure the quality and functionality of the final product:
-
Design and Layout: The first step in the manufacturing process is the design and layout of the PCB. This involves creating a schematic diagram and a physical layout using specialized PCB design software. The layout determines the placement of components, traces, and vias on the board.
-
Substrate Preparation: The substrate, typically made of materials like FR-4, ceramic, or polyimide, is cleaned and prepared for the subsequent manufacturing steps. This may involve drilling holes, applying a copper layer, and roughening the surface to improve adhesion.
-
Patterning and Etching: Using photolithography techniques, the desired circuit pattern is transferred onto the substrate. This involves applying a photoresist layer, exposing it to light through a mask, and developing the pattern. The exposed copper areas are then etched away, leaving behind the desired traces and pads.
-
Lamination and Drilling: Multiple layers of the patterned substrate are laminated together using heat and pressure to form a multi-layer PCB. Holes are drilled through the layers to accommodate vias and component leads.
-
Plating and Surface Finishing: The drilled holes are plated with copper to create electrical connections between layers. The exposed copper surfaces are then finished with a protective coating, such as solder mask, to prevent oxidation and improve solderability.
-
Component Assembly: The final step involves the assembly of semiconductor components onto the PCB. This can be done through various techniques, such as surface mount technology (SMT) or through-hole mounting, depending on the component types and the PCB design.
Applications of Semiconductor PCBs
Semiconductor PCBs find applications in a wide range of industries and devices, thanks to their ability to support high-performance semiconductor components. Some notable applications include:
-
Consumer Electronics: Semiconductor PCBs are extensively used in consumer electronic devices, such as smartphones, tablets, laptops, and gaming consoles. These PCBs enable the integration of powerful processors, memory chips, and other semiconductor components, allowing for the creation of feature-rich and compact devices.
-
Automotive Electronics: The automotive industry increasingly relies on semiconductor PCBs for various electronic systems, including engine control units (ECUs), infotainment systems, and advanced driver assistance systems (ADAS). These PCBs must withstand harsh environmental conditions and meet stringent reliability requirements.
-
Medical Devices: Semiconductor PCBs play a vital role in medical devices, such as implantable devices, diagnostic equipment, and monitoring systems. These PCBs must adhere to strict biocompatibility and safety standards to ensure patient safety and device performance.
-
Industrial Automation: In industrial automation systems, semiconductor PCBs are used in programmable logic controllers (PLCs), human-machine interfaces (HMIs), and various sensors and actuators. These PCBs enable the control and monitoring of industrial processes, improving efficiency and productivity.
-
Aerospace and Defense: Semiconductor PCBs are critical components in aerospace and defense applications, including avionics systems, satellite communications, and military equipment. These PCBs must meet rigorous standards for reliability, durability, and performance in extreme environments.
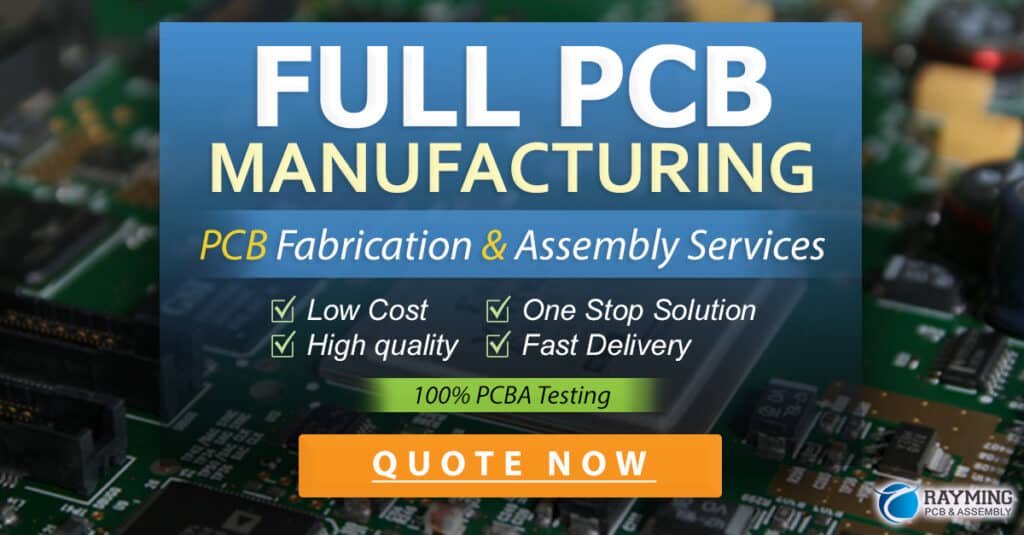
Advantages of Semiconductor PCBs
Semiconductor PCBs offer several advantages over traditional PCBs, making them an attractive choice for various applications:
-
Miniaturization: The use of HDI technology and advanced manufacturing techniques allows for the creation of highly compact semiconductor PCBs, enabling the development of smaller and more portable devices.
-
Improved Performance: Semiconductor PCBs are designed to optimize the performance of the semiconductor components they host. This includes efficient thermal management, controlled impedance, and high-speed signal transmission, resulting in enhanced device performance.
