Introduction to SAP@Averatek
Averatek Corporation, a leading innovator in advanced printed circuit board (PCB) technology, has developed a groundbreaking Semi Additive Process (SAP) that revolutionizes the manufacturing of high-density interconnects (HDI) and ultra-high density interconnects (UHDI) PCBs. This article will delve into the intricacies of SAP@Averatek, exploring its benefits, applications, and potential impact on the electronics industry.
Understanding the Semi Additive Process
What is the Semi Additive Process?
The Semi Additive Process is a PCB manufacturing technique that combines the advantages of subtractive and additive processes. It involves the selective deposition of copper on a substrate, followed by the removal of excess copper to create the desired circuit pattern. This approach enables the creation of fine-pitch traces and high-density interconnects, surpassing the limitations of traditional PCB manufacturing methods.
Key Steps in SAP@Averatek
-
Substrate Preparation: The process begins with the preparation of a substrate, typically a dielectric material, which serves as the base for the PCB.
-
Seed Layer Deposition: A thin layer of conductive material, such as copper, is deposited on the substrate using techniques like electroless plating or sputtering. This seed layer acts as a foundation for the subsequent copper deposition.
-
Photoresist Application: A photoresist material is applied to the substrate and patterned using photolithography. The photoresist selectively exposes areas where the copper traces will be formed.
-
Copper Plating: Copper is electroplated onto the exposed areas of the seed layer, building up the thickness of the copper traces to the desired level.
-
Photoresist Removal: The photoresist is stripped away, leaving behind the plated copper traces on the substrate.
-
Etching: The exposed seed layer between the copper traces is etched away, isolating the individual traces and creating the final circuit pattern.
Advantages of SAP@Averatek
SAP@Averatek offers several advantages over traditional PCB manufacturing processes:
-
High-Density Interconnects: SAP enables the creation of fine-pitch traces and high-density interconnects, allowing for the miniaturization of electronic devices and improved signal integrity.
-
Improved Reliability: The selective deposition of copper in SAP results in more uniform and consistent traces, reducing the risk of defects and improving the overall reliability of the PCB.
-
Cost-Effectiveness: SAP@Averatek optimizes material usage and reduces waste, leading to cost savings in PCB production.
-
Enhanced Design Flexibility: The ability to create fine-pitch traces and complex circuit patterns using SAP opens up new possibilities for PCB designers, enabling the development of innovative and compact electronic devices.
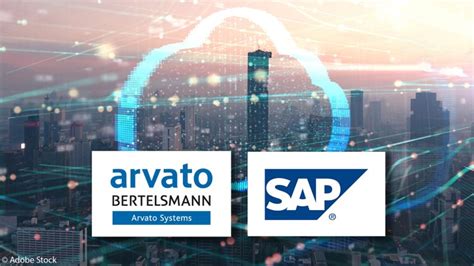
Applications of SAP@Averatek
Consumer Electronics
SAP@Averatek finds extensive applications in the consumer electronics industry, where the demand for smaller, faster, and more feature-rich devices is ever-increasing. By enabling the creation of HDI and UHDI PCBs, SAP technology allows for the development of compact and high-performance smartphones, tablets, wearables, and other consumer gadgets.
Automotive Electronics
The automotive industry is witnessing a rapid adoption of advanced electronics, from infotainment systems to advanced driver assistance systems (ADAS) and autonomous driving technologies. SAP@Averatek enables the manufacturing of reliable and high-density PCBs that can withstand the harsh automotive environment and meet the stringent reliability requirements of the industry.
Medical Devices
Medical devices, such as implantable devices, wearable monitors, and diagnostic equipment, require PCBs with high reliability, miniaturization, and signal integrity. SAP@Averatek’s ability to create fine-pitch traces and high-density interconnects makes it an ideal choice for medical device manufacturers, enabling the development of compact and reliable electronic components for medical applications.
Aerospace and Defense
The aerospace and defense industry demands PCBs that can withstand extreme conditions, such as high temperatures, vibrations, and electromagnetic interference. SAP@Averatek’s selective copper deposition process results in more uniform and robust traces, making it suitable for the manufacturing of PCBs for aerospace and defense applications, including avionics, satellite communication systems, and military equipment.
