Introduction to Soldering Techniques for Through-Hole PCBs
Soldering is an essential process in the manufacturing of printed circuit boards (PCBs) that involves joining electronic components to the board using a molten metal alloy. When it comes to through-hole PCBs, where component leads are inserted through holes drilled in the board and soldered on the opposite side, two primary soldering techniques are commonly used: selective soldering and wave soldering. Each method has its advantages and disadvantages, making it crucial for manufacturers to understand the differences and choose the most suitable technique for their specific requirements.
What is Through-Hole PCB Assembly?
Through-hole PCB assembly is a technique where electronic components with long leads are inserted into drilled holes on a printed circuit board. The leads are then soldered to the copper pads on the opposite side of the board, creating a strong mechanical and electrical connection. This assembly method has been widely used for decades and is known for its reliability and durability.
Importance of Soldering in Through-Hole PCB Assembly
Soldering plays a critical role in through-hole PCB assembly, as it ensures a robust and reliable connection between the electronic components and the PCB. A properly soldered joint provides:
-
Mechanical strength: The solder joint holds the component securely in place, preventing it from moving or becoming loose due to vibration or physical stress.
-
Electrical conductivity: The solder creates a low-resistance path for electrical current to flow between the component and the PCB, ensuring proper circuit functionality.
-
Protection against corrosion: The solder joint seals the connection, protecting it from environmental factors such as moisture and air, which can cause corrosion and deterioration over time.
Selective Soldering
Selective soldering is a precise and targeted approach to soldering through-hole components on a PCB. This technique involves applying solder only to specific areas of the board, leaving the rest of the components untouched.
How Selective Soldering Works
The selective soldering process typically follows these steps:
-
PCB preparation: The through-hole components are inserted into the PCB, and the board is placed in a fixture to hold it securely during the soldering process.
-
Flux application: A thin layer of flux is applied to the areas where soldering will take place. Flux helps remove oxides from the metal surfaces and promotes better solder wetting.
-
Preheating: The PCB is preheated to activate the flux and reduce thermal shock to the components during soldering.
-
Soldering: A soldering nozzle, guided by a computer-controlled system, precisely applies molten solder to the designated areas. The nozzle can be programmed to follow a specific path and adjust the solder flow and temperature as needed.
-
Cooling and cleaning: After soldering, the PCB is allowed to cool down, and any excess flux residue is removed using a cleaning agent.
Advantages of Selective Soldering
-
Precision: Selective soldering allows for highly accurate and targeted solder application, reducing the risk of bridging or short circuits between closely spaced components.
-
Flexibility: The process can be easily adapted to accommodate different component types, sizes, and configurations, making it suitable for a wide range of PCB designs.
-
Reduced thermal stress: Since only specific areas of the PCB are exposed to heat during soldering, the overall thermal stress on the board and components is minimized, reducing the risk of damage.
-
Cost-effective for low-volume production: Selective soldering is an economical choice for low-volume or prototype production, as it requires less setup time and material compared to wave soldering.
Disadvantages of Selective Soldering
-
Slower process: Selective soldering is a slower process compared to wave soldering, as each component or group of components is soldered individually.
-
Higher equipment cost: Selective soldering machines are generally more expensive than wave soldering equipment due to their advanced features and precision control systems.
-
Limited throughput: The slower nature of selective soldering limits its throughput, making it less suitable for high-volume production.
Wave Soldering
Wave soldering is a popular and efficient method for soldering through-hole components on a PCB. In this process, the entire board is passed over a wave of molten solder, which simultaneously solders all the components in a single pass.
How Wave Soldering Works
The wave soldering process typically involves the following steps:
-
PCB preparation: Through-hole components are inserted into the PCB, and the board is placed on a conveyor system.
-
Flux application: The bottom side of the PCB is sprayed with a thin layer of flux to remove oxides and promote better solder wetting.
-
Preheating: The PCB is preheated to activate the flux and minimize thermal shock during soldering.
-
Wave soldering: The PCB is passed over a wave of molten solder. As the board comes into contact with the solder wave, the molten solder is drawn up through the holes, soldering the component leads to the copper pads.
-
Cooling and cleaning: After soldering, the PCB is cooled down, and any excess flux residue is removed using a cleaning agent.
Advantages of Wave Soldering
-
High throughput: Wave soldering is a fast process that can handle high-volume production, as multiple boards can be soldered in rapid succession.
-
Cost-effective for high-volume production: Due to its speed and efficiency, wave soldering is an economical choice for large-scale production runs.
-
Consistency: Wave soldering provides a consistent solder joint quality across the entire PCB, as all components are soldered simultaneously under the same conditions.
-
Compatibility with various component types: Wave soldering can accommodate a wide range of through-hole component types and sizes.
Disadvantages of Wave Soldering
-
Limited precision: Wave soldering lacks the precision of selective soldering, as the entire board is exposed to the solder wave. This can lead to bridging or short circuits between closely spaced components.
-
Higher thermal stress: The entire PCB is subjected to high temperatures during wave soldering, which can cause thermal stress on the board and components, potentially leading to damage or reduced reliability.
-
Difficulty with mixed-technology boards: Wave soldering may not be suitable for PCBs that contain both through-hole and surface-mount components, as the solder wave can cause damage to the surface-mount components.
