Introduction
When designing and manufacturing printed circuit boards (PCBs), selecting the appropriate Surface Finish is crucial for ensuring the reliability, functionality, and longevity of the final product. The surface finish not only protects the copper traces and pads from oxidation and corrosion but also plays a vital role in the solderability and assembly process. With a variety of surface finish options available, each with its own advantages and disadvantages, it is essential to understand the factors that influence the selection process. In this article, we will explore the different types of surface finishes commonly used in PCB manufacturing, their properties, and the considerations to keep in mind when choosing the right surface finish for your specific application.
Importance of Surface Finish in PCB Manufacturing
The surface finish applied to a PCB serves several critical functions:
-
Protection: The surface finish acts as a barrier, preventing the underlying copper from oxidizing and corroding when exposed to the environment. Oxidation and corrosion can lead to reduced conductivity, poor solderability, and potential failure of the PCB.
-
Solderability: The surface finish plays a crucial role in the soldering process during PCB Assembly. It ensures good wetting and bonding between the solder and the copper pads, resulting in reliable electrical connections.
-
Durability: The right surface finish can enhance the durability of the PCB, protecting it from mechanical damage, wear, and tear during handling and operation.
-
Electrical Performance: Some surface finishes have superior electrical properties, such as lower contact resistance and better high-frequency performance, which can be important for certain applications.
-
Aesthetics: The surface finish can also impact the visual appearance of the PCB, which may be a consideration for certain products or applications.
Factors to Consider When Selecting a Surface Finish
When choosing a surface finish for your PCB, several factors need to be taken into account:
-
Application Requirements: The intended application of the PCB will heavily influence the choice of surface finish. Factors such as the operating environment, temperature range, humidity, and expected lifespan should be considered.
-
Soldering Process: The surface finish must be compatible with the soldering process used during PCB assembly. Different soldering techniques, such as wave soldering, reflow soldering, or hand soldering, may have specific requirements for the surface finish.
-
Cost: The cost of the surface finish is another important consideration. Some surface finishes are more expensive than others due to the materials and processes involved. It is essential to strike a balance between cost and performance based on the specific needs of the project.
-
Shelf Life: The shelf life of the surface finish refers to the duration for which it can maintain its solderability and protect the copper from oxidation. Some surface finishes have longer shelf lives than others, which can be a factor if the PCBs need to be stored for an extended period before assembly.
-
Compatibility with Components: The surface finish should be compatible with the components used on the PCB. Certain components may have specific requirements or restrictions regarding the surface finish to ensure proper soldering and reliability.
-
Manufacturing Capabilities: The choice of surface finish may also depend on the capabilities of the PCB manufacturer. Some surface finishes require specialized equipment or processes that may not be available at all manufacturing facilities.
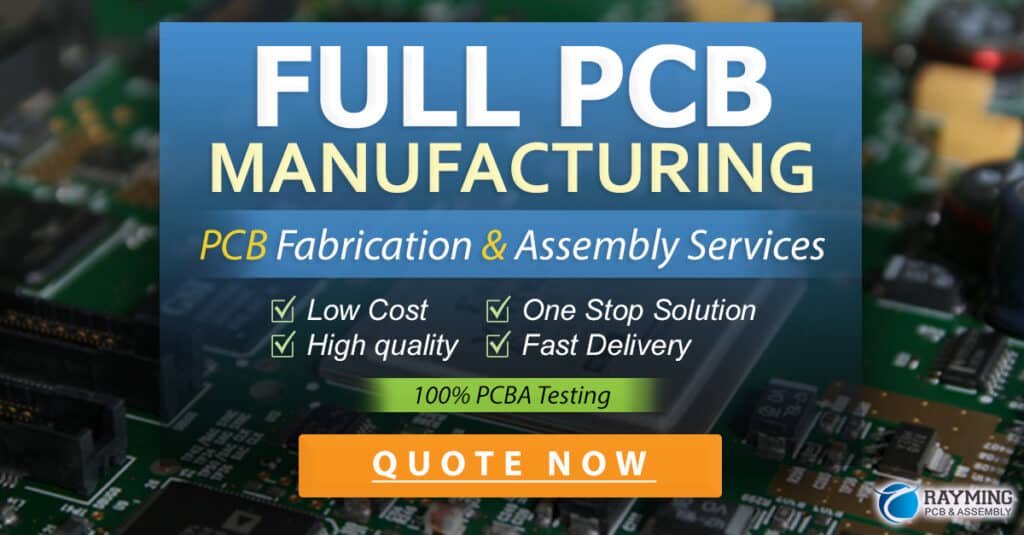
Common Types of PCB Surface Finishes
There are several commonly used surface finishes in PCB manufacturing, each with its own characteristics and benefits. Let’s explore some of the most popular options:
1. Hot Air Solder Leveling (HASL)
HASL is one of the most widely used surface finishes in the PCB industry. In this process, the PCB is dipped into a molten solder bath, and then hot air is used to blow off the excess solder, leaving a thin, uniform layer on the copper pads.
