Introduction to Multilayer PCB Substrates
Multilayer printed circuit boards (PCBs) have become an essential component in modern electronics, enabling the development of compact, high-performance devices. These complex structures consist of multiple layers of conductive and insulating materials, allowing for the interconnection of various electronic components. The choice of substrate material plays a crucial role in determining the performance, reliability, and cost of multilayer PCBs.
Traditionally, FR-4 (Flame Retardant 4) has been the most widely used substrate material for multilayer PCBs due to its excellent mechanical and electrical properties, as well as its cost-effectiveness. However, as the demand for higher performance, increased reliability, and specialized applications grows, alternative substrate materials are being explored to meet these requirements.
Factors to Consider When Selecting Multilayer PCB Substrates
When choosing an alternative substrate material for multilayer PCBs, several key factors must be considered to ensure optimal performance and reliability. These factors include:
-
Dielectric Constant (Dk): The dielectric constant of a substrate material determines its ability to store electrical energy. A lower Dk value is desirable for high-frequency applications, as it reduces signal propagation delay and minimizes signal loss.
-
Dissipation Factor (Df): The dissipation factor, also known as loss tangent, measures the amount of energy dissipated as heat within the substrate material. A lower Df value is preferred, as it minimizes signal attenuation and improves signal integrity.
-
Thermal Conductivity: The thermal conductivity of a substrate material determines its ability to dissipate heat generated by the electronic components. Higher thermal conductivity is essential for applications that generate significant heat, as it helps prevent thermal damage and improves reliability.
-
Coefficient of Thermal Expansion (CTE): The CTE of a substrate material refers to its dimensional change in response to temperature variations. A substrate with a CTE closely matched to that of the copper traces and electronic components minimizes stress and improves the overall reliability of the multilayer PCB.
-
Mechanical Strength: The mechanical strength of a substrate material is crucial for maintaining the structural integrity of the multilayer PCB during manufacturing, assembly, and operation. Substrates with higher mechanical strength are less susceptible to warping, twisting, and other physical deformations.
-
Cost: The cost of alternative substrate materials is an important consideration, as it directly impacts the overall cost of the multilayer PCB. While some high-performance substrates may offer superior properties, their higher cost may not be justified for all applications.
Alternative Substrate Materials for Multilayer PCBs
1. High-Frequency Laminates
High-frequency laminates are designed specifically for applications that operate at high frequencies, such as RF and microwave circuits. These substrate materials offer low dielectric constant and dissipation factor values, enabling faster signal propagation and minimizing signal loss. Some popular high-frequency laminates include:
a. Rogers RO4000 Series
The Rogers RO4000 series is a family of high-performance laminate materials designed for high-frequency applications. These substrates offer a low dielectric constant (3.55 to 3.66) and a low dissipation factor (0.0027 to 0.0037), making them suitable for applications up to 40 GHz. Additionally, the RO4000 series has a low CTE, which enhances the reliability of the multilayer PCB.
b. Isola IS680
Isola IS680 is a low-loss, high-speed laminate material designed for high-frequency applications up to 77 GHz. With a dielectric constant of 3.33 and a dissipation factor of 0.0028, IS680 provides excellent signal integrity and minimal signal attenuation. This substrate material also offers good thermal stability and low moisture absorption, ensuring reliable performance in demanding environments.
2. Low-Loss Substrates
Low-loss substrates are designed to minimize signal attenuation and improve signal integrity in high-speed digital and RF applications. These materials typically have a lower dissipation factor compared to standard FR-4, allowing for faster signal propagation and reduced signal distortion. Examples of low-loss substrates include:
a. Panasonic Megtron
Panasonic Megtron is a family of low-loss substrate materials designed for high-speed digital and RF applications. These laminates offer a range of dielectric constants (2.8 to 3.7) and low dissipation factors (0.002 to 0.007), enabling designers to choose the most suitable material for their specific application. Megtron substrates also provide excellent thermal stability and low moisture absorption, ensuring reliable performance in various environmental conditions.
b. Nelco N4000-13SI
Nelco N4000-13SI is a low-loss, high-speed substrate material designed for applications up to 28 GHz. With a dielectric constant of 3.7 and a dissipation factor of 0.009, this laminate offers excellent signal integrity and reduced signal attenuation. N4000-13SI also has a low CTE, which minimizes stress and improves the reliability of the multilayer PCB.
