Introduction
When it comes to designing and manufacturing printed Circuit Boards (PCBs), selecting the right surface finish is crucial for ensuring the reliability, durability, and performance of the final product. The surface finish not only protects the copper traces from oxidation and corrosion but also plays a vital role in the solderability and assembly process. With a variety of PCB Surface Finishes available, each with its own advantages and disadvantages, it can be challenging to choose the best option for your specific application. In this article, we will explore the different types of PCB Surface Finishes, their properties, and the factors to consider when making your selection.
What is a PCB Surface Finish?
A PCB surface finish is a thin layer of material applied to the exposed copper traces and pads on a printed circuit board. This layer serves multiple purposes:
-
Protection: The surface finish protects the copper from oxidation and corrosion, which can degrade the electrical performance and reliability of the PCB.
-
Solderability: The surface finish enhances the solderability of the copper, allowing for better wetting and bonding of the solder during the assembly process.
-
Aesthetics: Some surface finishes, such as immersion gold, provide an attractive appearance to the PCB.
-
Compatibility: The surface finish must be compatible with the components and the assembly process used, ensuring reliable connections and preventing issues like whisker growth or intermetallic compound formation.
Types of PCB Surface Finishes
There are several types of PCB surface finishes available, each with its own unique properties and advantages. Some of the most common surface finishes include:
1. Hot Air Solder Leveling (HASL)
HASL is one of the most widely used PCB surface finishes. In this process, the PCB is dipped into a molten solder bath, and then hot air is used to blow off the excess solder, leaving a thin, uniform layer on the copper traces and pads. HASL provides excellent solderability and is relatively inexpensive compared to other surface finishes.
Advantages:
– Good solderability
– Low cost
– Widely available
– Suitable for most applications
Disadvantages:
– Uneven surface due to the nature of the process
– Not suitable for fine-pitch components
– May cause thermal shock to the PCB
– Contains lead (in the case of leaded HASL)
2. Organic Solderability Preservative (OSP)
OSP is a thin, organic coating applied to the copper traces and pads. It acts as a barrier against oxidation and provides good solderability. OSP is a lead-free and relatively inexpensive surface finish.
Advantages:
– Lead-free and environmentally friendly
– Low cost
– Flat surface, suitable for fine-pitch components
– Good solderability
Disadvantages:
– Limited shelf life (typically 6-12 months)
– Not suitable for multiple reflow cycles
– May not be suitable for high-temperature applications
– Sensitive to handling and storage conditions
3. Electroless Nickel Immersion Gold (ENIG)
ENIG is a two-layer surface finish consisting of a thin layer of gold over a layer of nickel. The nickel layer provides a barrier against copper migration, while the gold layer ensures excellent solderability and protection against oxidation.
Advantages:
– Excellent solderability
– Good shelf life
– Suitable for fine-pitch components
– Resistant to multiple reflow cycles
– Provides a flat, uniform surface
Disadvantages:
– Higher cost compared to HASL and OSP
– Potential for black pad formation due to improper plating processes
– May be prone to gold embrittlement in certain conditions
4. Immersion Tin (ISn)
Immersion tin is a single-layer surface finish where a thin layer of tin is applied directly to the copper traces and pads. It provides good solderability and is a lead-free option.
Advantages:
– Lead-free and environmentally friendly
– Good solderability
– Flat surface, suitable for fine-pitch components
– Lower cost compared to ENIG
Disadvantages:
– Potential for tin whisker growth, which can cause short circuits
– Limited shelf life compared to ENIG
– May not be suitable for high-temperature applications
5. Immersion Silver (IAg)
Immersion silver is another single-layer surface finish that involves the deposition of a thin layer of silver on the copper traces and pads. It offers excellent solderability and conductivity.
Advantages:
– Excellent solderability
– High conductivity
– Lead-free and environmentally friendly
– Suitable for fine-pitch components
Disadvantages:
– Higher cost compared to OSP and immersion tin
– Potential for silver migration in high-humidity environments
– May tarnish over time, affecting appearance
6. Electroless Nickel Electroless Palladium Immersion Gold (ENEPIG)
ENEPIG is a three-layer surface finish consisting of a nickel layer, a palladium layer, and a thin gold layer. It combines the advantages of ENIG with the added benefits of a palladium layer, which enhances wire bonding capabilities.