-
Large solder waste and dross: The wave soldering process generates more solder waste and dross (oxidized solder) compared to selective soldering, which can increase material costs and environmental impact.
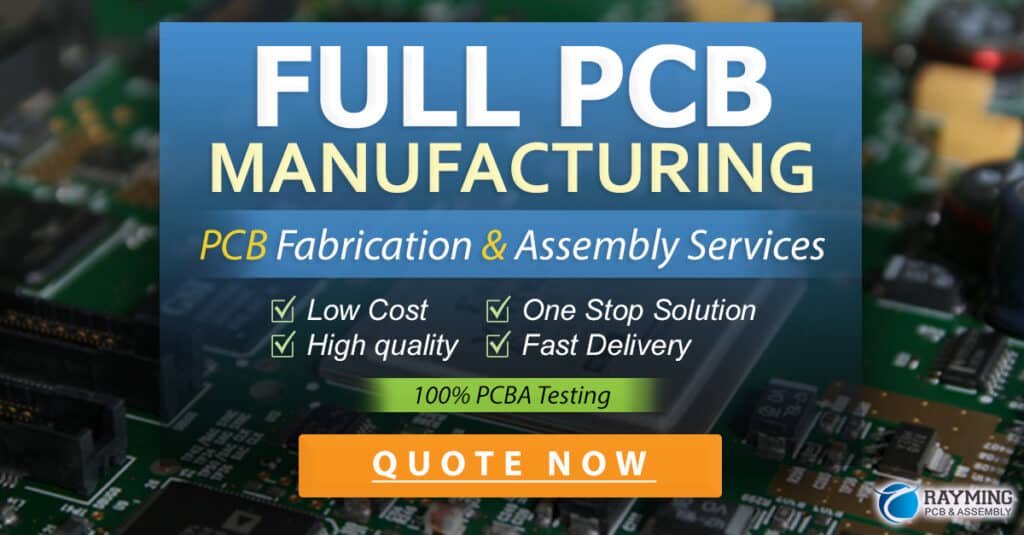
Comparison of Selective Soldering and Wave Soldering
To help manufacturers choose the most appropriate soldering technique for their through-hole PCB assembly needs, it is essential to compare the key aspects of selective soldering and wave soldering:
Factor | Selective Soldering | Wave Soldering |
---|---|---|
Precision | High | Low |
Flexibility | High | Moderate |
Thermal stress | Low | High |
Throughput | Low to moderate | High |
Cost-effectiveness | Low-volume | High-volume |
Equipment cost | High | Moderate |
Solder waste and dross | Low | High |
Mixed-technology PCBs | Suitable | Challenging |
Choosing the Right Soldering Technique
When deciding between selective soldering and wave soldering for through-hole PCB assembly, consider the following factors:
-
Production volume: If you have high-volume production needs, wave soldering is likely the more cost-effective choice. For low-volume or prototype production, selective soldering may be more suitable.
-
PCB design complexity: If your PCB has closely spaced components or requires precise soldering, selective soldering is the better option. Wave soldering is more suitable for simpler designs with larger component spacing.
-
Component mix: If your PCB contains a mix of through-hole and surface-mount components, selective soldering is the preferred choice to avoid damaging the surface-mount components.
-
Budget and equipment availability: Consider your budget and the availability of soldering equipment. Selective soldering machines are generally more expensive than wave soldering equipment, but they offer greater precision and flexibility.
Conclusion
Selective soldering and wave soldering are both viable techniques for through-hole PCB assembly, each with its own advantages and disadvantages. Selective soldering offers high precision, flexibility, and reduced thermal stress, making it ideal for low-volume production and complex PCB designs. On the other hand, wave soldering provides high throughput and cost-effectiveness for high-volume production, but with lower precision and higher thermal stress.
When choosing between selective soldering and wave soldering, manufacturers must carefully consider factors such as production volume, PCB design complexity, component mix, budget, and equipment availability. By understanding the differences between these two soldering techniques and their respective strengths and weaknesses, manufacturers can make an informed decision that best suits their specific through-hole PCB assembly requirements.
Frequently Asked Questions (FAQ)
- What is the main difference between selective soldering and wave soldering?
-
Selective soldering is a precise, targeted approach that applies solder only to specific areas of the PCB, while wave soldering involves passing the entire board over a wave of molten solder to simultaneously solder all components.
-
Which soldering technique is better for low-volume production?
-
Selective soldering is generally more cost-effective for low-volume or prototype production, as it requires less setup time and material compared to wave soldering.
-
Can wave soldering handle mixed-technology PCBs with both through-hole and surface-mount components?
-
Wave soldering may not be suitable for mixed-technology PCBs, as the solder wave can cause damage to the surface-mount components. Selective soldering is the preferred choice in such cases.
-
Which soldering technique offers higher precision?
-
Selective soldering offers higher precision compared to wave soldering, as it allows for highly accurate and targeted solder application, reducing the risk of bridging or short circuits between closely spaced components.
-
Is selective soldering equipment more expensive than wave soldering equipment?
- Yes, selective soldering machines are generally more expensive than wave soldering equipment due to their advanced features and precision control systems.
No responses yet