Advantages:
– Cost-effective and widely available
– Excellent solderability and wetting properties
– Good shelf life and durability
– Compatible with a wide range of soldering processes
Disadvantages:
– Uneven surface due to the nature of the process
– Potential for Solder Bridges and shorts
– Not suitable for fine-pitch components or high-density designs
– Contains lead (Pb), which may not be acceptable for certain applications
2. Electroless Nickel Immersion Gold (ENIG)
ENIG is a two-layer surface finish that consists of an electroless nickel plating followed by a thin layer of immersion gold. The nickel layer provides a barrier against copper diffusion, while the gold layer offers excellent solderability and protection against oxidation.
Advantages:
– Flat and uniform surface finish
– Excellent solderability and wetting properties
– Suitable for fine-pitch components and high-density designs
– Good shelf life and resistance to oxidation
– RoHS compliant (lead-free)
Disadvantages:
– Higher cost compared to HASL
– Potential for “black pad” defect due to improper plating processes
– Gold layer may dissolve into the solder joint during assembly
– Requires strict process control and quality monitoring
3. Immersion Silver (IAg)
Immersion silver is a single-layer surface finish that involves depositing a thin layer of silver directly onto the copper surface through a chemical process. It offers good solderability and is often used as a cost-effective alternative to ENIG.
Advantages:
– Lower cost compared to ENIG
– Good solderability and wetting properties
– Suitable for fine-pitch components and high-density designs
– RoHS compliant (lead-free)
– Faster and simpler process compared to ENIG
Disadvantages:
– Shorter shelf life compared to ENIG (prone to tarnishing over time)
– May require additional storage and handling precautions
– Not suitable for high-temperature applications
– Potential for silver migration in high-humidity environments
4. Organic Solderability Preservative (OSP)
OSP is a chemical coating that is applied to the copper surface to protect it from oxidation. It is a thin, transparent layer that is activated during the soldering process, allowing for good solder wetting.
Advantages:
– Cost-effective and simple process
– Flat and uniform surface finish
– Suitable for fine-pitch components and high-density designs
– RoHS compliant (lead-free)
– Good for quick-turn prototyping and short shelf life requirements
Disadvantages:
– Limited shelf life (typically a few months)
– Requires careful handling and storage to prevent contamination
– May not be suitable for multiple soldering cycles
– Can be difficult to inspect visually for defects or quality issues
Comparison of Surface Finishes
To help you make an informed decision, here is a comparison table of the common PCB Surface Finishes:
Surface Finish | Cost | Shelf Life | Solderability | Fine-Pitch Compatibility | RoHS Compliant |
---|---|---|---|---|---|
HASL | Low | Good | Excellent | Limited | No (contains lead) |
ENIG | High | Excellent | Excellent | Excellent | Yes |
Immersion Silver | Moderate | Moderate | Good | Excellent | Yes |
OSP | Low | Limited | Good | Excellent | Yes |
Frequently Asked Questions (FAQ)
-
Q: What is the most cost-effective surface finish for PCBs?
A: Hot Air Solder Leveling (HASL) and Organic Solderability Preservative (OSP) are generally the most cost-effective surface finish options. However, it’s important to consider other factors such as shelf life, solderability, and compatibility with your specific application requirements. -
Q: Which surface finish is best for high-density designs with fine-pitch components?
A: Electroless Nickel Immersion Gold (ENIG) and Immersion Silver (IAg) are excellent choices for high-density designs and fine-pitch components. These surface finishes provide a flat and uniform surface that facilitates precise component placement and soldering. -
Q: Can HASL be used for RoHS-Compliant PCBs?
A: Traditional HASL contains lead (Pb) and is not RoHS compliant. However, there are lead-free HASL options available that use alternative alloys to meet RoHS requirements. It’s important to specify the need for lead-free HASL when working with your PCB manufacturer. -
Q: What is the shelf life of OSP-coated PCBs?
A: OSP-coated PCBs typically have a limited shelf life of a few months. The exact shelf life depends on factors such as storage conditions and the specific OSP formulation used. It’s crucial to handle and store OSP-coated PCBs properly to maintain their solderability and prevent contamination. -
Q: How do I choose between ENIG and Immersion Silver for my PCB?
A: Both ENIG and Immersion Silver offer excellent solderability and are suitable for fine-pitch components. ENIG provides a longer shelf life and better resistance to oxidation compared to Immersion Silver. However, Immersion Silver is generally more cost-effective. Consider your specific application requirements, budget, and the expected storage duration before making a decision.
Conclusion
Selecting the right surface finish for your PCB is a critical decision that impacts the reliability, functionality, and manufacturability of your electronic device. By understanding the different types of surface finishes available, their properties, and the factors to consider, you can make an informed choice that meets your specific application requirements. Whether you prioritize cost, solderability, shelf life, or compatibility with fine-pitch components, there is a surface finish option that can cater to your needs. It’s essential to work closely with your PCB manufacturer and discuss your requirements to ensure the best possible outcome for your project.
No responses yet