3. Thermally Conductive Substrates
Thermally conductive substrates are designed to efficiently dissipate heat generated by electronic components, improving the thermal management of multilayer PCBs. These materials typically have a higher thermal conductivity compared to standard FR-4, allowing for better heat transfer and reduced thermal stress. Examples of thermally conductive substrates include:
a. Bergquist HT-04503
Bergquist HT-04503 is a thermally conductive substrate material designed for applications that require efficient heat dissipation. With a thermal conductivity of 1.0 W/mK, this laminate is capable of effectively transferring heat away from electronic components, reducing thermal stress and improving reliability. HT-04503 also has a low dielectric constant (3.8) and a low dissipation factor (0.012), making it suitable for high-speed applications.
b. Ventec VT-4B3
Ventec VT-4B3 is a thermally conductive substrate material designed for applications that generate significant heat. With a thermal conductivity of 1.2 W/mK, this laminate efficiently transfers heat away from electronic components, preventing thermal damage and improving the overall reliability of the multilayer PCB. VT-4B3 also offers a low CTE, which minimizes stress and enhances the long-term performance of the PCB.
Substrate Material | Dielectric Constant (Dk) | Dissipation Factor (Df) | Thermal Conductivity (W/mK) | CTE (ppm/°C) |
---|---|---|---|---|
Rogers RO4000 Series | 3.55 – 3.66 | 0.0027 – 0.0037 | 0.6 – 0.7 | 11 – 16 |
Isola IS680 | 3.33 | 0.0028 | 0.45 | 12 – 14 |
Panasonic Megtron | 2.8 – 3.7 | 0.002 – 0.007 | 0.4 – 0.5 | 10 – 15 |
Nelco N4000-13SI | 3.7 | 0.009 | 0.4 | 12 – 14 |
Bergquist HT-04503 | 3.8 | 0.012 | 1.0 | 14 – 16 |
Ventec VT-4B3 | 3.9 | 0.011 | 1.2 | 12 – 14 |
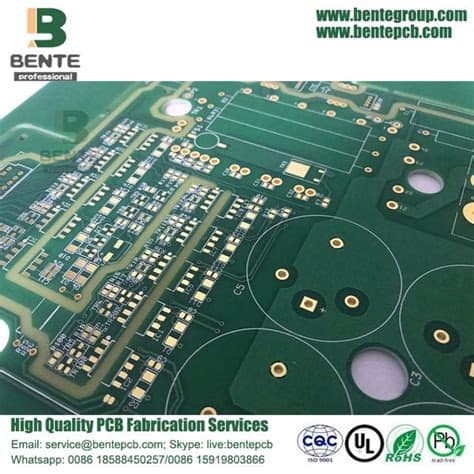
Selection Criteria for Alternative Multilayer PCB Substrates
When selecting an alternative substrate material for a multilayer PCB, designers should consider the following criteria:
-
Application Requirements: The choice of substrate material should be based on the specific requirements of the application, such as operating frequency, signal integrity, thermal management, and environmental conditions.
-
Performance vs. Cost: Designers must balance the performance benefits of alternative substrate materials against their associated costs. While high-performance substrates may offer superior properties, their higher cost may not be justified for all applications.
-
Manufacturing Compatibility: The selected substrate material should be compatible with the existing manufacturing processes and equipment. Some alternative substrates may require specialized processing or handling, which can impact the overall manufacturing cost and lead time.
-
Reliability and Durability: The substrate material should provide the necessary reliability and durability for the intended application. Factors such as thermal stability, moisture resistance, and mechanical strength should be considered to ensure the long-term performance of the multilayer PCB.
-
Availability and Supply Chain: The availability and stability of the supply chain for the selected substrate material should be evaluated. Designers should choose materials that are readily available and have a reliable supply chain to avoid potential delays or disruptions in production.