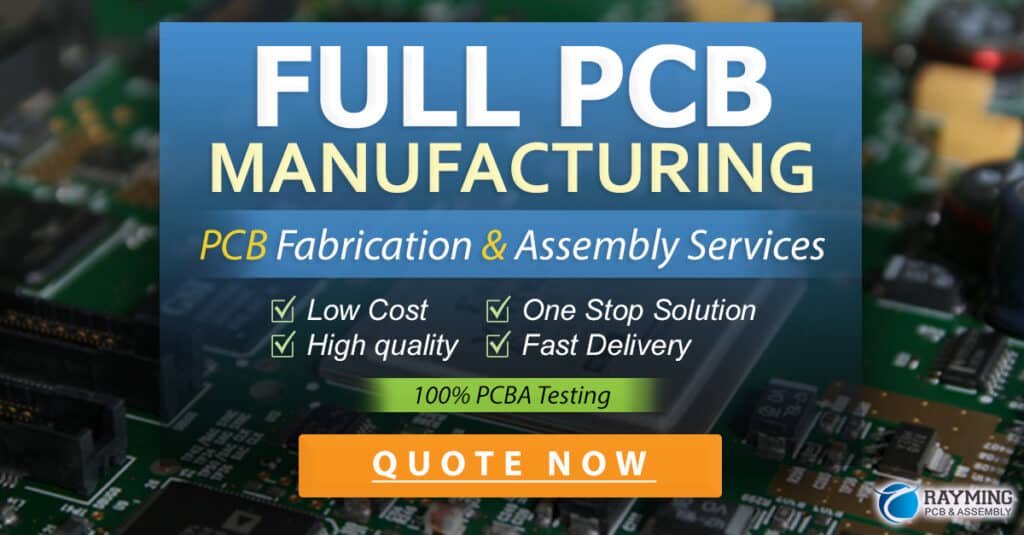
Averatek’s SAP Technology: A Closer Look
Averatek’s Expertise in SAP
Averatek Corporation has been at the forefront of developing and refining SAP technology for PCB manufacturing. With a team of experienced engineers and a state-of-the-art facility, Averatek has established itself as a leader in SAP solutions. The company’s expertise spans across various aspects of SAP, including process optimization, material selection, and quality control.
Averatek’s SAP Process Flow
Averatek’s SAP process flow is designed to ensure the highest quality and reliability of the manufactured PCBs. The process involves the following key steps:
-
Substrate Preparation: Averatek uses advanced substrate materials that offer excellent dielectric properties and dimensional stability, ensuring a robust foundation for the PCB.
-
Seed Layer Deposition: Averatek employs advanced deposition techniques, such as electroless plating and sputtering, to create a uniform and adherent seed layer on the substrate.
-
Photoresist Application and Patterning: Averatek uses high-resolution photoresists and advanced photolithography techniques to create precise circuit patterns on the substrate.
-
Copper Plating: Averatek’s copper plating process is optimized to achieve uniform and consistent copper deposition, resulting in high-quality traces with excellent electrical properties.
-
Photoresist Removal and Etching: Averatek employs environmentally friendly photoresist removal and etching processes to minimize waste and ensure the cleanliness of the final PCB.
-
Quality Control: Averatek implements rigorous quality control measures throughout the SAP process to ensure that the manufactured PCBs meet the highest standards of reliability and performance.
Averatek’s SAP Capabilities
Averatek’s SAP technology offers the following capabilities:
Feature | Capability |
---|---|
Trace Width/Spacing | Down to 10 μm |
Copper Thickness | Up to 35 μm |
Layer Count | Up to 16 layers |
Material Compatibility | FR-4, Polyimide, LCP, and more |
Surface Finishes | ENIG, ENEPIG, OSP, and more |
These capabilities enable Averatek to cater to a wide range of PCB design requirements, from simple single-layer boards to complex multi-layer HDI and UHDI PCBs.
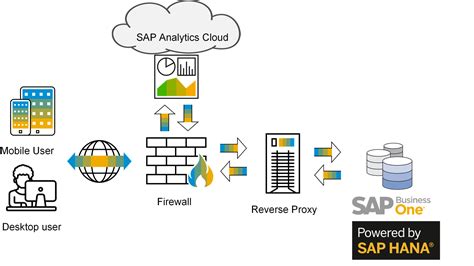
Future of SAP@Averatek
Advancements in SAP Technology
Averatek is continuously working on advancing its SAP technology to push the boundaries of PCB manufacturing. Some of the ongoing research and development efforts include:
-
Material Innovations: Averatek is exploring new substrate materials and seed layer compositions to enhance the performance and reliability of SAP-manufactured PCBs.