-
Reliability: Semiconductor PCBs undergo rigorous testing and quality control processes to ensure their reliability in demanding applications. This includes testing for thermal cycling, vibration, and electromagnetic compatibility (EMC).
-
Cost-Effectiveness: Despite their advanced features and manufacturing processes, semiconductor PCBs can be cost-effective in high-volume production. The use of automated assembly techniques and standardized manufacturing processes helps reduce costs and improve yield.
Challenges and Future Trends
While semiconductor PCBs have revolutionized the electronics industry, there are still challenges and opportunities for further advancement:
-
Increasing Complexity: As devices become more sophisticated and feature-rich, the complexity of semiconductor PCBs continues to grow. This requires the development of advanced design tools, manufacturing processes, and testing methodologies to ensure the reliability and performance of these complex boards.
-
Thermal Management: With the increasing power density of semiconductor devices, thermal management remains a critical challenge for semiconductor PCBs. Researchers and manufacturers are exploring novel materials, such as graphene and carbon nanotubes, to improve the thermal conductivity and heat dissipation capabilities of PCBs.
-
High-Frequency Applications: The demand for high-frequency applications, such as 5G networks and millimeter-wave radar, is driving the development of semiconductor PCBs that can operate at higher frequencies. This requires the use of specialized materials, such as low-loss dielectrics and advanced laminate structures, to minimize signal loss and maintain signal integrity.
-
Environmental Sustainability: As environmental concerns gain prominence, there is a growing focus on developing eco-friendly semiconductor PCBs. This includes the use of lead-free solders, halogen-free materials, and recyclable substrates. Manufacturers are also exploring ways to reduce waste and improve the energy efficiency of the manufacturing process.
Frequently Asked Questions (FAQ)
-
What is the difference between a semiconductor PCB and a traditional PCB?
A semiconductor PCB is specifically designed to accommodate and integrate semiconductor components, such as integrated circuits and transistors. It incorporates advanced features like high-density interconnects, thermal management solutions, and controlled impedance traces to optimize the performance of the semiconductor devices. Traditional PCBs, on the other hand, are more general-purpose and may not have the same level of complexity or specialized features. -
What materials are commonly used for semiconductor PCB substrates?
Common materials used for semiconductor PCB substrates include FR-4 (a glass-reinforced epoxy laminate), ceramic substrates (such as alumina or aluminum nitride), and polyimide. The choice of substrate material depends on factors such as the desired electrical properties, thermal conductivity, and mechanical stability required for the specific application. -
How do semiconductor PCBs handle thermal management?
Semiconductor PCBs employ various thermal management techniques to dissipate heat generated by the semiconductor components. These techniques include the use of heat sinks, thermal vias (conductive paths that transfer heat through the PCB layers), and specialized substrate materials with high thermal conductivity. The PCB layout is also optimized to promote efficient heat dissipation and prevent hot spots. -
What are the key considerations when designing a semiconductor PCB?
When designing a semiconductor PCB, several key considerations include: - Component placement and routing to minimize signal interference and optimize performance
- Thermal management to ensure proper heat dissipation and prevent component overheating
- Controlled impedance to maintain signal integrity and minimize signal distortion
-
Manufacturing feasibility and cost-effectiveness, considering factors such as layer count, via size, and component density
-
How are semiconductor PCBs tested for reliability and performance?
Semiconductor PCBs undergo extensive testing to ensure their reliability and performance. Some common testing methods include: - Thermal cycling tests to evaluate the PCB’s ability to withstand temperature variations
- Vibration and shock tests to assess the PCB’s mechanical stability and resistance to physical stress
- Electromagnetic compatibility (EMC) tests to ensure the PCB does not generate or is susceptible to electromagnetic interference
- Functional testing to verify that the PCB performs as intended and meets the specified requirements
Characteristic | Semiconductor PCB | Traditional PCB |
---|---|---|
Component Types | Semiconductor devices (ICs, transistors, diodes) | General-purpose components (resistors, capacitors, connectors) |
Interconnect Density | High-density interconnects (HDI) for compact designs | Lower interconnect density |
Thermal Management | Advanced thermal management solutions (heat sinks, thermal vias) | Basic thermal management |
Controlled Impedance | Designed with controlled impedance traces for signal integrity | May not have controlled impedance |
Manufacturing Standards | Stringent standards and extensive testing for reliability | Less rigorous standards and testing |
Conclusion
Semiconductor PCBs have become an indispensable part of modern-day electronics, enabling the development of advanced and compact devices across various industries. With their ability to support high-performance semiconductor components, these versatile circuit boards offer improved functionality, reliability, and cost-effectiveness.
As technology continues to evolve, semiconductor PCBs will play an increasingly critical role in shaping the future of electronics. Manufacturers and designers must stay abreast of the latest advancements in materials, manufacturing processes, and design techniques to overcome challenges and unlock new possibilities in the world of semiconductor PCBs.
By understanding the intricacies of semiconductor PCBs, from their manufacturing process to their applications and future trends, engineers, and technologists can leverage this powerful technology to create innovative and cutting-edge devices that push the boundaries of what is possible in the realm of electronics.
No responses yet