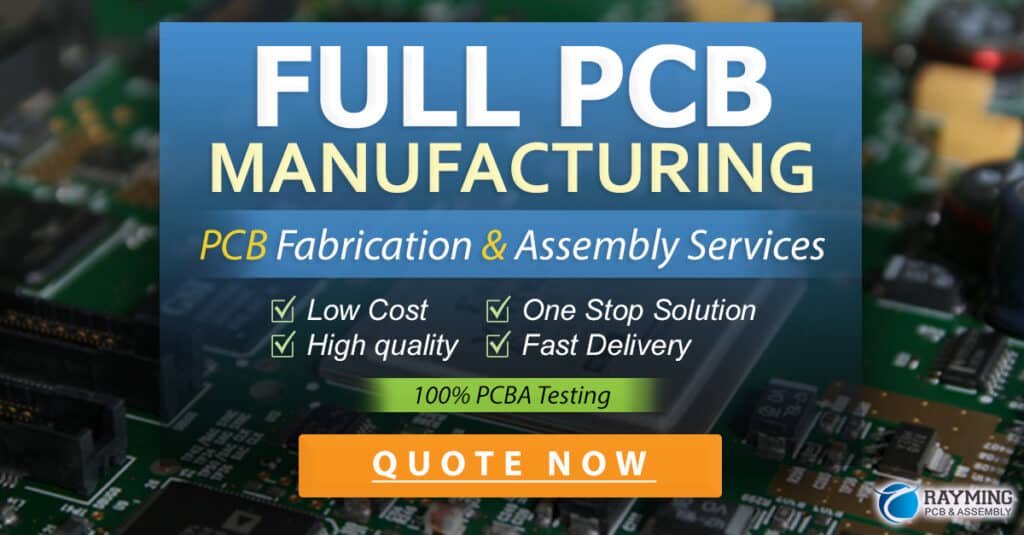
Conclusion
The selection of alternative substrate materials for multilayer PCBs is crucial for meeting the increasing demands of high-performance, reliable, and specialized electronic applications. By considering factors such as dielectric constant, dissipation factor, thermal conductivity, CTE, mechanical strength, and cost, designers can choose the most suitable substrate material for their specific requirements.
High-frequency laminates, low-loss substrates, and thermally conductive substrates are among the popular alternatives to traditional FR-4, each offering unique properties that cater to different application needs. When selecting an alternative substrate material, designers should carefully evaluate the application requirements, balance performance and cost, ensure manufacturing compatibility, consider reliability and durability, and assess the availability and supply chain stability.
By making an informed decision on the choice of substrate material, designers can optimize the performance, reliability, and cost-effectiveness of their multilayer PCBs, ultimately contributing to the development of advanced electronic devices and systems.
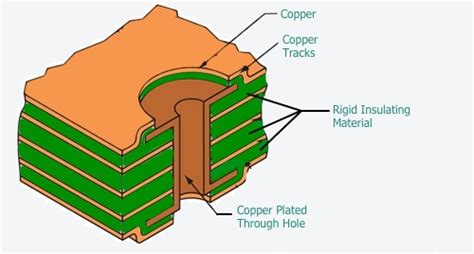
Frequently Asked Questions (FAQ)
-
Q: What is the most commonly used substrate material for multilayer PCBs?
A: FR-4 (Flame Retardant 4) is the most widely used substrate material for multilayer PCBs due to its excellent mechanical and electrical properties, as well as its cost-effectiveness. -
Q: What are the key factors to consider when selecting an alternative substrate material for multilayer PCBs?
A: The key factors to consider when selecting an alternative substrate material include dielectric constant (Dk), dissipation factor (Df), thermal conductivity, coefficient of thermal expansion (CTE), mechanical strength, and cost. -
Q: What are high-frequency laminates, and when are they used?
A: High-frequency laminates are substrate materials designed specifically for applications that operate at high frequencies, such as RF and microwave circuits. They offer low dielectric constant and dissipation factor values, enabling faster signal propagation and minimizing signal loss. -
Q: What are the benefits of using low-loss substrates in multilayer PCBs?
A: Low-loss substrates are designed to minimize signal attenuation and improve signal integrity in high-speed digital and RF applications. They typically have a lower dissipation factor compared to standard FR-4, allowing for faster signal propagation and reduced signal distortion. -
Q: Why are thermally conductive substrates used in multilayer PCBs?
A: Thermally conductive substrates are used in multilayer PCBs to efficiently dissipate heat generated by electronic components, improving the thermal management of the PCB. These materials have a higher thermal conductivity compared to standard FR-4, allowing for better heat transfer and reduced thermal stress, which enhances the reliability and performance of the PCB.
No responses yet