Advantages:
– Excellent solderability
– Suitable for wire bonding
– Good shelf life
– Resistant to multiple reflow cycles
– Provides a flat, uniform surface
Disadvantages:
– Higher cost compared to other surface finishes
– Complex plating process
– Potential for black pad formation if not properly controlled
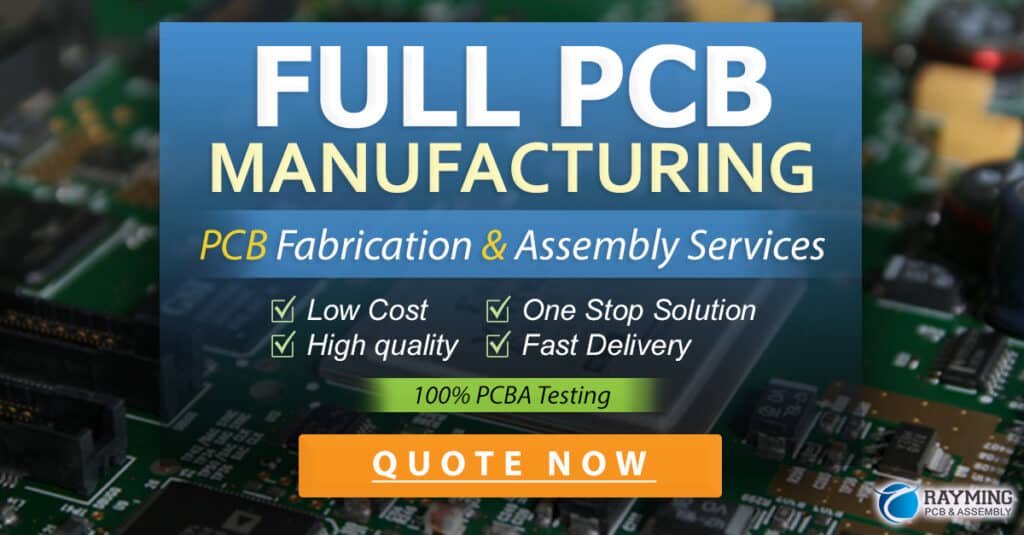
Factors to Consider When Selecting a PCB Surface Finish
When choosing a PCB surface finish for your application, there are several factors to consider:
-
Cost: The cost of the surface finish can vary significantly, with HASL being the least expensive and ENEPIG being the most costly. Consider your budget and the cost-benefit tradeoffs of each surface finish option.
-
Solderability: The surface finish must provide good solderability to ensure reliable connections during the assembly process. HASL, ENIG, and immersion silver offer excellent solderability, while OSP and immersion tin may have limitations in certain conditions.
-
Shelf Life: If your PCBs will be stored for an extended period before assembly, consider a surface finish with a longer shelf life, such as ENIG or immersion silver. OSP and immersion tin have shorter shelf lives and may degrade over time.
-
Component Compatibility: The surface finish must be compatible with the components used in your design. Fine-pitch components may require a flat, uniform surface, such as ENIG or immersion silver, while larger components can work well with HASL.
-
Environmental Concerns: If environmental sustainability is a priority, lead-free surface finishes like OSP, immersion tin, immersion silver, and ENEPIG are preferred over leaded HASL.
-
Assembly Process: The surface finish should be compatible with the assembly process used. For example, if your PCBs will undergo multiple reflow cycles, ENIG or ENEPIG may be more suitable than OSP or immersion tin.
-
Electrical Performance: Some surface finishes, like immersion silver, offer higher conductivity compared to others. Consider the electrical requirements of your application when selecting a surface finish.
-
Reliability: The surface finish plays a role in the long-term reliability of the PCB. ENIG and ENEPIG provide excellent protection against oxidation and corrosion, while immersion tin may be prone to tin whisker growth, which can cause short circuits.
PCB Surface Finish Comparison
Surface Finish | Cost | Solderability | Shelf Life | Fine-Pitch Compatibility | Environmental | Multiple Reflow | Conductivity |
---|---|---|---|---|---|---|---|
HASL | Low | Excellent | Good | Limited | Leaded | Good | Good |
OSP | Low | Good | Limited | Good | Lead-free | Limited | Good |
ENIG | High | Excellent | Excellent | Excellent | Lead-free | Excellent | Good |
Immersion Tin | Low | Good | Limited | Good | Lead-free | Limited | Good |
Immersion Silver | Moderate | Excellent | Good | Excellent | Lead-free | Good | Excellent |
ENEPIG | High | Excellent | Excellent | Excellent | Lead-free | Excellent | Good |
Frequently Asked Questions (FAQ)
-
Q: Which PCB surface finish is the most cost-effective?
A: Hot Air Solder Leveling (HASL) and Organic Solderability Preservative (OSP) are generally the most cost-effective PCB surface finishes. -
Q: Is ENIG suitable for high-reliability applications?
A: Yes, Electroless Nickel Immersion Gold (ENIG) provides excellent reliability and protection against oxidation and corrosion, making it suitable for high-reliability applications. -
Q: Can immersion tin be used for fine-pitch components?
A: Yes, immersion tin provides a flat, uniform surface that is suitable for fine-pitch components. However, it may be prone to tin whisker growth, which can cause short circuits in certain conditions. -
Q: Which surface finish offers the best shelf life?
A: ENIG and ENEPIG offer the best shelf life among PCB surface finishes, as they provide excellent protection against oxidation and corrosion. -
Q: Is OSP a lead-free surface finish?
A: Yes, Organic Solderability Preservative (OSP) is a lead-free and environmentally friendly surface finish option.
Conclusion
Selecting the right PCB surface finish is a critical decision that impacts the reliability, solderability, and overall performance of your printed circuit board. By understanding the different types of surface finishes available and considering factors such as cost, shelf life, component compatibility, and environmental concerns, you can make an informed decision that best suits your specific application.
Remember that each surface finish has its own advantages and disadvantages, and there is no one-size-fits-all solution. It’s essential to work closely with your PCB Manufacturer and assembly partner to discuss your requirements and ensure that the chosen surface finish meets your needs.
Investing time in selecting the appropriate PCB surface finish early in the design process can save you from potential issues down the line, such as poor solderability, reliability problems, or compatibility challenges. By making an informed decision and working with experienced professionals, you can ensure that your PCB performs optimally and meets the demands of your application.
No responses yet