-
Process Optimization: Averatek is continuously refining its SAP process flow to improve efficiency, reduce cycle times, and minimize waste.
-
Automation and Industry 4.0: Averatek is investing in automation and Industry 4.0 technologies to streamline its manufacturing processes, improve quality control, and enable real-time monitoring and optimization.
Collaborations and Partnerships
Averatek actively collaborates with industry partners, academic institutions, and research organizations to drive innovation in SAP technology. These collaborations aim to address the evolving needs of the electronics industry and develop novel solutions for PCB manufacturing challenges.
Future Applications
As SAP technology continues to advance, it is expected to find applications in emerging fields such as:
-
5G and Beyond: SAP-manufactured PCBs will play a crucial role in enabling the high-frequency and high-bandwidth requirements of 5G and future wireless communication technologies.
-
Internet of Things (IoT): SAP’s ability to create compact and reliable PCBs will be essential for the development of IoT devices and sensors that require miniaturization and low power consumption.
-
Artificial Intelligence (AI) and Machine Learning (ML): SAP-manufactured PCBs will be instrumental in the development of AI and ML hardware accelerators, enabling faster and more efficient processing of complex algorithms.
-
Quantum Computing: As quantum computing technologies advance, SAP’s capability to create high-density interconnects and fine-pitch traces will be crucial for the development of quantum computing hardware.
Frequently Asked Questions (FAQ)
-
What is the main advantage of SAP@Averatek compared to traditional PCB manufacturing processes?
SAP@Averatek enables the creation of fine-pitch traces and high-density interconnects, allowing for the miniaturization of electronic devices and improved signal integrity. It offers higher reliability, cost-effectiveness, and enhanced design flexibility compared to traditional PCB manufacturing processes. -
Can SAP@Averatek be used for both rigid and flexible PCBs?
Yes, SAP@Averatek is compatible with various substrate materials, including rigid substrates like FR-4 and flexible substrates like polyimide and liquid crystal polymer (LCP). This versatility allows SAP technology to be used for both rigid and flexible PCB applications. -
What are the typical trace widths and spacings achievable with SAP@Averatek?
SAP@Averatek can achieve trace widths and spacings down to 10 μm, enabling the creation of high-density interconnects and fine-pitch traces. This capability surpasses the limitations of traditional PCB manufacturing processes and allows for the development of compact and high-performance electronic devices. -
How does SAP@Averatek ensure the reliability and quality of the manufactured PCBs?
Averatek implements rigorous quality control measures throughout the SAP process, including advanced substrate preparation techniques, optimized copper plating processes, and thorough inspections. These measures ensure that the manufactured PCBs meet the highest standards of reliability and performance. -
What are the future prospects of SAP@Averatek in the electronics industry?
SAP@Averatek is poised to play a significant role in the future of the electronics industry, enabling the development of advanced technologies such as 5G, IoT, AI, and quantum computing. As the demand for miniaturization, high-density interconnects, and improved signal integrity continues to grow, SAP technology will be at the forefront of PCB manufacturing innovations.
Conclusion
SAP@Averatek represents a significant advancement in PCB manufacturing technology, offering a range of benefits over traditional processes. With its ability to create fine-pitch traces and high-density interconnects, SAP technology enables the miniaturization of electronic devices, improves signal integrity, and enhances reliability. Averatek Corporation, with its expertise and state-of-the-art facilities, is leading the way in the development and application of SAP technology.
As the electronics industry continues to evolve, demanding smaller, faster, and more feature-rich devices, SAP@Averatek will play a crucial role in enabling the development of advanced technologies. From consumer electronics to automotive, medical, aerospace, and defense applications, SAP-manufactured PCBs will be at the heart of innovative electronic solutions.
With ongoing advancements in SAP technology, collaborations with industry partners, and the exploration of new applications, Averatek is well-positioned to shape the future of PCB manufacturing. As the adoption of SAP@Averatek grows, it is expected to revolutionize the electronics industry, driving innovation, efficiency, and reliability in PCB production.
No responses yet